Here’s one for the engineers. I have a client that is replacing her current rock in wire-mesh sea wall, It’s on a lake but for lack of a better term I’m calling it a sea wall, with a concrete one. I will be building her new cantilevered deck over the sea wall. Another company is doing the sea wall. The lake they live on has been pumped down for city works and they want to take advantage of this. Her neighbor is driving the effort so the project will include at least 3 waterfront properties. Here’s the issue; the lake freezes in the winter and the concrete wall he is planning on having put in is just a vertical 3′ wide x 6′ tall rectangle. Won’t this crack when the ice freezes and pushes on it laterally? I do not know how these are engineered but I plan on placing 2 footings in the sea wall to support the beam and I don’t want them to move. Second question; Should this wall be angled at the front in order to allow the Ice to move up and down it?
Discussion Forum
Discussion Forum
Up Next
Video Shorts
Featured Story
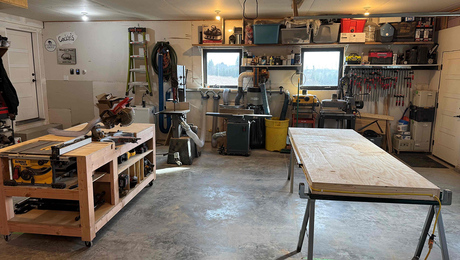
Listeners write in about running a profitable contracting business and ask questions about patching drywall, adding air barriers, and fixing a patio poured against the house.
Featured Video
How to Install Exterior Window TrimHighlights
"I have learned so much thanks to the searchable articles on the FHB website. I can confidently say that I expect to be a life-long subscriber." - M.K.
Fine Homebuilding Magazine
- Home Group
- Antique Trader
- Arts & Crafts Homes
- Bank Note Reporter
- Cabin Life
- Cuisine at Home
- Fine Gardening
- Fine Woodworking
- Green Building Advisor
- Garden Gate
- Horticulture
- Keep Craft Alive
- Log Home Living
- Military Trader/Vehicles
- Numismatic News
- Numismaster
- Old Cars Weekly
- Old House Journal
- Period Homes
- Popular Woodworking
- Script
- ShopNotes
- Sports Collectors Digest
- Threads
- Timber Home Living
- Traditional Building
- Woodsmith
- World Coin News
- Writer's Digest
Replies
Don't you have a local waterways/environment protection/conservation regulatory agency that oversees all lake and river issues?
In the states, some are called "Department of Natural Services, Dept. of Environmental Quality," or some similar name.
These boys and girls live to answer those questions and make money off of the permits they issue to allow such work.
If'n the city has already did a drawdown, there's already an engineering firm involved - unless you're up there in Bob. That engineering firm would be the fastest source for clarification.
But I would imagine somebody has to pull a permit for this job. And the inspector is the one whom would be expected to know if it's done right.
our three letter word is DEP - Dept of Environmental Protection.
Welcome to the Taunton University of Knowledge FHB Campus at Breaktime. where ... Excellence is its own reward!
Apparently, Environment Canada has OK'd the job, but my clients neighbor has no engineered drawing to give her. Very suspicious, and as I was finishing demo on the old (Perfectly fine deck) to get ready for the new one I asked her if they had a city permit for the sea wall. She was told by the neighbor it was not required. I told her that the city will require one for the deck, and that someone from some department must have to inspect the sea wall. I can't see Environment Canada giving permission without an engineered system either. So now I am concerned that the wall may be poorly constructed and done on the sly. I have a call in to the city but have not heard back from them??. I was paid for the demo but this sea wall is going to cost upwards of 12G for her alone. She has been a good client over the last 2 years and I hate the thought of getting in the middle of this.
but my clients neighbor has no engineered drawing to give her. Very suspicious, and as I was finishing demo on the old (Perfectly fine deck) to get ready for the new one I asked her if they had a city permit for the sea wall. She was told by the neighbor it was not required.
You'll want to get a haircut anda shave, sounds like Mike Holmes will be along in a bit, at least next door if no where else. <g>
Can't imagine much more agravation than being next door to one of "Mike's" houses.
I've done some lakeshore work, thousands of KM away here in Texas. Simple it has never been. (Even when the clients all seemed to feel it was the sort of thing a few 1x4 and cmu, cheap, would easily square away.)
I'm not picturing how a 3" concrete plank sufficing as a retaining wall, let alone a retaining wall submerged under water. Most of the bulkhead (the term-of-art for lake work here) work I have seen is installed 50/50--that's 50% supported (driven, buried, what have you) and 50% "esposed."
Occupational hazard of my occupation not being around (sorry Bubba)
With you on Mr. Holmes. LOL
Yeah, all the tv trucks would take the good parking places--a body'd never get any work done next door.
Almost as bad as being in the same builder's house, but next door--what would that suggest? <eek!> (Notwithstanding the the "hey what about us?" aspect <g>)
Piffin's idea gave me a mental image of a bit of over kill. Set some precast T sections vertically in a row, with the verticals into the retained soil (that gets you lots of stability for the retaining wall aspect). Then, "cover" the gaps with a matching set of T's, only facing out--which buys you a "breaking" surface to decrease wave action and the like; and the smooth surface allows ice to "climb" rather than "push" so much.
Ah, just got an email from a bulkhead guy. His "reflex" (not having any more ice experience than I) was to 8-12" driven pilings about 6' O.C., driven 2/3 "in" 1/3 out. He can get RR ties, so that'd be the "dirt" side support. Then corrugated sheets on PTD on the water/ice side.
His other thought was to just set a pier/piling as needed to cantilever the new porch out, and then let a locally-expereinced bulkhead guy work around that (and with a fistfull of of wet-stamped documentation that "your" pilings would be used for any other structural reason than holding up the deck (like dropping galvanized culvert around the deck pilings to isolate them from any ice thrust).Occupational hazard of my occupation not being around (sorry Bubba)
It's all for naught now. Showed up today with the engineer, who said the wall won't last as is. It should be sloped on the lake side, to allow the ice to ride up and down, and the dirt side has to be anchored in. All of this requiring an engineers stamp of course. I informed the clients that they were being seen off. They agreed with me but were stuck, it was either now or never and damn the consequences. The excavation company didn't even have a boom in the water. In the end their wall is going to fall over but my deck won't. The engineer told me keep the deck footings 4' away from and 1' lower than the bulkhead footing. Well I tried anyway. Just proves that homeowners need to be educated on what a good contractor can do for you: Planning, coordination and QC. Maybe Municipalities should hold semi-annual seminars with after pictures of botched jobs for their citizens. Thanks for the help
While I delight in hearing that the engineer said I was right, I hate hearing outcomes like this for sake of the HO. and really wonder how it ever got a permit. Partly the AHJ might be thinking this is only the HO's money and if they want to waste it, fine with us, but there is a lot of erosion and waterway pollution issues when soil gets distrubed by this sort of failure. i'm thinking your local AHJ is not doing their job.
Welcome to the Taunton University of Knowledge FHB Campus at Breaktime. where ... Excellence is its own reward!
Ahh the sea wall I live on a lake and a permit is needed to fart near the lake. all local contractors will gaurentee the wall.... will break over time. Most people put in a gabion and proper riprap. ICF won't help a footing pile from freezing as no heat from the land side.
Ice and wind win every time period I wish I would have videoed my neighbors wall fly apart during a big storm.
My Gabion is 1 yard square x 54 feet 11 years and no problem. I just built a 60 footer for my neighbor and passed inspection.
what ever wall system you go with make sure it has a curve in it to add more support as a curved section will hold better than a flat plane to the rolling pressure from the land side, from the freeze thaw cycle and soil pressure sloping to the lake.
The neighbor has some big friends in high places; No boom, no engineered drawing, no pencil drawing even scratched onto a cigarette pack. The engineer I contacted is drafting up a letter for us to keep on file stating that we informed the homeowners, all of them, what they needed to do this properly. When the blame game starts, it should cover us. I do wish my clients had of contacted me separately and we could of done this the simple & easy way; Survey, Engineered drawing put onto lot plan, submit for permits, Line up subs and have a wall building party. Thanks
Here is an object lesson for you from this.You feel good now about having done the right thing allied with the pro engineer.Had you gone with gut and seat of the pants on this, you'd always worry until it finally caved in.
Welcome to the Taunton University of Knowledge FHB Campus at Breaktime. where ... Excellence is its own reward!
Don't expect an inspector to have much of an opinion about an engineered plan. He will just be sure it matches the engineering.
You want to have that engineered by someone who does it in your area. It would be both laughable and not permitted here, and not because of the ice.
wave action is part of the formula, as is slope of the underlying beyond the seawall.
I presume this lake is large enough to have some wave action or they would have no need for a seawall.
what they have found happens with wave action, is that when they work at a straight up vertical wall, it creates excessive churning at the base, undercutting it, taking more erosion out to sea, and lowering the beach rather than protecting it. So when there is necessity for a vertical wall for some reason, the beach beyond it for some distance ( depending on the wave height and the pitch of the beach) must be lined with rip-rap to break waves and prevent soils erosion. Otherwise, the beach would go away bye-bye and the seawall would fall forward once undercut in five to ten years.
That's here. I don't know about there, but just to get a permit takes an engineered plan.
Know a guy who tried it with no permit - just to rip-rap - and it cost him about fourteen grand between the fine and having to restore to original condition.
Welcome to the
Taunton University of Knowledge FHB Campus at Breaktime.
where ...
Excellence is its own reward!
Sounded like fun. Is rip rap boulders/concrete shapes thrown in loose? she has a floating dock she wants to put back in the water when it's all said & done. I have nothing to do with the wall but I am not liking the sequence of events here. She said her neighbor received permission from Environment Canada but he did not give her anything on paper. Perhaps I should have asked these questions before I demoed her existing deck?
I can't imagine having a permit with no engineered plan. And if your deck connects somehow to all this, that is another fly in the ointment. I am NOT qualified as a civil engineer on this , but I'm thinking pilings driven and somehow =kept separate from the seawall.Yes, rip-rap is boulders ( or donuts as we call them) about 12"" to 24" size strewn and stacked up the angle to the high water mark probably similar to what you have in wire now. Here is a photo...
Welcome to the Taunton University of Knowledge FHB Campus at Breaktime. where ... Excellence is its own reward!
I can hear the death knoll on using the cement wall for footings. Their plan is to put the rock from the wire cage in behind the cement wall (3' wide and between the land and the wall) not sure I like that Idea either. The pilings would have to go below the level of the lake bottom to prevent frost heave would they not? The deck has to cantilever out over the sea wall by 4' (Planning on 2" x 12" x 16' joists 12" OC), so the footings/pilings will have to be right behind the sea wall. I emailed her and told that without an engineered drawing/system for this wall I can't proceed with her deck. So the ball is in her court now, hopefully she can wring some of this info out of her neighbor soon, the Lake goes back up on Dec 15th.
Well they have a document from environment agency allowing the work to progress. No mention of Rip Rap and the wall is only going to be 12" thick with 5000 PSI concrete. The current rock is to be removed from the site rather than placed in behind the wall. There is no way I'm attaching the deck to that skinny cement wall so here is the plan I emailed her; any opinions on it will be welcome. The contractor for the wall starts on Thursday. I won't be building the deck until spring but the bigfoots have to go in right away. Thanks"As a retaining wall it should be anchored and thicker at the bottom than the top but the description the permit gives is pretty vague on specifics other than to say it will only be 12" thick. If the sea wall is going to be a vertical concrete wall then we will use the big foots right beside the sea wall and hang the rear of the deck off of your existing wood retaining wall further back in the yard. That way we don't touch the sea wall and have to worry about anything moving on us. Before they backfill the wall we will have to insulate the wall with Extruded polystyrene extending 4' beyond the dimensions of the deck (Sideways). This should prevent one side of the big foot from having frozen soil pushed up on it. We will also insulate a 4' diameter around the top of the big foot, 8" below grade, further preventing any frost heave."
The frost heave is minimal compared to the hydrodynamic thrust of ice when it freezes..
Think of a massive hydraulic cylinder as big as the lake Ever notice that when you put ice in a ice cube tray it goes in flat but freezes with a dome? if you measured the tray has moved out as well. Liquid water when it freezes shoves outward dramatically..
Now add wind effect and tidal effects. (yes, the moon impacts lakes as well as the ocean) and we have some rather serious movement.
IF the concrete is solid enough to resist the pressure during freeze thaw cycles as the ice goes out the force of that ice shelf moved by the wind is powerful enough to move great big structures or land.. I've seen concrete able to resist the force enough to prevent damage but not to prevent the movement of earth behind the concrete wall caused by that ice flow shoving.
From the sounds of things I'd get paid for the work on the deck as I go and when finished make no warrenty with regard it it enduring ice damage..
As per new plan I will not be attaching anything to the sea wall. Big Foots will go in beside wall, but not touching it, and I am going to use EPS insulation to prevent the soil from freezing around the footings. I think insulating the inside portion of the sea wall 4' horizontally beyond the deck footings should help.
Edited 11/18/2008 5:34 am ET by losh
I think what frenchy is getting at is - how far a is your footing to be behind the wall? if only say 8", the crete wall can be moved that much by ice pretty easily, so your cast pier would be like a VW trying to run a red light in opposition to a mack truck. It WILL move.The way you wrote your plan implies to me a warrantee that certain things will not happen. Be somewhat more carefull with the language you use in communications so it is clear you are making your best effort to TRY to avoid bad outcome, while stipulating potential damage that you cannot be held responsible for due to the extenuating circumstance of proximity to seawall built by others.
Welcome to the Taunton University of Knowledge FHB Campus at Breaktime. where ... Excellence is its own reward!
Yes on ice forces. Even swimming pools regularly get broken sidewalls because of inadequate attention to winter prep work. I have known of one that got heaved right up out of the ground from frost under it.
Welcome to the Taunton University of Knowledge FHB Campus at Breaktime. where ... Excellence is its own reward!
Thanks, I was thinking 2' from the sea wall should be sufficient for the footings. Hear you on the communication bit
Edited 11/18/2008 2:15 pm ET by losh
"Thanks, I was thinking 2' from the sea wall should be sufficient for the footings."
Based on what?
Don't take that the wrong way, it's just a phrase I have found helpful around the jobsite to refocus the thinking. I have no idea how much lake water can push a small concrete wall, so I would try not to guess and build anything in the way until I had an answer.
I would first find that answer, the "what if it fails" answer, then design my deck as far away from that answer as possible. Two feet might be safe, two feet might not be safe, unless you already know for sure. Vic
"Based on what?"The seat of my pants on that one. Your quite correct in you statements, problem is the homeowner has no time, due to the lake going back up, to sit down and have this done properly. No one seems to have an answer to this problem, so I am going to be sitting down with the contractor for the sea wall on thursday afternoon, when work commences and come up with a plan for the footing. I will have him guarantee the wall not to move (As he should anyway) therefore limiting myself from a headache there. That being said, I don't want her deck to move so anyone know of an acceptable distance for a footing from a Sea Wall?
"anyone know of an acceptable distance for a footing from a Sea Wall?"The engineer familiar with that area who you are not hiring.I hate to bust your little round seeds over this, but that is the way to find an answer other than by guess and by gosh or by golly.If I had to do it that close by the seat of my pants, the pier base would be 3-4 feet deeper than the seawall base, and it would not be a pier. It would be a buttress wedge with the wing back away from the seawall.And yes, it would cost something big.
Welcome to the Taunton University of Knowledge FHB Campus at Breaktime. where ... Excellence is its own reward!
"The engineer familiar with that area who you are not hiring."I appreciate the help but please keep in mind that I am not the GC on this job, she only called me last week to demo the old deck and would like me to build the new one in the spring. At that time, six days ago, I was under the impression that a proper engineered sea wall was being put in place. Saturday, demo day, I discovered that no engineered drawings were in evidence. I posted my original question in order to gain some knowledge on the subject as I have none. That's why I am sitting down with the contractor for the sea wall as per my last post. If he can't give me an answer I am passing this back to the homeowner and telling them to hire an engineer and quickly. Your idea of the buttress wedge or gusset sounds like the best option i've seen yet. I will talk to the prime contractor on Thursday and if there is a proper engineered drawing in existence, see if he can do it. Once again, thanks
There yah go - refer it up, and document it down.
Welcome to the Taunton University of Knowledge FHB Campus at Breaktime. where ... Excellence is its own reward!
As was said earlier,
The city has an engineer on the project already. THAT engineering company has someone on staff that knows the answer. And most importantly, probably can push thru the permiting process within the short time available. Getting any other company involved will only add cost and time.
If you want the job, take the bull by the horns and contact them yourself. (The city will tell you who it is.) Tell your customer that you will and do it. Then YOU become the authority and a bigger scope of the project.
And the neighbor's, too.
Why don't you have pilings driven into the lake bed out beyond the seawall and carry your deck from them back to solid footings on shore?
Run that past the engineers maybeNo Tag
The environmental permit would have to be amended and their simply isn't time.
That's it charge the hill, I like it. I have an engineer coming with me tomorrow to consult with the client and the contractor doing the pour (I called this contractor this morning looking for a copy of whatever plan he was going to use; he does not have one!!!!!, and this is a well known company in this area.) I told my client to forget what her neighbors are doing and have the engineer draft and stamp a plan for her section of the wall, that includes the deck footings.
"I told my client to forget what her neighbors are doing and have the engineer draft and stamp a plan for her section of the wall, that includes the deck footings."
That is the best solution. Let the engineer do his job, let his stamp protect your reputation and bank account. Vic
Absolutely! Looks like our work here is done.Until the deck warming party!
;)
Welcome to the Taunton University of Knowledge FHB Campus at Breaktime. where ... Excellence is its own reward!
carefull! The hydrodynamic force of frozen water is awesome! Think of the biggest bull dozer you can imagine and multiply that times 10. You will need massively strong concrete to withstand the force and don't be surprised if the force shoves the dirt behind the wall up as the ice shoves things.
Far better to rip-rap the lake shore so the ice slides up and over the walls.
Well I hope she gets this straightened out with her neighbor. I think I have my answer, between the waves and the Ice, the wall definitely has to be sloped and rip rap put in. Thanks
As I was reading your post I thought of the same thing. Angle the front. It is simple and elegant.