I have read several articles concerning rim joist insulation. The issues are air sealing, cold surface condensation, spray foam, fiberglass, etc. A few years ago I had an energy audit done by an affiliate of my utility company. They recommendation for insulating the rim joist was to use spray foam. The affiliate shares the cost or pays for it all for certain insulation projects. I did not have the work done at that time. I contacted the affiliate recently to ask if the contract was still useable. Due to the time lapse I was told I would have to have my home re-audited. I just had the audit done and this time they recommended using fiberglass for insulating the rim joist in conjunction with air sealing. Has something changed….spray foam vs fiberglass?
Discussion Forum
Discussion Forum
Up Next
Video Shorts
Featured Story
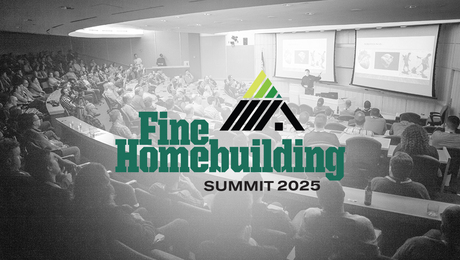
Join some of the most experienced and recognized building professionals for two days of presentations, panel discussions, networking, and more.
Featured Video
How to Install Exterior Window TrimRelated Stories
Highlights
"I have learned so much thanks to the searchable articles on the FHB website. I can confidently say that I expect to be a life-long subscriber." - M.K.
Fine Homebuilding Magazine
- Home Group
- Antique Trader
- Arts & Crafts Homes
- Bank Note Reporter
- Cabin Life
- Cuisine at Home
- Fine Gardening
- Fine Woodworking
- Green Building Advisor
- Garden Gate
- Horticulture
- Keep Craft Alive
- Log Home Living
- Military Trader/Vehicles
- Numismatic News
- Numismaster
- Old Cars Weekly
- Old House Journal
- Period Homes
- Popular Woodworking
- Script
- ShopNotes
- Sports Collectors Digest
- Threads
- Timber Home Living
- Traditional Building
- Woodsmith
- World Coin News
- Writer's Digest
Replies
they are running out of fed money???
if you need air sealing, you're not going to get it with FG. Even if it's faced.
My recommendtion? Just use foam. Spray foam if it's contracted out. It's faster and it'll fill around all the nooks and crannies.
If DIY, you can use rigid foam sheets, either friction fit, or under cut and then foamed in place with canned foam or it's equivalent. Or you can buy tanks from tigerfoam or foam-a-doam, etc, and spray your own.
Last fall I DIY'd my rim joists with two layers of 2" XPS, total of 4" and R-20. Friction fit. Went faster than I thought and they installed tight as a drum. Had a few bays that had electrical, plumbing, etc. Detailed around those. I'd cut slightly oversized holes for the penetrations and then fill them with canned foam.
I ripped the XPS to size with a table saw. Used a multi-tool to cut notches in the corners for the I-joist flanges. Had a utility knife for fine-tuning when fitting. Since they were friction-fit, I'd start them with my hands, then pound them in place with a hammer and a piece of 2x4 or 2x6 on the flat to distribute the force.
Good advice
I'm more a fan of undercutting and filling the gaps with expanding foam, but Mongo's approach is fine too.
One local energy efficiency company here only foam seals the top and bottom seams of the rim joists and replaces the fiberglass insulation. They are concerned more with CFM numbers because our energy rebates are based on those. If I only care about air sealing and not insulation, should this be okay? Would the insulation still absorb moisture and become black over time this way?
If fiberglass insulation turns black it's because it's filtering dust out of the air. And that occurs because air is flowing through the insulation (which isn't a good thing).
Foam is best by far - but only 3.25" thick
Foam is the best solution to insulate your rim joists. As Mongo noted, air sails through fiberglass. We also use the "cut and cobble" approach that Mongo described with pieces of XPS foam board. As AndyEngel noted, however, it is better to cut the pieces a bit loose so they are easy to install -- then seal the edges to block air leaks with the 'Windows and Doors' version of Great Stuff foam, which remains flexible after it cures to avoid cracks as things expand, contract and shift. This is actually more effective at stopping air leaks than trying to get a tight fit, which is rarely tight enough. 2" thick foam is required in many parts of the country, to stop condensation.
Thermal barrier exception - maximum 3.25" thickness: Another important point -- the IRC and IBC building codes allow you to install exposed foam board to insulate rim joists without a thermal barrier cover, e.g. 1/2" drywall. The maximum thickness of the foam is 3.25", however. (See IRC 314.5.11) Two layers of 2" thick foam board would be a code violation and fire risk. This could also lead to a 'failure' tag from your inspector and lots of time consuming rework. (The inspector on our last job was aware of this limit and quizzed me about what we had installed. Fortunately, I had read about the thickness limit.)
Read up on firestopping too: Modern homes burn 8 times faster than old ones, and exposed foam without firestopping is a key reason. Firestopping must be installed along the top of a basement wall, for example, next to the places where exposed foam may be used to insulate the rim joist -- and above the wall and stud bays that may also be insulated with flammable foam board. Do a Google search for "How to Firestop Your Basement" by Contractor Kurt -- a great summary of the key steps. We often stuff Roxul rock wool into the space at the top of basement stud walls and the adjpoining rim joist pockets (over the foam board), to seal this connection. Rock wool is much denser than fiberglass, molds kind of like clay and stays where you put it. Check with your inspector first, to see what he/she will approve; some require standard fireblocking, e.g. with pieces of plywood or OSB at the top of the stud wall.
I hope this is helpful.
Mark
Rim re-visited
BvilleBound. wrote:
Thermal barrier exception - maximum 3.25" thickness: Another important point -- the IRC and IBC building codes allow you to install exposed foam board to insulate rim joists without a thermal barrier cover, e.g. 1/2" drywall. The maximum thickness of the foam is 3.25", however. (See IRC 314.5.11) Two layers of 2" thick foam board would be a code violation and fire risk. This could also lead to a 'failure' tag from your inspector and lots of time consuming rework. (The inspector on our last job was aware of this limit and quizzed me about what we had installed. Fortunately, I had read about the thickness limit.)
I hope this is helpful.
Mark
This section of your post, Mark, makes it appears as if one needs to limit rim joist foam to 3.25". You don't. As you point out in your excerpt above (but not post subject line), that is only if you don't provide a termal barrier. When is this really the case? An unfinished basement?? Key word there is "unfiinished". If finished, then there is no expensive "rework" necessary.
However, if your contract only for an "unfinished" basment state, then I would argue that if you want to insulate above code and can cut 2 layers (or 3, 4, etc.) of 2" foam and fit them between (or along) joists to superinsulate your joist rim , then you can easily cut and fit an additional pc of 1/2" drywall to the same size in order to keep things code complient. It's not that big of a deal.