*
My new house will have two 36′ x 8′ front porches, and I am concerned with keeping water from soaking into the floor of the upstairs porch and causing water damage to the ceiling of the downstairs porch (it will be painted beadboard). I have planned on using cypress 1×6 t&g flooring (running longways away from the house and with 1″ of fall). Do you think I should put a subfloor underneath the flooring, and what precautions can I use to prevent water from soaking through the floor and damaging the ceiling of the porch below?
Thanks,
Whit
Discussion Forum
Discussion Forum
Up Next
Video Shorts
Featured Story
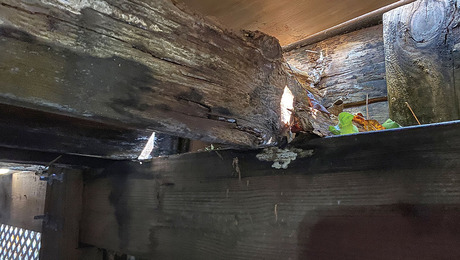
Newer pressure treatments don't offer the same rot and decay resistance. Follow these simple strategies to give outdoor lumber its best chance of survival.
Featured Video
Video: Build a Fireplace, Brick by BrickRelated Stories
Highlights
"I have learned so much thanks to the searchable articles on the FHB website. I can confidently say that I expect to be a life-long subscriber." - M.K.
Replies
*
I don't know the products that you have access to but you should install a subfloor and cover it with a self-sealing rubberized membrane. You have to extend this membrane to your flashing at the wall connection of your decks.
Gabe
*WhitThis may not be what you want to hear but Gabe's right, you need a roof under your floor. Rubber membrane, modified bitumen, or any other guality product. Over this you can install sleepers and your finished deck lumber. Don't short change this detail. Good luckTerry
*I agree with the added second response, I am not sure I would want wood to rest directly on rubber, I think it would accelerate rot.I would also, preprime each deck board individually by dipping and drying.
*Whit,We do waterproofing - in fact we're finishing up a deck job today, actually a second story covered balcony.I've attached a handout that I have put together and use in my business. It will give you a good idea of what it takes to get a warranty from me. Anything less, we'll do it sometimes but forget about any warranty.I have gone to using elastomeric, built-in-place, fabric reinforced, 100% fully adhered systems. My current preference is Sealoflex CT. You can call Sealoflex at (800) 770-6466. Ask for Rob and get whatever product information that you need from him.Why do I use what I use? Hot tar and modified bitumen products just don't cut it, IMHO. To me it's like installing guaranteed failure. I don't like callbacks - they gut profits. I want guaranteed success, not guaranteed failure. Sheet goods - well, unless they are 100% adhered to the substrate, all I can say is, "Wait until you have a leak and have to try to figure out where the source is!" It's nightmare city as the water can travel under the membrane for many feet (I've seen some go 60-70' on an old Wal-Mart building - we didn't take that job by the way). A glued-down sheet goods job can have some of the same problems as the glue job may not be perfect allowing water again to travel, granted not usually as much, but still a pain.So I've ended up using the Sealoflex CT system. When we roll and brush on the first coat we have full coverage quality control. In other words we can see exactly what we've covered as the material is colored pink. Often there will be areas where the plywood decking just literally soaks up the CT or there is a crack that sucks it up. We can see those areas and retreat them. Most of the time we'll roll on an additional coat (even though we don't have to) just to give us peace of mind - did this on the current job). Then it's just a matter of applying the fabric and a finish coat. Typically we apply two layers of fabric to all plywood butt joints and the wall/deck joints. On the current job we are applying a decorative Spray-Crete surface which will be finished with a faux flagstone pattern with a shadow grout line - very durable and very attractive.As for a floating wood deck on top of the Sealoflex CT system - it can be done. Just be sure to anchor the deck to the sidewalls.Any questions? If I can't answer them then Rob probably can.Good luck,Cliff.
*I'm in custom home building in San Antonio. We do a lot of covered balconies in tile, and I am curious about the product that you use. We have been hot-mopping and mud setting the tile for years without any problems. Maybe it is because the balconies are covered. The only leak we have had has been on an uncovered balcony. Our tile contractor used some new self leveling product on the repair. What kind of problems did you have with hot-mopping ???Thanks,Carl Nelson
*Carl,The problem that we have run up against is failure via a stress crack. The builders that I've talked with are only too happy to switch. I agree with your observation that covered decks/balconies are much less trouble.Tile goes over Sealoflex CT just fine too. I don't like to use tile simply because it chips too easily and most are very slippery when wet. When I've set tile, I too prefer to use a mud base. The sealers that we use with the Spray-Crete are by nature somewhat skid resistant when wet, even with bare feet. In this day and age of lawsuit happy consumers, it lets me sleep a little better at night, and at my age I need that.Cliff.
*Carl,Just a little addendum to my previous message: the failures that I've seen most often occured where the hot mopped tar went up and over metal flashing. My guess is that the metal gains/loses heat more rapidly than the tar (greatly different coefficients of expansion) causing it to expand and contract much faster than the tar can accomodate. Ergo, failure. I'm not saying this to be flip, but in my experience many builders in larger cities don't see their balcony/deck failures or dormer failures. They build the new house and move on to the next project. The homeowner stays 3-4 years on average, sells the house, and moves on. Then the new owner takes over just about when the tar/flashing union is about to fail. The second owner hardly ever goes back to the original builder because he/she doesn't know who that is.Out here in "Smallsville", TX, the new home builders who have lasted are known to just about everyone so they do see the failures. They are more than happy to talk about replacing hot mopping.By the way, I got onto this line of elastomers through an architect/builder friend in Florida. He has used the Sealoflex products for the better part of 12 years. According to him, he has never had a Sealoflex product failure. He has experienced structural failures due to poor design/construction, but that's an entirely different situation. We just finished up a deck yesterday, and I must say that compared to all of the other products that I have used (started using elastomers in 1985) this is in my opinion the easiest to use and has provided me with the greatest personal satisfaction. Why? The jobs have come out looking great. There have been no unpleasant surprises with product application and performance. No one at the factory hyped me, and I got exactly what they promised. What a novelty!!! Honest product and application disclosure. The materials aren't cheap, but no one has complained to me.Cliff.
*Cliff, I am really interested in learning more about this product that you are using. Before we started hot mopping, we were using a rubber underliner, much like a shower pan. Drop a few nails on that and walk on them and you have an umbrella with a hole in it. Our tile roofer still swears by this technique, but we did pick up a few leaks from that. Again, switching to tar seemed to remedy the leaks. The thing about hot mopping is that it seems antiquated. Where are you doing the majority of your work? Are you mostly doing residential decks ? We are paying around $600 for hot mop waterproofing on an average 8x14 covered balcony with lathe and plaster stucco (including soldered 3x5 flashing). Is that anywhere close to what you are getting ??? BTW, where is "Smallsville", TX ??Thank you,Carl Nelson
*Carl,Yeah, I've been the sheet rubber goods route too, not as the original contractor but following up and repairing them - EPDM and the others - they are great until you get a hole. 99 times out of 100 the water travels under the membrane before appearing on an indoor ceiling. Finding the source can be a nightmare. Would you believe one job where the roof mounted AC unit broke down. They called the service man on a Sunday. He came off the golf course with his metal spiked golf shoes on, went up on the EPDM roof (stair well access) and made Swiss cheese out of the membrane. No additional comments on this one!!!The decks that we do are mostly residential. We charge $5.50/sq. ft. for the Sealoflex CT system. It's competitive with what you are using pricewise; however, it does take additional time, especially in cooler weather. We take the length and width of the deck and add one foot to each dimension in doing our calculations. We may not go up the wall or over the edge of the deck more than 4" -6" sometimes, but we lay down double layers of fabric (and there are walls where we may go up a foot). These details take extra time and effort. Where we need to, we do whatever it takes to mask and protect finished surfaces (we use 3/4" filament reinforced tape first and them masking tape on top of that - the Sealoflex makes regular masking tape difficult to remove easily). These are all little details that take time, patience, and money, but add up to a first class job. There may be other contractors in the larger cities who charge less, but we stress quality. We pay attention to details. Our goal is "ZERO CALLBACKS". If we cut our pricing then we're back in the same league as the travelers, and we choose not to go there.We now live in Stephenville, TX. It's a long story as to how we got out in "cow country" from Brownsville and South Padre Island, but most of my work is in the Lake Granbury area where we are moving to soon - got our house up for sale. The deck that we just finished is on a house that is listed for $425,000. The contractor is going to have an open house toward the end of the month (hopefully). I'll be there talking with people about our part of the project. If you'd like to come up and have a look, we'd be glad to show you our work. We also do Spray-Crete decorative concrete resurfacing. This project has both the Sealoflex CT waterproofing on the deck and then a Spray-Crete decorative surface on top. The total pricing was $9.50/sq. ft. (should have been $10.50/sq. ft., but we had some addtional considerations). The Spray-Crete pattern is called keystone (faux flagstone look) with a shadow grout line. Our most prominent job is the entry walkway to the club house at the Pecan Plantation Country Club (the largest upscale gated community in the area). I wish that I had a digital camera. I've got some great storyboard photos that I'd like to post - may be later. Cliff.