Hi all….have a question. Will be building a house soon in California. (Gold Country, in the Sierra Foothills about 2,500 ft.) Really think radiant heat would be great, but some opinions differ. When is radiant heat not efficient? If there is too great of a temp. difference between day and night? Seems for every expert opinion, there is an equal and opposing opinion. Any thoughts?
Discussion Forum
Discussion Forum
Up Next
Video Shorts
Featured Story
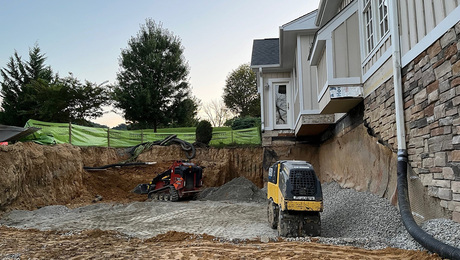
Listeners write in about ambitious projects and sinking patios before asking questions about old house specialists, attic headroom, and home shops.
Highlights
"I have learned so much thanks to the searchable articles on the FHB website. I can confidently say that I expect to be a life-long subscriber." - M.K.
Replies
Slab installations have a longer response time than other systems. As such, when in the "tween" season...not quite heating, not quite cooling...if you get a quick cold snap of short duration, radiant may not be the best bet in terms of comfort. It's slow to bring the slab up to temp, and by the time it has, you may not need the heat anymore and the house may be too warm. Gross simplification, but that's the biggest downfall I can think of.
Mongo. Do you think Warmboard would help with his system's response time?
--GoneSolo (aka Bernie)
P.S. As long as he installs one of your Defrizzilators with it!
C'mon...don't you remember anything? You can't use a defrizzilator with warmboard. They're not compatible. You need a frangelicator, sized at 2 amps per 100 square feet of floor space.
Warmboard, being low-mass, would give a quick response to heat demands. I think Jim covered the details pretty well.
For the other question, Warmboard is a subfloor with Al laminated in the center of it. It has grooves already routed so you can snap the tube in place. Convenient, though with some layout restrictions and required bvlocking under the seams. Pricey as well.
We do a lot of radiant heat in the homes we build. I know people do it but I do not recommend putting radiant heat under a floor system that will have a high R value, such as hardwood and carpetting with padding. It is best under tile floors, and by the same token that it takes some time to get warm, it also takes a long time to lose the heat. When it gets warm it stays warm.
A generically-designed RFH system based upon layout "rules-of-thumb" will work well under tile.
If using RFH under hardwood, it only requires a little more thought in the design layout.
Under carpet? I agree that some carpet/pad combos have high-r values that can make rfh difficult to design around. It can be used under carpet...but again, design and type of carpet comes into play.
I think the worst application is where you have a glue-down hardwood floor and there are either high r-value oriental rugs or W2W carpeting over the flooring. You'll need a higher water temp due to the r-value of the carpet, and that long-term higher floor temp can cause crystallization and brittleness in the flooring's adhesive. Depends on the temp, and depends on the adhesive.
Thanks for the response on the insulation.
Got another one for ya. You made a comment regarding WarmBoard way back in message 25444.8 about "required bvlocking" under seams. What's THAT?
(and does it draw more than 2 amps?) LOL--Solo
Remember, measure twice... then keep cuttin'
'til it fits really fine.
bvlocking": That's the European spelling of "blocking".
Oh man... If that was just a typo error, I'm really sorry. I thought that it was an abbreviation for something, you know, "trade lingo".
If you meant "blocking", then I know what you mean. I'm sure that some of the panel seams wil not fall over joists.--Solo
Remember, measure twice... then keep cuttin'
'til it fits really fine.
Yup, a typo. I've had a zillion of those lately. Check out the following un-proofed paragraph:
The clickking that came from my heavy paws ppoounding on the kyboard driives my son absolutely bonkkers, so I picked up a new, "siilent" keyboard. Made f siliicone and completey flexiible, iit's callle "Te Indestructable Keyboard." Unfortunatley, it misses soome letters and dubles up oon others.
The above is, as you can see...uncorrected. My son may now be happy, but now this keyboard is driviing me nuts.<g>
Sorry for the confusion.
Much of the between season issue Mongo discusses is affected by the rest of the house. Super-insulated or code-minimum? Orientation to sun? Glazing? Passive solar with high thermal mass, or no mass? If you have 3" of fiberglass in frame walls with no mass but for the 4" slab, then you'll have the problems with the mass not heating fast enough at night on a cold night/warm day. Such might be a good case for Warmboard with its quick ramp-up. But if you are built around passive solar concepts, with great insulation, and a lot of mass that can absorb some of the day's solar gain to moderate interior temperature spikes, then the RFH in a slab can work perfectly in tune with that. It might take some noodling around the first year to balance the system (find the right thermostat settings), but it'd be hands-off after that.
What's the rest of the house like, and what's its orientation to sun, etc?
Good questions, should have thought to give more particulars. Actually, we are very close to deciding on straw bale, so the insulation properties are excellant. We will also be utilizing passive solar and anything else we can do to keep us from being "owned" by P.G. and E. Thanks for info, will try and answer any other questions if needed. Thanks!
Edited 12/12/2002 9:51:28 AM ET by TOOLINAROUND
OOPS! Wanted to ask what "warmboard" is....also, we might be learning towards raised foundation. Thanks again. Becky
Google warmboard and you'll get to their site.
If you have a design that is passive solar, or high mass, such that you get a bit of the effect of a thermal battery (soak up and store btu's while the sun is shining, and transfer them to the inside when it isn't--in overly-simplistic terms), then I'm really fond of high-mass RFH (hydronics in concrete floor). From experience of building/living in such a beast, I feel they compliment each other well.
Warmboard is a lo-mass solution, and I'm sure they favor that instead.
I just worked on a house with RFH. I suppose it would be a low-mass system, it is under the wood floor in a layer of poured Gypcrete. the tubes were laied on the subfloor in 1 1/2" of gypcrete with a layer of 6mil plastic on that, then two layers of 3/4" plywood, then the finished floor. on both floors. the archatect who spec'ed this system told me that the key to it was that it had an external temperature guage that detected the outside temp swings so that the system could adjust accordingly. this prevents having the house warm up to 80 when the temp jumps up from 40 to 70. just another way that it could be done.
-zach
An outdoor rest should be a mandatory part of any radiant system. What is it? An outdoor reset helps maintain a comfortable temp in the house by varying the temp of the circulate dwater based upon the outdoor temp.
If the house is a cozy 68 degrees and the temp outside starts to plummet, the outdoor reset senses this outdoor temp drop and increases the temp of the circulated water. In essence, it "lead turns" the cold snap. Without the outdoor reset, the RFH wouldn’t kick in until the actual interior temp of the structure fell, and then, because of the lag time between the heat demand and the heat delivery, the interior of the house may get a little chilly before the heat is actually delivered.
The resets normally have "heating curves" or "reset ratios" that will adjust the amount of heat delivered in the ramp-up phase. This allows someone with a phenomenally tight and well-insulated house to have their system deliver less heat than someone with an older, drafty structure.
There are several other options available on many models that allows the user to customize the outdoor reset to their specific needs. Anything from automatic outdoor cutoff temps (no heat demanded when the outside temp is above a certain temp) to setback clocks (automatically lowers the temp at night and ramps it up in the morning) to a full manual override (ON/OFF/AUTO).
A radiant system without an outdoor reset is a poorly design radiant system.
Mongo, do you think that the outdoor reset would be as important in a Warmboard application, because of it's quicker response time?
yes
I want to apologize for my abrupt "yes" answer in my previous post. I live in a heating climate, and I'd say that an outdoor reset is a neccessity for RFH in my area.
Ask around your area and see what the installers say. You can also ask at the supply houses, and call tech reps at places that sell RFH materials like Wirsbo. They may be able to give you more specific information than my blanket reply.
Thanks, but no apology needed.
I'm in Michigan. We've had some days this fall that went from above freezing to down into the teens in a matter of a few hours in the middle of the afternoon.
My local WarmBoard distributor considers the resets to be unneccessary, His opinion is based in the context of bragging about his products response time. I will always value the advice of someone, hands on, in the field over a sales rep quoting a brochure.
BTW, can the outdoor reset component be added later without reworking much of the original install?
--Solo
In Michigan I'd recommend the reset. It can be added later. Tell your designer/installer that you may eventually put in a reset, as there are low/no-expense things that can be done during the initial installation that can make the eventual installation of the reset less ($$) painful.
Can you be more specific, mongo, about what can be done at installation to permit retrofit of a reset device?I am going to be using a Radiantec system with a Polaris heater, and they don't talk about the reset device, but the Wirsbo manual deals with it rather extensively.
Our house will be in Colorado at 8000', and extensive passive solar features. I am somewhat concerned about the disparity between Radiantec and Wirsbo on this matter. So What to do to facilitate retrofit?
Stef
Radiantech is very low-tech. Set up so the DIY can DIY. Not a bad thing, but they skimp a bit here and there with the technological services they provide.
Sounds like you're familiar with Wirbo. If you're using Wirsbo's tubing over Radiantech's, good job.
You need to ensure that your controller can accept an outdoor rest. That's it. If you have one, wire it in. If you don't, you don't. Normally there may be switches, jumpers, etc, that need to be set depending on circumstances. The manual for your controller will have the details.
I'm guessing that Raidantech will be bare-bones. Water heater, t-stat, circulating pump. Still works, but not as flexible or precise. One size fits all mentality.
I am a DIY'er, preparing for a major remodel in my house in the mountains of CO (8000', heating only climate), and have been convinced of the merits of RFH. The problems I am running into is the different brands and styles. In-slab tubing won't work for me, so I am looking at the various methods that work between floor joists or over the decking.
The general opinion I've gathered from this site is that Wirsbo has the superior product, and Radiantec may not be worth the money saved. But Wirsbo and Radiantec both seem to be using cross-linked polyethylene. Wirsbo installs on top of the decking in their Quik Trak system, while the Radiantec mounts under the decking using aluminum plates to disperse the heat.
Can anyone provide any insight on the differences advantages of the different mounting styles and brands? Is Wirsbo better because of the connections, or is the tubing better too? My budget is tight so I am looking for the solutions that will have the most effect for money spent. In other words, I don't want to buy cheap products just to save money (we all know that method ends up costing more in the long run), but I can't buy top-of-the-line on everything!
Thanks in advance!
-Rich
RFH doesn't have to be "all or nothing" when comparing one supplier against anoother. Feel free to take the cafeteria menu approach..."I'll take one of those, and two of those...", etc.
PEX is PEX...kind of. There are different ways to cross-link PE to get PEX. Some are more effective than others. The Engel Method is recognized as superior to others. When it comes to tubing, go with quality, and Wirsbo is quality. Others are as well, but Wirsbo is best known due too their heavy advertising.
Quik Trak iis effective, but pricey. If you need Al plates, you can buy stock sheet material from anyone...Radiantec included...form them on your oown and save $$$ in the process. It's very easy too makke a bending jig from scrap plywood and a piece of pipe, and the pieces can be pumped oout in no time at all.
Also, since this is a "major remodel" vs new coonstruction, staple-up is often easiest in terms of maintaining floor height since you're adding material under the subfloor instead of on top of the subfloor.
For a DIYer, I think an underfloor staple-up is easiest due to future considerations. It gives a liittle more leeway when it comes to installing underlayment/finish flooring. I say that only because I know of a few innstances where DIYers popped holes in the tubing, and they all occured in track systems. I've never known a DIYer that nailed through a staple-up. When modifyiing the first floor platform, you can access staple-up tubing (first floor) to ascertain its location, vs hoping and guessing with tubing buried in a track system. Again, these comments are geared towards DIY installations, and modifications down the road by DIYers.
For manifolds, you can cobble together your own for next to nothing, or you can spend hundreds for ready-made, highly adjustable manufactured manifolds. Sometimes being able to tweak water flow through a loop is desired, sometimes it's unneccessary.
I do use Tekmar controls and Taco pumps. Good stuff, zero complaiints. There may be other product out there that does as good a job for less money. Then again, you may not need total control. Depends on the design of your system.
One more thing, is your system is closed and you have a cast iron-type burner, you might want PEX wth an oxygen barrier. It's a couple cents more per foot, but it'll minimize rust in your system.
I think your easiest and least expensive system would be a RFH-dedicated gas-fired water heater. Sweat your own manifold(s) together, with the house zoned with manifolds supplying like-used rooms. Example...all bedrooms off one manifold and controlled by a t-stat in a bedroom. All day use living spaces on another manifold, controlled by another t-stat. Guest suite on it's own manifold, controlled by a third t-stat. Etc, etc. Wirsbo tubing. T-stats that open zone (manifold) valves and kick on circulating pumps. Have supply and return temp gauges on the manifolds so you can monitor supply and return temps.
Valves. On a tight budget it may be painful, but install more than you thiink yuu need. Try too install valves so you can isolate and item in your system without having too drain the system. A valve on each side of each manifold, etc. Single-throw, full-port ball valves are common and affordable, and donnt restrict water flow through the valve when their open.
It has been a while since I looked at Raduantec's offerings. I do remember their tubing being suspect. I thought their design layouts were simplistic, but do-able. I don't recall what they offered in terms of controllers.
Regardless of the type of installation that you do, insulate under the subfloor to encourage the heat to go where it's supposed to go...upwards into the livng space. I friction fit half-inch foil-faced polyiso insulation (r3.6) up against the tubing. If more R-value is needed, unfaced FG batts can be friction-fit up against the bottom of the polyiso.
I just finished a RFH job in Golden, CO, and will be doing another in Leadville this spring (elev 10,200).
Wirsbo probably is the best way to go and all their stuff in available at Geo. T. Sanders in Wheat Ridge or Silverthorne. I like the staple up method and have done several of them. However, be sure to use a foil faced insulation under the pex tubing with the foil face up.
If you go to the Wirsbo web site, Wirsbo.com, you can order a trial CD that will enable you to design your own system.
I have never used any material to embed the tubing in such as gypcrete, and have found good results with the staple up under hardwood and tile.
Glad to answer any questions.
Hi Mongo. When you said:
"Regardless of the type of installation that you do, insulate under the subfloor to encourage the heat to go where it's supposed to go...upwards into the livng space."
Does this include a WarmBoard installation? If it does, what type of insulation would you use?
Thanks.--Solo
Remember, measure twice... then keep cuttin'
'til it fits really fine.
In general, it's nice to have three tiimes the R-value under the tubiing that you have over the tubing.
With warmboard, pick your poison. The easiest would probably be unfaced FG batts, friction-fit and tucked up against the bottom of the warmboard.
Thanks for the great info!! I just spent an hour on the HeatingHelp.com forum getting discouraged about the possibilities of doing this myself. Your response, and Bob's tip about the design CD, have restored my desire to find a way to do this myself.
Will the Wirsbo program help me with a "heat loss analysis" that I have read about as a critical factor in designing my system?
My initial instinct is a closed loop system with a tankless to heat it. I will only have about 1500 sq. ft. and probably three or four zones. One concern is that if the system is closed, then I have to have another water heater for the house water. Is it conceivable to try it as a open system with one water heater and then add another (and close the system) if we didn't like the performance (or the taste) of the water?
Thanks again!
-Rich
All ya all ....Came across a DIY'er that did his version of rfh . Has 2by10 flr joists on a 12 foot span and he nailed 1by1 cleats to the inside bay of each floor joist . installed 2 runs of 1/2 in. copper between joist then nailed 1/2 ply to the bottom of cleats and as he went he filled the space with 3/8 pea rock around the copper. It's kind of hard to explain this in detail but maybe you can get the idea ,ask him what caused him to do it this way and he said his wife said he was spending to much time in the beer tavern.
Lots of great info from Mongo, as usual. But he only partially retracted his "Yes" answer to the "Is outdoor reset needed as much in warmboard as in a gypcrete installation?" question. I would say firmly that No, it is not as necessary in a warmboard installation. Still helpful, maybe even quite helpful depending on the particulars for insulation, tightness, climate, etc. But not as necessary as in a high-mass system.
Feed-forward control always works better than feed-back control. A system that can look at what will be required in the FUTURE (by looking at the outdoor temperature) will preform better than one that looks at the PAST (responding to inside temperature only after it has deviated from the set point).
You can demonstrate this by driving your car forward by only looking in your rearview mirror. If you respond quickly (low-mass system) to what happened in the recent past, you won't be serving too much. But any additional lags in the system (high-mass, insulative floor coverings, small BTU source) and you'll be pulled over as a suspected drunk driver. The analogy also works for straight (or constant curvature) roads versus very twisty roads. Feed-back controls and high-mass systems are at their weakest when outside temperature or solar-input change quickly. You have a big truck moving in a set direction, with the driver looking backwards instead of forwards and there's a sharp curve in the road coming up.
David Thomas Overlooking Cook Inlet in Kenai, Alaska
The Wirsbo CD does a complete job of heat loss analysis. You even have to put in your door and window sizes. The program takes a little getting use to, but it really is pretty good.
Another good source of info and quotes is http://www.radiantcompany.com. They have a installation manual that is very helpful and will send it to you if you give them the info so they can make up a quote for you. They like the open system of one heater for both domestic hot water and heating, but I don't feel confident about this yet.
Another way to go is to get a set of plans to George T. Sanders, Wholesale Plumbing Supply Company. I use the Wheat Ridge office, but they have offices all over the state. They will work up a system and quote for you, including heat loss calculations.
Finally, I am not a plumber, a retired general contractor, but I have found most plumbers are not proficient on radiant heat jobs. I have done several jobs where I did all the pex tubing work and just left the connections to the heater or boiler to the plumber.
Email me if I can help: [email protected]
Check out Tekmarcontrols at http://www.tekmarcontrols.com. Tekmar makes some of the best reset controls in the business - easy to setup and great documentation. Also, check out http://www.heatingHelp.com some if not all of the best Hydronics technicians in the country hang out at the "wall" forum and answer questions. A simple heads up, beware of Radient Tech.
Tekmar puts out good products. Their stuff drives my own RFH system.
Thanks, I'll consider it.
How about a "real experience" response. I live in Castro Valley (used to live in Cool so I know your temperatures too) and have installed a radiant system in our remodeled home. Much of the ballyhoo I heard before I started in our case has turned out to be bogus. One of the best was that with California weather the walls would sweat. I am not sure what they meant. The only sweat is the installation (oh how I dreamed of building from scratch while the spiders danced around on my face in the crawl space).
You will have cooler temperature than we do to balance things out. Our only problem has been the transition seasons- before rain in December or so and during rain in February and March. I have to set the time on to only an hour or so early in the morning. Otherwise the house continues to warm up long after the pumps have stopped for the day. We just wear long sleeve shirts when we first get up while we dance around barefoot (throw away those slippers you will not need them).
I have mine rigged up to cool a little in the summer. Not a huge difference but cool on the feet is fun too. No noise, no allergies, cheaper gas and electric bills-love it! With a tankless water heater that is fed by the preheated returning hydronic water the burner hardly ever fires.
Drawbacks? Hydronic is not cheap. The more zones the more cost. We have lots of zones because our house is 45 years old and we can vary temperature (kind of the charm of an "old" home).
Basically I dread the day we move into a home that blasts a bunch of hot air around our faces for awhile making us think we are warm (as we turn up the thermostat a few more degrees)........
hmmm....some great info, we've been thinking about tankless for a long time as well. Seem to get many negative responses. Hasn't the technology improved greatly on those things?? Are you pretty happy with the tankless?? Our house will have 4 people living in it. And with pretty much different schedules. Would like to use solar, with a tankless to boost the temp if needed. As for the radiant heat, we are leaning more and more towards using it. We also detest the warm air blowing in our hair. Beck
Just a quick add-on, I have read you can specify carpets to have low r-value so they don't insulate your room from the floor.
On the same topic. Does anyone out there have an opinion when doing radiant flooring of using lightweight concrete vs a gypsum underlayment (gypcrete)? The project manager says that either are fine, the subcontractor (of gypcrete) says that lightweight has more insulating than radiating properties, so instead of releasing the heat, the lightweight will hold onto the heat where as the gypcrete will radiate better into the rooms. my feeling is with that type of mass, the heat has to go somewhere...so it can't just disappear, so either would be fine.
any experiences/advice?
thanks
I have gypcrete. I don't like its surface for installing whatever goes above it (I've glued bamboo and installed tile w/ thinset, and it worked, but I didn't like the process compared to doing the same over concrete). As a heating medium, it has neither the quick response of Warmboard, for example, nor the sustained warmth of a slab. I personally am being drawn toward the true hi-mass or lo-mass solutions, rather than those in the middle.