I am looking to build a new garage/shop and have had a set of plans made up at the local menards to build a pole building that at some point I would like to heat and finish the inside est cost of $ 17000 so its on hold untill spring. Now a buddy of mine is looking to sell a stick frame garage kit but its a little smaller but also about half the cost. My question is should I wait and spend more money and get what I think I wanted or should I get the stick frame building because I have been told its a better form of construction and would probably be big enough 50 x 28 verses 62 x 42? I am not a builder but have built a number of pole frames over the years so I know how they go together but the stick frame will be a learning process but I am sure I can figure it out in the long run. The biggest problem is if I want the stick frame I need to pull the trigger now but would probably stil have to wait until spring to erect as I do not have a slab or a permit yet and winter is here. and ideas?
Discussion Forum
Discussion Forum
Up Next
Video Shorts
Featured Story
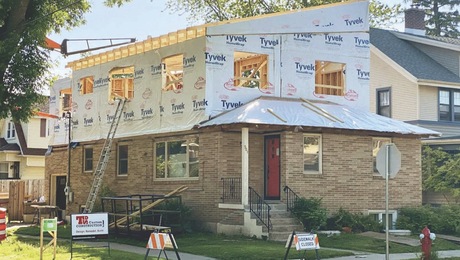
Get expert guidance on finding a fixer-upper that's worth the effort.
Featured Video
SawStop's Portable Tablesaw is Bigger and Better Than BeforeHighlights
"I have learned so much thanks to the searchable articles on the FHB website. I can confidently say that I expect to be a life-long subscriber." - M.K.
Fine Homebuilding Magazine
- Home Group
- Antique Trader
- Arts & Crafts Homes
- Bank Note Reporter
- Cabin Life
- Cuisine at Home
- Fine Gardening
- Fine Woodworking
- Green Building Advisor
- Garden Gate
- Horticulture
- Keep Craft Alive
- Log Home Living
- Military Trader/Vehicles
- Numismatic News
- Numismaster
- Old Cars Weekly
- Old House Journal
- Period Homes
- Popular Woodworking
- Script
- ShopNotes
- Sports Collectors Digest
- Threads
- Timber Home Living
- Traditional Building
- Woodsmith
- World Coin News
- Writer's Digest
Replies
How well can you insulate a pole frame vs. stick? That would be my first question, since you mention winter.
from what i have seen you can insulate but it does require more work/cost and that is one of my issues but I have seen it done well.
we do quite a few pole buildings... they save a LOT of money on excavation and foundation work
for a garage that size,,, if we stick frame , i'd have to pour a 48" foundation
we can easily insulate a pole structure just like a stick frame
so if you add the foundation cost to your stick frame.... then how do they compare ?Mike Hussein Smith Rhode Island : Design / Build / Repair / Restore
You say you want to finish the inside. Pole buildings usually dont fit well with finished interiors.There are no studs to affix your sheetrock or whatever to.
With a pole building we usually don't pour the slab until after the roof is on. That might make a big difference to your schedule. There are some construction details at my web site here http://www.chandlerdesignbuild.com/files/PoleBarnOutbuildingsDetail.pdf
------------------
"You cannot work hard enough to make up for a sloppy estimate."
I would not mind if the schedual gets a little longer as I am trying to build this without going into debt so taking it one step ata time my be the best bet for the budget. I guess my concern is how much more work will it be for me to finish the inside after I am done with the shell? the building in you attachment looks great but I will be using steel to try and cut down on maintenance.
I'm interested in knowing more details about the pier and post connections if you don't mind sharing. Piers always seemed like they would be easy to do while adding little cost, but I've never seen any details.I was really impressed with your website. At first I thought I was looking at a link to a magazine.
We pour the footings 24 x 24 x10 and set the posts using simpson post anchors that are big L braces that drill into the side of the post and hammer drill down into the footing after the posts are stood and braced. Once we have the roof on we screw the forms to the outside of the posts and pour the floor. pull the forms and do a z-flashing termite detail and go on the exterior with purlins and sheathing per the article generall don't notch anything build all up around a core 6x6 w/ jacks between the purlins and under the headers. We don't even notch the headers. Fast and dirty construction.
and thanks for the kind words about the site. I think if you go to the home page and drill down into green building details you'll find the second pole barn page that has better detail drawings downloadable. Still haven't up loaded the large pole barn drawing because the original needed to e re-drawn.
m------------------
"You cannot work hard enough to make up for a sloppy estimate."
Thanks.
I used stick framing for my shop (30x42') and skinned it with light gauge steel. With footing, block foundation, poured slab,plumbing, electric, insulation, drywall, doors, windows, and HVAC I have about $22K in it. That is with me doing everything except pouring the slab, and that figure was payed out over three years, over six years ago.
I'm with Mike smith on this one. Run the numbers for the two different methods and then make your decision.
i'm not that sold on pole construction. you can have the same roof,siding doors on both buildings.the concrete floor cost the same. for what a pole cost every 10' you can buy 2x4's for a little more. but the extra cost comes in on foundation,with stick you have to excavate and pour the footings and foundation,which if your where it's real cold can be pretty expensive,so to me thats the difference in cost right there.maybe 4-6k on a 2600' building
if you was to buy your buddies kit what would keep you from expanding it out another 20'? if you need or want a 2600' building ,you won't be happy with a 1500' building.that is quite a difference and tells you why it's half price.
if a man speaks in the forest,and there's not a woman to hear him,is he still wrong?
Something to consider.. depending on where you are at it might be difficult (or impossible) to get a permit for a pole building that is a matter of course for a stick framed one..
Some communities have real prejudices against pole buildings and no such issue with stick framed..
By the way if you are interested you can build a timber frame for much less than you can build a Menards pole building..
(assuming that you live near a local sawmill).
The reason is sawmills sell wood for a tiny fraction of what even big box builders like Menards sell wood for..
You don't have to do all the mortice and tenion work you can lag bolt stuff together or even nail it..
You all have some great points
1) I was told that I could just pour a thinkened edge slab rather than dig a full foundation is this true? we are in wisconsin and I did build a pole building at my shop with just a six inch slab and it is holding fine after two years but ie is also unheated storage and I do plan to heat mine in the future.
2) I live in a ag area so a permit should really be no problem. Most of the nieghbors have at least one shed or barn and most are some form of pole building.
3)I agree about the size not making me happy I guess I hust thought it was a very good deal but the more I look at it I will probably be better off just getting what I was think of in the first place.
4) now that I will probably move ahead with the pole concept any suggestions I see french says I can timber frame for less any books on this? the only timber frame I have seem are the high end units used in log cabins etc.
nathan... if you're planning on heating it....i'd go with a fully insulated slab and put radiant heat ina lot of the answers are going to depend on your local code and your building inspectorMike Hussein Smith Rhode Island : Design / Build / Repair / Restore
I was told that I could just pour a thinkened edge slab rather than dig a full foundation is this true?
Depends on your BI. I live in a part of NY where we can build like that, but the cities where the BI are more strict, frown on it.
Forget the high end stuff. Just think, do you want to build with round poles or square poles? It's that simple.. Timberframeing uses timbers instead of poles and because they do so they use what's called heart centers of logs.. Now the going price for a 9"x7" x 8 1/2 feet timber is $20.00 at most saw mills because that's what the railroads pay for a tie before it's treated.. Most mills will sell 18 fot long versions of the same for $40.00 each.
How much does Menards want for their poles? See how you can save money? Just so you know you can make those timbers out of any wood you want the price is the same.. I'd suggest using ash instead of oak for 2 reasons.. it's nearly as strong as white oak and it doesn't need stainless steel nails/ bolts etc. to build with.. If you use regular nails into oak the tannic acids in it which give it it's decay resistance will rust the nail and rot the wood.
Right now ash is really cheap due to it flooding the market because of the green ash borer. so the purlins and etc. would be really cheap. I wouldn't be surprised if by using ash as barn siding rather than tin you would save a lot of money. Wait at least a year or more before painting it though.. if you nail it up green and paint it right away the paint will always blister off quickly. Wait a year or two and then paint it and the paint will really adhere well. Don't brush paint it, too labor intensive.. use one of the big commercial airless sprayers and you'll have the whole thing done in a few hours..
Finally Yes I've seen a lot of buildings go up around here with nothing more than a six inch slab. If you are going to heat it though, pour the slab over foam and then bury loops of pex tubing in it for in floor radiant heat.. It'll be the nicest most comfortable shop around. (cheap and easy to do)
There are some details if you'd like I'd be willing to share with you on how you can make the building more durable and stronger. Also consider the insulation package. Fiberglas makes a lousy insulation.
Pier footing design is typically extensive (note one of your replies 22"x22"x10')for each pole location. Not everyone wish to dig a 10' hole for each pole. This is because the load is concentrated at each pole versus distributed loads on a continuous foundation and less depth too.
I have done hybrid systems.
Posts for structure and the trusses for pole barns, stud infill , non-bearing and built after the slab is poured.
Gets you a quick roof, sheltered work area for stud wall construction and easy to fully insulate. Also gets you a covered area done fast for out of heavy weather storage.
If you are going to pour a slab you can avoid localized loading by putting a bottom plate on to spread the load.. just remember to isolate the plate from the concrete.