My wife and I just purchased an old house. The walls are in terrible shape, so we plan to replace the plaster and lath with beadboard and drywall. But when we pulled the lath off the outside walls, we found more plaster and lath between the studs. It effectively creates a channel on the inside of the bay. We want to insulate the walls (there is blown-in cellulose on the outside of the bay, but it can’t be much), but I don’t know if taking out the stuff will affect the structural stability. Should I take this out and block the walls? Should I settle for adding a little rigid insulation (3/4 inch) between the studs? What is the purpose of the plaster and lath inside the studs?
Discussion Forum
Discussion Forum
Up Next
Video Shorts
Featured Story
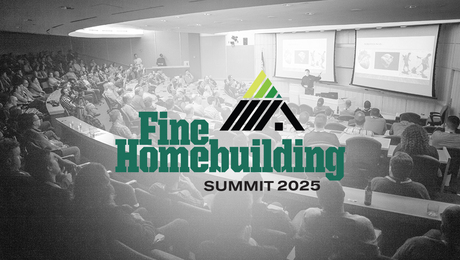
Join some of the most experienced and recognized building professionals for two days of presentations, panel discussions, networking, and more.
Highlights
"I have learned so much thanks to the searchable articles on the FHB website. I can confidently say that I expect to be a life-long subscriber." - M.K.
Fine Homebuilding Magazine
- Home Group
- Antique Trader
- Arts & Crafts Homes
- Bank Note Reporter
- Cabin Life
- Cuisine at Home
- Fine Gardening
- Fine Woodworking
- Green Building Advisor
- Garden Gate
- Horticulture
- Keep Craft Alive
- Log Home Living
- Military Trader/Vehicles
- Numismatic News
- Numismaster
- Old Cars Weekly
- Old House Journal
- Period Homes
- Popular Woodworking
- Script
- ShopNotes
- Sports Collectors Digest
- Threads
- Timber Home Living
- Traditional Building
- Woodsmith
- World Coin News
- Writer's Digest
Replies
That was done to baffle drafts and keep the wind from blowing through. Think of it as an ancestor to Tyvek.
;)
I wouldn't take it out and lose all that cellulose without the ghostbusters to help cleanup and a bank to rob to pay for it all. If you have the dimensional space, add a layer of foam insulation on the inside of the studs, then sheet rock over it. That will give you a vapour bar and prevent thermal bridging. To do it good, you'd be adding an inch of foam panel and a half inch of SR totaling 1-1/2". So if the plaster and lath you took off was 5/8" or so, you'd need to use extension jambs at the windows when you re-trim. Or, if you left the casings in place, you could fit foam the same thickness as the palster & lath in behind it and then finish SR up to it providing it is the older, 15/16" thick casing stock.
Excellence is its own reward!
"The first rule is to keep an untroubled spirit.
The second is to look things in the face and know them for what they are."
--Marcus Aurelius
Piffin:
A double-layer of lath and plaster is something I haven't seen before. What year were they doing this sort of thing?
Is the sub-layer actually between the studs, like I think Steve is describing? How much space is there between the surface of the sub-layer and the back side of the lath of the finish layer?
The houses where I've seen this were all over a hundred years old. I have read that it was fairly common aboput 160 years ago. It is a weak sand/lime grout plastered on the inside of the exterior sheathing. They would usually plug the base of the studs space solid since that was the main point for drafts.
I was some kind of shocked the fiorst time I saw it, thinking at first, " Boy, they sure got sloppy with that plaster job." until I got the wall all openned up to see it all.
It's really not suprising as an evolution in construction technigue. For thousands of years, some version of wattle and daub was the way we kept ourselves warm and separated from a hostile environment..
Excellence is its own reward!
"The first rule is to keep an untroubled spirit.
The second is to look things in the face and know them for what they are."
--Marcus Aurelius
Yeah...pull it out....its your can `o worms. Sounds like this outta be a room by room project though.....unless its too late for that?
J. D. Reynolds
Home Improvements
"DO IT RIGHT, DO IT ONCE"
Steve
If Piffy didnt get here before me I'd have told you the exact same thing. I also thought to use riged foam boards on the inside. Use the dense stuff with higher R value. The only thing I can add is that if you dont want to deal with the extention jambs and it looks right, you might consider adding onto the outside of the moldings to project it into the room with more detail.
Have fun.....
Namaste
Andy
It's not who's right, it's who's left ~ http://CLIFFORDRENOVATIONS.COM
Steve:
As others have pointed out, if you build up the thickness of your wall (with extra layers of insulation, rock, etc.), you will need to build out all your window and door jambs to accomodate the new depth.
You haven't mentioned whether you plan to do any new electrical work. If so, it's a good idea to do so while the walls are open, and this might be an additional reason to tear out the existing work.
Demolition work is cheap and easy compared to finish work, so I would suggest keeping the original jamb depth intact. Furthermore, if you have jamb extensions in some rooms and not others, it might look funny, depending on your level of sensitivity to congruency and historical detail.
When you put up the new rock, fur out the faces of the studs so that they're in a common plane with respect to one another, and with respect to the jambs. Sometimes, the old lath works well for furring. You can also get cardboard butt strips that are about 1/8" thick for the same purpose. Also, consider using 5/8" rock if it will help match things up to existing conditions.
Ragnar
The plaster and lath is actually between the studs. There are scrap 1X2s nailed in between the studs, on edge (so you can see the 2X side when looking straight in from the room). So you end up with a stud bay with a 1X2 about 2 inches from the outside 1X10s. Then the lath is nailed onto the 1X2s, running vertically. The plaster is on the interior side or the lath, leaving about 3/4 to 1 inch between it and the normal layer of lath. This runs continuously thru the second floor wall. I have no idea how old the house is, but the earliest renovation we can date so far is 1934.
Steve,
Thanks for the clarification. It sounds like what you have is something even Piffin has yet to encounter thus far!
What part of the country do you live in? Can you tell me anything else about the house? Does it have any original windows and doors? Ceiling heights? These pieces of infomation sometimes help to date the house....
Ragnar
I've seen this identical setup several times in houses here in Minneapolis, usually dating to about the turn of the century or earlier. I usually wind up knocking it out of any bay that I have open and putting rigid foam or cellulose in its place. I wouldn't bother with fiberglass in an old house (and not in a new one if I could avoid it, but that's another issue...).
Steve
Working on a 100 year old house. Yesterday was tear out old plaster, 100 years of dirt and even a few artifacts. Tearing out to empty stud space is always a challenge and the temptation is to do only what is necessary. But the day after you clean the dirt out of your eyes you will be glad. Today we made some new headers and widened doorways. It is good to see what is in there.
Now we can insulate and finish much easier. Biggest down side of course is that the plaster man was the last one in and his job was to make everything plumb. Now it is our challenge to shim.
Richard
First floor walls are 8 and a half feet; second floor walls are only 5'1" before they intersect the roof line on the east and west and are 8' on the gable ends (N & S). The house is in southwestern WI, not too far from the ones STEVENZERBY has seen. Maybe it's a regional thing. I think I'll leave the plaster intact - as a substitute for blocking between the studs. The doors and windows are mostly original, but are in bad shape. They are all being replaced, as is all the wiring. Thanks to everyone for the responses and the help.
Steve,
I worked on a bunch of houses in Central Maine years back that all had stud plaster walls. The ones in the best shape all seemed to have the same thing in common. The outside bays were uninsulated all the way to the attic.
The most common framing method I saw was that the posts extended from the sill to the top plate which generally was a 5 or 6 x 12 or 14 inch beam on its side with the posts mortised into it. This beam usually was higher than the attic floor, and formed the soffit under the rafters (which did not have lconventional tails). Floor and ceiling joists running perpendiculat to the top plate were usually supported by an inlet 1 by on edge. Beams and girts mortised into posts carried joists running parallel to the top plate. There was unobstructed air flow into the attic from the outside bays, around the old whiskey bottles dropped into them.
On those houses which were in bad shape (ie. every post rotted right at the junction of the post and the stud plaster, and of course at the bases) most, if not all, had been renovated. The attics had been insulated into and over the outside bays, vermiculite, sawdust newspapers, you name it had been stuffed into them.
My feeling is that once the airflow stopped, the rot started.
I would definitely be sure to be very meticulous in putting a good vapor barrier in before closing up your walls.
good luck
Clampman
No large beams or mortising on this one. But I was worried about the airflow. I don't know if the outside was designed to do that, but the inside does go all the way up to the second floor uninterrupted. (I haven't torn off the "new" asbestos siding on the outside or the second floor walls yet.) I do have the 1X4's let into the studs to hold the perpendicular joists, at least on the first floor. I will definitely put in the vapor barrier. Thanks for the tip.
Do you know if your house was originally built by Germans? Sounds like what you have is what's called "pugging." It was usually done just in floors, but sometimes walls in ballon framing. The purpose was for the control of sound, smells and fire. Shouldn't be too hard to find info on the practice. If you can get a copy of Millars, "Plastering, Plain and Decorative," you can read about it and other methods. It's also the history behind the blocking we do today.
Don
Actually, just yesterday I was taking off some more plaster and found some writing on a piece of lath. After all these years, I couldn't read it very well, but it looked like it had the German "double ss" in it. I sort of thought it was German, even though this is a Scandinavian area now. Thanks for the tip and I will try to get a hold of that book!
Steve,
For the book, try the library. There's not many around and you should be able to get it at least through interlibray loan.
With ballon framing you need to be careful of blocking your soffitseves. This depends on how your roof is built, and you may need to use the same vents you have to use for vaulted ceilings on your walls.
Don