Interesting Question about Framing Design
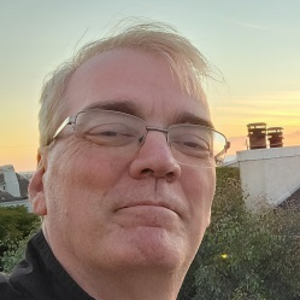
I have been thinking about a new framing design that allows me to pre-fabricate parts of the framing and add strength to the frame for geologically active areas. I would like as much input as possible on both pros and cons for this idea so I can figure out if it is possible to use it.
The basic idea is to create a vertical truss style frame item that can be pre-fabricated and nailed to a sill plate. A row of them would then make an automatically braced frame structure (see attached image). Each frame item would have holes drilled in the plates, ribs and cross members to allow conduit to be run in horizontal and vertical directions.
Materials used to create this type of framing item:
1) 2×6 Douglas Fir #2 or better
2) Simpson Strong Tie flat connectors
3) 16D nails for shear points and construction screws for tensile points (you can see where each might be needed from the image)
After the framing is complete 5/8 or 7/8 OSB can be added to the exterior wall frames to create a shear wall. I think this type of framed structure would have better resilience against geological activity.
I AM NOT an architect, so I do not know if this idea is a waste of time or the smartest idea since sliced bread. I just want any thoughts from the world out there.
Thank you in advanced for your help and thoughts.
Tom
Replies
Looks like a ton of lumber to me. Probably oversized and extermely strong. Also expensive and not that thermally efficient.
I agree on the thermally inefficient thing. The price was not that bad. I have thought about an assembly line approach, cut multiple pieces at a time, drill holes using a jig, frame it together quickly and efficiently guaranteeing standardization of each component. The cost compared to stick construction was only 15% to 20% more expensive.
I think the wall would need some type of additional sheet insulation (3/8 or 1/2 inch 4x8 ft)
Thanks for the input. Anything else is appreciated.
Tom
Tom it's probably 15-20% more in material but it looks like 100% more in labor.
There is a reason we build the way we do. What you are drawing might be a significant structural improvement but its not efficient in time and material and energy.
Steve,
I did not consider the overall labor cost of the prefabrication. Renting a small warehouse to build these, storage, etc will increase the price per component. I will be building a custom home in a about 24 months, thus my question.
Thank you for the input.
You are looking for a solution to a problem that doesn't exist. Prefab panelized construction is already an accepted thing. By "geologically active" I assume you mean seismic areas. You seem to think that all these diagonals will resist these loads differently than shear panels. These are the same loads -- that's what shear panels are for. You certainly don't need 5/8 or 7/8 osb. If you want to build prefab panels just use studs @ 16" oc. Use a single top plate so that a second can be added after the panels are in place to tie them all together. If you are building 8' walls you can make the panels as long as you choose, depending on how large you want to handle. If your walls are taller than 8', you should build panels no wider than 8' so they can be transported as a normal load. As you prefab the panels use 3/8 plywood sheathing. If you want to increase the shear strength use struc. 1. You can easily predrill the studs. Drilling horizontal and vertical holes through all those diagonals looks like a bitch to me, even in a shop and not on site.
I would have to agree with others here that replied to you in that we already have techniques and approved processes for building structures for earthquake zones. We even have Structurally Insulated Panels (SIPs) that are composed of layers of OSB on the outside structural polyiso foam, another layer of OSB and a final interior layer of wall board. This has been going on for more than 20 years. My brother had a home built in New York State using this method with interior post and beam framing. The windows and door location were painted on the exterior layer of OSB to show were the window and door openings were to be cut and framed after removing a few inches of the foam in the perimeter of the windows and doors. The layers of OSB were then nailed to the framing. The SIP were screwed to the exterior facing surfaces of the posts and beams.
There is Efficient Building construction that uses 2X6 on 24 inch centers along with single layer mud sills and top plates covered with structurally rated 1/2 inch to 5/8 inch plywood or OSB that is also covered with a WRB layer that could be built in a warehouse under controlled conditions with everything nailed/screwed/ bonded together and insulated. The final insulation should be on the outside to prevent thermal bridging. All of the wood in the wall provides a path for heat to leave the structure even with insulation in the hollow spaces. That is why exterior insulation is so effective. External insulation prevents thermal bridging. In fact the most effective insulation is that on the outside even if there is no insulation in the hollow wall spaces.