Rainscreen Wall Detail in Northeast
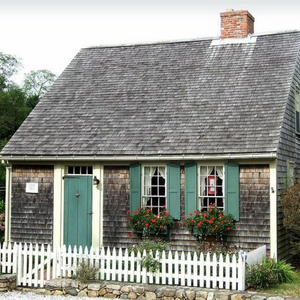
Hi All,
I’m new to posting but a long-time reader of the forum.
We are preparing to build a small Cape in North Central Connecticut, and would like advice on handling rainscreen and WRB / vapor details for our climate.
We are designing for 2×8 walls, mineral wool insulation, CDX plywood sheathing, 3/4″ thick CDX vertical rain screen furring strips, and solid wood clapboard siding.
We are pretty firm on the wall construction, but less certain about the WRB and vapor barrier / retarder products that are appropriate for our climate.
We like the idea of a fluid-applied barrier, but are unsure which would be most appropriate.
Would appreciate any thoughts and feedback from people who have designed or built rainscreens in the Northeast.
Many thanks to you all!
George Gordon
Replies
For the wall are you doing anything as a thermal break? Seems strange to do 2x8 with no thermal break.
Based on your current wall with a vented cladding, non-continuous exterior insulation, and permeable interior stud bay insulation, you'll want a class 2 vapor retarder on attached on the face of the studs behind your drywall, not necessarily right behind your WRB.
In general remember to air seal well since most of your vapor in transported through air and not diffused through your drywall or plywood sheathing.
This site has some other options based on climate zone and what type of wall/siding you have: https://www.iccsafe.org/wp-content/uploads/proclamations/TN06-Vapor-Retarders_pdf.pdf
Thank you very much for the reply and the document link.
In response to your question: we are not planning for a thermal break, the 2x8 walls are meant to achieve a decent R value while using mineral wool insulation. We're trying to build a house with natural-leaning materials that won't degrade into the environment, and hence avoiding a lot of foam insulations. We also supplement our heat with a wood stove (we have a near-endless supply of oak on our property) so achieving ultra high energy performance from the walls is not our principal objective.
Very cool, seems like a great project. In regards to the WRB, making sure it has enough vapor permeance is probably a primary goal, and if you want to be more environmentally friendly, an STPE fluid applied membrane would be ideal.
Here's one more article which details some issues and how to alleviate them with liquid applied membranes, specifically around joints and gaps - https://www.buildingscience.com/documents/building-science-insights-newsletters/bsi-103-joints-and-corners-and-penetrations
Finally, if you wanted to save money you can also do a self adhered vapor open adhesive WRB - again vapor open is important here since not all of the self adhered tapes are vapor open.
Thank you again for the reply — this is very, very helpful. The STPE fluid applied membrane definitely sounds like the way to go. Fluid-applied seems like such a no-brainer in that it embeds into to the texture of the substrate rather that laying atop (or fastened to) its surface.
You might want to look at double 2x4 walls with staggered studs, You can even space them a bit apart if you want even more R value.
Smaller structural lumber parts will be less impactful on the overall environment.
I know it is not your question......
While I am at it, will your wood stove have provisions for exterior combustion air? Keep in mind that it will need air to work.
Hi Mike,
Thank you for the reply. I have a slight preference for the simplicity and generally better quality of 2x8 framing, but 2x4 staggered stud walls is a good suggestion and something to consider.
Yes, we are required to provide make-up air details. It will probably be a heated unit with an electric heat element.
Circling back with our current concept. Still working out some details, but this is what the architect and I are considering at the moment.
Missing in the drawing is insulation and vapor barrier/retarder of the rim joists at the top and bottom of the wall. (and along the attic ceiling)
Correct, we will be insulating the floor joists and loft joists, it's just not shown on this rainscreen detail.
Have you looked at engineered studs for the walls?
I don't like engineered lumber for studs because such products (which rely on adhesives) do not hold up well to water and moisture. In time, all adhesives fail, especially when exposed to moisture. This is not a such a problem for roof, floor, and wall sheathing, which can be replaced without demolishing the house (and, in fact, are expected to be replaced periodically). It's a different story entirely when dealing with structural engineered lumber relying on adhesives.
If you expect your 2x8 wall studs to perform well when exposed to moisture, you may be surprised.
It is true that some parts will need to be replaced if inspection and maintenance is neglected, but the same can happen to solid lumber. mold and rot is mold and rot.
But is it your house, so your decisions.
It's not so much that I expect 2x8 Douglas Fir studs to perform "well" when exposed to moisture, but because their strength relies on long-grain wood fibers, (and not adhesive as in engineered lumber), I believe they will perform better for much longer than an engineered product.
Would you mind sharing why you're a proponent of engineered lumber for wall framing?
Thanks,
George
I would add two observations. First, any lumber relies on naturally occurring adhesives (lignins) to hold the cellulose fibers together. I doubt their reliability is much greater than the adhesives in engineered lumber. Second, why not do an exterior layer of rigid mineral wool insulation? It doesn't perform quite as well as foam, but meets your criteria and would improve the whole-wall performance.
Hi Andy,
The exterior layer of rigid mineral wool is a nice idea to boost energy performance! I'll run this by the architect. Definitely something to consider, especially as the energy code changes.
As for the debate surrounding natural vs synthetic adhesives: I once lived in a circa 1760 house in Connecticut, timber framed primarily from red oak, many of the floor joists were true 2x4 material, also oak. There was rot damage in some places, (it was at one point badly neglected, and one could see daylight through the roof when standing in the cellar!) and yet the house was still standing upright, and still is to this day, with few structural repairs over the years.
Would it still be standing if built from engineered lumber? Maybe, but we can only speculate because engineered lumber is relatively new to the scene. In most cases this speculation (and the tests which support the use of engineered lumber) are perfectly fine for the expected lifespan of North American residential construction.
In my case, however, we're trying to do something that is practical but also connotes a sense of permanence and integrity, and for me this means good quality natural materials for the "bones" of the house.
Notwithstanding this philosophy, I am interested to understand the perceived advantages to engineered lumber for stud walls.
Most of my work is in old houses, and I appreciate their longevity as well as your impulse to build in the same way. I would say the durability of old houses is due to a number of things, only the first of which is still relevant - A deep understanding by the builders of how to build appropriately for the climate, old-growth lumber (which is by its nature less prone to rot), and lots of air leakage that dried out the framing. Also, only the best examples survive, so our sample is skewed. The paradigm has shifted.
It's definitely true that only the best examples have survived. And most of us have a nostalgic affinity for the past that over-romanticizes the work, skills, and techniques.
Even so, it's not as easy as saying the past is gone and things are different now, therefore we should 'all' be building with vinyl and OSB.
It is true that I am fortunate enough to be able to consider alternatives to these materials, and not every American can do the same. It's neither sustainable nor economically realistic.
But that doesn't mean that every house needs to be built in the cheapest most economically realistic way (almost all surviving historical examples exceeded the minimum standards of the time, for example).
The important point being that it is not wrong to build a house with poor quality modern materials, but let's not fool ourselves into thinking that the bones of these houses are likely to be standing in ~250 years.
That's not necessarily a bad thing, but it's something that we should be honest with ourselves about.
There will always people who are interested in exceeding the standards of the time, and there will always be people who say it's wasteful and pointless.
Engineered lumber should be more uniform than current production 2x lumber. This could result in savings in finishing labor that makes up the extra cost of the framing material. I bring it up here inspired by your desire to use more expensive framing lumber for the wall studs.
You could increase the stud spacing with the 2x8s.
With your wall, however, I wonder about the wisdom of using CDX on the outside of your liquid boundary layer. It seems to me the place to prefer a solid wood would be outside the rain layer.
Mike, I'm not sure I follow your confusion...
The fluid applied barrier goes on the CDX (on the exterior facing side). Then there is an air gap (created by furring strips), then the solid wood clapboard siding gets attached to furring strips. I think this is pretty standard practice all around, I've never heard of anyone putting sheathing outside the water barrier. (To what would the barrier be applied?).
The 2x8 framing is required in order to achieve R-30 in walls using mineral wool insulation. In a modernist house engineered lumber would be a good idea to achieve perfectly flat walls, but we are not looking for this sort of perfection in our Cape's plaster finishes.
Not the sheathing, but the furring strips.
https://www.finehomebuilding.com/membership/pdf/5490/021213032.pdf
I had missed the note in your plan to apply the vapor barrier over the strips as well as the sheathing.
More than one person who has replied suggested a way other than use of the 2x8 as wall studs to get the R value you are looking for.
Yes, I believe one advantage to using a fluid applied barrier is that it can be applied over the furring strips as well.
And yes, there are many ways to get a high R-value these days. One has to weight the methods and decide which considerations are most important to them: upfront cost, environmental impact, permanence and integrity, regional availability of materials and regional skillsets, energy performance (which is not a simple analysis — the carbon footprint of demolishing foam & plastic houses every ~40 years and rebuilding them is truly massive, even if monthly energy bills are reduced — which also assumes that this energy comes from non-renewable sources). The number of variables are considerable.
My original post was concerned with water resistant barrier and vapor retarders, and states that we are pretty firm on wall construction. Nevertheless, I am always happy to receive and consider alternative methods. It just so happens that none have been persuasive enough to alter our building philosophy and values, but I thank you for your feedback.
Since you’re in the mood to learn alternatives to building practices, search Mooney Walls here on this forum. Just another way to skin a cat, my apologies to cats.
Yes, I think Mooney Walls are a very cool idea, especially for retrofit applications. It's great that they increase R value so much, but my understanding is that to capture these benefits in the eyes of the building inspector, we would have to have energy modeling performed in lieu of the much easier prescriptive method...
I know that a former member here (Mike Smith) builds permitted new and additions / remodels in Rhode Island . In your search his name probably popped up.
One beauty of the method is that your direct contact framing outside to inside finished surface is reduced.
You mentioned in another thread a chimney. Are you thinking a masonry heater, wood stove, fireplace?
Thanks for this tip. Yes, we expect to have a single flue masonry chimney to vent a wood burning stove.
George,
We have a soapstone heater. Way bigger than a stove but glad we included it in the build.
Check out the Masonry Heating Association
and Tulikivi.
One more thing to confuse the issue.
Thanks Calvin. Yes the soapstone heaters are very cool. We checked into it but unfortunately they're too big for our current plan, but maybe something to consider in the future if we expand...
We live in cold Ontario and have owned several homes with masonry chimneys located on an outside wall. They were always cold and very hard to light due to cold air coming down the chimney. If you are using a masonry chimney try to locate it on an inside wall inside the house insulation, or in my opinion it would be better to use an insulated stainless steel chimney also located inside the house insulation. A stainless steel chimney will burn hotter reducing dangerous creosote buildup
Hi Bobble,
Thanks for the note. Our masonry chimney will be a center chimney with a cavity to accept stainless steel stove pipe, probably double wall.
Just a small note, I installed a flexible stainless steel flue into my stone chimney with a square clay flue. It's in a one story addition to the house so it's only 13' high from the stove connector to the top, and, although the pipe came in 15' lengths, the insulation only came in 25' pieces, so I doubled most of it on the pipe. The pipe and insulation combination has eliminated virtually any creosote buildup in the chimney. In the 7 years since I installed it I've probably filled a maybe quart can with the creosote I've brushed out of the chimney from top to bottom, even the top where it meets the cold Vermont air has only had a thin coating of creosote at the end of the heating season.