I know rain can’t be a good thing for construction before the roof is sheethed. Subflooring swells, nails rust, etc. Ideally, the roof deck goes on ASAP, but that’s not always soon enough for the rain gods. Also, I notice a lot of builders don’t seem in much of a hurry to get the place weatherized – framing interior walls (besides bearing walls) before the roof is closed, even in rainy season. Is this a real quality control issue? How do you deal with it.
Discussion Forum
Discussion Forum
Up Next
Video Shorts
Featured Story
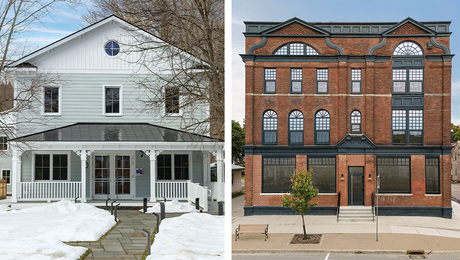
A high-performance single-family home builder shares tips from his early experience with two apartment buildings.
Featured Video
SawStop's Portable Tablesaw is Bigger and Better Than BeforeHighlights
"I have learned so much thanks to the searchable articles on the FHB website. I can confidently say that I expect to be a life-long subscriber." - M.K.
Fine Homebuilding Magazine
- Home Group
- Antique Trader
- Arts & Crafts Homes
- Bank Note Reporter
- Cabin Life
- Cuisine at Home
- Fine Gardening
- Fine Woodworking
- Green Building Advisor
- Garden Gate
- Horticulture
- Keep Craft Alive
- Log Home Living
- Military Trader/Vehicles
- Numismatic News
- Numismaster
- Old Cars Weekly
- Old House Journal
- Period Homes
- Popular Woodworking
- Script
- ShopNotes
- Sports Collectors Digest
- Threads
- Timber Home Living
- Traditional Building
- Woodsmith
- World Coin News
- Writer's Digest
Replies
IMHO. Yes it is. Specify dry in requirements in the contract. Contact the building inspectors, AHJ, and ask about their recommendations for your area. Some of them around here are adamant about limiting exposure. I don't know if there is a set time period but they have been known to check for obvious delamination, swelling, warp and saturated wood.
This time of year, mid June - July, we get rain nearly every day, at least once, and often 3 times a day. 8AM, 2PM and 7PM being a common pattern unless it rains all day or throws in another shower or two. :]
Most of the crews around here are pretty good about drying in or tarping the house.
Getting wet is just another part of building and the materials in common use are able to take it. As long as your builder is showing up every day and progress is being made there is nothing to worry about. Closing in a house can take two days or six months depending on the size and complexity of the house and the size and experience of the crew, but the house and materials will be ok in either case. You may have to wait a little to dry out the rain water that has soaked the subfloor and framing but if the house is big and complex it will take a while to get everything ready for insulation and drywall.
IMO, tarping is a waste of time and money. It is hard enough to do well when it is absolutely needed, as on some reroofing jobs.
"...but the house and materials will be ok in either case"
I find it hard to believe that 6 months, or even one month, is okay. When plywoods delam, osb swells, 2x's warp...
Anyway, I gotta go to work in a nice, cool basement now (on this hot and muggy day) but I'll check back on this thread later.
Ted W.
"I find it hard to believe that 6 months, or even one month, is okay. When plywoods delam, osb swells, 2x's warp..."
You are right. All this happens and some of it happens in the absence of water (warpage). Nonetheless, some houses are very large and complicated and take a long time to close in and other houses are built by owners who frame a house when they can. Six months is not that unusual for an owner-builder framing job.
Is it ideal? Of course not, but all the problems caused by moisture in the frame can be fixed and they are usually not that bad. The simple fact is that most people cannot afford to keep the weather out unless the house is small and simple and then why bother? It is possible to get a dome that will enclose the house for the duration of construction but the last time I looked into this it was going to cost us a minimum of $50,000. That was ten years ago and we haven't gotten any more requests since then.
I see your point, that what's ideal and what's practical is usually two different things, especially when it comes to dealing with nature. There must be some ways of dealing with water/lumber issues though. I figure, if a house frame is soaked before its sealed then later, after the drywall is up, doors and windows are in, etc... that wood is going to do some serious shrinking. The drywall is going to crack and some of the doors and windows will not function properly.
I notice this happens on a lot of additions and its usually credited to poor workmanship. Could it be that the workmanship was fine but rather, the structure was exposed to the elements too long and/or not let to dry out enough before the insulators and drywallers jumped in?
Excepting the sheathing, every house I've built, and most of the houses I've seen built here in the Northeast, are built from lumber that had leaves on it the week before. That's an exageration, but the question is, How much wetter is SGRN lumber going to get in the rain? Roofing asap is good practice, but I don't think most sawn lumber suffers much in the normal course of construction. The floor sheathing is another question entirely, as are engineered lumber products. Andy Engel, The Accidental Forum moderator
Andy
Once wood loses it's free water and gets down to about 19% (where KD lumber is) this it won't take up any free water if it gets wet. Now the mositure content of the wood will go up if wet, but it will quickly dry back out.
If you build two houses, both with KD lumber. One is a HfH quick build done over night.
The other has the frame up for 4 months with daily ran. Then one week of relatively dry weather and then it is closed it.
The lumber in the two houses will have about the same mositure conditions when closed in.
But this is only for KD lumber and not green or engineered.
Another issue I wonder about is mold.Iwork on a lot of town home ,condo projects and many times drywall is used for fire wall between units.You might have 40' of wall with double5/8 on each side 3or 4 stories high .I've seen this drywall turn black and funky and it just gets covered up and there it stays.What's up with that?
Happiness is all the bubbles reading the same
Mold has to have a certain percentage level of moisture to grow, I think that it is around 20%, but I am not sure, and food (wood).
Now I am not familar with that kind of construction, but it appears that they are puting up the drwall while there is plent of moisture in the structure. I don't know if they are using green wood or putting it up the day after a week of rain (0r both)
In some cases masonary fire walls are used. As each deck is built the masons build the fire wall up to ceiling height,then the walls are framed ,or as with the outfit I'm with now, landed(they build the walls in there own shop and truck them to the site and crane them on the deck.)The second floor deck goes on then more block,etc. etc...But most times we use core wall.Double 1inch drywall 2'X10'which goes up the same way the block goes up.This wall of drywall goes all the way to the bottom of the roof sheating.Now picture a16 unit building 3stories tall with just the second floor deck on fire walls built and it rains or snows for two days.Stops raining,third floor goes on, with fire walls,waiting for roof trusses.Rain again.You can see the exposure that this material is getting.It's the same with double 5/8 that I described before.Either way,it's wall board that is moisture proof(green board or gyp board) but not water proof.And I have seen it with black "stuff"all over it.I've seen OSB with green and black stuff all over it also.I never thought twice about it untill all this attention to mold has come to light in the past few years,but I think someone ought to address this issue.Like maybe the home buyer needs to get the ball rolling.I don't know but all I can see is this is going to cost big $$$$$ in the long run,for the home buyer.