Screw gun or Nail gun for Fiber cement siding?
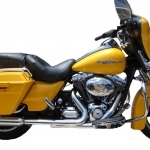
I’m getting ready to re-side the south facing wall of my house with 4 x 8 sheets of fiber cement panels. After tearing off the deteriorated, 38 year old T111 and any building papers under it, a 1″ layer of taped polyiso and new building papers will go on before hanging the FC sheets.
I haven’t worked with Fiber Cement before, but I understand it is quite brittle, hence my question of screw gun vs nail gun. I own a new Bostich N66 BC-1 coil nail gun that can shoot both caps & and nails simultaneously or nails only, that was purchased specifically for this job and any future roofing or other projects that require caps. My first concern is breaking a panel edge, corner or field due to under or overdrive from the nail gun. (Obviously, I plan to do some testing before putting up panels.) My second concern is nails working loose over time. I will use Stainless (’cause I live a mile from the gulf), Ring Shank’s for better holding power, but I know that screws have significantly more holding power.
So far, most of the forums I’ve read about reasonably priced collated screw guns (like the Senco) give me the impression that while great for drywall & flooring, they may not perform as well with vertical fiber cement panels.
Any thoughts would be a great help. I’m not looking for an excuse to buy another tool, but I do believe in getting the right tool for the job at hand. I also have to re- drywall over 40% of the interior in the next phase of the remodel so just trying to think ahead.
Ken
Replies
Nails without caps.I can't even imagine screwing Hardi up. A properly sized and placed nail shoots through the Hardi with no trouble and no breakage. It's pretty tough stuff. Also, screws with a tapered head will break Hardi. As far as holding power just wait until you need ot pull one of those SS ring shanks out.
Make sure the hardi is tight to the wall before firing a nail, or it can blow through. Also, hand nail the panel first, it's easier than farting around with the siding nailer while muscling a heavy panel around.
MarkH,
Your point is well taken since these panels weight about 80 pounds each. As a retired guy with a broken back, it takes me longer to get things done because of the additional steps I need to take without muscling too much.
The eaves on this ranch house are slightly less than 8 feet, so each sheet will be trimmed to height before mounting. My solo work plan includes horizontally mounting a 2 x 4 bottom rail (on edge) with a wide rabbet (1") for the FC sheet bottom to sit in to carry the panel weight. The rail is through bolted to the slab with masonry anchors and then removed when the job is finished.
Once the sheet has been offloaded from a lift cart modified to allow sliding off & rotating the panel up vertically and is sitting in the lower rail rabbet, a 4x4 "H" (about 5' tall) is leaned up against the sheet as a temporary keeper.
After adjustments, when the sheet is in the correct position to fasten, 2 identical clamping mechanisms, one attached to the soffit framing and one attached to the lower rail, are set to securely hold the sheet in place so I can answer the phone, eat lunch, take a leak, etc.
Suggestions or questions?
Ken
MarkH,
Your point is well taken, at 80 pounds per panel, these are not the things I can hold steady in position any more without some mechanical help.
My work plan includes bolting a horizontal 2 x 4 rail with masonry anchors into the slab to take the weight of the sheet. Also considering cutting a wide rabbet (~1") into the top edge of the 2 x 4 to prevent the panel bottom from kicking out while mounting the sheets.
I have modified a scissor lift cart to provide a 3' x 6' articulating table top. The cart brings the panel to the spot needed, then panel height is trimmed to fit. Finally, the panel is rotated up with the articulating top (while wheels are locked) and slid into position on the lower rail and against the 1 x 4 furring.
(I'm furring out over the studs to make sure the entire wall surface will be straight & plumb and to provide a drainage plane between the back of the FC sheet and the building paper that covers the taped polyiso layer over the studs.)
A 4" x 4" rectangle that is 4' x 5' is then leaned up against the vertical sheet as a temporary "keeper" while both an upper & lower clamping mechanism is engaged to secure the sheet for nailing.
The 2 clamping mechanisms use the new Kreg Automax 6" bench clamps mounted on their "Klamp Track" which allows the clamps to be moved to any position desired or even removed quickly if needed. The lower "Klamp Track" is mounted to the lower 2 x 4 rail and the upper "Klamp Track" is mounted to a 2 x 4 base that is nailed to the soffit framing with duplex nails.
Both clamps bear on a 4' section of 2 x 6 to keep the panel tight to the furring while nailing. Once the sheet is secured by the clamps, the 4 x 4 rectangle can be moved for use to the next position.
Thoughts, comments or questions?
Ken
sorry Ken
sorry for your needing to repost above-I flipped the switch that should allow all your posts to STINK'N easily be shown.
and no need to thank me,
thank the bogus settings on this "modern" forum software.
That was a little hard for me to follow. But it sounds like a plan. I don't know if there are clips made that you could screw to the wall and set the panels into them while fastening. They are made for lap siding, but would not be strong enough to hold a panel, as far as I know.
MarkH,
Hard to follow was surely my fault, didn't mean it to be. Probably TMI (too much information).
Clips would be a good thing but I've never seen or heard of them for these 4 x 8 FC panels, I'll do a little Binging (as opposed to googling) to see if something like that is on the super highway of information.
For a solo worker (because I can't afford to hire a non skilled helper, never mind one who is skilled) with a broken back, I have to resort to things like a lift cart and clamps to mechanize the muscling part of work.
My attitude is I enjoy working with both my hands and my head.
Since I'm retired and my time is my own, it does not matter how long it takes, only that I do not let obstacles deter me, and that I finish it at some point.
Only riding my Harley gives me more pleasure!
Ken
I can tell you'll be allright. Just be careful, and read the instructions. I would use stainless fasteners, 316 ss if you are ocean coastal.
Yes this website is an amateur unfinished prototype, but they know all about it, and wont listen to anyone.
Ken
To the screw shooter question-I know of no drywallers that use them. They are awkward-often slower because you can load a reg. drywall screwgun almost as fast. Maybe-tack up a ceiling and then go back over and screw it off..............maybe.
However, most of those same drywall shooters come as a standup screwgun (for underlay/floor sheeting and even durock) that can be broken down to the common collated screwer, by removing the long tube and re-inserting the business end on the driver.
Have any need to not kneel or bend over to drive thousand of sq. ft. of screws into a floor?
Best of luck on your project.
You kinda gotta be into self abuse to be here.
DanH,
It certainly feels like that many times, so you're probably right.
@ Taunton :
What's wrong with this picture?
Taunton charges very premium prices for all of their many publications (how many "Fines" are there?) and for Green Building, which I also subscribe to.
Yet they have probably the worst quality control over their on-line presence that I've ever seen.
There is and hopefully will always be a place for printed publications, but it is undeniable that at least for the present and foreseeable future, the internet will prevail in providing information to more people than all other sources combined. Proof? How many Newspapers & Magazines have been shuttered already?
Any company that fails to recognize this fact of life, and to drag it's reputation in the mud with a poor on-line presence, is flaunting commercial death.
It is a life cycle that forces ever increasing prices for print publications and at some point the cash cow dies when customers that are squeezed by crappy economics AND by brilliant CEO's who sent 15 million US jobs to China in return for crappy product quality so they could "enhance" their own paycheck.
TAUNTON: wake up & smell the coffee, your bacon is in the fire!
Ken Ackerman
There are lots of thing not right or user friendly .............
Tell me about it.
And yes, there is a poor bas tard that takes on the position of "sounding board" for suggestions..........
but,
fact remains, there is little movement in site improvement. Many reasons why, none of which amount to any real change.
The carrot hanging from the stick about how this software was moldable to fit the wishes and needs of an online community is all shriveled up.
Your suggestion of one sign in good for all public (and private if you opt for the fhb member status) Taunton forum and web pages seems like one of the first things you'd do, now wouldn't it.
Shoot, you were a member for a couple yrs, right? And I had to go back into your profile and flip a switch?
Beats the hell outta me. It's easy to get discouraged here, but I'm bull headed enough to say fuck it, it ain't anywhere near close to perfect-but I'm not quitting.
"you cannot petition the Lord with prayer............."
Calvin,
If Taunton got my profile correct, it shows 3 years & 52 weeks. Some of us would normally say 4 years, because each year has 52 weeks, if the school I went to got it right. You'd think that any switches that need flipping would have been done long ago, wouldn't you?
@ TAUNTON:
The problem appears to me to be that whoever Taunton hired for website work (you did hire someone, didn't you?), has not understood the basic concept of take the time to check their work before "publishing". Do you think the Vatican is a little humbled by striking a coin where the name of Jesus is spelled with an "L" instead of a "J"?
Many times, in today's world, there are not enough managers who have the stones to stand up & tell their chain of command that not enough time is allotted to review and cross check the details. This pressure to save time & money is foolhardy at best and downright stupid at worst, but unprofessional for certain, and certainly not "FINE" by any means.
Too many "managers" have become errand boys or girls fetching coffee for the all knowing Egomonsta with the big office. If the "manager" isn't given the authority to actually manage then it's time for a new Egomonsta. On the other hand, if the company culture is such that it doesn't or can't recognize a manager at ANY LEVEL who doesn't understand the need for quality work, then it's the blind leading the blind over the cliffs of LEMMINGS.
I have thought many times that your organization turned over website building to the local high school computer club, which would be fine as a gesture, but not fine for a company whose leading word for their publications is "FINE", used to elevate the perception of customers and to charge accordingly.
Continuing to ignore the fact that customer perceptions have already eroded due to poor quality control of your website is not fine at all.
Even if the website builders are your kids, you must fire them and hire someone who actually knows what they are doing.
YOUR FUTURE DEPENDS ON IT!
Ken Ackerman
Ken
you got me on why 52 weeks isn't a year.
But, let's give it a week and see if you turn over 53 weeks.
As far as the rest of what you wrote-let's hope one of those that might do something, sees it and takes it to heart.
Hope
andwithout change.I saw a shack in the North Carolina woods with bottlecap and roofing nails secured tar paper. Most of it was shot to hades, but it must have worked well. Also had the remains of newspaper wallpaper that was from the 1940's inside.
You are not going to want to use that gun. Use a standard roofing gun and roofing nails.(in ss if you like)
edit: wait, you plan to cover the nails with batten strips right?
3onthetree,
Which gun were you referring to? The Bostitch nc that is designed to shoot siding nails with or without caps so it can do double duty with building papers? It can also be used in roofing applications, it's a coil feed.That's what I own. I've read probably 50 reviews on it, all good. It has a depth adjustment, that gets excellent marks from reviewers.
Admittedly, I haven't used it on this job yet and you might find a future post from me with lots of D#*n punctuation marks in words.
If you're talking about a screw gun, I've decided against that.
Which one did you mean?
The nails are 316 stainless to be painted after installation.
No battens are planned to be used either for nail columns or sheet joints. The sheet joints will be sealed with elastomeric patcher that is made for use with all masonry surfaces including Fiber Cement. I've been using it for several years on brick walls and it works excellently with no cracking or separation like caulk.
The FC sheets have a factory finish texture that simulates a stucco look.
Plan B is: the elastomeric patcher/sealer is also textured so, if needed, a thin coat of it can be applied to the entire surface hiding everything, while keeping the stucco look.
Here's a before & after set of pix for the same section of the front wall so you can see what the patcher can do. No paint has been applied over the patcher yet. It will get a prime coat and then 2 coats of Benjamin Moore White Dove: Attached
My thoughts are, since I can hide the significant pitting & erosion of almost 40 years of salt erosion and poor quality brick, I'll be able to hide screw heads & sheet joints too. Yes, it will cost more and take much longer to do than battens, but to my eye it will look much better and bump up curb appeal more than battens.
One of the things that drove me to the elastomeric patcher / sealer, was that the full course brick veneer has the usual 1 inch air gap standing 1" off from the stick built frame. The patcher is also a sealer and far more impervious to water penetration than the brick is. After the patcher is primed and then painted with 2 coats of premium Benjamin Moore exterior Softgloss paint, it is, for all intents & purposes, good for another 40 years without fear of wind borne water penetration (assuming it gets repainted when needed). In other words, it's one more reason to get a premium price when sold. We get the occasional glancing hurricane here.
I don't think you mentioned the brand name of your FC panels, but I strongly suggest you go to the manufacturer's website and download all the information possible about installation, best practices, etc. The most important thing to remember is probably to paint all cut edges before installation--ideally, reprime the entire panel before putting it up (I remember someone saying that the primer Hardi applies at the factory is just a good base for the "real" primer to stick to. YMMV.) As far as the fastening method, once again, check the mfgr's "best practices" literature. I used both screws and nails for my Hardi plank--some screws have fletches on the underside to allow the head to plow its own seating space. Definitely use those and not the smooth type or, as someone else said, the panel will likely cr ack.
Hokuto,
For the record, the brand name is Maxi Panel. It's made here in Texas for the last 20 to 30 years, so the price is better than Hardi (less transportation cost). It has all the same ratings, etc as Hardi and is approved by the Texas Windstorm Insurance Agency (TWIA) just like Hardi.
I did download all the information on their site and am aware that all cut surfaces must be primed and re primed if cut again. Best practices are always used by me when they are available from the manufacturer and in that vein, there will be a rain screen behind the panel on the rear wall as well as polyiso sheets with taped joints for energy efficiency too. I think we are all becoming more aware what trapped water means to future failures.
As you can see from the above reply, I decided not to use screws even though they are manufacturer approved, I'm going with 316 stainless ringshanks driven by my Bostitch siding/roofing nailer with depth adjuster.
I have several window boxes (there's a glimpse of one in the reply above) on the front wall and 2 gable ends that need to be rebuilt and will start with those to get my cutting & hanging skills down before advancing to the rear wall where mostly whole sheets will be put up.
After reading so much about silica dust, I decided to bite the bullet and buy the heavy duty snapper shears AND a Trend powered air helmet. Belts & suspenders, but the lungs will be clean.
Happy trails!