Simplifying hillside construction. (Continued from elsewhere.)
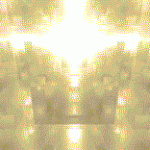
Simplifying hillside construction. Continuing a discustion from another topic. Starting a new thread.
In a discussion on another topic I wrote:
The only reason a basement makes sense is if you have a deep enough frost line to justify the excacvation. So slab on grade makes the most sense. Lately I’ve been dealing with slopes most of the time. I’ve found that it’s often less expensive to build foundations on the existing grade and used a raised subfloor than do the engineering, grading and compaction to do a slab. Soils work has gotten quite expensive. Often access for machinery is an issue. A couple of years ago I built a garage with a zero stem wall on the high side and an 8′ cripple wall on the low side. It was alot cheaper to engineer an build the subfloor for vehicle loads than to build an 8′ + retaining wall and bring in god only knows how much fill.
Oops replied:
I’ve thought of doing that, but it always seemed so out of the box for single family homes, I discarded the idea. Do you run into any code problems?
Here the developers cut and fill, stepping down the slope, to create flat lots. If it is sever enough, they have to build retaining wall at the property line. Basiclly making the lot fit the house instead of making the house fit the lot. Of course they wipe out all of any trees on the site.
It is quite a bit more economical to grade the lot, but it would make for a more architecturally divirse neighborhood to fit the house to the lot.
Too eliminate the cost of compaction etc, when necessary, they set the slab on piers down into understurbed bearing soil.
I reply:
Here in California building slab-on-grade foundations has been the norm for many years. Just grade a flat pad on the side of a hill; cut the top fill the bottom. I built like this for years. There are lots of advantages. I like slabs. They have a lot of thermal mass. I like tile floors and stained concrete finishes. But the cost of building like this has risen dramatically. Local jurisdictions have gotten very picky about grading and compaction, so soils engineering is often required. Compaction testing is almost always necessary. Environmental costs have also risen. California now requires construction projects to observe “best management practices” or BMPs. This involves creating a detailed plan for controlling the direct environmental impact of grading, construction and the developed building site. This involves silt fences, wattles, sand bagging, drainage plans, retaining walls, swales, etc. You can no longer just grade off a pad and build. It’s become very expensive. I’ve also come to believe that preserving natural features and vegitation of a site is desirable. Removing established trees should be avoided. Most owners agree, especially when this is the less expensive alternative. Three examples.
There are options for building on sloped or severely sloped sites. Grade beams, concrete piers and retaining walls are options but these are not conventional construction and/or involve extensive engineering and soils work. Stepped footings with stem and cripple walls and wood framed floor systems are conventional construction and often covered in building department hand-outs. (See the attached detail.) Excavation is labor intensive (and I mean Labor with a capital L) involving shovels and jack hammers, and many contractors seem to be afraid of hand digging, trying to avoid it at all costs. I don’t mind busting my butt and I’m almost 70. Clearances to daylight must be maintained and this often equates to some deep footings. I’ve never had to go more than 5′. With careful use floor framing lumber can be used for stem wall forms before it is used for the floor. I have a supply of 2x form lumber left over from decks I’ve demolished to supliment this. I use Simpson’s wedge ties. I’ve never had to buy form lumber.
The first hillside project I did was an extensive residential addition on the downhill side of an existing residence. The top floor was at street level, the bottom floor had a retaining wall on the high side. Access was through a 4′ side yard. The owner had been told that it couldn’t be done. I used stepped footings with a couple of post and piers. The only soils work was a bearing test. The structure was engineered, but conventional construction. All excavation was by hand.
I did an artist studio on a hillside. Site options were extremely limited. Two walls of the structure were right on the setback lines. Because this was a single story no engineering was involved. Excavation was by hand. I probably could have used a mini excavator for some of it but access was over a 4′ drop. Photo and drawings attached.
I did another studio, which for reasons I won’t go into was permited as a garage. We had only one possible location on an already developed site. I could have used an 8′ + retaining wall on the down hill side and lots of imported fill. It was cheaper to engineer and build a conventional subfloor for vehicle loads, than do the engineering and construction of the retaining wall. If the subfloor area is not intended for any additional use, engineering is easy because mutiple piers can be used. In this case they were 4′ oc in one direction 4′ 6″ the other. The only other requirement for the garage was that the floor be non combustible. This was accomplished with a light weight coating. No soils engineering was required. Excavation of the wall footings was by backhoe. The posts were dug by hand after the walls were poured. Photo and drawings attached. BMPs for this project involved a silt fence and nothing more.
Replies
Mike
This thread could make for an interesting discussion. Different parts of the country have vastly different terrain, etc and how it is dealt with in site planning and construction should be pretty varied as you pointed out.
Here in NW Ohio our topography is pretty darn flat. Terrain changes occur at rivers, streams and the drainage ditches that made The Great Black Swamp livable. Most construction is done on the flatlands with slight slope to the road bed. Basements are plentiful, but the slow drain provided by our location and elevation have compromised the old ones and in many cases, challenged the newer construction.
if by chance you can find an interesting lot with grade change, you are afforded the opportunity to easily drain to daylight........but there's the constant reminder often ignored, that most everything else has the possibility to want to drain by you as well.
In the 80's we found such a lot. Wary of the talent of masons used to working on the flat, I imported an old friend from the mts. outside of Asheville, NC. With his input and skill and a good excavator (the doctor of dirt), we had a decent start to a good build. Cut back into the hill, stepped the footings and foundation, swaled around, latest waterproofing "techniques" at the time.........so far so good.
thanks
slab foundations
Thanks for your reply Mark. I like the step down in that it allows the ext. finish extends down to grade. Nearly all our extterior finsh is brick veneer which requires a brick ledge which the forming of can get pretty complicated when the finish grade well below the finish floor. Most of the time, they just leave several feet of exposted foundation between the brick and the finish grade.
Big expensive, Archy stuff different story. Generally.
Texas is not much for environmental regulations. Dollars and cents pretty much rule. Getting better though.
As example of a Texas solution to building on a sloped site.
A typical slab foundation here is a monolithicly poured,structurally reinforced, concrete slab, with a +/-2'deep perimeter and interior beams max. 16' o.c. both ways. Sometimes called a waffle slab. Normally the beam steel is 2#5 top and bot. with #3 18" o.c. B/W in the slab/field.
The exterior perimeter forms are set and braced. These forms may vary from 1' on the high side to as much as 5'or 6' on the low side. The interior beams are formed by stacking sand bags on the interior existing grade thus creating beams +/-1'wide and from 2' deep to 5'+deep. These so called sand bags or usually old paper feed bags filed with what ever is handy.
The large areas created by the sand bag beams are then filled with what ever dirt/rock/etc that is handy. No compaction. The vapor barriier is installed,the steel is placed and tied in the beams and the concrete is poured. This makes for some good sized beams. :)
I saw this while doing a project near San Antonio back a good while ago, I don't know if they still do it or not,
For the last few years, Texas requires foundations to have engineers seal which for the most part is a farce. There is no state or county building codes per se. Only city and tributary.