*
FredL-As a P.E., I take exception to your solution to “overbuilding” by going to the next size I beam versus hiring an engineer. Did you check your beam for lateral buckling?. Do you know how to interpret the AISC manual to know if your section is compact or not? An engineer’s fee can sometimes be the best money you ever spend, particuarly if you are looking back in hindsight from the vantage of a courtroom. Competent engineers do not overbuild to cover their ass, nor charge exhorbitant fees to save you a lot of “thinking effort”. We are paid to exercise our engineering judgement, training, experience and common sense to solve problems in as expeditious and economical way for the client and, in many cases, save normally well-intentioned people from making disasterous and costly mistakes. Perhaps your clients steel footbridge is doing just fine due to your “overbuilding”, but it is not advice I would follow.
Mike M.- You raise some interesting points. I disagree that Codes are meant to be minimum standards. Codes are meant to protect life and property in that order. They are constantly revised and generally improved to more efficiently utilize the materials of construction. Often natural disasters point out the deficiencies in our codes as evidenced by Northridge and Andrew and the codes are reviewed and improved if necessary.
Insofar as your need for a PE to do your lateral analysis: Why would you ask the PE to increase the loads beyond the Code requirements? A good PE wouldn’t nor should you. And you apparently take some comfort in the PE’s “butt and insurance” being on the line vs. yours. Thats what we get paid for, to do the calculations that the State licenses us for and then stamp your plans with our professional liablity.
Discussion Forum
Discussion Forum
Up Next
Video Shorts
Featured Story
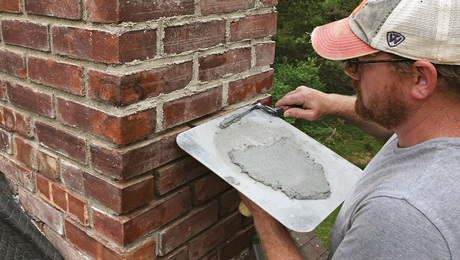
Old masonry may look tough, but the wrong mortar can destroy it—here's how to choose the right mix for lasting repairs.
Featured Video
How to Install Cable Rail Around Wood-Post CornersHighlights
"I have learned so much thanks to the searchable articles on the FHB website. I can confidently say that I expect to be a life-long subscriber." - M.K.
Fine Homebuilding Magazine
- Home Group
- Antique Trader
- Arts & Crafts Homes
- Bank Note Reporter
- Cabin Life
- Cuisine at Home
- Fine Gardening
- Fine Woodworking
- Green Building Advisor
- Garden Gate
- Horticulture
- Keep Craft Alive
- Log Home Living
- Military Trader/Vehicles
- Numismatic News
- Numismaster
- Old Cars Weekly
- Old House Journal
- Period Homes
- Popular Woodworking
- Script
- ShopNotes
- Sports Collectors Digest
- Threads
- Timber Home Living
- Traditional Building
- Woodsmith
- World Coin News
- Writer's Digest
Replies
*
Fellows,
I knew a guy once who sheathed all the interior walls and ceiling of his mobile home with recycled 5/8 ply (from concrete forming) and then drywall. He said he wanted a quieter, more solid, stronger home. He got quieter, felt more solid, can't say about stronger. Was it overbuilt? Yes. Was it any less a tornado appetizer? No. But shows that both Fred and Mike are right. My friend's problem, and I think the real issue being questioned here, is that he was trying to "fix" a bad system.
Many times it seems that "upsizing" part of the system will achieve what we really want - a home that is safe in fact AND feel, that will be there for 3 centuries. The problem is that this upsizing isn't going to fix bad design, or even a poorly thought out construction system, especially one that doesn't have backups or failsafes. If you are going to overbuild effectively, you need to start at the begining, not halfway through. Fred did with his drain thing, and it worked, my friend didn't with trying to "fix" his house (a bad system) and it still got munched by a storm.
There is the debate between 2x4 and 2x6 stud walls. Are 2x6 overbuilt? Are 2x4 underbuilt? Perhaps it is the stick system rather than the size of the sticks. Gene L talks about his search for a better stick framing system, that is easier and cheaper and better insulated and USES LESS MATERIALS. This is because he discovered that with the staggered stud or doubled walls, he didn't NEED 2x4, so he switched to 2x3 and still got a stronger, tighter, solider wall. He says he's got an even better system going, but he hasn't spilled the beans yet. (Hey Gene, whats up?)
Also, look at seismic and hurricane protection. It is how the whole system of walls, roofs, and floors work together that determines success or failure. As Mike says, we should look at upgrading (by increasing load requirements) the system, and not a part of it.
And by the by, Fred Matthews, while the codes before Andrew were definately on the skimpy side, it was FAR AND AWAY the sh***y construction practices, the corrupt and nonexistent inspections, defficient zoning, and the unmittigated greed of the McDevelopers that precipitated the damage. Obviously the codes didn't do the job because the imperative ingredient, concientous people, was missing.
Perhaps overbuilding (as a negative term) should be defined as oversizing a material WITHOUT CONSIDERATION OF ITS EFFECT ON THE CONSTRUCTION SYSTEM AS A WHOLE. Upgrading is the improvement of the system as a whole through redesign and improvement in material efficiency (strength, placement, amount, use, etc.).
Just my 2 cents,
Lisa
*
Fred brings up an isue that I referr to as "perceived quality." This is a concept taught to me in plastic injection molding classes. Lighter partrs are better from a manufacturing point of view, but added mass appeases the consumer because the part "feels" right even though it is no stronger. And in my experience it will probably break anyways - so don't buy plastic 8-).
This brings up an issue of standards. Someone has to maintain standards even though it is a thankless job. Take an architect. They pick colors and fixtures and light spacing, etc. etc. In the filed that all serves as a starting point, and what gets built is something less substantial. So what would have happened if no one set the standrads in the first place? Who judges how well something is built? Is it the builder who knows, or the consumer (the one with the money). Do you build quality for the sake of quality, or do you build perceived quality to make a happy customer and maybe repeat business.
I for one am for higher standards, but so are the few people I have worked for so it has been easy so far.
-Rob
*Mike answers it all with the last two words in his first paragraph..."arbirtarily overbuilding". Other poster children have taken and expounded on this.To me "Fine" is not just using, bigger, better, thicker, or increased quantities of because you can. It's giving the end-user a BETTER, more EFFECTIVE PRODUCT at a reasonable cost.Code is code. It's a minimum. Today's minimum. You can "overbuild" for tomorrow, you can "overbuild" for peace-of-mind, you can "overbuild" because of a problem you as the builder or the homeowner experienced in the past. However, have a reason. As Mike wrote, don't do it "arbitrarily".
*
It was with some shock and dismay that I discovered, some years ago now, that my provincial (Ontario) building code no longer required diagonal bracing in any form or any sort of blocking in exterior walls, and that drywall was considered acceptable racking reinforcement in residential construction. Unbeknownst to me, and any contemporaries I questioned, those requirements had been abandoned sometime before 1990.
Even though we are not subject to hurricanes,tornadoes or earthquakes of any significance I have never felt comfortable with these changes and never ceased sheathing the exterior walls of all new construction with 1/2" ply, nor stopped putting in solid blocking (diaghram ?)at the appropriate spot in exterior and interior walls and floors. Overbuilding? Upgrading? Making myself feel better? All of the above I guess. For me the code has come to represent the Bare Minimum that my slipshod contemporaries can get away with. Do I get under bid? Does the sun come up every day? I think that anything that I do that improves upon the 'structure' is neither a waste of time or materials, but I fully agree with the observation that a wily-nily approach is at best questionable. Not every potential customer understands this or for that matter wants to understand.
Solid as a rock, with no apologies.
Patrick
*I am seeking information about insulated concrete form construction such as experiences with termites, ease of construction versus "stick built", insulation values.
*
Overbuilding is something we deal with as architects and builders. Codes are "minimum" values most of the time.
Code values are not always adequate for earthquakes all the time for instance. They do not allow for the weight of the furnishings in a home for instance, or the weight of walls paralell to the direction of the force you are calculating. Although as a practical matter, these loads contribute to the forces acting on a building durring an earthquake. Often earthquake design by code only insures that the building holds together enough for the occupants to get out, and does not mean the building will survive as an occupiable space.
It depends on the "use" of the building whether it should be overbuilt. For instance, a cooperative market on the warves in Kobe, Japan was overbuilt by a factor of two, but it survived that earthquake and stayed in business. Keeping many small businesses intact and supplying the public with food.
There are times when designers deliberately overbuild to give homeowners an overwhelming sense of security. For instance, the wide elephant-foot shaped columns on bungalow-style front porches. Technically, a skinny steel column or 4x4 or smaller post would have been adequate as long as the connections were good, but the "look" would not have been right.
In my own home, the builder didn't get it quite right. There is a 4x12 summer beam throught the center of the living room carrying the second floor (2x6's)above. They built massive elephantine columns in the room to carry the beam but put the 4x12 in the flat or weak direction and it sags.
They say they don't build them like they used to, but the image of quality we get from the past is an illusion. Most of the realy BAD stuff has already been torn down or covered up. Even if something is overbuilt, if they don't get the details right the extra effort is futile. The homeowner through house payments pays several times the original cost of a project and deserves appropriate consideration. Overbuilding doesn't always help.
*
Sirs, It seems to me that any activity that uses as many resources as Homebuilding brings with it the responsibility to utilize those expended raw materials in the most effective way possible. That doesn't necessarily mean that 'over building' is bad. Anything that markedly extends the useful life of a building has the potetial of making it less expensive per unit of use. Houses with a design life of 30 or 40 years are under built no matter what code criteria they may meet. If we build for the long term with the hope that down the line our houses merit restoration by some future generation of craftsmen then any slight and unintended overkill will eventually prove to have been worthwhile. But that's just my opinion, I could be wrong.
*
Following Steve Jackson, it seems like we would need to ask the question "What are we building for?" before we could know if we were overbuilding or not.
Is this a mindfully designed and constructed social investment of time, materials, resources, and skill for the sake of posterity? I've worked on some houses like this, and it was a priviledge. Is it a pretext for cash flow so someone can make money? We've all had to repair these. I almost ended up buying one, billed as "affordable" housing. I usually feel like whoever built these houses (to code) ought to be tried and convicted for all kinds of bad things, not the least of which be the killing of trees for no good reason. Oh, and let's include aggravated assault on public sensibilities.
Regarding such structures, someone once said to me "What do you care? You'll just live there 5 years and sell it." Like that makes it OK.
Are we just providing shelter?
Are we building a monument to an architect's ego?
Are we trying to provide the most inexpensive housing we can? Does it need to be beautiful? Energy-efficient? Well appointed? Earthquake and hurricane proof? Environmentally responsible? Use a minimal amount of materials? Profitable? Capable of lasting 300 years? 100 years? Until the mortgage is paid? Until I get out of the parking lot?
Sometimes compromises are OK, sometimes they don't work for anyone. I quit buying anything that says "one size fits all". It usually doesn't.
So where do we put the priorities? We've all seen houses "built to code" that were nothing to be proud of. Design (ideally) implies a function or purpose. Codes are a good point of departure, but hardly seem sufficient as criteria.
*
Lisa : You may be right that sh***y construction practices contributed to the damage from Andrew, but a lot of valuable lessons were learned about the pullout value of staples in OSB in the aftermath. We'll always have to deal with the incompetent tradesperson/inspector and those that enforce codes but don't comprehend the "why" of the rules they enforce, or engineers who don't have the common sense God gave a rock. But I always feel there is hope and bright, conscientious souls out there building when I read these discussions.
*
It seems to me that the comments of an aquaintence who is a welding inspector are pertinent here, despite the difference in trades. To wit: A weld fails with too little material because it doesn't meet design requirements. It fails with too much material because it wastes time, money and material and may conceal a defect.
In my experience "overbuilding" is practiced by folks who really don't know what they are doing but have a good line as a disguise. The fellow who said design it right and build it to design is right on.
*I'm with Fred here. Better to build it right than to show off by trying to "overbuild". There are so many things not done right in modern home building. Why not focus on doing things right, than in trying to make a few things look impressive.
*We seem to have gotten into one of those nasty circles with the dog chasing it's own tail. Are semantics involved? Fred and Ron both seem to be saying all structures should be built to design. Well, what if the design is flawed? What if the design is MINIMUM code. In that case (assuming non-engineered), why not "overbuild". Is it wrong to build better then the design to eliminate potential problems?Does one need to exceed code in all facets? Absolutely not. But there are areas where I ALWAYS exceed code. History and experience make that a smart thing for me to do. I build two houses, each identical...With the first, I am involved in the planning/design stage. With the owner's blessing it is designed to my minimums. I build it as designed. Have I overbuilt?The plans for the second are handed to me, the house is designed to the minimum code. I upgrade as I go along, exceeding the design in certain areas. Have I overbuilt?Is building to current code minima underbuilding?I still agree in principle with Steve and Dave's posts. Their posts in turn reflect, once again, on the last two word of the first paragraph of Mike's original post. "Arbitrarily overbuilding" can be bad. But, overbuilding (which I define as exceeding code) can be a good, and sometimes neccessary thing if it is done for a purpose and with proper destination in mind...
*I posted these before and have just posted them again in another thread. But here they are again.UVA Architecture Publications THE HANNOVER PRINCIPLES 1. Insist on rights of humanity and nature to co-exist in a healthy, supportive, diverse and sustainable condition. 2. Recognize interdependence. The elements of human design interact with and depend upon the natural world, with broad and diverse implications at every scale. Expand design considerations to recognizing even distant effects. 3. Respect relationships between spirit and matter. Consider all aspects of human settlement including community, dwelling, industry and trade in terms of existing and evolving connections between spiritual and material consciousness. 4. Accept responsibility for the consequences of design decisions upon human well-being, the viability of natural systems and their right to co-exist. 5. Create safe objects of long-term value. Do not burden future generations with requirements for maintenance or vigilant administration of potential danger due to the careless creation of products, processes or standards. 6. Eliminate the concept of waste. Evaluate and optimize the full life-cycle of products and processes, to approach the state of natural systems, in which there is no waste. 7. Rely on natural energy flows. Human designs should, like the living world, derive their creative forces from perpetual solar income. Incorporate this energy efficiently and safely for responsible use. 8. Understand the limitations of design. No human creation lasts forever and design does not solve all problems. Those who create and plan should practice humility in the face of nature. Treat nature as a model and mentor, not as an inconvenience to be evaded or controlled. 9. Seek constant improvement by the sharing of knowledge. Encourage direct and open communication between colleagues, patrons, manufacturers and users to link long term sustainable considerations with ethical responsibility, and re-establish the integral relationship between natural processes and human activity. The Hannover Principles should be seen as a living document committed to the transformation and growth in the understanding of our interdependence with nature, so that they may adapt as our knowledge of the world evolves. copyright © 1992 William McDonough Architects
*
The notion has been expressed by others in this forum, that "fine" home building involves something more than just "building to code". The idea that the structural requirements of the various building codes are minimum standards is basically true, but it strikes me as somewhat naïve to think that these can be improved on in any meaningful way simply by arbitrarily overbuilding.
Building codes define maximum loads that a building can reasonably be expected to incur. These are: 1. Loads caused by gravity. The dead load of the building itself and live loads expected to be imposed on it by the type of occupancy. 2. Lateral loads caused by wind or seismic forces acting on it. Although wind and seismic forces occur in different ways, the way the building resists these is the same. Therefore it is not designed for both, but for the greater of the two.
Gravity loads are resisted in shear, in bending and in deflection. Failures in shear or bending are essentially catastrophic failures. The member will either resist or fail. In deflection a member must not exceed a certain limit, usually 1/240 or 1/360 of its span. Failure occurs when deflection exceeds the prescribed limit. Resistance of lateral loads is significantly more complicated. It involves multiple building components working together to transfer the loads to the building foundation.
A building can be designed to resist these maximum loads in one of two ways. Through certain prescriptive measures, or through specific design i.e. engineering. If the building official accepts prescriptive design it is because he or she feels it is more than adequate for the loads. If there is any doubt then engineering should be required. An engineered design is more likely to be closer to the so called minimum, because it is essentially not over designed.
Over building of gravity design makes a certain amount of sense, because it will decrease the limit of deflection under normal loading. But there is no assurance that it will increase the maximum design load. I will not build a floor with joist spacing greater than 16". I use 5/8" t&g plywood floor sheathing. I have never once felt, or had a client feel, that this resulted in anything but a solid floor. If the floor will be tiled I will oversize the joists by 2" and use ¾" plywood. In certain cases, if the tile will go directly to the plywood, I will use 1 1/8". I use 3/8, 7/16 or ½ inch plywood for roof sheathing and have never once had a problem in almost 30 years of building.
Over building of lateral design makes very little sense, since in involves many systems working together. I engineer all my houses by computer program, and if the building official requires have the lateral analysis done by a PE. I generally have it done so that the PE's butt and insurance are on the line rather than mine. I have never told an engineer to increase the design loads above the code requirements. Nor have I felt that the engineer's design could be improved upon. Somehow, it has never occurred to me that a shear panel with 7/8" x 34" anchor bolts imbedded 28" in a 30"+ deep footing, with HD10a hold downs, 6x6 boundary members, and 7/16" osb nailed 2 and 12 could be improved just by using 5/8" plywood. Why not 1 1/4" anchor bolts, or 6x8 boundary members, or an HD15? Nor has it occurred to me that since this was "just to code" it was anything other than quality construction. I trust that codes insure good construction, but I do not trust building officials to insure that codes are met. That is where the quality of the builder comes in.
It seems to me that over building accomplishes little and wastes a lot. If the object is better building then money is better spent by increasing the original load parameters and designing accordingly.
Comments, please.
*Mike: you make the excellent point that to beef up only one component (e.g. plywood) of a system (e.g. shear panel) may be pointless. But if all components are improved (ideally, if the maximum design forces were increased and the whole system redesigned), a stronger house could result. What lateral forces do the codes design for? That resulting from a 8.0 earthquake? - I don't know.Well in 1964, Alaska had a 9.2 quake (strongest recorded since the white boys showed up in North America) and I'm building my house on the Kenai Peninsula. How much will my foundation, framing, and sheathing costs increase to upgrade the anchors, hold-downs, sheathing, etc? Maybe 5-10%? I know I'd never get it back in re-sale but my peace of mind and pride of ownership is worth something. And if a 8.5 rolls through in the next decade, I might have the only house standing.But I'd agree that for most people, overbulding a few aspects of a house may not show a good return. Money might be better spent making sure that the contractor builds everything up to code (by doing construction over sight or selecting the best builder) rather than building a few things beyond code. -David
*Mike,When I said over code, I mostly was thinking floors, Boise Cascade has 3 floor span tables for their Ijoists "code approved,(L/360) 3 star (L/480),4 star ( 4 star goes to L/960 and says for the discriminating purchaser)! Also all roof trusses in this area toenailed to outside and inside walls (everthing I've read in FHB, JLC say this is a no-no)plus ALL use 1/2 OSB ( really only 7/16 ) and rock is always nailed to truss never 1X3's or 1X4's
*Unfortunately building codes do not classify earthquake loads in a Richter scale equivalent. Wind pressure is in mph, with an exposure rating.Quite understandable. In the worst case this would probably account for any expected hurricane. I doubt that it would be economically practical to make a whole building tornadoprof.Although there is a design in the most recent FHb on making a shelter that would be. Seismic is by zone. It is possible that recent code changes since the Northridge quake may reflect resistance to a 9.2. But then what of a 10.2 or greater which is theoretically conceivable. I would discuss this with your engineer.
*My remarks were mostly directed to the idea that there might be a reason for 5/8" wall sheathing, without the suggestion that increased hold-downs might be necessary for this to have any effect. It seems that when people over build they do so by upgrading materials. There are labor intensive ways to overbuild, such as diaphram blocking all floors or roofs. I wonder if anyone does things like this.
*MikeWhat's diaphram blocking?
*Diaphram blocking is blocking perpendicular to the joists or rafters , at the edges of the plywood. The purpose is to tie the plywood edges together so that under lateral loads the entire roof or floor diaphram moves as a single rectangle rather than slips along the plywood edges as many rectangles. It is quiet common in panelized roof construction in concrete tilt-ups. In frame construction with heavily loaded shear panels,it is often called for in floor sections to distribute loads among the individual panels. The reason I suggest that it is labor intensive is that it utilizes a lot of scrap material, 2x4 blocks are all that is needed, and a lot of time.
*Bravo, Fred!You know, I disagree with you sometimes, and admire you most of the time, and I think you stated my opinion exactly.
*FredL-As a P.E., I take exception to your solution to "overbuilding" by going to the next size I beam versus hiring an engineer. Did you check your beam for lateral buckling?. Do you know how to interpret the AISC manual to know if your section is compact or not? An engineer's fee can sometimes be the best money you ever spend, particuarly if you are looking back in hindsight from the vantage of a courtroom. Competent engineers do not overbuild to cover their ass, nor charge exhorbitant fees to save you a lot of "thinking effort". We are paid to exercise our engineering judgement, training, experience and common sense to solve problems in as expeditious and economical way for the client and, in many cases, save normally well-intentioned people from making disasterous and costly mistakes. Perhaps your clients steel footbridge is doing just fine due to your "overbuilding", but it is not advice I would follow.Mike M.- You raise some interesting points. I disagree that Codes are meant to be minimum standards. Codes are meant to protect life and property in that order. They are constantly revised and generally improved to more efficiently utilize the materials of construction. Often natural disasters point out the deficiencies in our codes as evidenced by Northridge and Andrew and the codes are reviewed and improved if necessary.Insofar as your need for a PE to do your lateral analysis: Why would you ask the PE to increase the loads beyond the Code requirements? A good PE wouldn't nor should you. And you apparently take some comfort in the PE's "butt and insurance" being on the line vs. yours. Thats what we get paid for, to do the calculations that the State licenses us for and then stamp your plans with our professional liablity.