Rescue for cast iron internal threads scored by hacksaw blade?
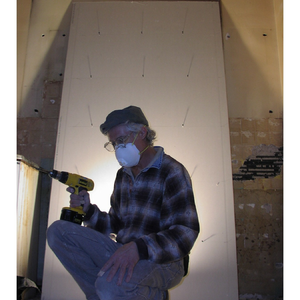
I’m replacing a freeze-cracked hot water radiator with a hundred-year-old cast iron unit. No mate, neither modern nor salvage, was to be found for the brass tailpiece coming out of the giant reducer at the radiator’s return end, so I had to remove the tailpiece. Its spuds were too corroded to give the spud wrench a bite; and despite applying penetrating oil and heating the reducer, it just warped from the torque of a pipe wrench; therefore it had to be cut out. That involved hacksawing slots inside the length of the tailpiece, then collapsing the piece by way of chisel blows against the half-inch of it I’d left protruding from the radiator. The brass piece broke into lengthwise segments, which were extracted as intended; but when I brushed the rust and filings away, I discovered that with one of my hacksaw cuts I’d scored the cast iron threads inside the return port of the radiator. I need to repair those threads, if possible, and fit a 1″ brass or black iron nipple into that port, or else replace the radiator’s reducer–a really daunting prospect–because of the damage. Starting over with a more amenable unit would seem almost smart–if I hadn’t already had the radiator blasted and powder-coated.
At first I’d thought to hit the threads with a good brushing and a little naval jelly, then applying some JB Weld along the narrow hacksaw cut, “tapping” new threads in the repair by threading in the nipple, then backing the nipple out and prepping it with Teflon tape before installing it.
Any better advice?
Replies
Lots of info on the web about JB Weld for fixing cast iron, but I'd run a bead of brazing rod along it and then re-tap as you suggest. Lots of info on brazing cast iron on the web also.
That sounds like a much better solution. Thanks, and I'll let you know how it works out.
After extensive reading, think I'll revert to the JB Weld scenario. Brazing seems like overkill for this shallow groove; and I'd worry about A) unevenly heating the part and causing further damage; and B) having no good way to retard cool-down, due to the size of the rad and the location of the repair. JB is good to over 500 degrees F, well above operating temp for a hot water radiator; and I think that since it's a thread repair, the threads on the male piece will help the repair hold its shape and seal over the long run. I'll use a V file to shape the groove before applying the stuff, let it set for a good long while, and cut the threads.
Thinking about it further, you're probably right. It looks like a "direct leak" out the cut, but in fact the male threads will force the water to circle around the threads. Rads also operate at low pressure, less than 20 psi, so JB Weld and pipe dope is the way to go. In fact, I'd hazard a guess that pipe dope and a very well-tightened NPT connection alone, would work.--but I'm not a steam-fitter.
# 1 Permatex
It's too late now, but next time you want to remove a brass spud, drive a tight fitting dowel into it before engaging the pipe wrench, and, heat the spud and let it cool before trying to unthread it.
When connecting to damaged threads, we've had good luck using ball / string wicking on the male thread - wrap the wicking clockwise on the threads followed by 3 or 4 wraps of quality Teflon tape on top. Then, add a brushed on coat of pipe joint compound.
I suggest testing the repair before putting the rad back in service; it's fairly simple to make a test set up & pressure test with 30 lbs of compressed air.......