*
Nick,
I designed and installed a radiant floor heating system in our home now occupied for 6 winters which in Winnipeg Canada are harsh (-32 design temp). The installation used almost 4000 feet of 3/8″ ID Sceptre triple wall tubing stapled to 3/4 fir ply on 16″ o.c. joists and topped with 1 1/4″ Gypcrete. Finished floors were either ceramic and granite laid directly on gypcrete or hardwood (maple, walnut and cherry). Hardwood was 3/4″ x 2,3,4 or 5″ widths applied to 1 1/4″ fir sleepers screwed to subfloor on 8″to10″ centres. Tubing went between sleepers and gypcrete poured level with sleepers. I designed this approach before reading about similar designs in FH a few months later. In all the years of operation, the heating system has never made any popping sounds or developed stress cracks (I still have a few uncovered areas of Gypcrete where I can guage this). The amount of movement by the wood floors between summer and winter is minimal and very acceptable. It is the only way to go for comfort and cleanliness. Hope this helps. Alex
Discussion Forum
Discussion Forum
Up Next
Video Shorts
Featured Story
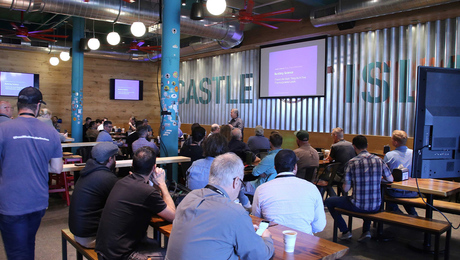
Listeners write in about shower panels and cordless tools and ask questions about old wiring, air leaks, and gutter covers.
Featured Video
Builder’s Advocate: An Interview With ViewrailHighlights
"I have learned so much thanks to the searchable articles on the FHB website. I can confidently say that I expect to be a life-long subscriber." - M.K.
Fine Homebuilding Magazine
- Home Group
- Antique Trader
- Arts & Crafts Homes
- Bank Note Reporter
- Cabin Life
- Cuisine at Home
- Fine Gardening
- Fine Woodworking
- Green Building Advisor
- Garden Gate
- Horticulture
- Keep Craft Alive
- Log Home Living
- Military Trader/Vehicles
- Numismatic News
- Numismaster
- Old Cars Weekly
- Old House Journal
- Period Homes
- Popular Woodworking
- Script
- ShopNotes
- Sports Collectors Digest
- Threads
- Timber Home Living
- Traditional Building
- Woodsmith
- World Coin News
- Writer's Digest
Replies
*
Nick,
I designed and installed a radiant floor heating system in our home now occupied for 6 winters which in Winnipeg Canada are harsh (-32 design temp). The installation used almost 4000 feet of 3/8" ID Sceptre triple wall tubing stapled to 3/4 fir ply on 16" o.c. joists and topped with 1 1/4" Gypcrete. Finished floors were either ceramic and granite laid directly on gypcrete or hardwood (maple, walnut and cherry). Hardwood was 3/4" x 2,3,4 or 5" widths applied to 1 1/4" fir sleepers screwed to subfloor on 8"to10" centres. Tubing went between sleepers and gypcrete poured level with sleepers. I designed this approach before reading about similar designs in FH a few months later. In all the years of operation, the heating system has never made any popping sounds or developed stress cracks (I still have a few uncovered areas of Gypcrete where I can guage this). The amount of movement by the wood floors between summer and winter is minimal and very acceptable. It is the only way to go for comfort and cleanliness. Hope this helps. Alex
*
Is radiant floor electric heat feasible?
I have a building lot in an area that does not have natural gas available. In order to have radiant floor heat it would have to be either electric, or LP. I'd like to stay away from LP if possible. Is it feasible/economical to have an electric hot water radiant system or do they really need to be gas fired?
I live in the mid-south-east US, so our needs for heat are modest compared to some of yours. Most days, the temperature gets above freezing, and it hits zero (Fahrenheit) about 2 nights a year.
Also, what about these attach up under the wood subfloor radiant heat systems I've seen advertised (in FHB, I think)? Common sense says that having the heat tubing under the subfloor wouldn't be nearly as effective/efficient as the system Alex S. describes - which sounds way warm.
Alex - I've never seen a radiant floor system - is the Gypcrete installed before or after the interior (non-load bearing) partitions?
Full of questions….
Matt
*Alex, Thank you for the info on the radiant floor heat. Not to be a pain,but when the system is off and you get that first cold snap of the fall or winter, how long before you feel the heat at a comfortable level does it take after you turn the system on. thanks greatly, Nick
*
Hello Nick,
I normally turn our system on in the fall when inside temperatures drop to between 65 and 68F and outside temperatures are consistantly below 32F. Inside temperatures will attain 68F quickly, say within 0.5 - 1.0 hr. This is the advantage of a thin slab thermal mass. Achieving comfort levels quickly is also a function of the high insulation values in our walls (R44)and ceilings (R70). The thermostats are set at 67-68 and left for the entire heating season. We do not set back at night although with the relatively rapid response of the system it would be feasible. I have four zones, each with four circuits, in the house, each governed by a simple thermostat. I initially gave some thought to individual room controls but ultimately decided to simplify to four zones and found it completely adequate.
*Hi Matt,I think you have two choices. (1)I believe Infloor, a subsidiary of Gypcrete, still offers an electric wire-in-gypcrete version of their radiant floor systems. Wire spacing in the floors will depend on your heating load and design temperature. (2) I have seen hydronic systems that rely on simple electric hot water tanks as heat sources. Again, you must determine your heat load and the capability of the electric tank. It has been six years since I researched and designed my system and there may be other equipment options available today. I am using a Polaris natural gas (also available in LP)condensing unit rated at 100,000 BTU input and 94K out for my floor and DHW systems. I used HotCan software to determine my heating load (about 35,000 BTU/Hr at -32F). We poured the Gypcrete after all interior partitions, furing strips (for hardwood finished floors)and tubing was in place. Alex
*
Matt: As Alex points out, you could either bury electrical heating wires in the slab or heat hot water electrically - in either a tanked or tankless (instant) hot water heater. The water pipes are put in about 1 linear foot/ square foot and cost $.50-.60/foot. If the wires are less than $1/foot that'd be the cheaper way to go. And if you put in multiple loops of wires and one ever does snap - you've still got a heating system.
Double check your comparative energy costs. I've bought propane for between $.90 and $1.30/ gallon, depending on location, quantity and my willingness to shop around. Assuming $1.30/gallon and a cheap 75% efficient hot water heater, 1 million BTUs costs $17.33. That equals electric at $.059/kwh which is cheap for electricity. Although WA and OR get it for half as much, NY'ers pay twice to triple that. And in Kenai, Alaska, we sit on top of a natural gas field, so the choice is obvious and cheap ($3.80/ million BTUs).
-David
*It's having a well- to super-insulated house (like Alex's) that eliminate any concern over thermal expansion/contraction of the wood flooring. The tighter the house, less the heat load. The less the heat load, the lower a floor temp will maintain happy thermostats. In 50's and 60's construction radiant floors were 30-40F above roof temperatures. My elementary school floor was HOT to the touch (there was a whole wall of single pane windows). Modern, tight houses need so much less heat that floor temps are only 4F above room temp - far less temp rise than from the sun shining on a section of floor. So if your house will be insulated and vapor barriered to modern standards, don't worry about it. Alex: You mentioned miminal floor movement summer and winter. I suspect your floor boards are smaller in the winter (low humidity in the interior air outwieghing any heating from the radiant slab) and larger in the summer (due to the same summer-time humidity that causes the bath towels to mildew on the towel rack). ??-David
*
F.H. editors, I think this would be a great topic for articles on a regular basis; there are so many options available to builders/owners and it often seems to involve more than just the HVAC trade for planning and installation.
Here's my question. Can I retrofit a system that is stapled to the bottom of a 3/4 inch ply subfloor which is covered with a finish floor, say 1/2 to 3/4 inches thick and has carpets laid over much of the area? I realize that it would be slow to respond, but all that heat eventually has to go somewhere; won't it rise to the top of all those layers and begin to warm the house?
*Hi Dave,Merry Christmas! Yes essentially you're correct. The floors contract in winter with the heat on and expand in summer with heat off. But interior humidity also plays an important part in floor tightness. Right now my floors are about as tight as when I installed them. According to the humidistat on my HRV, we are maintaining about 50-55% RH in the house and this helps to keep the floors in a "summer tight" condition. As winter progresses and absolute outdoor humidities drop, indoor moisture drops to 40 -45% and the floors open a wee bit but its short lived because we shut heat down in spring. It's a very natural cycle. Alex S
*Hi David,Once again, it depends on your heat load. Once you know it, you can determine if your retrofit can deliver enough heat through the finish flooring plus carpets to keep the room at the desired comfort level. In the past, Infloor (TM) provided a heating system designing guide which determined the required tube spacing adjustments for different types of carpets with different insulating properties. Alex
*Alex S 1:00am Dec.26,1998 EST. First time on FH. With the radiant floor heating is the air up around the chest area cold or do you feel warm all over. Is a gas fired boiler the best way to go? Is there a good place to learn about this sustem as I am trying to get the nerve up to build my house. I have really enjoyed reading this column. TAnde
*Hi Terry,My experience living on radiant floors for 5 winters is the best source of data that I can offer. Perhaps the most remarkable attribute of radiant heat is the complete uniformity of heat distribution, both horizontally and vertically. Inspite of a relatively open home design with several levels, temperatures are uniform from top to bottom and our chests never feel cool relative to our feet. (Uniform vertical temperature profiles are often quoted in advertising by manufacturers and suppliers of radiant floor systems.) In addition, I have never heard complaints from family members about cold drafts from fresh air supply ducts thoughout the house. I would suggest that gas boilers with their high recovery rates are a good way to go but individual case needs will dictate approaches to take. If your heating climate is not severe, simple hot water tanks, gas or electric may work. When I began to learn about floor systems about 10 years ago, there weren't as many suppliers as today. Infloor, Staedler, Heatway were the main choices. I obtained an Infloor Installer's Training Manual which provided details for system design. I found a local tubing and component supplier and together we customized a system for my home at a much better price than what the main contenders were asking. Today you can visit several websites to view their offerings. I see that Gypcrete products are now produced by Maxxon at http://www.maxxon.com. Hope this helps. Alex
*Matt, why don't you use an ordinary hot water heater for a heat source? These things can be set up so both elements will come on at the same time. (Naturally, the branch circuit wiring has to be heavy enough to meet the code for the higher load.)
*
Terry: All air above the floor is a fairly uniform temperature. Unlike heating with a wood stove, forced hot air, or baseboards around the perimeter of the room. With these point source of heat, hot air rises over the heat source and pools at the highest point in the room/house. This rising of hot air is an advantage only if 1) your heat source is low (e.g. wood stove in the basement), 2) you are trying to circulate air with any fans (living off the electrical grid?) AND 3) you don't mind the hot ceilings and cold floors. But for the rest of us, the diffuse heating of a radiant floor creates more uniform temperatures and without the convection of a forced-air system, you can set the thermostat 3-4 degrees lower, saving energy. Natural gas is always the cheapest way to heat if you can get it. But you don't actually want a "boiler" that creates steam. One of the efficiencies of radiant floor heating is that the water in a water heater (and it can be an off-the-shelf hot water heater, $119 from Home Depot) is 80-90F and that boosts the heater efficiency beyond the nameplate efficiency generated in standardized testing.
I liked the literature that Radiantec (www.radiantec.com 1-800-451-7593) sent me. They included ideas for both sophisicated and simple, cheap systems and include prices for all components and rules of thumb for calculating materials and operating costs.
Good luck with the house! Go for it!
-David
*
AlexS and David. What type of heating systems are you useing, and what type of floors do you have in your homes. I live in Ohio, as a kid it would get down in the o,s but not like that any more.
can a water heater work, is there a limit on how hot the water should be. A Happy Holiday thanks.
Terry
*Alex S and David thanks so much for your reply.I like the idea of usuing a water heater to heatmy house, would be a great savings. What type of floors do you have or recomend. A Happy Holidaythanks. Terry
*
Check out a recent Journal of Light Construction Article at "www.jlconline.com/jlc/archive/energy/water_heater_heat/index.html"
*
Alex S and David thands for your help. In your homes do you have different types of flooring; carpet,wood,tile,or ceramic. Is there a great deal of difference, do you prefer one over the other. A HAPPY HOLIDAY GREETING AND THANKS.
TERRY
*
Terry: I'm in a rental house in Kasilof, Alaska (was -22F this morning) as we plan our owner-built house on the shores of Cook Inlet and wait for the ground to thaw. The rental has radiant slab in the basement and radiators around the perimeter of the first and second floors controlled with thermostatic flow valves at the base of each radiator. It works pretty well. The finished basement is amazingly comfortable - very uniform heat and much more livable than most basements. The second floor gets too hot when it is above 10F outside if we leave that loop on. So we only turn on the upstairs loop when it gets cold.
In the slab-on-grade house we will build, there will be radiant in the atached garage (great for melting the snow and ice off the car and evaporating the resulting puddle) and radiant slab in the first floor kitchen, dining and living rooms (open floor plan) under hardwood flooring. The upstairs loft will be open to the heated floor below, so will not have a seperate system except for the upstairs bathroom and guestroom which will have a fan (to get air heated from the wood stove) and a hot-water radiator loop for when the wood stove is not on. I'll use a hot-water heater to heat the radiant slab and upstairs radiators. Still need to check into direct-went units - both tankless and traditional. I only need about 30,000 BTU/hour for space heating, but might use a direct-vent, 100,000 BTU/hour, tankless hot water heater. With an unplugged electric water heater as a storage tank operated as a zone off the tankless we'd have endless hot showers/laundry/dishwashing water without the temperature variations typical of a tankless.
Maximum temperatures depend on tubing type. Partially cross-linked polyethylene (POLY PXC) is rated for 150F at 50 psi. Fully cross-linked polyethylene (PEX) is rated at 180F at 100 psi. Hardwood, tile, carpet, or linoleum are all options. People seem more comfortable with the radiant tubing in a concrete slab. Reportedly, none of the contractors up here are good at installing gypcrete on a floor over joists. Therefore, if I was doing radiant floor on the second floor, I'd use the aluminum heat emission plates (mounted on the tubing) within the joist bays and skip the gypcrete.
-David
*
Hi Terry,
My heating system consists of a Polaris direct-vent,condensing, natural gas hot water tank (100,000 BTU/hr input, 94,000 output) in the primary loop that is separated from the secondary with a Stainless Steel Heat Exchanger. The tank can be adjusted to deliver water at temps ranging from 100F to 160F and it serves both my radiant floor system and my DHW supply so the system is very efficient. Right now my tank delivers 145F water to the exchanger and DHW branch. The DHW branch uses a tempering valve to limit maximum temperatures to 120F. Water temperatures delivered to my floors range between 80-90F so they are just warm to the feet. I used Sceptre 3/8"ID triple walled tubing (a middle aluminium layer, the air-barrier, encased in polyE) which is approved for both hot and cold DW lines and heating systems in Canada. My zone manifolds were made of copper with T-brazed fittings. I used appropriately sized pumps (Grundfos- one in the primary loop and 2 in the secondary),electric zone valves, expansion tank, air bleed, etc.
My floors consisted of 3/4" fir ply over 2x10" fir joists @ 16oc to which tubing was stappled and topped with 1 1/4" Thermaflor (Gypcrete). Floor coverings are 3/4"hardwood (maple,cherry,walnut) or ceramic. I fastened hardwood to 1 1/4" x 2 1/2" strapping screwed to the 3/4" ply subfloor with strapping perpendicular to joists. We have only a few scatter rugs, no carpets.
To ensure a properly sized system, you should do a home energy audit to determine how many BTUs/hr it requires to keep it comfortable in your climate. Knowing this you can decide if a simple hot water tank will be sufficient. Most heating specialists could do this for you or you could get software to do your own. I used one of the original HotCan programs to evaluate the heat load for my home.
I wouldn't let impressions of a warmer climate dictate the design you adopt for a heating system. One of the characteristics of "global climate change" will be more dramatic temperature extremes in both directions so our heating and cooling systems will need to deal with more variation.
Alex.
*Alex S I hope this isn't a off the wall question but what happens if there is an ice storm, wind storm, snow storm and the electric is turned off. Do you have a back up system. On my current wood/gas furnace it has an electric ignition so no electic no heat. Even with the wood burning the blower would not come on. If you had no heat for an extended period of time you could get some frozen florrs, an just ice skate indoors [alittle late 1998 humor]. A tip of the old champagne glass to FH and my radiant floor friends.
*Terry; Gutsy question! My initial plans for woodstove backup in our new home were quashed by my significant other who would not relinquish after years of wood ash, smoke and creosote produced by a wood stove (supplement heat only) in our first home. So we installed a direct vent gas piloted fireplace (23,000 BTU) and a gas cooktop (about 10,000 BTU - I can't recall exactly) that can carry the house for a significant period without power even at -30F. The open plan allows good distribution of heat to most areas of the house. PS I would still love to sneak in a wood stove because I miss sleeping in front of it with the dog. Cheers and good health in the New Year. Alex.
*I thought one had to be careful about using a water heater for both DHW and for heating a radiant floor; ie most heaters wouldn't last under the conditions of the regular hot water needs of a radiant system. Sacie
*
This thread, along with reading the article in
Journal of Light Construction (thanks for the tip
and the site!) about water heater-supplied radiant
heat, has gotten me to wondering about
retrofitting my slab-floored woodworking shop w/
radiant floor heat.
Has anyone done a real shade-tree installation on
top of an existing slab floor? I would not do this
on a permit, since the shop itself is not
permitted.
I'm wondering about insulation under tubing; and, is
there a reasonable alternative to expensive PEX
tubing? I suppose I'd float glued-together t&g
plywood on top, leaving expansion room around edges.
The JLC article fairly well covers the water
heater and other mechanicals.
Any experiences? Or even theories you wouldn't
mind letting the world se
*
Yep, you can put a radiant floor over an existing slab. You should insulate it as well as you can
afford to do (according to how much room you have)
otherwise you will be wasting heat on the slab
and the subsoil. It can be do with even a thin type of foam board, such as is used behind vinyl
siding. You can put an R-max down also. Then
either put down PEX (or copper tubing) and cover
with 1 1/2" concrete. OR you can put some sleepers
down, and run the tubing in the resulting air space. If concrete, use 12"OC, if air space heating, use 8"OC. My personal choice is PEX.
Prices are down. Be sure to use a tempering valve,
to supply water around 110F, in concrete, and up
to 160F if you are heating the air space.
I don't recommend using hot water heaters for
anything but small add-ons or shop building, say
below 30,000 btuh. Visit the manufactures web
sites, ie., Wirsbo, Stadler or the Radiant Panel
Assoc, or Dan Holohan's site for "wet heads".
*
Jim: While insulation under the slab is preferred, another perspective is that once you get the old slab and underlaying soils up to temperature, you don't lose much more heat. You do always lose a little downward and, if the perimeter is uninsulated, you'll lose some there (more, percentage-wise, in a small slab). Radiant floor heating in a garage is really nice in snow country. All the snow and ice melt off the vehicles quickly and the resulting puddles evaporate much more quickly. And in the winter, you're always trying to humidify the air anyway.
On the subject of doing radiant slab heating on the sly and on the cheap, is there a reason not to use PVC? Wouldn't have the corrosion problems of metal piping. I realize it doesn't take high temps, having explored the hairy edge of PVC temperature tolerance in many different ways (peak strength at 78F, pressure rating should be decreased for higher temps, gets really floppy at 140F and threaded joints can creep apart above 135-145F, depending on schedule). But in a radiant slab, fed through a mixing valve, you could keep the water to 90 or 110F. PVC is like 0.10/foot not 0.50-.60/foot like PEX. Heck, put it in at half the spacing and it could be operated even cooler. -David
*David,I was thinking about PVC, too, or, if necessary (probably not, from what you have learned), CPVC. BTW, isn't using radiant heat to melt snow in the garage kinda expensive? Or is it a perk that Alaskans need? :-) And/or meybe electricity is cheaper up there than here in Boobville, CA (12-13 cents KWH).TJ,You and David seem to be at odds about need for insulation. I suppose "common sense" tells me that a little insulation wouldn't hurt, especially if used with creepers instead of, say, gypcrete.You say prices are down for PEX; do you have a web-so
*Jim: Some additional thoughts on PVC: in addition to a mixing valve to make sure the PVC never sees really hot water, I'd also install a thermometer after the mixing valve to confirm what temp is going to the PVC - a peace of mind thing. Put in several loops (like in the diagrams any of the radiant floor companies put out) and bring them all back to an above-grade manifold. Although you can find leaks accousitically if someone should shoot a nail in the wrong place, it is nice to have the option of just cutting off one of four loops. Do really good joints - primer both pipe and fitting, glue both pipe and fitting, jam on, twist, and hold for thirty seconds. Leakless plumbing is just following ALL the steps, ALL the time.I agree insulation under the new slab is better. But it's a economic balancing act. High energy costs make it more important. If you have very high point loads in the shop, you'll get better total strength without the insulation (because you'll have 8 inches of concrete). But 4 inches of concrete on top of insulation ought to handle most normal loads fine.Cost of melting snow off car? After it's been broomed off but there's still ice in the wheel wells, door jambs, wipers, freezing the windows closed, there's maybe 5 gallons of water or 40 pounds of ice so that's 7,000 BTU to melt ($0.03) and 40,000 BTU to evaporate ($0.19). Based on $0.38/therm (cheap natural gas) and an 80% efficiency. So is it worth putting a quarter in the slot to defrost the car, get the windows working again, and avoid having to scrap ice off the windows? Oh yeah. And the heat to evaporate would have been required by the humidifier anyway (if you are trying to keep the garage humidified). P.S. the Kenai Peninsula lies on top of an oil and natural gas field. Electric is $0.0836/kwh, wood is free from any state land (dead or down spruce only). -David
*
I'm currently designing my own home here in SW Colorado at 7,000ft. I hope to come up with a simple radiant floor system that avoids much of the cost and complexity of some that I've seen.
Around here plumbers will commonly fire a floor system with a high efficiency, high-dollar boiler. When I want water that's around 100F., I can't see the need. Am I missing something? Some 14 years ago I installed a polybutylene (I know, I know) tubing-in-the-slab system fired by a $300, maybe 80,000 BTU Regular Old Water Heater. Big commercial one but nothing special. The owner still loves the performance. Excepting the ball valves on the circuits, there were two moving parts, the pump and the air vent.
I wonder about the possibility of putting the heating tubing in the poured concrete exterior walls of the carpeted bedrooms of my new house and running the same temperature of fluid in them as the tiled floors in other areas? The 6" thick walls will be insulated w/2" styrene on the outside and comprise half the perimeter of each room.I can't seem to find anyone that's tried this or even has an opinion.I'd greatly appreciate any feed back. Thanks, HY2K-1 Tim.
*I am very happy with radiant in-floor heating in my exposed 3500# house on Cape Cod...but is is super insulated and I embedded it in polished, colored concrete floors AND I have a small Vermont Casting wood stove for those sudden cold days and for the enjoyment of a fire in the evening. Look into the polished concrete if your not stuck on oak. It helped pay for the German high tech heating system. We put in the tubing and manifolds DIY. Used direct vented propane so no chimney was needed either. Cost is OK.
*
I am going to build my house within the year and am looking not for the cheapest heating system but rather the most efficient and have been considering radient floor heating. PROBLEM- I want to install wood floors (oak) and I am told by some plumbers that any time they have seen it installed under wood floors , it invariably pops and cracks every time the T-STAT calls for heat due to expansion and contraction. Also if a sudden cold front were to come through here in the north east during a mild fall (which happens a lot), the system takes a long time to come up to temp(days!). Does anyone "in the know" have the answers to these ?, or should I look at another heating system. thank you Nick