I have all kinds of tools but the one tool I don’t own is a welder, I have been getting by asking friends to do small welding jobs, but this results in down time waiting for them to help me out or dragging the broken thing to them. So the question is this I want to buy my own but I also don’t want to spend tons of money on it and I don’t want to not spend enough. Most of the work to done with the welder will be repairing broken farm type equipment light sheet metal repair and some fabrication work. I am looking at a sears ac/dc 200a stick welder seems to be the way I want to go my 2nd choice would be a 140a flux core wire feed unit ……..anybody got any ideas or advice ……………thanks for you input JNavare656 @aol.com
Discussion Forum
Discussion Forum
Up Next
Video Shorts
Featured Story
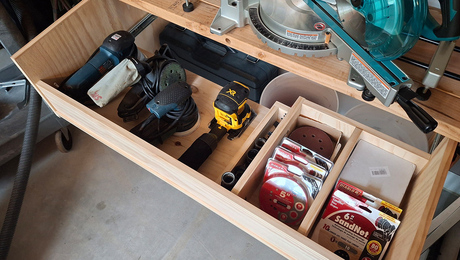
Listeners write in about removing masonry chimneys and ask about blocked ridge vents, deal-breakers with fixer-uppers, and flashing ledgers that are spaced from the wall.
Featured Video
Video: Build a Fireplace, Brick by BrickHighlights
"I have learned so much thanks to the searchable articles on the FHB website. I can confidently say that I expect to be a life-long subscriber." - M.K.
Fine Homebuilding Magazine
- Home Group
- Antique Trader
- Arts & Crafts Homes
- Bank Note Reporter
- Cabin Life
- Cuisine at Home
- Fine Gardening
- Fine Woodworking
- Green Building Advisor
- Garden Gate
- Horticulture
- Keep Craft Alive
- Log Home Living
- Military Trader/Vehicles
- Numismatic News
- Numismaster
- Old Cars Weekly
- Old House Journal
- Period Homes
- Popular Woodworking
- Script
- ShopNotes
- Sports Collectors Digest
- Threads
- Timber Home Living
- Traditional Building
- Woodsmith
- World Coin News
- Writer's Digest
Replies
J,
Before he worked for me my brother worked as a welder/fabicator in a local shop for 10 years. So when I went to pick out a small mig welder for my shop I took him along. We went with a Hobart 135. Nice small unit. We run it with 75/25 mix and added no accesories. Cost about $450 here. DanT
CHECK eBAY
"Understanding yourself is like trying to bite your own teeth"
Alan Watts
http://CLIFFORDRENOVATIONS.COM
I can weld ALMOST as well as I can understand women. I'm better with a torch, cutting things up.
Dad is a good welder, though. He's always used Lincoln AC/DC welders on his farm.
He looked at wire welders once, but decided against them for some reason. I think the smaller ones can't weld thicker steel, and the bigger ones were something like $1,000.
My wife says if I go fishing one more time, she's going to leave me. I'm going to miss her.
Boss
Always considered getting a welder which is why I'm reading this thread but the reason I'm writting you is cause they have a welder called a "Bush Hog"? Ever think about a name change? Dont think your wife'd appreciate it though....well its the thought that counts.
BE a bush hog....lol
Namaste
andy
"Understanding yourself is like trying to bite your own teeth"
Alan Watts
http://CLIFFORDRENOVATIONS.COM
A welder called a "Bush Hog"???
I think you're a bit mixed up. WmP said he used a welder to REPAIR a bush hog in post #7.Money can't buy happiness. But it sure makes misery easier to live with.
Hobart 135, ten pound roll of.035, no gas, a grinder, a 7" steel-cutter for your PC sidewinder and you'll never believe you could be so happy!
Only accessories you'll need: Fume mask, hood, long sleeves and some soft leather gloves. Weld a tray for the welder and hooks for the leads and a container for tips onto a $35 hand truck and you're ready to fab brackets and hangers on site that'll make you giddy with the realization of how easy it all can be.
Do some grind-into-the-weld, destructive testing to verify the quality of your welds and before you know it your quiver will quiver with efficacity.
well I still think it'd be a good name none the less.
"Understanding yourself is like trying to bite your own teeth"
Alan Watts
http://CLIFFORDRENOVATIONS.COM
For a starter, go with cheapest stick welder you can find ,which will be AC only (have found 230 A Sears unit at garage sales for $60) would be my recommendation. Stay with horizontal flat welds with 7014 and 6011 rod to start with to build your confidence. Caveat is that if you are only going to do thin sheet metal, then consider a small wire feed unit.
When (if, as implied by Boss) you think you are gettiong good with AC arc, try overhead 11018 rod and get an x-ray check on voids) <G>
PS: Loved Boss's comment - years ago, did ask the local tech school (Renton tech college -votec then) if they had a 2 or 3 hours 'course' for people who just wanted a few hints on welding. Guy said yes, but he was refering to 'credit hours', like 200 real hours! Learn on your own better than that I think.
PS: do I ever love the vacuum electron beam welder at the local aerospace co., welds 6" titanium to stainless with no voids! (think it cost more than my house + everything else)
I run the millermatic 185 wire feed and the lincoln crackerbox ac/dc. At first I had the lincoln ac only box. I started playing with a dc unit on the job one day and will never go back to an ac unit. so much easier with dc. beside you can pick up drop rods on jobsites for dc.
i use the wire for sheetmetal (hobby work) and lincoln for anything over 1/4 inch
My recomendation any wire feed over 135 amp (That HD licoln wire feed is junk) and a cracker box that will do DC. Stay away from ac only cracker box, couple dollars more and the welding improves 300% with dc.
I have a hobart 135 welder. Use 25/75 gas and either .30 or .35 wire. I prefer the .30 wire for most things. Do use the .23/4 wire for smaller gauge touch ups and tacks.
Ive repaired my Heavy Duty Bush Hog rotarty cutter, my light duty bush hog, the bucket of my front end loader. Boat trailer got fixed and built some racks and frames. It can do probably 90% of most welding needs. The remaining 10% takes into consideration any aluminum or special alloys, that require your TIG process, or really heavy duty machinery repair like dozers, excavators or scrapers etc.
Overall all its a great welder, its fan cooled, comes with a regulator for gas, can use the 2# spools and the bigger spools as well. Polarity can be reversed for use with flux core and reversed back for plain wire. With the right gas you can weld Stainless steel. the 135 uses standard 120v while the 175 uses 240v, thats the only difference really for the most part.
The draw back ive had is the gun and hose from the welder. Mostly due to my end i believe. I let some wire get oxidized and the wire will skip and bind in the gun. Getting the little felt pads to pre-lube the wire before the gun is a must in any welder. Other then this the hobart 135 is a fine unit, but my cons are user induced.
Ive used stick and wire feeds and prefer the wire feed. While many thing the output is limited with those small welders they really arent. I can weld 1/4 plate on multi-passed lace ups, The wire sizes are plentiful, and the power is perfectly fine. Stick welders have their place, but the versitility of a wire feed just wins hands down. The price of a reverse polarity stick and a gas wire feed close.
Your main expense will be gas if you chose to opt for gas sheilding as opposed to flux core wire. I prefer gas shield because flux wire is just nasty and smokey. If you weld outside, use flux core, inside use gas IMO. FWIW buy the bottle outright, while the upfront expense is there, you dont throw your money away with a bottle lease. I paid $70 a year for a bottle in two years you can pay for that bottle. Unless you leave your gas on or weld every day bottles will last a while. I pay $35 for a 25/75 mix (thats 75% argon and 25% co2) Other mixes are Helium,Full argon and full co2. each gas has its +/- and some metals use special gas like Stainless and Aluminum. Flux core wire has a greater cost, but no shielding gas since its built into the wire (the wire creates a gas in that smoke to shield the bead and kernel.
Esab, Hobart, Miller and Lincoln are brands to look for as some others. Look for fan cooling, Duty cycles that are realistic. Cheaper junk welders have horrible duty cycle and no fan cooling. FWIW id buy the Hobart 135 or 175 if my current 135 dies or gets lost somehow.
So you want to buy a welder and only want to use it for
"repairing broken farm type equipment light sheet metal repair and some fabrication work."
That's quite a range to ask for in an "inexpensive" welder. There are welders out there that can do it all, but plan on spending at least $2000. For anything other than sheet metal, (and assuming you'll only be welding steel) it's hard to beat a Lincoln 225/125 AC/DC stick welder (less than$300. I think new). Most wire feed MIG welders (while cheap upfront) often need other accessories at extra cost to be real versatile.
Jon
JmP says it mostest.
If you can find one go with a copper wound machine instead of aluminium. Over work an aluminium coil and you risk melting a hole in the transformer. Fan cooled and at least 25% duty cycle. Multi tap input voltage [110, 208, 240v] is a super plus. 208v tap for those extension cord and temp power days. Spray some splatter shield before you weld. Stick gives you Lo-Hi. Wire / flux core. I like wire for versatility. Use wire more than stick. MIG then MAG then TIG.
I've got a small Miller wire with gas. Flux core makes a mess & gas works better. But, yes, not in the wind.
Sold my old Lincon buzz box for $100, that's about the going price with hood & bunch of rod.
Get one of those auto darkening hoods too, but not the cheapo with only one sensor. The multi sensor ones will work when something blocks the flash from hitting the one sensor type. You have to be careful where your head is if you buy the cheaper one. Mine is old, and I didn't know about the other ones when I got it. Got that?
Joe H
three welders are called for.. (don't flinch, they can be affordable)
get a cheap used AC stick welder for heavier stuff. (I've seen good ones sell for as little as $35.00) Buy a millermatic 185 for wire feed. and get a used gas welding rig for cutting and the occasional brazing use..
I've given away a century wire feed since it caused me so much grief, and won't recommend their converted battery chargers to anyone..
I have an oxy-acetylene set and a 50+ year old AC arc welder that was my father's.
Arc welding is one of those skills like plastering that you lose if you don't practice regularly. For the infrequent user, fire is by far a better choice. You can get back up to an acceptable skill level quicker. At this point, I wouldn't even try to use the arc unit.
Before you buy anything, try a few different kinds of welding. Perhaps your welding friends will let you come over, and teach you the basics. Or maybe take a junior college beginning class. Whatever you do, get a feel for what you're getting into before you part with your cash. That's far more important than specific makes and models.
-- J.S.
I agree with JOHN_SPRUNG. I have done just a bit of welding, both oxy-acetylene and arc, and found that a gas rig with just a few attachments is by far the most versatile set up. You can reliably weld steel and aluminum in a wide range of thickness and you can braze many materials not normally weldable. Torches can easily handle smaller jobs in lighter materials than either regular arc or MIG welding. The ability to cut ferrous alloys and ability to apply heat for bending, hardening, tempering and forge work can make a big difference to workshop users.
Another up side is that an oxy-acetylene rig works without the need for power. This makes the rig, especially with smaller tanks, much handier for tight or remote spots where an arc welder would need either a long set of leads and power or an expensive motor driven welder.
The down side is that torches, even properly sized, take longer than arc welding to lay down a similar sized bead but for occasional or small jobs this is less of a problem. Larger tanks are about as heavy as a heavy duty welding transformer and running out of either gas brings production to a halt. Arc welding uses electrodes but these are relatively cheap and small enough to easily stock up on compared to tanks of volatile gasses.
Safety is also a concern. Arc welding can be fairly hazardous as you are dealing with high temperatures. An oxy-acetylene torch has the added hazard of highly compressed and volatile gasses. You have to know what you are doing or an explosion or fire is quite possible. Training, many community colleges have welding classes, a neat and careful demeanor and common sense can make gas welding as safe any other workshop procedures.
IMHO a high quality oxy-acetylene rig would be a fine addition to a shop. Like a Swiss army knife it is multi-functional. While it often is not the absolute best tool for a job it is still good for most situations and can do the work of many specialized, and much more expensive, tools. Just a bit slower.
There are real limits to a gas welding rig.. for example if you have a 1/4 inch thick beam to weld together in place, unless you don't have any wood around you can't gas weld it.. too much time and the flame will start the wood on fire..
with a stick welder you just turn up the heat and lay down a bead.. seldom anything evan if the beam is sitting on wood! I've done that where I welded a beam in place and the slight cgharring was easily stopped with some available snow. (if it'd been summer i would have had a bucket of water handy)
The manuals, at least the ones I'm familiar with, usually list 1/4" as being the upper end of any but the biggest gas rig without making multiple passes. My experience agrees with this. But then again how often do you really weld anything larger than 1/4" and needing more than a few inches of weld.
Your point about welding steel on top of wood points this out. The gas rig, being at the limit of its capacity, cannot generate enough heat fast enough to contain the heat to a small area. But here again how often is this a real problem.
If you commonly weld structural I-beams by all means an arc welder, either stick or large MIG, would be the preferred tool but it would still be nice to have a fire hatchet to do the trimming. And to heat up soup and coffee at lunch.
Of course an industrial arc welder can be set, with a bit of creativity, up to heat things up also but it is not nearly as convenient or easy. Of course if you go so far as to have an generator welder you could do what at least one crew I have seen did. They mounted a microwave oven to the trailer and plug it into the 120v outlet on the gen set.
Edited to add last sentences.
Edited 4/5/2003 12:53:46 AM ET by 4LORN1
You are right about multiple passes being needed for thicker stock when using the wire feed models. Fortunately the MIG welders make that very easy to do. Because there is no slag or oxides to clean off between passes, you can just keep on welding till you have a bead of sufficient depth. I used to run the maintenance department for a mobile home factory. We had a tractor to move trailers in the yard that had a set of heavy weights welded to the front of it (to counterbalance the trailer weights on the hitch). I was taking it back to the welders every other day to have the weights welded back on. I finally got tired of that and I laid on successive beads of wire until I had built up about a 1 1/2" thick weld. Two years later that tractor was still holding together with those welds. Doing that with a stick welder would have taken at least a full day, I did it in about an hour.
I want to pick a welder but cannot find check it and suggest me best one https://protigwelders.com/best-small-tig-welders/