Hello all.. I have a crawl space that I am doing some work in and am trying to figure out the best way to do it.. It’s maybe 3 1/2 feet below grade, and builder put a few small vents on the ribbon boards letting all the warm and cold air and the moisture. I believe that he did actually put visqueen under the pebbles on the floor, but you can’t see much of it. And to top it off he used R-11 for the insulation on the joists. Needless to say, there is a decent amount of moisture in there. I plan on ripping out the R-11, using R-30 and then putting visqueen over the insulation to trap any moisture away from the joist bays and insulation. Then cut some pieces of wood and cover up those vents, and finally put visqueen on the whole bottom of the floor.. Does this make sense or do you guys have some different ideas? I believe that this is basically what a perma-seal type company would do.
Discussion Forum
Discussion Forum
Up Next
Video Shorts
Featured Story
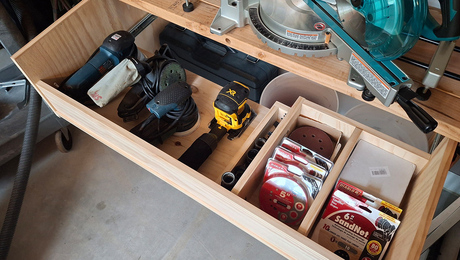
Listeners write in about removing masonry chimneys and ask about blocked ridge vents, deal-breakers with fixer-uppers, and flashing ledgers that are spaced from the wall.
Featured Video
How to Install Cable Rail Around Wood-Post CornersHighlights
"I have learned so much thanks to the searchable articles on the FHB website. I can confidently say that I expect to be a life-long subscriber." - M.K.
Fine Homebuilding Magazine
- Home Group
- Antique Trader
- Arts & Crafts Homes
- Bank Note Reporter
- Cabin Life
- Cuisine at Home
- Fine Gardening
- Fine Woodworking
- Green Building Advisor
- Garden Gate
- Horticulture
- Keep Craft Alive
- Log Home Living
- Military Trader/Vehicles
- Numismatic News
- Numismaster
- Old Cars Weekly
- Old House Journal
- Period Homes
- Popular Woodworking
- Script
- ShopNotes
- Sports Collectors Digest
- Threads
- Timber Home Living
- Traditional Building
- Woodsmith
- World Coin News
- Writer's Digest
Replies
View Image
http://www.quittintime.com/ View Image
More info in your profile would help in fitting a response relating to your environmental factors.
Vinyl & Foam board would be a better filler for the CS vents than wood.
Where do you live? How much rainfall per year?
Do your gutters work? And how far from the house do they drain.
Does your landscape elevation insure that rainwater moves quickly away from the foundation.
What is the foundation construction materials?
How much of the wall is exposed to the exterior?
Is your HVAC ductwork located in the crawlspace?
Do you have a water intrusion problem?
Is there a sump pump and pit?
How do you plan to eleminate/control the CS humidity after you "seal it up"?
Have you used the "advanced search" for "conditioned crawlspace" and read the numerous previous discussions on this subject?
............Iron Helix
I live in the Chicago land area. And I need to take care of some gutter issues for sure.. But as far as the actual grade, it seems to be o.k. There are 3 of the 4 walls exposed to the exterior
Lpf...........
Do you have summer cooling capacity...? Dehumidifier?
Dig a pit in the CS....say 12-18" deep. See if it fills with water. Grab a handfull of the excavated dirt...is it dry....moist......gooey.....sopping wet? Sample addition areas to see if the conditions are overall consistent or just localized.
Buy a humistat and place it inthe CS to determine how much humidity you really have. If we know the temp and humidity of the CS the dew point can be calculated. The dewpoint will tell us if your CS needs to be conditioned and if your insulation plans are reasonable. Likewise obtain the readings in the basement and upstairs living areas.
Plastic on the bottom of the joist may actually generate another moisture problem in addition to what CS problems that you have. Be cautious as the where and how you apply moisture barriers, as they also can be moisture traps.
Is there any foam insulation applied to the poured concrete CS walls?
Describe in detail the CS vents that have been installed. Size, material, and if they are thermostatically activated. Does your city codes mandate a"vented crawlspace?
A general rule of thumb at the exterior of a house is that the bottom piece of siding should be 6" above the dirt/sod/gravel and from that point out and away from the house there should be another 6"drop in elevation in 10 feet.
During the next rainstorm, put on a rain coat and waterproof shoes and wonder out side and observe where and how the rain water flows and or puddles at your house perimeter. At the same time observe how well the gutters handle water dispersal and if they have been hung as to flow properly to the down spouts and not overflow at the center of a long run.
Power venting a crawlspace has its own set of "issues", such as where are you pushing the damp humid air and where is the "make-up air" coming from. A system could work perfectly well in the Chicago summer time, but be a farce in the winter.
Sorry for more questions, but to achieve a good solution lots of information is needed to arrive at a reasonable fix and not create another problem.
..............Iron Helix
Sounds like you are tuned in to the rain gutter issue and will work toward mitigating issues there. That's important.
The poly on the crawl ground ... definately should be continuous, so yes, check it and remedy it.
I agree w/ Iron re: poly on the bottom of joists ... DO NOT do that. Vents should be operable for Chicago land ... closed in winter, open in summer.
Consider also insulating walls/rim w/ e.g. foil faced polyiso - may be the only legal rigid insulation that you don't have to fire protect (a BO would say for sure what your options are, though). If you insulate walls, you MUST have operable vents or your wasting your time.
Power vent the crawl ... by dragging air through the basement? Yes, but only under certain conditions. Wouldn't recommend it in general or as your primary means of controlling moisture. When/if you finish the basement, much of the 'smell' should disappear.
I wouldn't necessarily attempt to heat the crawl. You want to heat the basement? The crawl is open to the basement at the old window, right? Maybe a lot of your musty smell is from the crawl. After mitigating the gutters and ensuring a poly ground cover, consider closing off the crawl ... e.g. removable access panel over the window. Crawl by code usually must always have access.
food for thought ... hope it helps a little
O.k... Couple questions. The walls around the footing in the crawlspace are not insulated. So I was thinking about using some kind of foam board such as an owens corning foamular type system. Which seems to be a modular system that has a tongue and groove. Now the question becomes how do I attach it? I believe that some people use glue, but that might deteriorate after a while. So the next type of fastening would be a ramset, cut nails, or tap-cons. Any suggestions? Also, there is a couple different thicknesses available, should I go with a thicker (meaning higher R value) or does it not really matter. I have read some back issues of Fine Homebuilding and see that instead of insulating with typical roll type insulation and a moister barrier, they recommend foam board, then sleepers, then drywall. Would it matter if I use the foam board, then maybe 4-5 inches out I have my 2x4 stud wall and then the drywall?? BTW I did check the ground in the crawlspace and the moisture barrier does go around the entire floor. It's kind of a thinner ML than what I was going to use.. Should I use another one on top of it? Then finally.. The grade outside this crawlspace is pitched in toward the house a little bit. I have some trees that I was going to cut down and mulch.. Instead of top soil around the perimeter, would mulch be o.k? I was thinking that the wood would absorb the rain water. Keep in mind it's not a dramatic pitch. Thanks guy's!!
I think you should read up at Building Science website or get their book on building for your climate. It's all spelled out with numerous examples.Foam insulation is only effective inasmuch as its sealed-in
airtight, so I don't like cut nails. That's why adhesive is good, because it seals it against the concrete. Maybe better is thinset or other cement adhesive applied with a notched trowel.
Landscape mulch is not necessarily the answer to your drainage problem.
The 6" below the siding and 6" of fall in the next 10' run away from the foundation, still is the best circumstance.
Putting mulch against your siding/foundation intersect is asking for moisture problems as well as inviting critters into your wall and floor system. Mulch holds water...the opposite of what needs to be happening as per yor description.
Mechanical fasteners through 2" of foam should give your crawlspace what it needs. Adhesives can fail due to several reasons. All the specs from the architects I work with call out mechanical fasteners as a minimum.
Also you need to upgrade the insulation installation at the box sills. Your local codes may require the foam to have a fire rated covering.
What is the moisture content of the soil in your CS? Do you intend to condition/ ventilate, etc.?
.........Iron Helix
Using the Foamular is fine ... but check w/ the BO, too. You don't want to create a fire hazard. Attaching it ... always an issue. Glue should work (e.g. constructiion adhesive ... they use it to glue sheetrock to concrete, etc. You have to clean the substrait. If you can, you could friction fit and then backfill a little against e.g. the bottom 2-3 inches to help secure the bottom (the top being friction fit to the rim). ... just a thought ... no experience.
It might be easier to clean and glue insulation stick pins to the wall and secure that way (standard detail in commercial construction); you only need maybe one row at about the middle and then you only have to clean about 2 sqin of wall per pin.
You have an insulated floor, too? If so, simply use 2 inches of foam. That's probably all you need anyway.
Not sure why you are contemplating a framed wall and sheetrock. Don't think you need this. Sounds like a lot of work.
Re: the drainage ... hmmm doesn't sound to me like a good way to ensure drainage. Make sure your gutters drain to a point well away from the house (extend them below grade if necessary w/ flex drain pipe). I wouldn't rely on the mulch to simply 'absorb' the water to control it. That's my opinion ... no expert in draining, but I know Chicago can get some serious moisture ... MUCH more than Seattle (which is really a myth).
"always an issue. Glue should work (e.g. constructiion adhesive ... they use it to glue sheetrock to concrete, etc."You need to check the label on the construction adhesive.Many of them have solvents that will attach the foam..
William the Geezer, the sequel to Billy the Kid - Shoe
solvents that attach [to?] the foam??? Good, I think. We do want to attach the foam to the walls. Am I missing something??
Methinks he meant "attack" the foam.
Yes, of course. I thought I've seen standard construction adhesive used on polystyrene before. I may be wrong. I was wrong once ... I thought I was wrong, but I was really right! ;)
Yeah, it could be an issue. Always good to do a reality check.
Yes, I meant ATTACK the foam.And in many cases the problem is not immediate, but in a few years you will find it falling off and glue "tracks" etched in the back.But many did not.I know that PL Premium does not..
William the Geezer, the sequel to Billy the Kid - Shoe
The framed wall and sheetrock is for the basement area not the crawlspace. Thank you guys again for the advice.,, Following that I went to buildingscience.com and they actually say that NO venting should be allowed in the crawlspace, due to the fact that the moisture from the outside would be allowed to come inside. Makes sense. I am on my way to buy a humidistat like you guys suggested, and when I do I will post the results. As far as friction backfilling, there's a small ledge under the knee wall (crawlspace wall) that I would imagine that I should just butt the foam boards up to. As far as going up, from what the site suggests I should use the foam board between the joist bays, around the ribbon. Then I would imagine that I would insulate the run of the joist bays with the R-30 that I've purchased
Another question.. I've painted the walls (in the crawlspace) with UGL basement paint.. Now I'm getting ready to install the foam board around the perimeter of the crawl. Was the basement water profing paint a bad idea? And also from what building science.com is saying.. I should NOT insulate the joists between the crawl and the floor above it. Would it hurt to? Also like I posted earlier.. They are saying that there should be NO venting whatsoever in the crawl space. What do you guys think?
Not sure why they would say to not insulate the rim joist. That is as normal as anything whether insulating the floor or the crawlspace walls. Don't recall your location ... re: venting. I'd talk w/ the building official. If venting is normal/required, then do it. Operable vents allow you to control venting seasonally. If you have poly on the crawl ground, you may not need to vent, but usually poly is not continuous, so venting is desireable at least during some periods. Talk w/ the BO and let him give you some direction. Not venting is good energy wise, but venting is a moisture issue.
Iron Helix is right ... need LOTS more information, here. Foundation vents are required in many locations ... by code ... and for good reason. Consider an operable vent as an alternative ... gives you the option of venting seasonally.
Why isn't the poly on the floor 'visible'? Sounds like you know it's there, but aren't real sure ... so 'splain yourself a bit more.
Moisture often is from the ground and if you block vents, you block the ability to dissipate that moisture. What are you insulating to R-30?
What is the foundation walls? Concrete? Answer Iron Helix questions ... get this ball rolling a bit more ... we can't help w/out information.
I should dig up the gravel a bit more.. But it seems like the poly is only in a certain area. I'll answer that tomorrow.. The R-30 is going between the joists for the floor above the crawl. The foundation walls are concrete. And there is no sump. Right now I have to fix the downspouts because they seem to be leaking into the crawl. After that is taken care of I'm hoping that the moisture will stay out of there. Right next to the crawl is a full basement with the former basement window leading into the crawl space (the crawl was part of a new addition) and I would also like to somehow get some kind of fresh air system into the basement to get rid of the basement kind of smell. We have radiant heat at the house so running some duct work off my furnace isn't an option. Any ideas for that one?