Being a deck builder, I’m looking for a challenge and now I’m getting it. I want to finish the basement in my personal residence over the winter. Question I have is, how are people framing up the exterior walls for basement remodels? I live in a relatively cold climate region, (Milwaukee, WI) and hear all different methods for doing the framing. I’m concerned about the long term possibility of mold growth, (who isn’t nowadays?) and just plain want to do it right the first time. Some techniques I’ve heard are; first visqueen against the block, then framing, then insulate and visqueen over the insulation and drywall. Another method I’ve got; no visqueen on the block, just frame and insulate, then put visqueen over the insulation and drywall. Last, my building inspectors say no visqueen is required at all, just frame, insulate and drywall, which I really question. A variation on the insulation was that I only need to insulate from the sill down to the frost line, in our area that’s 4 feet. Any thoughts out there? Am I opening up a can of worms here? I’ve talked to a 1/2 dozen remodelers at my local NARI remodelers show and it seems there’s as many solutions as there are beer brands and they’re all the best way to go.
Discussion Forum
Discussion Forum
Up Next
Video Shorts
Featured Story
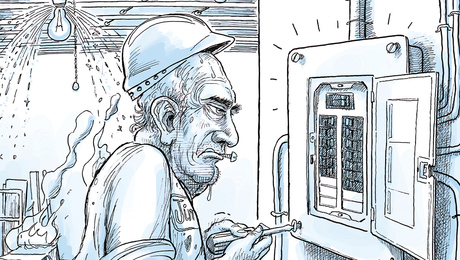
Dangerous electrical work and widespread misconceptions cause fires, deaths, and $1.5 billion in property damage annually.
Featured Video
How to Install Cable Rail Around Wood-Post CornersHighlights
"I have learned so much thanks to the searchable articles on the FHB website. I can confidently say that I expect to be a life-long subscriber." - M.K.
Fine Homebuilding Magazine
- Home Group
- Antique Trader
- Arts & Crafts Homes
- Bank Note Reporter
- Cabin Life
- Cuisine at Home
- Fine Gardening
- Fine Woodworking
- Green Building Advisor
- Garden Gate
- Horticulture
- Keep Craft Alive
- Log Home Living
- Military Trader/Vehicles
- Numismatic News
- Numismaster
- Old Cars Weekly
- Old House Journal
- Period Homes
- Popular Woodworking
- Script
- ShopNotes
- Sports Collectors Digest
- Threads
- Timber Home Living
- Traditional Building
- Woodsmith
- World Coin News
- Writer's Digest
Replies
nonyup-- one method I've used is to seal the block walls with Drylock or similar, glue rigid foam insulation to the block, and then frame the walls in front of the insulation. I prefer to frame basements with steel studs 'cause they're lighter, straighter, and faster to install than wood, plus they're not likely to support mold.
Hi Shep, thanks for the note. With your steel stud suggestion, I've also had someone else recommend that. Then, I've also had even another person say that steel studs create a lot of moisture because of sub grade and that can lead to mold/moisture problems. Have you ever heard/experienced that???
thanks, jim
I like Shep's plan, but you would need conventional, flat, bow-free walls. In my 1924 we had non-flat block work and bows in places of 1 1/2". But it was a dry basement, which is about 90% of the issue.
I used conventional lumber for all but the sill plate, but I could see the advantage of steel if you're comfortable working with it.
First I painted on the best moisture retarder I could find, then after setting the sills, I set the exterior walls about 1" away from the block so as not to touch and conduct moisture.I used FG insulation down to about 2' above the floor, then 1/2" of rigid foam over everything, then drywall. I know, folks don't recomment setting drywall over foam because of screw pops, etc, but I've had no problems after two years.
I have a wood stove down there heating the whole house and my theory was that all the heat was going to hang around the ceiling before it works it's way upstairs, so that's where most of the insulation is. I wanted the block to be able to breathe so the treated sills have a 2" gap every 8' that allows any moist air hanging around behind the wall to work it's way out.
It's not the most energy efficient system, but it does help keep the heat in without me having to worry about what's going on behind those walls.
Good Luck
nonyup-- like Nannygee, I frame the walls about an inch off the exterior walls ( in this case, the foam insul.). This allows some air flow. If you have moisture problems, I don't know of any construction technique to stop mold/mildew. You first have to eliminate the moisture by sealing the walls and/or floor and possibly having a French drain installed around the basement perimeter. Its really not worth finishing a basement unless you can fix the moisture problems. If its just a matter of normal basement dampness, I've found that once its finished with a little heat, the dampness usually goes away.
SHEP, Are you insulating the stud cavities as well as using the rigid on the walls?
astrozam-- I don't insulate the stud cavities for three reasons. first is I don't think its really necessary with the foam board, second is I'm concerned with the fiberglass holding moisture, and third is its a pain installing fiberglass batts in steel studs because they're not quite wide enough and there is no easy way ( that I know) to fasten them. I use a 2" thick high R rigid foam insulation which seems to be more than enough for a basement. Customers usually want a little heat in the basement to take the chill off, so the insulation just helps to hold it in. The walls usually end up warmer than the slab floor, anyways, unless by some miracle the slab was insulated before it was poured.
Shep, just for your information, not necessarily for use in a damp basement. There is insulation sized to fit steel stud framing. 16"/24" unfaced. All studs turned the same way, friction fit with help when necessary.Remodeling Contractor just outside the Glass City.
Quittin' Time
calvin-- Thanks for the info. Is that a special order product? My local yard doesn't carry it.
Shep, I get my drywall products, steel studs, susp ceiling tile/metal, eifs etc from a dedicated commercial drywall supply. The supply residential dw contractors as well as the commercial builders. They have the insulation in stock. It does come baled a little bigger than residential in 3.5 & 6". All are unfaced. Call Manville, Guardian maybe and even OC and ask for closest supplier. I think the order would have to be too big for special. If you're near a city of any size, you should be able to find it.
Here's some of the methods to hold in place, tho 8' batts usually don't settle out.
Ceiling wire run horizontally through the stud knockouts, passing through the fibreglass. Slits cut in the fibreglass at the point it crosses the cold rolled steel reinforcing bars that lock into the stud knockouts (square part) to tie a wall together and stiffen. Strip of duct tape (cloth) applied horizontally to the studs. Any cuts (rips) of fibreglass should be proud of the width measurement.Remodeling Contractor just outside the Glass City.
Quittin' Time
We have an additional problem in the Denver area. Bentonite or soil that swells and moves. Basements have to be framed with a double bottom plate (PT against the floor) and the plates spaced 1-1/2" apart, held apart with 40p nails. If the basement floor moves upward it doesn't shove your 2X's through the 1st floor. Just a little something else to figure in the planning. Tyr (but really Thor)
No vapor barrier and no steel studs. Check out this web site on preventing mold.
http://www.buildingscience.com/resources/homeowner.htm
You get out of life what you put into it......minus taxes.
Marv
similar to what Shep is talking about.....
Buck Construction Pittsburgh,PA
Fine Carpentery.....While U Waite
1" insulation board .... friction fit against wall.... const adhesive and expanding foam will eat thru it.....
PT bottom plate ... big thick bead of const adhesive and shot down to straighten and hold with Remington gun ... there's radiant floor heating in the slab so I used the 2 1/2 nails with the washers pre-attached.
Steel framing set on top and plumbed. Walls were really straight and plumb .... helped keep everything fairly tight against the block.
No VB.
Drywall will be installed right over the studs .... lifted off the floor an inch or two.
JeffBuck Construction Pittsburgh,PA
Fine Carpentery.....While U Waite
Jeff-- that's very similar to what I do. I use a panel adhesive designed for foam products that won't eat the foamboard to glue it to the wall. Its probably overkill, but what the heck.
Shep .... what brand/product of adhesive.
I haven't looked around ... but that would defintely come in handy.
I agree steel studs are the way to go in a basement too.
I have a shot down about a 25' length of wall ..... hard to see what it is unless ya know what to look for.... I tool it to show customers just how straight an arrow can be!
I use steel for my kitchen bulkheads too. Depending on the situation.... I make them up as 2 short "walls" .... "L" shaped ...
Or if it's something I want to lift and install as a unit ..... I'll make a complete box with cross bracing. I set my temp ledger .... lift the whole bulkhead onto the ladder...
climb up and lift into place. A coupla screws hold till I can secure the whole thing.
JeffBuck Construction Pittsburgh,PA
Fine Carpentery.....While U Waite
Jeff
You need to check the labels, I have seen some brand of "construction adhesive" that is good for foam, but I don't know what it is now.
Most Pannel Adhesives are can be used with foam.
Jeff, I use a pc of L metal from the same DW supplier to make the turn of soffits. I'll hang the track and stud pcs from the joists. Then I'll attach the L metal level and install the wall track. Insert the bottom studs plumbing the front as I go. I usually use 1-5/8's stud and track, inserting 2x4 were I want solid wood blocking.Remodeling Contractor just outside the Glass City.
Quittin' Time
Jeff-- I think its one of the Tite-Bond products. I'll check and make sure next time I stop by my local yard. I know better than to rely on my memory about exactly which one.
Jeff-- I checked out the yard today and they had 2 TiteBond const. adhesives for foam. First, and the one I've used, is the multi-purpose in a red tube. It's for interior/exterior use. The other one is a solvent-free adhesive in a green tube. My yard only had them in the 10.5 oz. tubes. I hope this was useful.
I do them similar to Shep - drylock block, I then hang visqueen, then 2" ridgid foam(taped seams on foam), then frame wall, drywall, done. Haven't tried the steel studs, but, I don't know why not.
I concur that there seems to be no 'right' answer to basement framing. I've asked this questions a few times and have gotten a lot of great feedback.
My plan, at this point:
1) rigid foam against block down to about 2ft. above floor
2) framing
3) sheetrock on top half
4) some sort of wainscotting on lower half, possible vented (peg board or corrugated metal or something funky)
Logic:
I wanted to keep the bottom of the wall...the part most likely to get wet in a disaster, relatively free of anything that would trap water and/or get soaked (ie, sheetrock).
The foam won't hold moisture as much as FB and having it against the wall helps keep the wet summer air away from it. Granted, the wet summer air can still be in contact with the lower 2', hence the ventilation.
We're also possible skipping heating at this stage and maybe just converting the basment FP to gas. If it's not enough heat, then it's just a simply matter of popping of the wainscotting and running the water pipes.
Things I'm not decided on yet:
- whether to just slap the foam boards up, or if I will take the time to make them airtight with expanding foam along top and bottom (since walls aren't perfectly flat) and taped seams.
- what to do with the spaces between the floor joists across the top.
- what to do with the ceiling. I wanted to leave it open for aesthetic and practicality purposes, but I probably need to put something up to reduce sound transmission from the basement (will be the family room with the TV and all) and the first floor. I'm leaning toward stapling felt bats to the subfloor underneath and then using a floating (from the walls) drop ceiling to allow for ventilation above it.
Shoeman-- the only place I use steel studs is basements. They're good because they won't absorb moisture, they're a lot lighter than the wood studs I've been getting recently, they're straight, and they're fairly easy to work with. You don't have to be real precise with your cuts since screws hold everything together anyway.
2x3 walls set plumb, glued and shot into slab 3/4 of an inch away from fondation then spayed as soon as possible with about 1 - 1 1/2 inches of polyurethane insulation to keep everything straight and sealed. No vapor barrier
Hmm...sprayed insulation...yet another options...