*
With young workers, what message works?
Do you try to scare them?
Have weekly safety meetings? booorrrring
How about us old guys?
Discussion Forum
Discussion Forum
Up Next
Video Shorts
Featured Story
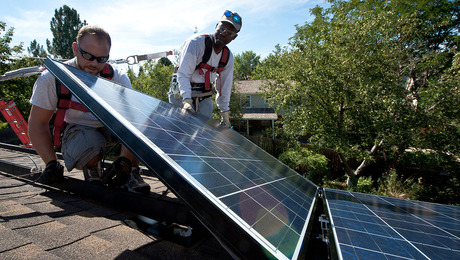
Does drilling new screws into the roof rafters compromise the strength of the roof?
Highlights
"I have learned so much thanks to the searchable articles on the FHB website. I can confidently say that I expect to be a life-long subscriber." - M.K.
Replies
*
In my experience, if management wants employees to have a particular attitude as they do their job, the most effective way to accomplish that is for management to have the same attitude.
If
b you
practice safety first
b at all times,
then you can get your crew to practice it also. Make it the first subject discussed with new hires, talk it up frequently, be fairly rigid about enforcing your safety policies, and religiously follow the policies yourself.
If you don't live and breathe safety, then all of the policies and meetings in the world won't get your crew to do so.
Rich Beckman
*The ONLY way to have the workers practice safety is for you to set the rules, follow them yourself and fire anyone who violates them. It only takes one firing to convince everyone that you mean business and that if they want a paycheck they best do what it takes to be around to collect it.Said another way, the only way to get to them is in the wallet, just like OSHA gets to businesses. You doing the right thing is just good leadership.
*Glad to see this topic. We had a situation at work that I'd like to see your take on. Guy shows up for work, then goes to boss before punching in and asks if he can have an hour to sleep before he starts his shift, or can he take the night off, his kid was sick the day before. Boss says to get real, if he came to work then there's his job. Guy punches in and goes to work. As the shift goes on he is steadily headed downhill, and at lunch again asks if he can punch out and go sleep in his car. Other guys are now concerned for their safety as well, he's getting sloppy and someone is going to get hurt. They back him up when he asks for a nap time. This is unusual for this employee. Boss says he needs job done today, and doesn't want guys thinking they can come in half asleep. Everyone goes back to work. About 2 hours later, the guy in question put both his hands on the die to stand up from the brake press and steps on the foot pedal as he stumbles up from his chair. 3 tonnes come down on his hands and trims all his fingers back to behind the second knuckle.Now who was in the wrong, the guy for coming in in the first place? The boss for not giving him to rest, the Crew for not pushing harder for safety? What ought to be done in the shop about this? Of course in the comp claims it will never come up that he asked to have a rest or go home, and it will all end up being his (the worker's) fault on paper. BTW, this was at a machine shop and took place on a night shift earlier this week.
*This is a perfect example of how Unions came to be. The owners could care less for people except as talking machines. The worker did the right thing. He checked in told the boss the situation and offered a possible solution. In his sick condition the worker didn't have the umph to stand up for himself. The rest of the crew was just trying to live with a bad situation and not lose their jobs too.May the boss be visited by the slimiest of lawyers and forced to work at slave labor for the rest of his days to pay for this. If you have any concience at all you will be very sure the actual facts come out in the investigation. You owe it to yourself, the crew and to your community.
*I consider myself an old time hard driver.I still yell when I need to.I push past most peoples excepted levels.But I'm going strong at 45.I now work 38 hrs a week on site instead of 45.My point is I now listen to my body, When it's tired I quit. If you want to go the long haul this is what you do.Do I like it when someone phones in sick? no no and no But I'm smart enough to realize that the good employee takes care of himself. He's healthy, fit, well rested and safe. This works in both of our favors.We also live in a different world than I grew up. Back then the women jumped out of bed for the kids. What did we miss not having dad do it occasionally.Take care of the kids. Take care of your family and yourself. Be happy first and be a good employee. This is the only way to go the long haul.Sorry for the speech. There's no question, this stupid boss should have sent the guy home.
*Terry, Rich said it best, "You practice safety at all times." The only thing I might add is that when you start to think about the fastest or safest way to preform a job, make sure safety wins. Safety pays for itself in the long run. You don't need to fire an employee for a first time minor safety infraction. Give them the rest of the day off to think about it, but do it so they understand why you are sending them home. If it is a serious offense from any employee, use your best judgment on how to handle it. Some need to be fired, some need a few days off, etc. By the way, the single most common OHSA infraction is not having a daily job safety briefing. It only takes two to three min. to say "ok guys, today we are going up on the roof....". Go over your short list of equipment needs and saftey procedures for roofs,etc.Document the safety tailgate and have everyone intial thier presents at the tailgate. Your tail is covered, and they know what you expect everyday. Dave
*I think Rich Beckman is right on target too. The best way to lead is by example. The employee/employer situation is always complex and changes daily. I don't want my guys hurt, nothing in construction is worth becoming permanently disabled or worse. We look for guys with common sense when we hire, it only takes one day on a job site for the new guy to be evaluated by my crew, if he makes those boys nervous, I don't want him either. I never push people past their limits or yell and scream. If an employee is not performing well enough at his pay level then down the road he goes. Working safely is a real priority with me and anyone who isn't with that program is gone quickly. As for the machine shop owner, if it was me I would have sent him home right away for a full day's rest and not taken a chance on a hour of napping in the parking lot to fully refresh him for the day's work, and certainly not let him work if he is that tired. It is never worth the gamble.
*Poor guy...terrible story. My heart goes out to him.The boss is at fault here. No doubt about it. He was told of this guys physical condition, but ignored it for the sake of production. Bastard. I say we all jump in my truck and go whip his sorry ass.Safty......Say it loud, say it proud.Ed.
*Bad boss!...NO donuts. Whatever happened to humane bosses? That was obviously a good employee, with job concerns, should have been listened to. It's a lot like showing up for work sick, and making others sick as well....then more time is lost, but do the big bad bosses care, Noooooooo!
*I don't like to use quotes much but Dave's comment> "Document the safety tailgate and have everyone intial thier presents at the tailgate. Your tail is covered, and they know what you expect everyday." sets this off. This is a CYA type of statement. "your tail is covered" is the legal type of approach and has little to do with real safety. I've attended many safety meetings and signed the form on such topics as not getting cranes near electric lines and using safe shoring practices and not standing on the top step of a step-ladder. I've never worked around cranes. Shoring is expensive [and not used]. Ladders are a different story. I get very uncomfortable standing on the top step of a step ladder but don't mind a bit if there is something to grab onto. The best way to indoctrinate safety is to tell stories, true stories. Not just recite rules. I'll give an example. I worked for United Electric and they had an employee who carried a bucket of tools up a ladder. This was good because he didn't waste time setting up a rope and pulley system. But one hand was occupied with holding the bucket and the other hand had to leap from rung to rung quickly before he fell off balance. As he reached the top, his free hand didn't move rapidly enough or missed or something. The weight of the bucket pulled him off balance and he plummeted to the ground. This was no longer good because now there a $10,000 fine, an OSHA investigation, loss of productivity on the part of the "good worker" and higher insurance premiums. Also the guy got hurt. -Peter
*I don't like to use quotes much but Dave's comment"Document the safety tailgate and have everyone intial thier presents at the tailgate. Your tail is covered, and they know what you expect everyday." sets this off. This is a CYA type of statement. "your tail is covered" is the legal type of approach and has little to do with real safety. I've attended many safety meetings and signed the form on such topics as not getting cranes near electric lines and using safe shoring practices and not standing on the top step of a step-ladder. I've never worked around cranes. Shoring is expensive [and not used]. Ladders are a different story. I get very uncomfortable standing on the top step of a step ladder but don't mind a bit if there is something to grab onto. The best way to indoctrinate safety is to tell stories, true stories. Not just recite rules. I'll give an example. I worked for United Electric and they had an employee who carried a bucket of tools up a ladder. This was good because he didn't waste time setting up a rope and pulley system. But one hand was occupied with holding the bucket and the other hand had to leap from rung to rung quickly before he fell off balance. As he reached the top, his free hand didn't move rapidly enough or missed or something. The weight of the bucket pulled him off balance and he plummeted to the ground. This was no longer good because now there a $10,000 fine, an OSHA investigation, loss of productivity on the part of the "good worker" and higher insurance premiums. Also the guy got hurt. -Peter
*Paddel Head, your co worker may have something to go on, the last time I heard, OSHA regs. says that punch press needs a "two hand activation" commonly done with a big button on each side of the machine. The press will only cycle when both buttons are pushed at the same time, making it impossible to get your hand stamped. Foot operated punch press is a huge no no! All the machines I have worked around were refitted years ago to comply. It might be worth checking out, your friend may just have some leverage. Bill
*Peter, Yes, there was was a CYA in my post, but my my main thought was the tailgate to reinforce the safety rules that apply to the current days job. If done properly they it can convey your sense of concern for your employees and reinforce your standing policy for safety. I was not refering to the gange meeting held in the shop that covers the 12 to 14 items that OSHA requires every year. I am refering to the heads up thinking that should be part of every crew leaders everyday thinking. If the employee that fell carrying a bucket of tools up a ladder had been told not to do it that way, that morning would he have been hurt? Or better still would have been for one of the crew members should have stopped him. My point is that the little reminder in the morning may have been enough to have raised a red flag for someone on the crew to stop an unsafe practice before someone else got hurt. You bet I will always cover my butt! Having a workmans comp. suite file agianst me once thought me the cold hard facts of life. That was before OSHA was also a factor in the equation. I hate to think what my fine could have been in addtion to the considerable legal fees I incurred. United is one of the contractors the company I work for uses on a very regular basis. We require all contractor employees to go through training on our safety rules, which in many cases go beyond OSHA regs. The company has also empowered any employee to stop any job when they see an unsafe act or situation develope. I personaly have loaned my switching jacket and low voltage gloves to United employees so they could perform thier jobs and be in compliance with our safety rules. I don't want anyone hurt or tossed off of the job because they aren't working safe. Safety is an attitude that can become a part of your everyday working experience if you reinforce it everyday. Just my humble oppinion.Dave
*Yes bill, you are right, for punch presses, this was a Brake press though, you need hands free operation on them in order to manipulate the bends on the parts. We havve 8 Brake presses in our shop, ranging from archaic to state of the art CNC wonders. He was on the oldest one we have, it has since been locked out and will be sold to the third world before Comp gets in the plant. (I've seen these kinds of accidents handled by our management team before). He was flat folding to .060, guys in the shop are still talking about how his hands looked when they came out of the press.All out Bed and punch presses are operated with the 2 pom-poms you describe, but even there, you have to be careful, its easy to move your hands faster than the die drops on some of the tonnages.
*One of the biggest safety lessons I got was from a teacher at the college where I took the practical segment for my apprenticeship (General Machinist) he was going along reading everything out of the book, guys were joking about this and that, and he dropped the book, and told us to go to the shop. We met him down there, and he stood a guy against the wall and grabbed a 3X3 chunk of steel. Ok he said, you stand still and close your eyes, I'll throw this at your head as hard as I can, maybe I'll hit, maybe I won't. Alot of the guys didn't think things were funny anymore. Then he took us around the shop and talked and showed us the dangers on each machine. It was alot more effective to go that way than to sit and read a book.Funny, but apart from guys sitting around talking about the latest accident in the shop there isn't a whole lot of safety talk in the place. Every year when we come back from Christmas a notice posted reminding us that right after a vacation is the most common time for accidents to happen, but apart from that, nothing. Once I saw an old timer running a reciprocating table surface grinder, and wiping the cuttings from the part as it slid back and forth under the wheel. I mentioned to him that it would really suck if the rag got caught in the grinding wheel and pulled his hand in with it. He yelled at me about how he'd been doing things that way for 20 yrs, an us young pups were just trying to piss on the old dogs tree. Next time i walked by his rag was in his back pocket and ha just scowled at me. I laughed to myself and kept on walking.
*Well Paddle Head the more you write the more I wonder why in the world you work there! The Owner/Boss doesn't care about the employees. The employees don't seem to care about each other. You have antiquated, unsafe equipment. How about the pay?Seems to me the smartest thing you can do is earn your beans somewhere else.As a going away present to your present employer be sure you document what happened in the latest accident so the poor guy can at least get some bucks to ease his life.
*Rich Beckman,b Your post is no joke.You said it better than anyone, and I think you covered it all. The reason I asked the question was to be sure I was doing enough for my guys. Their longevity is important to me. I really do appreciate your input, and sincerely hope you're someone's boss. Leading by this example.Thanks, and tight linesTerry
*Thanks. Not currently anyone's boss, but check back in a few months. I was someone's boss from the age of 20 til the age of 36 (ten years ago!). I learnedb a lotin that time!> Their longevity is important to me.Sounds like you've got a lucky crew.This post is also not a joke!Rich Beckman
*i This post is also not a joke! But what if I think it might be ?b Marion, Indiana. If you think my post might be a joke, it is
*> But what if I think it might be ?Luka,Then the joke is on you!Rich Beckman
*Then I'd like to ask for a little truth in advertising, please.Your tagline should read...b Marion, Indiana. If you think my post might be a joke, the joke is on you.
*Luka,No, no. You misunderstand (not that I didn't set you up!).When I say the joke is on you I mean it in the same way as you would understand "the drinks are on you".It's not a joke, but if you think it is a joke, then it is becauseb youthink so. Therefore, the joke is on you! It is a joke courtesy of Luka!Rich Beckman
*aaaaaaaaaaaaaaaaaaaaaaaghhhhhhhhhhhThe buzzing, the buzzing.It's in my head !
*Of course it's in your head. You are a jester in your own mind.Rich Beckman
*
With young workers, what message works?
Do you try to scare them?
Have weekly safety meetings? booorrrring
How about us old guys?