Money no object: Best floor joist system
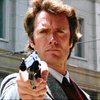
Growing up I remember the good old days of solid wood floor joists. I then remember the first times I got to see the truss-style of floor joists and then the engineered ‘I’ joists (stiles & webbing). I’ve often wondered about which were better liked from a quality-build frame of reference and not which is more quickly nailed into place by day laborers.
A couple of years ago I though that truss-style joists would be better as they typically had large openings already available between their top/bottom plates and these openings could be readily used for hiding mechanicals, but then someone said they tend to ‘sag’ over time. I took this comment with a grain of salt.
My current home uses Boise-Cascade I-Joists and they seem fine when used properly (mine were abused), but the aspect of having to spend considerable labor-time to cut openings into the webbing often was not accepted practice and mechanicals were simply run 6-14″ below the joists and wasted valuable basement headroom.
So, I wonder what the non-business (aka personal) preference is for the type/style of floor joist is and why?
Replies
I don't think there's any one perfect floor system overall. They all have their advantages and disadvantages. And every house is different.
If there was one thing I'd like to see folks do more often it's use long span wood webbed floor trusses.
For instance - On the "Spec House from Hell", I used 24" deep trusses to clear span 28'. That way there are no posts or beams in that part of the basement.
Every last bit of the plumbing, wiring, and HVAC is up in the trusses. (Except where the drain line exits the house) So to finish the basement, all that has to be done is put the ceiling directly on the trusses.
If you think back, there are plenty of threads here on BT about removing posts in a basement and/or cutting out sections of load bearing walls. So who not do away with thoses posts, beams and load bearing walls altogether? Sure makes remodelling easier down the road.
.
Another thing I've seen on floors that I think is a good idea is "roll-out" floors. By that I mean the floor system is dropped down into the basement as much as possible. And the garage floor/porch floors are raised to be at almost the same level.
Makes for easy accessability for wheelchairs and older folks who can't handle stairs.
With floor trusses, you can do top chord bearing to accomodate this. It can be done with other types of floors too, but is a bit more difficult.
Wow, 24" deep! I could almost get a coffin up there. :)
I am really impressed with the 28' span you got. Were these on 16" OC? And was LVL beaming to beak the span not an option in your House From Hell project? Were the webbed-trusses you used like the BC I-Joist products?
Here's a rough representation of the truss I have:
View Image
Actually, I set 'em 2' O.C. Don't really see any reason to put them closer, since I don't plan on having tile floors.
These are made entirely of 2X4s - They aren't I-joists.
I could eaasily have used an LVL to beak up the span. But why would I want to? This way I never have to worry about posts being in the way. That's the whole reason I like these kind of trusses.
Dance like nobody's watching; Love like you've never been hurt.
Boss, those are the trsses I want! Unfortunately, I hear locals (I am in a foreign land as I am a Yank in the South) say that those kinds of trusses 'sag'. This is unfortunate if it is either improper use that florishes the notion of sagging, or just simply misinformation.
Curious, did you do a cost comparison for alternative solutions? I really have no idea what those trusses would have cost each for 28' long 2' high versions.
"I hear locals...say that those kinds of trusses 'sag'"
Consider this: I'm EXTRAORDINARILY conservative on floor design. But I have no problem with these floors. I'd invite any one of you to come check 'em out if you like. They're in the house I live in now.
So I'd say your locals are full of it.
"Curious, did you do a cost comparison for alternative solutions?"
Why would I? Don't really care. They're expensive, but I consider them an upgrade. Just like others might consider marble countertops an upgrade. After all, you asked about OUR personal preferences, if "money is no object".
"I really have no idea what those trusses would have cost each for 28' long 2' high versions."
Prices vary widely from one manufacturer to the next. Around here, I'd say you're looking at $3.50 to $4.00 a running foot. That's expensive, I know. But you also save the cost of posts, beams, footings, and the labor to install them.
He has never been known to use a word that might send a reader to the dictionary. [William Faulkner] (about Ernest Hemingway)Poor Faulkner. Does he really think big emotions come from big words?" [Ernest Hemingway] (about William Faulkner)
I was wondering on that issue of sagging - I thought that a floor truss might fail if overloaded or underdesigned, but more catastrophicly like steel without sagging in the meantime. What say yee?But I also thought that maybe this local myth about agging trusses might have started when a builder with his HUA installed his floor trusses upside down and then bad-mouthed the truss company, repeating the story until it became believed as fact
Welcome to the Taunton University of Knowledge FHB Campus at Breaktime. where ... Excellence is its own reward!
"I thought that a floor truss might fail if overloaded or underdesigned, but more catastrophicly like steel without sagging in the meantime."
I've never heard of any evidence to support that theory. And I've never seen a floor truss loaded to failure.
In general, I've always heard that wood sags, creaks, and pops before failure, but steel fails without warning.
"But I also thought that maybe this local myth about sagging trusses might have started when a builder with his HUA installed his floor trusses upside down and then bad-mouthed the truss company, repeating the story until it became believed as fact"
Hard to say. It could be that it's just out of the "norm", so they're reluctant to accept it. The percieved "norm" is that floor systems can't span over ~20. So maybe they just don't believe anything new.
I've only had 2 floor systems installed upside down that I was involved with. (That I know of) Both were a nightmare to fix. Hopefully I'll never have another one.
The most absurd and reckless aspirations have sometimes led to extraordinary success. [Vauvenargues]
and the labor to install them.
Dont get mad at me dogging you but the facts are that it costs significanly more on most houses that we frame to install floor trusses.
Some day I'll tell you the story about Alcoa company introducing aluminum floor trusses and beams and stanchions. Their engineers had to be the biggest dreamers on earth at the time!
blueJust because you can, doesn't mean you should!
Warning! Be cautious when taking any framing advice from me. There are some in here who think I'm a hackmeister...they might be right! Of course, they might be wrong too!
"Dont get mad at me dogging you but the facts are that it costs significanly more on most houses that we frame to install floor trusses."
I remember you talking about your local codes for firestopping requirements. But that's the exception, not the norm.
And - Like I said earlier - Every house is different.
Procrastinate now.
I normally find truss floors faster
Welcome to the Taunton University of Knowledge FHB Campus at Breaktime. where ... Excellence is its own reward!
We find that floor trusses generally take twice as long.
blueJust because you can, doesn't mean you should!
Warning! Be cautious when taking any framing advice from me. There are some in here who think I'm a hackmeister...they might be right! Of course, they might be wrong too!
We've found that I-joist floors take longer than solid sawn in most cases. They are nice, but there is some extra time in certain houeses.
"We've found that I-joist floors take longer than solid sawn in most cases."
Never heard anyone say that before, so I'm curious what it is that would take longer.
The Irish gave the bagpipes to the Scotts as a joke, but the Scotts haven't seen the joke yet [Oliver Herford]
You know what I think it is? I think it's the drawing that comes with the floor package. You have to make sure you don't cut something you shouldn't have and you need to inventory the package to make sure it matches the drawing that's stapled to the package. You need to make sure you put the right beams in the right places, etc.
With I-joists, the joists are usually cut to the nearest foot, with solid sawn, nearest 2'. You have to seperate and count to make sure you have the right number of each. Often times, they've shipped us lengths longer than we need, so what you have on the site doesn't match the drawing, other times it does. I don't want to cut a joist and then realize I'm short somewhere and have to order and wait for it.
That process slows things down so I don't screw up :-)
With solid sawn, you can eyeball the stack that comes from the lumber yard and you can instantly tell the difference in lengths by the way they are banded together.
That's just been my experience. We are closing the gap though. A forklift and a chainsaw are I-joist installers best friends :-)
I will tell you though that some floors fly with I-joists because they are 35' long and we don't have to break the joists over girders. You handle one peice for that run instead of 2 or 3.
Thanks for the post - I was just curious.We sell I-joists in 4' increments. (Mostly) And there are ALWAYS instructions with the layout. And the lengths are clearly shown on the layout. With shorter stuff we write something like: Cut one 36 footer in half for 17' I-joists. (Or something like that)I'm surprised your supplier doesn't give you better layouts and clearer info.
It is very unfair to expect a politician to live in private up to the statements he makes in public [Somerset Maugham]
Ya, I wish that too. Our supplier is Cascade Capitol in Tacoma, WA and they use Roseburg joists and beams and they are really good to deal with, rarely make mistakes.
Tim, we also find that I joists take longer. Usually the biggest diferences occur because of significant time spent sorting. The rim joists take longer and probably another big time consumer is the headers and hangers.
We figure about 50% more time for engineered floor systems, but I think a system with multiple special situations (cantilevers, etc) might take as much as 100% more time!
There are rare occasions where the engineered floor systems might be equal or less, but I cant think of one right off hand.
blueJust because you can, doesn't mean you should!
Warning! Be cautious when taking any framing advice from me. There are some in here who think I'm a hackmeister...they might be right! Of course, they might be wrong too!
Its not easy finding truss-joist supplies on the locality. I know Schneider (spelling) makes them, or supplies them, as I see tractor-trailers hauling them, but I've not been fortunate to stumble across a residential development using them. Are there product guides for the curious to guesstimating depth, OC, etc. for desired spans, loading, etc.?
No, I am not a builder but I do get curious for information I may never use. :)
I stopped framing for a living back when most things were still framed with 2x, so I don't have much current comparison.
On our house we used BCI joists and my thoughts were:
Since they are flimsy when unattached, we spent extra time being carefull with them. If it had been 2x12 fir I know we wouldn't have worried much about breaking one.
We moved slower due to inability to just walk all over on the joists. The Ijoists had to be stabilized with 1x temporarily before we put on the subfloor. That took extra time.
There was a saving in that we skipped center footings and support (wall or beams) and for us that was the tipping point: we built on very expansive soil and having no extra bearing points was a plus for overall integrity down the road.
I still prefer wood. Years back I built a floor with 6x12 and t&g flooring. I liked it, but it did squeek a little.
I can see how you would come to the conclusion that it takes longer for framing, but the builder may still have a saving in the long run.I'm thankful for the loyal opposition! It's hard to learn much from those who simply agree with you.
I try to be helpful without being encouraging.
For some houses I'm building now, I priced out 2x10s (SPF), I-joists and floor trusses. 2x10s were the least expensive, then I-joists, then trusses. Matt
That's for the materials. Add for labor on each and how do packages compare? I'm just not understanding how so many are claiming more time for trusses. maybe it is partly because they are unfamiliar and truying to get their heads wraped around the differences and letting it all confound them.it's ironic that I never use roof trusses and feel intimidated by them, but I use the flor trusses henever I can. But these pro framers who uise a lot of roof trusses can't figure out how to use floor trusses without it slowing them down, while I know it makes me faster.or maybe the diff lies in an inappropriate choice of materials, which they have less choice over and they are given trusses whether or not they are the efficient choice while i only use them when it is the best way to go.
Welcome to the Taunton University of Knowledge FHB Campus at Breaktime. where ... Excellence is its own reward!
My comments were directed toward I-joists. I've never used floor trusses and the first time I saw them outside the magazines was driving around outside Las Vegas.
That is a good point about using roof trusses but not floor trusses. I'm just not smart enough to put together roof trusses :-) I'll stick with stick framing.
Tim, I was including Ijoists and web trusses together in my statement, The open web trusses I get have a solid webbed end that can be cut to length just like the Ijoists are most of the time. I dod remember some ttop hanging ones once
Welcome to the Taunton University of Knowledge FHB Campus at Breaktime. where ... Excellence is its own reward!
In this instance the 2 framers I interviewed said the labor price for 2x/I-joist/truss was the same. I didn't speculate on the time to install as I personally have only done simple floor systems with I-joists or floor trusses so didn't feel qualified to comment on labor time. I found them (Is & FTs) faster and easier - but again, I was just building "box houses", and I'm not a pro framer - or at least not in the past 20 or so years.
Matt
But these pro framers who uise a lot of roof trusses can't figure out how to use floor trusses without it slowing them down, while I know it makes me faster.
I've done enough of both to actually know the differences and where the time is lost.
If you are building a very simply rectangular house, the floor trusses might be equal. I say equal because you might not believe how fast a regular rectangular house might be closed up with dimensional lumber. I'm thinking in terms of minutes, not hours to lay all the joist.
To illustrate my point, I remember a carpenter acquaintence walking up to one of our jobs back in the days when I worked only with a partner that was my equal. It probably was coffee time and the deck was substantially framed. He casually mentioned that we had made pretty good time since we obviously had only started the job yesterday. I corrected him and explained that we didn't start yesterday, that we had only started this morning, two or three hours ago (I can't remember the exact details). He didn't belive me. I really didn't care what he believes.
The point is that covering a basement with joists is actually a very easy thing to do. Most guys get hung up walking back and forth uneffeciently, doing stupid unecessary things. When you actually analyze the numbers, you'll find that a 40 deck requires 30 joist. I can pretty much lay a joist every minute and so can my partner. He tends to carry more than one, I tend to carry only one. I move faster, I load faster, and I position faster. He does one side, I do the other. In 30 minutes, our deck is covered. Now we have to nail them. If we were going to use floor trusses, it's not uncommon to spend that much time studying the layout and orientating everything. By the time I've studied the truss plans, I've already got the dimension lumber layed.
Now, if we're building a 12 unit and every truss is 24' and we have to lay them 12 times, the trusses might win out.
The advantages of floor trusses isn't time, it's span. I've layed 32 ' floor trusses over a clear spanned building. I'll take the beam, three stanchions and dimensions lumber every day, any day and I know I'll be done first!
blue
Just because you can, doesn't mean you should!
Warning! Be cautious when taking any framing advice from me. There are some in here who think I'm a hackmeister...they might be right! Of course, they might be wrong too!
I built the house I'm in now, mostly solo, and I used I-joists because I could easily handle them myself. Because they could span so far I was able to put up the frame and the roof without doing interior framing. My span was 24' and the 11' I-joists were rated to 22'...when I went back and added the carrying beams I ended up with a nice stiff floor with lots of room for mechanicals...I even used a lot of the punchouts for wiring. I would have used more had I kept a circ saw at each end of the pile when cutting. The extra depth was nice...the waste pipe is buried in the floor so no lost headroom in the basement.
I can see how you would come to the conclusion that it takes longer for framing, but the builder may still have a saving in the long run.
Of course they have savings! First, the truss designers tell them that they'll savee labor costs, so they believe it. Then, they tell the carpenters that they'll save on time and their bids should be lower, so they believe it. Then since the carpenters are not astute enough to actually do time studies, they begin to believe that it saves them time, so they bid lower and viola, the savings appear!
It's a viscous circle.
Did I mention that a lot of framers are going out of business lately?
blue
spelling edit.
Just because you can, doesn't mean you should!
Warning! Be cautious when taking any framing advice from me. There are some in here who think I'm a hackmeister...they might be right! Of course, they might be wrong too!
Edited 4/13/2005 12:12 pm ET by blue_eyed_devil
I understand what you're saying, but there have been a lot of framers going out of business ever since I started in business. The most common reason for that is that a good framing technician may not know beans about business. Then there's the immigrant influence. Then there's the general waning of quality in a big portion of the market.
The good ones will survive, as always.I'm thankful for the loyal opposition! It's hard to learn much from those who simply agree with you.
I try to be helpful without being encouraging.
"Then there's the immigrant influence."An immigrant called me last night. He married a local girl. He is a hard worker, and I believe we need more immigrants, I'm not prejudiced, but here's the story...Last year I gave a woman an estimate on cedar shingle siding of ten grand. She couldn't afford that, only seven grand, so I said, if we only do this much I can do it for that much. She said OK, but let's wait until spring.OK, but I'll have to see what my schedule is come sopring and when I can fit it in. I'm ready now...she wanted to keep money at work in the market in the meantime, fine.so last week, she sends me a check for deposit, unsolicited by me for $2500, along with a list of requirements for the job that were not part of the original estimate, and wanting it done immediately.I sent her check back and declined the job with a list of other recommended contractors in the area who could probably do her.Then, I get this call from her new caretaker. He wants to do the shingling."How should i do this work?">go watch somebody doing it for a day or two and learn from watching them"How much should I charge her to do this work?">Figure out how long it will take you and how much you want to make onthe job and tell her"can I borrow your staging to get up high?">no- I need it to do my work"When she calls you, tell her that you think i can do this well, OK?"I was still laughing when I hung up the phone
Welcome to the Taunton University of Knowledge FHB Campus at Breaktime. where ... Excellence is its own reward!
I have no dislike of immigration per se and I've seen, and even hired, some very good immigrant help.
The US population isn't growing much, except for immigration. Do we want to wind up with population density like China?
No easy answers that I know of.
RE your story.... I've heard just as bad from local boys in various areas.
Seems that nowdays everyone wants to start at the top. Of course, back when I was in my 20's and knew a lot more than I do now, I wanted to start at the top, too!I'm thankful for the loyal opposition! It's hard to learn much from those who simply agree with you.
I try to be helpful without being encouraging.
I'd like to add one qualifier to your statement about ""roll-out" floors.":
Great for covered porches... Not good for open porches, as they can easily contribute to water leaks at the door(s). I hate it when that happens... Matt
"Great for covered porches... Not good for open porches, as they can easily contribute to water leaks at the door(s)."
Good point. I didn't mean they shoule be exactly the same level - Probably should have pointed that out.
But they can be CLOSE to the same level, as opposed to the typical 12 to 14" step up I see around here.
China is a big country, inhabited by many Chinese [Charles de Gaulle]
My opinion - there is no "best" for any and all situations.
High load design values can be acheived with any of these materials, but not all at same cost. Depth in elevation varies also. Vibration has to be considered.
I think that open web trusses can be the best value considering subs and install cost, but they - along with Ijoists, & steel ard not as good a performer in fires, as any fireman will tell you.
for overkill or when meeting an extreme challenge or the customer who wants to support dancing elephants on his dining romm table when cost is not concern, use LVLs instead of lumber.
Welcome to the
Taunton University of Knowledge FHB Campus at Breaktime.
where ...
Excellence is its own reward!
My choice is steel bar joists. 40' span no problem with only 20" depth. 50' span gets you up to 26" depth. Inexpensive. Shooting the deck down works great.
PAHS Designer/Builder- Bury it!
I saw a cool garage with owner built trusses consisting of rebar web with back to back angle iron at the top and bottom. How do you attach decking to factory made trusses? Hilti into the top flange?
Yup. Hilti works great, with the right pins. Had some carps borrow my Hilti and later tell me it wouldn't shoot through steel. They'd bought their pins at Lowe's, which doesn't sell pins for steel. Instead of asking, they drilled hundreds of holes.
I've bought a lot of bar joists at auction. Moving them got interesting until I built a pole hauler, telescoping tongue with 2 wheels between an inverted U over the load. Then you design the building around what you have. Notice the step in the building (steel cost was $275, including beams):
PAHS Designer/Builder- Bury it!
In the residential construction market I work in floor trusses are made of wood. You see metal in commercial, but even there some of the smaller buildings use wood trusses. Matt
Are you sure that they were owner built? There was a factory neer us that used to build trusses like you described. The smaller ones used rebar and the larger ones used steel round bars.
Yep. He was a welder by trade. He was the owner-builder. ICF place. The trusses spanned a garage with a deck above.
From a builders standpoint, engineered materials are stronger, lighter and more cost effective.
But, as a Firefighter, I wish that these innovations were never created. In a hot structure fire, (funny...never been in a COLD structure fire, LOL) an engineered truss starts to fail in just ten minutes! And when you consider that a fire doubles in size every 30 seconds, that doesn't leave the local Fire Dept. very long to do a search for anyone that may not have gotten out, or aggressively fight the fire, before the structure becomes completely unsafe.
However, when dimensional lumber is used for rafters and joists, it takes almost twice as long to reach the failure point and that additional time is enough for us to get anyone out and aggressively attack the fire at its seat. That dramatically increases our odds at saving a larger portion of the structure.
But then, if money is no object, use oversized dimensional lumber for the joists and deck it with two layers of 5/4 T&G ply using adhesive and screws. It'll be feel solid under your feet and withstand degradation in lees than ideal situations.
Thanks for reading.
We can easily forgive a child who is afraid of the dark.
The real tragedy of life is when adults are afraid of the light.
-Plato
off topic -I love your signature line. It is a quote i hope to remember
Welcome to the Taunton University of Knowledge FHB Campus at Breaktime. where ... Excellence is its own reward!
My dad is also a firefighter (volunteer) and told me the same thing about engineered stuctural systems. His pet peeve is the metal connectors that hold most trusses together--the lumber may survive the fire, but the thin metal heats up and fails way too quickly. He (being the cheap Yankee he is) sees the value in trusses, but would like to see plywood gussets instead of the metal connectors.
Cost no object? I would generally go for LVL's, because they're solid and strong for their depth. Add an extra foot or two to the height of the foundation so you can run mechanicals underneath the joists. Provide a ledge for the joists at the top of the foundation wall as someone else suggested, not just for accessibility but because it makes the house feel more integrated with the landscape if the first floor is close to grade, not floating two feet or more above grade as is common.
Mike
"His pet peeve is the metal connectors that hold most trusses together--the lumber may survive the fire, but the thin metal heats up and fails way too quickly."
That's typical of the misconceptions I see about trusses and fires. The plates don't typically fail - The lumber burns through.
I did a thread about it a while back. It's here
if you're interested in reading it.
I almost hate to bring it up again, as it's such a hot button issue. It's hard to have a civil discussion about it when everyone is polarized and touchy.
Everyone has a right to be stupid, some just abuse the privilege.
Boss, I just read through that thread, very interesting. Sounds like fire departments everywhere are trained to be wary of trusses, and there's no definitive answer on how trusses react in a fire.
Contributing to your fire-loss chart are changes other than framing in the last twenty years. Better codes on fire detectors, better fire equipment, more years of research and training. I tried to read with an open mind, but I have to say that despite all the advantages of trusses, being more sound than other means of construction in a fire is not one of them.
I know your livelyhood and that of many others depends on trusses, and since I mostly do trimwork and when I frame it's with more traditional methods the whole debate doesn't affect me much personally. It is an interesting debate though.
One question, you just said The plates don't typically fail - The lumber burns through. But in the old thread you and everyone else said there hasn't been much research in how trusses react in a fire. Has some research been done on this in the last couple of years?
Mike
Nice feedback, folks! Curious, these trusses you have used, Boss, are formed from 2x4's? I guess I am more surprised that they are deemed expensive but what the hey? I do agree with you 100% about looking at them as an upgrade and that is where they truly come into play. And locals are locals, so I do not doubt that one builder over time can create a myth based on a lack of understanding, incorrect installation, etc.
Curious about how one related the engineered products like I-joists ... The adhesive in them is hygroscopic, which means it readily takes water and vapor-moisture. But, isn't this the same adhesive in the webbing, OSB sheathing, and even CDX plywood? If so, I wonder about the scenario of joists lasting longer during a fire but the subfloor failing (joist hopping fire-nightmare escape scene, hehe).
You're covering a lot of ground here. Probably too much to go into in one post.When I talk about there not being enough research, I mean SPECIFIC research. Like an independent testing firm builds a building, then burns it down and observes what happens. Most of what's called "research" has so far been someone from one side or the other gathering info from subjective fire reports.Both the truss industry AND the fire service have put out a bunch of stuff that I think is wrong. Neither side is blameless. There is a group that's been put together that I hope will help some called the "Carbeck Structural Components Institute". http://www.carbeck.org/It's suposed to be a joint project between the WTCA and the Houston Fire Department to do research and provide info to the fire service. I have high hopes for this program.One of the things I'd like to see BOTH sides do is train firefighters on which situations involving trusses are most dangerous, and which ones aren't. Currenty I don't see that from anyone. .Honestly, I don't think trusses pose anywhere NEAR the fire risk that I-joists do. I think you'll hear a lot more about them over the next 10 or 20 years.
In America you can always find a party. In Russia the party finds YOU. [Yakov Smirnoff]
Thanks for the clarification. Interesting that you say Honestly, I don't think trusses pose anywhere NEAR the fire risk that I-joists do. I think you'll hear a lot more about them over the next 10 or 20 years. I tend to group I-joist with trusses in the category "modern engineered building materials", not meant as a bad label, just one way to categorize. What do you see as the fire risk in I-joists? Is it what Stickman (I think) said, that the neutral axis is weakened relatively quickly?
Mike
Boss,
Haven't worked with floor trusses at all since I'm in an area with slab-on-grade constuction. But I was curious if any sort of firestop is required for them. Also, do you put in access panels at various locations to allow inspection and the opportunity to fish wire, etc?
As for a "price is no object" floor, I would use an all-steel floor system using beams and steel trusses.
Andy
"But I was curious if any sort of firestop is required for them."
That varies with local codes.
"do you put in access panels at various locations to allow inspection and the opportunity to fish wire, etc?"
I've never seen that done. I suppose that would be up to the builder and HO.
Just a side note - I have an Uncle who has deep floor trusses like the ones in my house. His also have a rectangular duct chase in the middle of them.
He laid a plywood "floor" in that duct chase from one end of his house to the other. And he has an access panel in his garage where he can get into the duct chase.
When he needs acces to his wiring, he uses a mechanic's creeper to roll down through the trusses to get where he wants to go.
Homosexuality in Russia is a crime and the punishment is seven years in prison, locked up with the other men. There is a three year waiting list. [Yakov Smirnoff]
I read the thread that you referenced, thanks for pointing it out.
In our department, we don't consider trusses "fireman killers" as most of us are carpenters, builders, etc... We have, however, seen more than our fair share of structural collapse during a fire. We take the time during overhaul to look closely at what collapsed and what failed. A majority of the time, if the house (as were in a mostly rural area) had trusses used as floor joists and we had a floor collapse, it was the metal plates that let go from the wood. If the roof collapsed, it was usually from the fire self ventilating and a large area of the structure was consumed by the fire.
We use these observations to make sure that the new guys on the dept. understand what and why things fail in a fire and then strongly emphasize how important it is for them to sound out the floor when doing search and rescue or an interior attack. And that they need to be aware of what the structure is telling them while their inside.
By our very nature, firefighters love to go in and attack, attack, attack! But the majority of us would rather "save the basement" than lose a life, be it an occupants or a firefighters.
Our department long ago realized that truss construction was here to stay. We don't bad mouth the industry, but we do try to work with the industry and let them know our concerns. I have always appreciated your expertise and now I appreciate it even more.
Stickman
We can easily forgive a child who is afraid of the dark.The real tragedy of life is when adults are afraid of the light.-Plato
"A majority of the time, if the house (as were in a mostly rural area) had trusses used as floor joists and we had a floor collapse, it was the metal plates that let go from the wood. "
There's a lot of talk about what exactly the plates do in a fire. Some say they protect the wood under the joint. Others say the plates conduct heat into the wood and cause the plate to let go first.
The ones you saw may in fact have come off the joints. But I also wonder if the trusses didn't collapse first, THEN the wood continued to burn away under the plates.
That's where I think independent testing would be good. If they could somehow FILM some joints burning, they'd be able to see exactly what happens.
"By our very nature, firefighters love to go in and attack, attack, attack!"
That's one of the things I hear too. I did a talk about trusses at one of the local fire departments, one of the guys told me that I didn't want to "let them have any fun" when I suggested they consider staying out of unoccupied buildings. Firemen just aren't programed to stand around and watch something burn.
But that's one of the things I suggest. If there's no doubt that the occupants are all out of a building, why go in?
But that's a pretty serious paradigm shift for firemen, so it's tough to accept.
If you're interested, I'll send you the outline notes I use when I talk to fire departments. Just email me through this board.
Capitalism is the exploitation of man by man. Socialism is exactly the reverse
Mike,
I can see your point regarding the LVLs, but my problem with that solution, and this is from under my FF hat, is the high level of toxic gases that the glue resins create while its burning. I have yet to meet anyone that could survive breathing cyanide and phosgene and all of the other nasty thing that are a result of burning.
Now, from under my carpenters hat, I can see the merits of what you are suggesting. I might try that when I build my new shop.
StickmanWe can easily forgive a child who is afraid of the dark.The real tragedy of life is when adults are afraid of the light.-Plato
I suppose you're right about the chemicals; I assumed that FF's nowadays wore gas masks. The chemicals in glue make be bad, but the chemicals in wood can't be much better.
I'm also a big fan of lots of fire blocking, sheetrock (5/8" type X when possible), hard-wired smoke and heat detectors, proper means of egress, and all the other nice things that have come out of modern codes. If the fire can't make it to the trusses it's a moot point.
When my dad helped start up his local fire department in the 60's they called themselves the "Cellar Savers!" I'm glad things have improved since then.
Mike
In my town (older suburb just outside Chicago) code specifies that when using engineered lumber you must have a sprinkler system. So I guess no one uses them here!
What city is that?I didn't know there were any in Illinois like that.
Hell is when the person you are meets the person you could have been [Michael Castellano, Texas Jaycees]
Post-tensioned concrete.
Nuke,
Wow! have you ever opened a can of worms with that statement, best joist without regard to cost..
My fiirst choice would be white oak timbers, they are decay resistant and extremely strong. They do have aweakness however and that weakness is that ordinary metal fasteners (nails) will corrade in about 100 years or so due to the tannic acids in the wood that corrosin will also cause decay. thus you are forced to use stainless steel fasteners. Adding to the cost dramatically!
However if you don't want the added expense and since joists aren't often exposed to steady water issues, you could substitute Black Ash instead. Right now Black Ash is selling at a real discount since there isn't much of a market, less than a 10% premium for it over traditional doug fir joists. Black Ash can be nailed with any nail and it even nails relatively easily if you nail it while it's still green. Green or grey ash is selling for less than the price of Black Ash and if you go up in size a bit you can gain back all of the strength issues lost. It really is six of one half dozen of the other cost wise.
The real benefit of using solid timbers in lue of trusses and TGI's is fire surviability. Toss a TGI or a truss in a fire and inside of 5 minutes the strength has left them both. toss a timber in that same fire and depending on the size it may retain 80% of it's strength for an hour or more.. In fact due to the basic fire triangle it may well survive any fire.. (the great mass of a decent sized timber prevents most fires from being able to sustain itself)...
On a more practical level, if you buy your timbers directly from a sawmill as I do your cost will be the same or less than buying a much smaller 2x from the lumberyard. I can buy 6x12 timbers for less than the price per foot of a similar sized TGI or truss. (black ash is about 3.60 per foot in a 6x12 size while green or grey ash is $2.40 per foot) The only differance is that you might have to give the sawmill warning, time for them to find the right size and length tree.. Lumberyards on the other hand will most likely have stuff on hand and you won't need such lead times..
Edited 4/8/2005 11:54 am ET by frenchy
Great post, frenchy. I was beginning to wonder if anyone would suggest real wood!I'm thankful for the loyal opposition! It's hard to learn much from those who simply agree with you.
I try to be helpful without being encouraging.
I am an HVAC guy. I like forced air and I like duct work in conditioned specs. Given those reasons and the fact that an electrition or plumber with a hole saw is more dangerous than a minivan with a soccerball sticker in a mall parking lot, I prefer open wood trusses, especially between floors.
6" galvanized sheet metal can be run everywhere, and if some hack runs flex when no one's looking, at least it can be run without getting crushed or kinked.
BTW, the truss that BH showed earlier is exaclty what I used between floor for an addition we did a few years ago. 18" deep on 24" centers, all constructed of 2x4 members and truss plates.
Edited 4/8/2005 12:48 pm ET by Timbo