Pour the whole thing, at once. Slab on grade with thickened edges, garage, drop, curb
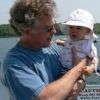
We’ve a little discussion going on over on the forum for the users of the software I use to draw house plans. It concerns how well the software can model the kinds of foundations done in the sunbelt states, where it does not freeze.
The talks there center on whether the 3D model the software can make, is an accurate representation of how the actual build takes place. The goal is to be able to have software produce a 3D model, from which 2D plans, sections, and details, can easily be taken.
A very simplified slab foundation is shown here in the picture.
Note that there is a thickened edge around the perimeter, per the text on the pics. Note also that the garage floor is dropped 6″ from the house floor, and that the garage has a curb feature.
Would your foundation specialist form and and pour this monolithically? If so, what would be the method employed to form the step from garage to house, and the inside faces of the garage curb?
If instead he would do it in more than one pour, what would be the sequence, and why?
Replies
Mono foundations
Gene. I am not a foundation contractor, but I have been designing/drawing this type foundation for more years than I care to think and have watched hundreds being poured..
To answer your question, yes around here we would pour the house slab and the dropped garage floor all at one pour. If I were more skilled in computers I would show you how we would draw our foundation plans and detail them. I'm still paper and pencil.
At the drop, we would install/stake in a temporary form that would be pulled as soon as the concrete had set up enough to support it's self, then fill the hole left by the stakes and finish out as usual. I always detail the temp. form to be beveled so as to allow for the proper slope to the garage floor.
Gene I hope the makes sense and answers your question. If I can be of futher help, just holler. I don't know how one does it in this new form, but if I had a fax # or a mailing address, I would be glad to send something if it would help.
I just got smart enough to look at the enlarged pic. What I originally stated still applies, except that the sloped temporay forms would be along the curbs. I would probably have a 3&1/2": drop at the house and bevel a 2x6 from 3&1/2" to 5&1/2" at the curbs. The curbs at the front/door would then be 5&1/2". This creats the sloped garage floor I mentioned above.
Insulate mono slab?
I see you're in Texas, so maybe you don't have to, but we have to insulate a turn down slab to R-10. If you do too, how do you detail that?
I think for a monolithic pour, the insulation might have to go on the exterior and then you have to flash or finish it on the exterior. Surprising to me that NC requires the insulation, I assume the climate is quite mild there? Or do they require it for the cooling loads?
It gets cold for short periods...
and an exposed slab transfers it.
Currently, we put it on the outside of the slab, and extend out whatever distance the particular project requires. Covering it, is the inelegant part.
I've looked at some insulated systems, but the exposed vinyl looks exactly like exposed vinyl.
R-10 everywhere?
All edges, and every single bottom surface, so there is no slab-to-soil contact? No footing-to-soil contact? Just curious about your code requirements.
On tract homes for years we did it in three pours; the footings and garage mudsill first, the house slab second, and then the garage slab third. They would nail expansion felt around the perimiter of the garage slab to act as a screed to guide the slope of the garage floor.
If they were behind schedule they would occasionally pour monolithic garage slab and mudsill footings.
Kuffel, were the tracts in CA?
Thanks for your input.
Your pic didn't open for me but I can comment.
My concrete guy will form the main slab with curb extensions for the perimeter of the garage. The garage floor is cut to the grade and and slope spec'd. The curb, except for the garage door opening, is a set of parallel forms, deeper on the inside because of the step down and level with the main slab forms, which include the depth of the footing. A #5 rebar is suspended in the top center of the curb form as well as the 2 #5's in the trench.
This curb and footing and the adjacent slab footing and slab portion is poured first and then the rest of the main slab, By the time the mono slab is poured and screeded, the curb is set up enough so the inside form boards are pulled, the curb is troweled smooth and a sloped line is snapped on the inside face of the curb. The truck then backs up into the garage area and the garage floor is poured with the guys troweling and screeding to the snapped lines.
When the truck clears the garage entrance that entrance is quickly shoveled to provide a thickened edge (not a footing), a form board is dropped in across the opening and the pour and screeding is completed.
I had a photo of this in a thread before the changeover and don't happen to have it on this computer.
Thanks a lot, Ralph. Some quesions follow.
Can you give me a better description of the method for forming the garage curb? I'm not getting it. See my pic, attached, that shows my idea of how a section cut might look along a garage wall. The red things are form boards, and both tops are level and with their tops at mainfloor elevation for the house. The outside form makes the total face of foundation, from top to bottom of footing. The inside form makes the face of curb inside, and forms it down far enough to allow for the sloping slab.
The first big pour that does the house slab and its integral edge footings, includes these garage curbs and the thickened "footing" underneath them, and then with enough set-up, those inside-face forms are pulled, and things proceed as you so well describe.
Does my pic show things as they get done? Is there in fact a wider "footing" under the curb edges as I show, or is the footing just the width of the curb itself?
As for the sloping garage floor, what would you say is the typical fall from back to front, for a 24-foot garage depth?
I got both your screen shots now.
I think you understood my explanation. The footing is wider than the curb and the inside form would be suspended so the perimeter pour would ooze up somewhat on the garage side but not enough to impede removal of that form board. The slump is pretty stiff and can fill the form without trying to seek level like water would.
I've got a whole sequence of photos of the job with exactly what you are describing. Let's see if I can post them.
Continuation of garage photos:
Yes, the tracts were in Southern California. They wouldn't even finish grading inside the garage until the house slab was poured.