I’m still in the process of trying to figure out how to go about insulating the sloped ceiling areas on my second floor. This is a living space with 2 full dormers. The rafters in the house are 2×6 which have been firred out another 1-1/2 inches (using a 2×4 ripped in half). Between the rafters (which are all on odd spacings) currently there are proper vents and R-19 paper faced or non-faced fiberglass. Then, a 6 mil vapor barrier and 1″ foil faced rigid insulation then 1/2″ sheetrock. Currently with the R-19 and 1″ rigid, there just isn’t enough insulation to prevent warm air from getting up to the roof, causing some nasty ice dams. There has been talk of taking everything out – back to the rafters – putting in new proper vents and installing 5 inches of closed cell spray foam. But, there is also talk of leaving everything in place, installing 3/4″ strapping, followed by 2 layers of 1″ rigid and a new layer of sheetrock. The cost of taking everything out and putting in the spray foam would be quite a bit more than just leaving the existing setup in place and going over it (or under it? as the case may be). Is there anything wrong with the latter method I described? Would there be problems down the road? One other thing I should mention – the proper vents and insulation I put in myself and discovered recently that I may not have installed the vents properly. They don’t quite fill the cavity and they don’t extend out into the soffit quite far enough. So, while there may be proper vents, they may not be working to their full potential. My initial thinking was that everything should be ripped back to the rafters, get the proper vents installed the right way and then try to maximize the insulation R-value, whether it be spray foam or rigid or a combination of products. Any suggestions would be greatly appreciated. Thank you.
Discussion Forum
Discussion Forum
Up Next
Video Shorts
Featured Story
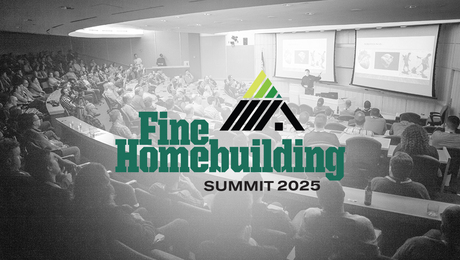
Join some of the most experienced and recognized building professionals for two days of presentations, panel discussions, networking, and more.
Featured Video
Builder’s Advocate: An Interview With ViewrailRelated Stories
Highlights
"I have learned so much thanks to the searchable articles on the FHB website. I can confidently say that I expect to be a life-long subscriber." - M.K.
Fine Homebuilding Magazine
- Home Group
- Antique Trader
- Arts & Crafts Homes
- Bank Note Reporter
- Cabin Life
- Cuisine at Home
- Fine Gardening
- Fine Woodworking
- Green Building Advisor
- Garden Gate
- Horticulture
- Keep Craft Alive
- Log Home Living
- Military Trader/Vehicles
- Numismatic News
- Numismaster
- Old Cars Weekly
- Old House Journal
- Period Homes
- Popular Woodworking
- Script
- ShopNotes
- Sports Collectors Digest
- Threads
- Timber Home Living
- Traditional Building
- Woodsmith
- World Coin News
- Writer's Digest
Replies
(There's a button just above the right-hand shift key on your keyboard. Maybe you should use it on occasion.)
If the problem is ice dams, there are two possible causes. One is too much heat getting though the insulation, and other is insufficient cold-side ventilation.
Your existing insulation is not enough to prevent ice dams with your existing ventilation and insulation. Improving either your venting or your insulation, or improving both will eventually eliminate ice dams. If your ventilation were properly installed and reasonably adequate; and if your fiberglass were properly installed, it would make sense to just add more insulation on top of your existing system. However, it seems rather doubtful that the make-or-break threshold is so specific that 2” of foam will make the difference between ice dams or no ice dams.
Even if the existing insulation and/or ventilation has defects, if you add enough insulation to the room side, you will eventually prevent ice dams, but that may take much more than just 2” of foam.
So if there is any question about the quality of ventilation and/or fiberglass installation, I would consider tearing that existing system out and redoing it perfectly. That way you will know you are getting the most out of it before you continue thickening up the insulation toward the inside.
You say the rafters are random spacing. How did you fit fiberglass into those spaces? Did you custom cut the batts to fit the spaces? That fiberglass should fit tightly between the rafters and fill the whole gap throughout the 7.5” space depth. I have seen it rumpled and rolled down where it touches the rafters in order to make it stick in place. You can’t allow that.
After tearing out the existing system, you could tightly press two sheets of 2” foam into the gaps between the rafters, and calked the joints. Although that would require sawing the foam to fit since the rafters are irregular spacing. Then you could add another inch of foam over the room side of the rafters. That would add more R-value and help reduce the thermal bridging through the rafters.
Then make sure you have ventilation inlet and outlet flow on the cold side of the insulation passing though that 2-3” air space under the roof deck for all of the rafter bays. If you do all that and make it first class, tight, and sealed, I think you will dramatically improve what you have now and minimize, if not eliminate ice dams.
You wrote
a lengthy post on ice dams without once mentioning air sealing. Here is an authoritative article on the topic: http://www.greenbuildingadvisor.com/blogs/dept/musings/prevent-ice-dams-air-sealing-and-insulation
random spacing on rafters
This house was built in 1952 for $400 - a do it yourselfer. We are the second owners. All of the rafters and studs are at random spacings. Yes, insulating this place was a challenge. We had to custom cut each piece of insulation to fit each space.
I was thinking if we were to use 4" rigid - cut to fit tightly- we may not need to install any proper vents on the cold side, as the face of the rigid would be flush with the faces of the rafters and there would be enough air space behind it. We could then put a 1" or 2" rigid on the room side - caulking and sealing any gaps. We would still need a vapor barrier installed if we go this route - is that correct? My understanding is that if we go this route, there will be quite a bit of labor cost involved due to the custom cutting for each piece to fit properly.
If you installed 4" of rigid
If you installed 4" of rigid foam flush with the inside edges of the rafters, you would have about a 3" air space on the cold side. That is fine for the vent air flow. The idea is to wash the underside of the roof deck with cold air. But for the ventilation to work, you need inlets at the low side under the eaves and outlets at the high side at the ridge. I am not sure what you have for these inlet and outlet openings, or if there would be any difficulty in creating them if they don't now exist. But if you can provide those vent openings, I think it would be a good idea to so. Otherwise, without those openings, the air chutes behind the insulation will not serve any purpose for ventilation.
It is possible that you could get by without any ventilation with 4" of foam if it were tighly installed and sealed. But rather than gamble on not needed the ventilation, I think it would be better to create the ventilation if it is doable.
I have never put in 4" rigid foam board. Two sheets of 2" foam might be easier to get tightly fitted. The random spacing will require custom cutting of the foam, but another issue is the consistency of the space width. If the rafters are within 1/8" or so of being parallel, you can cut the foam on a table saw. You can cut the foam a little oversize, so it presses into the space. Pound it in with a mallet and a piece of plywood to spread the impact out on the foam sheet. If the rafters wander too much in their spacing, the foam may leave some gaps if you cut it with a constant width on a table saw. That might still be okay as long as you can get the pieces secure enough to hang in place. You can caulk the joints and fill the gaps. You would just have to play the fitting by ear.
I would get foam with foil on both sides, and leave about a 3/8" space between the two sheets of 2" foam, and between the sheetrock and the foam. A final sheet of 1" foam over the rafter faces under the sheetrock would break the thermal bridge of the rafters, and add some more R-value. Leave a 3/8" gap between the 1" foam and the next sheet of 2" foam. Then you would have five shiny radiation barriers and two trapped air spaces that will boost the R-value.
If you sealed the seams of the 1" layer, you could probably get by without a separate film vapor barrier, but the film would be added insurance. I don't have any feeling for how big of an area you will be insulating. The custom cutting will be a lot of work, but if you get an efficient routine worked out, it should not be too bad. With a little care, you should be able to do an excellent job and have enough time to control the quality as you go.
inlets and outlets
The house is 24x26, but even though it's small, nothing was consistant when it was constructed. When we bought the house we had to gut the entire place and start over. THe original owner built it for only $400. It was never finished and never kept up. So each bay, between rafters and between studs, is a different width. It was quite a challenge to insulate.
There are soffit vents, gable end vents as well as ridge vents. Unfortunately the soffit is not extended very far out from the house. When we bought the house the roof line was flush with the house and the rafters had to be extended - they just weren't extended out enough. At some point, when money allows, I'd like to extend the soffit out more.
Which would give us the higher R-value - the 3 layers of rigid with the 3/8" gaps you suggested, or 5" of closed cell spray foam (with an adequate proper vent installed)? I think the spray foam would give us about an R-34.
If you can afford
to remove everything and install closed cell spray foam directly to the roof deck. do that. Trimming the foam flush and installing a layer of rigid under the rafter will give you a big improvement in thermal bridging. Trying to cut and install three layers of foam with air gaps is nuts, in my opinion, unless your time is worth nothing. You are as likely to create problems that way are you are to get results.
Compare two approaches
It is a relatively small space, so I don't see a problem in doing the work yourself. It is a matter of your time, but it sounds like you have been willing to put your time into it in the past. But if you save your time, you be trading it for your money. Get a quote on spray foam and price the foam board product. You can cover the bottoms of the rafters to reduce thermal bridging with either approach.
With the foam board, you have to control your quality. With the spray foam, you have to trust the installer to control quality that you may not be able to see. With either approach, the R-value could be compromised depending on the quality of the job. Inherently, the R-value would be the same per inch. The R-value of spray foam can vary with the mix, and diminish over time, whereas foam board is quality controlled in manufacturing and maintains its R-value over time.
With foam board, you will have less inches of insulation plus an air space for ventilation. With spay foam, you will have more inches of insulation and no ventilation. If the foam is installed properly, you won't need ventilation.
The radiant barriers provided by the foil faces in the foam board approach would provide additional R-value beyond the basic foam R-value. I can't give you a number on it, however. I doubt any two people would agree on the number. Moreover, many people do not understand how foil insulates.