Discussion Forum
Discussion Forum
Up Next
Video Shorts
Featured Story
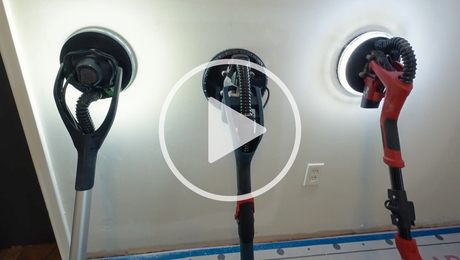
A pro painter evaluates a variety of drywall sanders and dust collection systems for quality of finish, user fatigue, and more.
Featured Video
Builder’s Advocate: An Interview With ViewrailHighlights
"I have learned so much thanks to the searchable articles on the FHB website. I can confidently say that I expect to be a life-long subscriber." - M.K.
Fine Homebuilding Magazine
- Home Group
- Antique Trader
- Arts & Crafts Homes
- Bank Note Reporter
- Cabin Life
- Cuisine at Home
- Fine Gardening
- Fine Woodworking
- Green Building Advisor
- Garden Gate
- Horticulture
- Keep Craft Alive
- Log Home Living
- Military Trader/Vehicles
- Numismatic News
- Numismaster
- Old Cars Weekly
- Old House Journal
- Period Homes
- Popular Woodworking
- Script
- ShopNotes
- Sports Collectors Digest
- Threads
- Timber Home Living
- Traditional Building
- Woodsmith
- World Coin News
- Writer's Digest
Replies
I've known about structurally insulated panels for a long time. My introduction to them was while watching a This Old House about 10-15 years ago when they tore down an old timberframe barn and built a new one in mimic-form and used SIPs for the exterior wall panels.
That project presented a variety of neat aspects about their use:
You can erect a shell in a dayy, roof included. SIPs can be used for walls, ceiling, and floor. They can be made & delivered in 4'x12' sizes, and I think even much longer lengths now. They can be up to a foot thing, come pre-channeled for wiring. They provide not only thermal performance, but acoustical as well. That TOH project commented that in the middle of Winter with no heaters inside the 'shell' the worker's body heat kept the place warm (in New England).
I would find myself some current information on sip.org and see if there is a wholesalers (supplier) in your area. I think the costs when labor is factored in is about the same, and this includes the crane rental, too.
Thanks for the info. I found a local mfg. at a show and got a price quote. It sounds like a good way to go.
May I ask what the quote was for/based-on? Where these based on standard 4'x8' panels for 4-5" thickness, pre-channeled? I would be interested in knowing what they cost. Being in the southeast they are extremely slow to implement new technologies that were introduced decades ago. So far, the only applications I've seen it in around me (Atlanta) have been public buildings and churches, maybe a home or two in the multi-million dollar market.
I asked for a quote on a 24x30 shop with 8ft walls, 5:12 roof, 7x12 OH door, 3/0 walkthrough and 2 windows on the side walls and one on the end wall.
Here's what they sent -"Using 4" walls and gables and 6" roof panels and sales tax and our drafting and drawings . The total fob Korwall is $8751.62"
What do you think on the pricing? It seems more expensive than stick built but it has some advantages.
Geography can have a play, here. Also, this does not include foundation, right? I had a friend that had a 2x by 30' building built for his boat and I think the foundation, stick-building (no insulation) cost was around $10-11K in an Atlanta suburb.
It only included the SIPs. Sounds a bit high when put that way. Metal is my lowest cost option but I'm not to keen on standard metal building design.
Only material cost, or does it include the delivery and erection of the shell? Again, I am curious to know where you are located geographically. Regional differences surely play somewhat into this aspect.
It includes material delivered only. I'm in the Fort Worth, TX area. If you add the slab in that's already over the price you had mentioned earlier.
Our timberframe currently being built will use SIPs, and we've done a lot of research on them over the past 2 years.
One thing to remember: when comparing pricing on SIPS to conventionally built walls, make sure to take into consideration not just the material cost difference--and when you do that, use the TOTAL material cost difference for what would be used other than the SIP--but the labor and time costs for the installation, especially in buildings that have a lot of windows and/or doors.
We had to remind our GC that while the SIPS cost more initially, they came with the electrical chases and boxes pre-installed on the outer walls and roof panels, and, more importantly, the window and door roughouts already in place. Once that was figured in, the price for the SIPs versus conventional framing was comparable.
Add in the fact that it forced us to decide all the window placements, sizes, etc., much earlier in the process, which in turn caused us to really think the whole design of the house through early on which has led to fewer changes now, which has reduced the overall cost of the house.
All this doesn't include the energy savings over the life of the house, of course.
Now, with a shop, I'm not sure how favorably the two construction methods would compare on initial price, but for us, on our house, it was an easy decision to make.
Leigh
Taunton has a book on SIPs:
Building with Structural Insulated Panels (SIPs)
Michael Morley
Strength and energy efficiency through structural panel construction
Every once in a while a new technology comes along that makes its predecessors obsolete. Today, Structural Insulated Panels (SIPs) are in the process of replacing the postwar norm of stick-framed, fiberglass-insulated houses and light commercial buildings. SIPs produce a structurally superior, better insulated, faster to erect, and more environmentally friendly house than ever before possible.
See "Shop Taunton" on this web site.
Al Mollitor, Sharon MA
Its too bad track builders won't build with them. This is not to say that there are no track builders building with SIP, just that those that do are in the extreme minority of percentage representation.