“more power” for “hot wire” foam cutter
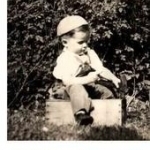
We are trying to soundproof basement rooms using (in part)2 inch dense foamboard. We have made a 8 1/2 ft “bow” with stainless steel safety wire (about .03in) for the hot wire. We were trying to power it today with a 12 amp battery charger, but couldn’t get it hot enough for 8 1/2 feet – it was ok when we connected at 4 1/2 feet. We were just trying to clip the cheap battery charger clamps on the wire, so tomorrow we’ll get a more direct connection (bypass the cheap clamps)and put a dimmer switch in one leg of the 120 vt to battery charger just in case.
If this isn’t enough heat – is there any easy source for more? Would it be safe to put a light bulb in series with a dimmer switch and hook in series with the cutting wire? We could use a GFI and rubber gloves, etc. I have been searching for a simple circuit for “more power” with no success.
Replies
If you don't mind taking some risks during testing you could rig a resister bank, keyless fixtures, number to be determined, on a piece of plywood, and run it off 120v line current. By varying the number of bulbs, fixtures in line, and the wattage of the bulbs, higher wattage have lower resistance, you adjust the current, and so the heat, the wire 'sees'.
I have rigged one before in this general configuration. We didn't but it would be wise to run this rig on a GFI receptacle. An Edison base fuse in one of the fixtures would also be wise. But here again we just 'wing' it. Sometimes the electricians get to play. Fun working out a design.
Thanks 4L -- and I'll be careful. That confirms what I was thinking.
Be careful.As long as your fuse and GFI protected and take reasonable care, assuming your of average intelligence and not a Klutz, you should be OK. Try to keep the damage sub-lethal.Any method of upping the voltage or lowering the resistance will improve performance. I use line voltage because it is what I work with.
Right, I am responsible for that. We have a little safety program - the guy I work for knows CPR - so I am focused on never becomming unconscious. He also knows I don't dance. The thing I am always watching for is getting in to electricity in such a way I can't get out of it. Also one time I got shocked screwing in a breaker box and the screwdriver inadvertently came back just above an eye. Thereafter I always wear protection. Thanks for the caution, and with all the lawyer fodder going on it gets hard to find out some of the ways to get anything done these days. I'll watch it and tx for telling me.
I have used standard house voltage for cutting foam for many years. I use a heavy duty lamp dimmer and an incandescent lamp in series with the cutting wire.
The level of power available for the wire is adjusted by using different bulbs in the lamp fixture. Low wattage bulbs have higher resistance, high wattage (100 watts or higher) have lower resistance. The lower the resistance, the higher heat at the wire. Small adjustments to the heat are made with the dimmer.
Small dimmers aren't good with this, but having the bulb in series makes it ok. I don't trust the smaller but cheaper units.
Regards,
Don
I have a working model now 8 1/2 feet long. A bungee on the leg pivot keeps it tight. I tried the bulb in series with the dimmer, but it wasn't enough heat, so I sent it straight through the dimmer, turned it up until it buzzed, then backed it off and it worked great. I have the dimmer right at hand for adjusting, and we used a "H" shaped guide (flat 2x4 on the foam and a vertical leg flush on each end) to cut straight and square. I think this worked because I had a real small stainless steel wire that must have several ohms to slow it down. We're working on a 4 1/2 ft model now. I think the bulb idea will work on it - or two bulbs in parallel & hone in the right wattage.Don, what wattage do you consider a heavy duty dimmer? Thanks to all for the responses. I was really encouraged when it finally worked.
Please include a GFCI.
Is this OSHA approved? If not, I'm calling Gabe.
blueJust because you can, doesn't mean you should!
Warning! Be cautious when taking any framing advice from me. There are some in here who think I'm a hackmeister...they might be right! Of course, they might be wrong too!
Using 110v is pretty risky. Try connecting the wire directly to a 12v battery, not the charger -- you should be able to get 80 - 100 amps easily. You might want to consider a current-limiting resistor in the circuit, depending on the resistance of the stainless steel wire.
Replace the SS wire with nichrome. (Eg, from an old radient heater.) The ideal PS is a large variable transformer, but they're hard to find. The light bulb bank, with either isolation transformer or GFCI, is probably your best bet.
Follow Dan's advice, the Nichrome has 5-6 times the resistance of SS for a given diameter, consequently higher heat for any given current.
I've used a battery charger and NiCr wire in the past (gives a red hot wire) with good results, think I used 22 Awg nichrome from some surplus store source ( too long ago to recall details about how long the wire was).
I used to use a 24 V battery.
Please forgive my ignorance, but why do you need 8 1/2' of hot wire?
I have used an ersatz "table saw" arangement with 6" of hot wire strung vertically to cut 2 boards at a time, just line them up and push through. An old electric train transformer provided more than enough DC.
Jim
The awful thing is that beauty is mysterious as well as terrible. God and the devil are fighting there, and the battlefield is the heart of man.
- Fyodor Dostoyevski
On the 8 1/2 feet "bow wire" cutter question - you're right it's just one way to do it. There are two reasons I didn't want to do the cutting the "table saw" way with the wire. First, we are trying to fit pieces up into the joist spaces (tight). The spaces vary in a 8 ft cut. This method allows us to make the tapered cut easily.The other reason is that we are in a tight basement and running the 4 x 8 sheets through would take more room than we can spare.