Hello there. I am a contractor remodeling a home I bought. I am replacing joists that are set inside a block wall. I know treated is standard when dealing with concrete/block what can I do to add some sort of a sill barrier and can I do something so I dont have to buy all treated joists? You can see in the picture where the old joists were they rotted out. Appreciate any help.
Discussion Forum
Discussion Forum
Up Next
Video Shorts
Featured Story
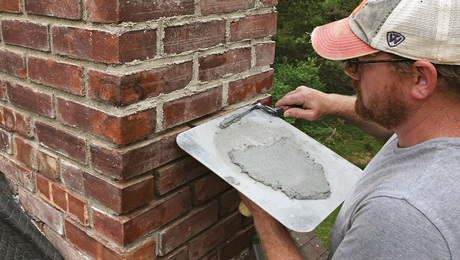
Old masonry may look tough, but the wrong mortar can destroy it—here's how to choose the right mix for lasting repairs.
Featured Video
How to Install Exterior Window TrimHighlights
"I have learned so much thanks to the searchable articles on the FHB website. I can confidently say that I expect to be a life-long subscriber." - M.K.
Fine Homebuilding Magazine
- Home Group
- Antique Trader
- Arts & Crafts Homes
- Bank Note Reporter
- Cabin Life
- Cuisine at Home
- Fine Gardening
- Fine Woodworking
- Green Building Advisor
- Garden Gate
- Horticulture
- Keep Craft Alive
- Log Home Living
- Military Trader/Vehicles
- Numismatic News
- Numismaster
- Old Cars Weekly
- Old House Journal
- Period Homes
- Popular Woodworking
- Script
- ShopNotes
- Sports Collectors Digest
- Threads
- Timber Home Living
- Traditional Building
- Woodsmith
- World Coin News
- Writer's Digest
Replies
That looks a bit rough. Just a spitball here. Perhaps you could grout the block and bolt a ledger on then hang regular joists to that. Looks like the block wall could use a little help anyway.
So, the joists sit inside the block? Just used treated ones. That's really the only solution.
The top course of that wall needs lots of help if you plan to do anything else. (the rest of the wall might need some help too)
use of a ledger board, or direct joist hangers on the cmu wall would require a sound wall to attach. If you can open the tops of all the cores, and fill with proper concrete/grout, you could proceed, but my guess is it will end up cheaper to use treated joists.
You also want to understand if the wall on top is meant to be supported by the now-missing joists, or on the partial block wall.
Are you asking this question because you dont want to spend the extra money on treated joists? You're savings on going with regular lumber over PT is miniscule. The risk by not using PT is infinite.
There is a reason that PT is used whenever lumber is in contact with concrete!
Doesnt the code now state you cant do this in brick/block walls because in a fire the joists in pockets like that pul the brick walls in with them if they burn through
The top is "firecut" at a 30 degree angle.
back in my grand pops day they would use roofing tar on the ends of the rough sawn board and they would last longer than the board itself. May not be code anymore though.
2sheps is right. His method has been approved by both engineers and code officials in my town. I’ve restored a lot of historic properties where floors are built the way yours is. The ledger board method is best if removing large sections of floor. Code does require that anywhere reinforcement and/or anchors are placed that the cells of block need to be filled with grout completely. Can’t attach bolts to hollow block. If working smaller sections pressure treated joists will probably be cheaper/easiest. Another method we have used is to switch the direction of joists utilizing beams placed in beam pockets in masonry. The code does allow for wood beams to be installed in masonry pocket, but there are requirements of an air space around the beam to allow the beam to breathe. The wood beam also requires separation on the bottom where it meets the masonry. A steel shim or treated wood plate meets this requirement. Keep in mind this is my town, yours may have different requirements. I have found inspectors to be very forgiving when working on old structures. It’s probably worth a call to you local inspector. He may allow the use of standard lumber in the pockets if you can separate the wood with use of flashing tape or something similar.
“[Deleted]”