*
First time enquirer….an enterprising do-it yourselfer.
I will be adding a kitchen/dinning room bump out on the back of our straight faced 2 story colonial here in Denver Colorado. Dimensions are 30″ long x 10′ deep.
I’m planning for a simple shed roof and was wondering what type of load bearing material should I use to span the entire length of the 30′ opening in the wall. I do not want a supporting post in the way. What’s the smallest dimensional thing I can get by with? Steel I-beam better than glue lams?.
I know that I can always hire an engineer, but seems that there must be a fairly simple answer. The load consists of two upstairs rooms and the roof (trusses perpendicular to the wall)
Hope I won’t have to be constantly ducking a big thick beam as a tradeoff to no supporting posts.
Anyone had a similar challenge or seen a solution?
Ra lph
Discussion Forum
Discussion Forum
Up Next
Video Shorts
Featured Story
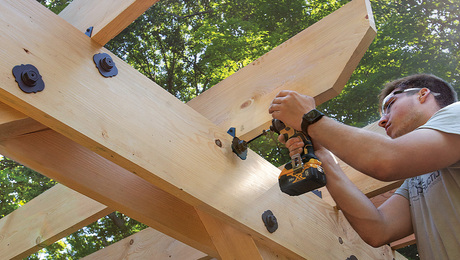
Built from locally sawn hemlock, this functional outdoor feature uses structural screws and metal connectors for fast, sturdy construction.
Featured Video
How to Install Exterior Window TrimHighlights
"I have learned so much thanks to the searchable articles on the FHB website. I can confidently say that I expect to be a life-long subscriber." - M.K.
Fine Homebuilding Magazine
- Home Group
- Antique Trader
- Arts & Crafts Homes
- Bank Note Reporter
- Cabin Life
- Cuisine at Home
- Fine Gardening
- Fine Woodworking
- Green Building Advisor
- Garden Gate
- Horticulture
- Keep Craft Alive
- Log Home Living
- Military Trader/Vehicles
- Numismatic News
- Numismaster
- Old Cars Weekly
- Old House Journal
- Period Homes
- Popular Woodworking
- Script
- ShopNotes
- Sports Collectors Digest
- Threads
- Timber Home Living
- Traditional Building
- Woodsmith
- World Coin News
- Writer's Digest
Replies
*
Ralph,
I'll prepare you for the ensuing advice. Hire an engineer. You don't want to anyone to offer armchair advice. Besides the fact that they wont. Imagine that your a doctor. I write you an email and say "my knee hurts. What do I need to do." Good luck.
Jon
*Ralph- Are you talking about needing a 30' header for the entry way into the bumpout? There are any number of materials that will span 30' but it is going to be one heavy mother to retrofit. Another consideration is thickness of the wall it will be going into. You likely have a 2x6 wall that you are going to tuck that into so I don't know if a glulam or the like to span 30' would tuck into that thickness. Also, if you are going to carry that load in from your corners (bearing all the way down to your foundation) you would likely need some kind of reenforced concrete footing below the trimmers to carry that load. Is this the kind of problem you are talking about?
*Ralph, I'm with Jon, you need an engineer.I doubt if a builder would build that opening without a set of stamped drawings.If you are the DIY-builder, then I doubt if your building official will issue a permit without a stamped set of drawings.If you are the DIY-builder and live in an area that is not overseen by a building officer...meaning no permit is required...then as backup, being the smart guy that you are, you'd want an engineer to spec this out so your house doesn't fall down on top of your family...or on top of subsequent buyers should you ever sell.The internet is good for a lot of things, but spec'ing out a 30-foot load-bearing beam based upon an unclear, 3-sentence description of the house?That said, thee are a few options...steel, a built-up laminated beam, a truss-type assembly...but your best DIY-solution may be steel. Many steel yards have engineers that will spec out a beam for you if you buy the steel from them. Some of these "engineers" are degreed engineers, some are rule-of-thumb enjineers.If there ever was a case for buyer beware, this is it. This is a case where saving a couple of hundred dollars today could cost you tens of thousands tomorrow.Remember, it's not just the beam that has to carry the overhead load...the posts have to support the beam, the platform has to support the posts, the foundation has to support the platform, the footings have to support the foundation, the soil has to...Good luck!
*Three things come to mind that might work. First would be a huge special order engineered beam - Probably 4 plies thick and 24 to 28 inches tall.Second would be a hell of a steel beam. I'm sure you're looking at 18 inches tall or more - I don't have that much experience with steel. Third would be a roof truss girder. This may be your best bet, as it could be recessed into the roof, and your floor system hung off the side of it. Hard to say how many plies would be needed - depends on the depth and your design loads, and how your floor is framed. Keep in mind that if you do get any of these thingsd to work, you could be looking at a reaction of 20,000# at each end. How are you going to deal with that? Will your foundation support that ? Your reaction might be even more, depending on the snow load required in your area of Colorado, the width of your house, and how your floor is framed. I think Jon Blakemore is correct in saying you need an engineer, or scrap the idea of keeping the whole 30' open. Is it really worth it, as expensive as it's going to get ?
*Ralph... a 30 ' hole is a BIG hole... i'd cut the span in half and work it into your plan...and get an engineer... or do the engineering yourself...
*I have spanned 30' with 18" tall steel H beams. But like all have said, the footers for this steel were rather large and all concrete. There was no wood in between the steel and concrete columns and the columns were reinforced.near the steelhead stream,aj
*Ralph,Bear in mind that I am not offering engineering advice...A steel beam to span this distance would probably weigh in excess of 130 lbs/lf. So you would have to wrestle a two ton piece of steel into an existing wall (while still supporting the existing structure from collapse. It can be done but I would rather have an engineer, with his/her license to protect, be the one giving me advice.
*Whoa. Speaking from the standpoint of an aircraft structures engineer, that's one big-ass clear span. This is NOT something to be taken lightly. Sam
*Ralph --I guess a piece of W 36x300 steel would probably do you fine, but the sucker would weigh about four and a half tons, and cost you more than a properly designed job would for both the engineering and the construction. As for ducking a beam that's 36" high, there's no problem with letting the beam form the bottom three feet of the upstairs wall, and hanging the floor under it.What you can reasonably do to help yourself here is to carefully measure and draw everything that this beam would have to support, and everything that's under it to support it. Draw what you want to end up with when the job is done. If you can document clearly enough what exists and what you want to do with it, your engineer may be able to do the design for you without the expense of a visit to the site. If permits are required where you live, look for an engineer who will act as your agent in pulling the permit.-- J.S.
*A simple box beam would do the trick. I have one in my house spanning 29' carrying a comparable load. Of course, it's only been 18 years or so since I built it, so it really hasn't stood the test of time yet.
*The ability of the beam to carry live and dead load is only half the fun. Taking out that much shear wall exposes a structure to racking from wind load and seismic effect. With the exception of catastrophic material failure (possible here) structures fall side-ways not down.
*Same caveats as all the others. We span about 27' and support an 8" slab and a second floor above on a W16 x 100. The columns are 4x4 steel and rest on 11' x 11' x 12" footers with a grid of #5 steel every 6" both ways. Of course, it was engineered. That beam cost about $1,500, plus took a crane and crew to set.I mention it only to show something that's been done that is in the ballpark of your span, and not as advice other than to get thee to an engineer.
*Haven't heard anyone mention using a pre-tensioned concrete beam. Probably will weigh about 8 tons, and require additional foundation work to support this extra added weight. I'm with the others that mentioned breaking up the span into manageable increments, and incorporating this into your design somehow. An engineered floor girder also comes to mind, but these are definately better utilized during the construction of a new home. Does your site have enough room for a crane??
*Ralph,I'm also a DIY. I like defending us DIYs here against the pros. But like Clint says, "A man's got to know his limitations."How much is your house worth now? If you put this hole in your wall wrong, that value will surely decrease x percent - maybe to zero. Now, how much is that engineer gonna cost? Compare the three numbers. The engineer will probably cost about 1% of the overall worth of your home. Not using him/her will probably cost 50%+, and closer to 85%+ the value of the home. That cute little stamp the PE's got is a pretty damn good investment in times like this. You need to ask yourself how much you're really saving, and how much you're really risking here.I do DIY because I enjoy it, not to save money. I think your perspective is the opposite way in this case.
*Ralph - Are you still around, or did you ditch us ???Just curious, as you haven't answered any of the posts.
*while you're out looking for engineers .. run your addition by a good architect....the 10 x 30 with a shed roof sounds like it could use some TLC...good contractors are still a dime a dozen.. but good design is a treasure beyond worth(and bad contractors are legion)b but hey, whadda i no ?
*Ralph- let's see if I've got this.. You want a 10' second story addition with a flat/shed style roof 30' long and supported at each corner with posts?
*Assuming house is 24' deep.30x12=360# floor load @50 psf= 18000lbs30x(12+10)=660# roof load @35 psf= 23100lbsTotal load = 41100 lbsBearing on two posts > 20550lbs on eachNo wood will take this much wight in one spot without crushing so you need steel or about 20 jackstuds under each end!If you have not got the idea yetengineerengineerengineerGood luck!Mr T
*Like I said..... Whoa.....
*FWIW... Not to deter you from spending money on an engineer (hey, a guy's gotta make a living...), but: buy a copy of "Wood Structural Design Data" from the American Forest & Paper Association. Well worth the $20.00. When your county inspector questions your drawings you'll pull out your load calculations, and that book. Or, check out: http://www.tjm.com/PDFFiles/2060.pdf. That is also handy when convincing the county types that you can find your center of mass with both hands. Per the guys in my county office, quite a few residential builders in my area can't quite locate theirs...If you're not handy with simple math & keeping track of a few details, or refuse to read the CABO code book (because you know better or don't understand it) then def. go spend the $$ on an engineer. YMMVNot saying I'd do what you want, but looks like there is lumber out there to make it work...
*Ralph,I just went throught a similar beam sizing exercise. I ended up hiring an engineer based on the sage advice offered here on Breaktime. Best money I ever spent. It didn't cost too much and I'll sleep better at night, which in my case is directly above the beam in question!
*I'm with Mike,The design sounds like it is lacking something. Unless this is for a chicken coop off the side of your barn.This roof has the potential for lots of drift loading. Either call an engineer or send pictures of the before and after.I can't think of an instance where a 30 foot clear span carrying the loads mentioned would be practical or functional, not to mention compatible with a colonial design.
*Ralph there is a simple answer to your problem. The formula is in most first year engineering books.But the solution is not going to be one you like. As others have pointed out 20,000 pounds has to be transfered to the ground at end of the beam. I think typical soils support 2,000 pounds per square foot. That is a lot of footing to pour.Others have estimated the size of a steel beam. Lot of weight in the steel beam (add 1-2000 pounds to the load in the above paragraph).There are solutions that have some merit. Rebuild the second floor wall as a beam. A few pieces of 2x at the top and bottom, a couple layers of plywood on each side to carry the shear. Expensive but doable (make the beam curved so it deforms tothe proper shape).Print this thread out and take it to a good engineer. We might say something he would miss.
*I want a 40' motorhome that can go 200mph....Oh, and I want it to be affordable and safe. Can it be done? Of course, but why?There is a solution that will cost you only a few hundred or so. It's called posts. You don't want them. I understand. The folks here like to stretch the limits and test new techniques, so they want to find a way for you to do what you want to do, but I'll volunteer to be the a**hole and tell you to forget about it and find an architect or even a friend with an eye for design to hide the posts or make them an attractive element in the design.Good luck-Randy
*Ralph - Listen to Randy! Listen to Mike! Listen to Tommy B.! With posts you can get back to 'normal' residential construction.i but seems that there must be a fairly simple answerNope.Jeff(on the other hand, do you think you guys got carried away enough?) ... this is an easy (tabular) calculation for an engineer, and if the beam can be upset (into the 'high' shed portion of the addition) so that it is laterally braced with uniform loading he's looking at something like a W16 x 26 or W16 x 31, maybe a W18 to limit deflection. Ralph - This is for planning purposes - DO NOT ORDER A BEAM BASED ON THAT COMMENT! - you didn't hire me, you don't know how to laterally brace a beam, and no DIY in his right mind would attempt this, but to answer your GENERAL question regarding approach you're looking at a sizable, though not ridiculous, steel beam. Posts will probably be 4 X 4 tubular steel due to higher yield strength in TS columns. Remember, you're going to have significant deflection, on the order of (design) - 1-1/2" - can you stand that?. It would be visually noticeable across a flat opening. You can accommodate it by boxing in the underside in a level manner that allows the steel to deflect within the box (ie, you can't fasten the box to the beam). BTW, 'normal' assumed soil bearing capacity is 2 tons/SF, not 2,000 lbs/SF, assuming you have normal soils. Again you're looking a larger-than-typical, but not ridiculous footing. PS - You'll be surprised at how important the thickness of the baseplate is at that loading.Now go hire that engineer!
*where'd ralph go...
*> When your county inspector questions your drawings you'll pull out your load calculations, and that bookI tried exactly that. Here in L.A., Building and Safety has an absolute policy of not even looking at engineering calculations done by anybody but a licensed engineer. No stamp, they throw it back in your face. So, I asked the guy who just rebuilt the place next to mine, and he recommended a very good engineer, who looked at my calculations and said that I had gone into far more detail than they want to see. His calculations showed that I could use 4x6 or 4x8 beams where I had planned to use 4x10's because I was being too conservative. He also looked at parts of the building that I hadn't planned on changing, and suggested adding some blocking and Simpson hardware as a very cost effective way of making it much stronger.If you want to, get the Ambrose book and do as much as you can. Then take it all to a pro to get a second opinion based on a more complete education and a lot of experience.-- J.S.
*"Where'd Ralph go?"I don't know, but I really like being able to come here and listen to y'all think out loud.It makes the decisions I've been making as a lowly DIYer ever so much more rational.BTW -- I cut an 11' opening in my house under a truss roof, and put in a double 2x8 beam just to avoid having to pull out the top plate and redo the ceiling.Ken
*Jeff,You are correct. When I threw out the figure of 130 lb/lf I was assuming worst case based on so little information. Another option would be to make a composite beam using channels. Say a C15 x 40 bolted to each side of the upper floor wall studs and TS columns cut into the existing wall to footings. Then temporarily support existing floor load and install 12 x ?? to carry the floor load tied into columns. This is where the engineer could use the tables to crank out a quick, accurate answer. Ralph, it you decide to return for the answer...remeber that my comments are not based on calculations to finalize sizing but on a quick look at the ASD book.
*What are the snow loads in your area? How wide is the home (for tributary purposes)? What pitch is the roof? Do you have any wind loads to be concerned with in your area? I think your looking at somewhere around a (ie.W18x55 A992-50 Grd. that is assuming your home is 24' wide w/12/12 pitch + the 5' tributary of the addition w/ a 4/12 pitch w/a 40# snow load & a 10# dead load and with a 40# live load & 10# dead load w/a 12' second floor tributary width and a 100# dead load for 2nd flr. exterior wall.) I would go with a steel I-Beam over an engineered wood beam if cost is a concern. I agree with Jeff that you will probably need 4X3X3/16 T.S. to support approx. 26,000# reaction on each end. You need to give a lot more information about your project before anybody can give you an accurate beam size.http://bsbad.tripod.com
*Mike,I checked into using C channel on a recently installed beam, and it was prohibitively expensive as opposed to a I beam. We ended up lifting that heavy ass beam by by hand.This was about a twenty foot span, set the beam on 4" round steel columns on 12x12 by 1/2 inch plate on block. Filled the cores of the 12 inch block foundation with 4000 psi concrete to the footer.Cost me about $250 to have three beams sized and downloaded. If your looking to save a few bucks, this is not the place to do it.A major difference between a professional builder and a DIY is knowing when to hire and pay for expertise.
*RalphYour open wall plan sounds good, but, what you need is an engineer. A glue lam is not going to work for that size span. Everyone of these responses are right... size of beam?? size of supporting post?? size of point load footings?? Unfortunately, you'll probable going to have a beam that hangs down further than you want. One thing to remember, you are going to need to support that entire second story while you remove the existing wall and set the new beam.Good luck!! Let us know what you decide.
*Any outdoor span over 20' is legally a bridge, requiring inspection by a qualified Professional Engineer every two years, yet people want a table for 30' spans in houses. Who here wants to drive over the river on something your neighbor looked up in a table?No one asks for DIY appendectomy charts, or how to pull their own wisdom teeth, and only on TV do people represent themselves without legal counsel. A man with a span chart is a dangerous thing.
*bj... the walls of hell are papered with span charts... hah, hah, hah
*Jon- Had no idea!!!! Guess the leap from a simple window or french door installation to a larger span is more than I can do. Thx' for the advice.RA
*Matt, et al:As a first- timer in the Breaktime, I am blow away by the response and advice. Way more than I anticipated - thank you all !!!! Yes, solicit an engineer is the best advice as most of the responses uncovered things beyond what I had envisioned. Sorry for not responsding sooner, buy my regular job keeps me way to busy. Thanks again- you all were GREAT!RalphKen Caryl area, Colorado
*Boss- You seem to be a regular here....Sorry, but I have to steal time at work to check messages. Home bandwidth sucks.Great resource -you all. I'lll visit more often.RA