This is the spiral railing that I just glued up today. It took every clamp I had in the shop..abut 120 of them.
Discussion Forum
Discussion Forum
Up Next
Video Shorts
Featured Story
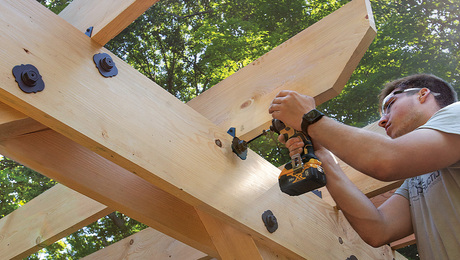
Built from locally sawn hemlock, this functional outdoor feature uses structural screws and metal connectors for fast, sturdy construction.
Featured Video
Builder’s Advocate: An Interview With ViewrailHighlights
"I have learned so much thanks to the searchable articles on the FHB website. I can confidently say that I expect to be a life-long subscriber." - M.K.
Fine Homebuilding Magazine
- Home Group
- Antique Trader
- Arts & Crafts Homes
- Bank Note Reporter
- Cabin Life
- Cuisine at Home
- Fine Gardening
- Fine Woodworking
- Green Building Advisor
- Garden Gate
- Horticulture
- Keep Craft Alive
- Log Home Living
- Military Trader/Vehicles
- Numismatic News
- Numismaster
- Old Cars Weekly
- Old House Journal
- Period Homes
- Popular Woodworking
- Script
- ShopNotes
- Sports Collectors Digest
- Threads
- Timber Home Living
- Traditional Building
- Woodsmith
- World Coin News
- Writer's Digest
Replies
Here are some of the newels that go with this stairway. I have mortised them to receive the handrail. I much prefer mortised in handrails.
Holy smokes, Stan,
How do you sequence that monster?
Do you glue all the treads and risers, and then glue the skirt?
What an engineering marvel.
We are not worthy.
STef
stef: I am confused. There are no risers or skirtboards on this spiral stairs. Maybe you were referring to the other curved stairway post I have?
Stan, we have a curbed spiral comming together. The center posts {risers} were being turned today.
Sad thing is some archetict only wanted a 4' dia spiral.......gonna be a small/busy stair!
Need to get some pics.........
GEO
geo...4 foot is awfully small. I built one several years ago and now will only consider a 4 ft. 6 in. as the smallest I will build. I will do my best to talk the client into at least a five ft. size. The one I have posted here is 5 ft. 6. and is very comfortable.
Edited 10/10/2003 6:47:31 AM ET by Stan Foster
Thanks for posting your pix, Stan. I can't see how you fastened your temporary clamp blocks to the treads.
Tim: The rail jigs are just clamped to each tread with two clamps. I have a little over correction calculated into this rail...about 1/2 inch tighter radius. It should be real close once its released. I still have the option of adjusting the curvature with either tension or compressin on the rail by means of the top and bottom newels.
Sir, I have FINALLY one-upped you...I have one hundred twenty ONE clamps, now...to work on the skill.....fine fine work as usual...cheers,Phil.If it is to be.... 'twil be done by me.
I just took the rail out of the forms today. Now I have to make a silks purse out of a sows ear the way it looked. I had a lot of power planing followed by handplaning,then beltsanding. Next I had to roundover the four corners. I then placed it back on the stairs to see how my springback came out. I put 1/2 inch of over correction into the forms..and this was just about right. It sprung back very close to the ideal path. Had it not..I could have either tensioned or put some compression on it between the top and bottom newels. Here are some pictures in sequence from rough to almost finished.
Thanks, Stan for the pix. It's really fun to watch.
How hard is it to run a router on a cork screw?
Cag: I just ran a bearing guided 3/8 inch radius roundover bit up and down the rail. The hardest part was keeping the router in a comfortable attitude to run it.
that's what I wondering about, seems like it would be an awkward job, and I don't like being awkward with a bit spinning at 20k RPM that will turn me to hamburger.
but then you like those "safe" gyrocopters ;)....
Yeah yeah, I know they are safe, but it would scare the bejeebers out of me.
Very good work Stan... Your reputation is one of the best in our area.
Larry: Thanks for the compliment...but excuse my ignorance. Are you from the central Illinois area...and if so..may I ask who you heard from about my work? Just curious. :)
I generally work in Champaign-Bloomington-Springfield-Peoria areas...
In the first set of pictures with the clamps on, it looks like alternating colors of wood strips. In the bottom set, the rail looks pretty uniform. Magic or optical illusion? Were all the strips the same or did you "cheat" and put some cheaper wood in the middle? Standard yellow glue?
Thanks
Casey: The handrail is made up of 8 oak laminates 3/16 of an inch. I used Titebond glue. What you are seeing in the first photos are the laminates not all perfectly aligned in height and the glue is running down onto the lower laminates giving the striped effect.
Stan,
I live in Urbana and have a shop in Mahomet . I have heard of your stair building from others.
Larry: I think we have talked before. I remember a cabinet shop in Mahomet. My sister used to live there. Hows your cabinet business?
Yep.... We have talked before. I have all the work I want. But that ain't sayn much. I am trying to retire... <wink>
Just got to thinkin about your 8 strips of oak. Seems like getting those into the clamps while coating them with glue could be sort of like trying to dance with an octopus. Do you pin any of the strips or do you just have lots of extra hands to keep everything in place when you lay the next strip into the clamps?
Casey: I use a 4 inch paint roller and roll on titebond glue on all the laminates. I then wrap the laminates with that wrapping plastic about every three feet. My son and I had no problems laying it in the forms. I clamped the bottom as he guided and twisted the laminates. I just then clamped all the way to the top. Laminates are interesting. They have to be twisted the same inclination angle of the railing for every 90 degrees that they go around. In other words...if the rail is inclined at 44 degrees....then the laminates have to be twisted 44 degrees for every quarter circle of floor that they turn over.
So, you're saying that you basically lay all 8 strips into the "forms" at the same time as a unit?
Casey: Yep...the laminates are 3/16 of an inch thick and are very pliable. It is a very busy 20 minutes.....lots of clamps.
Here are the balusters that will go on this spiral stairway and the second floor railing. There are 90 of these to install. They are 1.25 inches square...rounded tops and bottoms..and all the corners have been rounded over with a 3/16 inch radius bit.
Here is a view at the top showing the curved handrail transitioning to level..then making a quarter turn. This stub will fit into a mortised socket in the newel post that will hold the top of the rail. I like to do all the fitting in my shop as this greatly reduces my jobsite time. It basically will be a bolt together kit which I should be able to full install including all the second floor railing in two days.
Couple more views...the first is looking up showing the tread bottoms and tread supports that are tenoned throught the ten inch column.
Stan
Nice pictures.
How much of that will be asembled for transport, I know that you get a lot of help carrying those in but it seams like it would be difficult with the length of the thing.
Doug
Doug: I can knock that stairs down to just the column in two minutes. Those treads just pull out of the mortised column.
Awesome, Stan. That looks like really interesting work. I hope I have the chance to do that someday.
Have you ever read any books on what you are doing, or did you learn it the hard way? Any books in particular you would recomend?
Dave: I just became obsessed with curved stairways years ago while working as a trim carpenter. I read every thing I could get my hands on. The math part was the easiest as I have always had a basic grasp of trigonometry. It is just learning what it takes to make the wood do what is required. I just have built on experience. I may have different methods than others..and that may be because I basically taught myself and never worked under anyone else. I am sure I have some methods that are not the fastest..but they work for me and thats all that counts.
Stan, uh could you borrow me about 18 bar clamps................
It's always amazing just how many clamps get used for glue ups.
For those contemporary rails, your bar clamps are the best.
I've welded up some steel with a triangle profile that clamps to the tread for bender rail.
We make easings from solid stock and profile on an obscene looking router table. Will try and get some pics, mebee you do yours similiar?
I've gotten used to 10" C clamps for glue ups. Weld a 3/4" nut on the sliding bar end and race em down with an electric/air impact.
Makes "the dance" a little easier!
Don't you just love making wood "bend" to your will!
GEO