Any one have any do’s or don’ts regarding sprayed on wall insulation. Anything I should look for specificly when hiring a contractor.
Discussion Forum
Discussion Forum
Up Next
Video Shorts
Featured Story
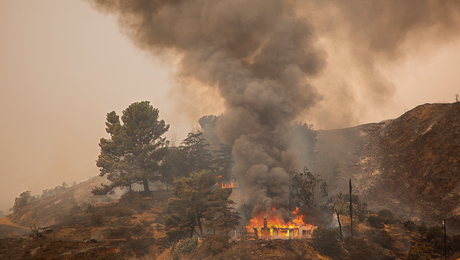
These defensive details give homes a better chances of surviving wildfires.
Featured Video
Video: Build a Fireplace, Brick by BrickHighlights
"I have learned so much thanks to the searchable articles on the FHB website. I can confidently say that I expect to be a life-long subscriber." - M.K.
Fine Homebuilding Magazine
- Home Group
- Antique Trader
- Arts & Crafts Homes
- Bank Note Reporter
- Cabin Life
- Cuisine at Home
- Fine Gardening
- Fine Woodworking
- Green Building Advisor
- Garden Gate
- Horticulture
- Keep Craft Alive
- Log Home Living
- Military Trader/Vehicles
- Numismatic News
- Numismaster
- Old Cars Weekly
- Old House Journal
- Period Homes
- Popular Woodworking
- Script
- ShopNotes
- Sports Collectors Digest
- Threads
- Timber Home Living
- Traditional Building
- Woodsmith
- World Coin News
- Writer's Digest
Replies
i'm just going to bump you and see if you can get some response. i just got a bid from a couple of icyene installers. both came in at 1.20 ft new const. didn't seem like there was much difference. other than one guy would go around and seal the windows. i'm not sure wheter i'm going to go with it or not,i think it's probably the best out there,but my sign on name says it all!and we are way over budget on this project. larry
The price of energy (heating or cooling) is not going to go down. That $1.20 now may look real cheap 5 years from now.
Joe H
I would go for polyurethane foam for sprayed on open cavity. Icynene looks good as an alternative to cells for between-the-walls in existing construction, but like cells it is water permeable and needs VB etc. I got quoted $4/sf for icynene, $2/sf for SPF. Besides cost, my major reservation about foam is the toxic smoke it may produce in a fire, so I may just apply it in certain parts of the house.
Let's not have any furniture, carpet, drapery, plastic parts in electronis equipment or a thousand other things that offgas when consumed by fire eiother. At least with the foam insulation, it is encapsualted behind the wall surface and removed from most of the normal causeds of home fires.
Welcome to the Taunton University of Knowledge FHB Campus at Breaktime. where ... Excellence is its own reward!
Foam in a wall isn't able to ignite or usually even smoke because the sheetrock cuts off oxygen.
I don't know about stick built but SIPs have a great record of insulating the fire from the foam, I suspect that the 2x's every 16 inches could conduct enough heat behind the wall to cause a problem..
What does $4/ft² mean? Floor area of house, wall area, board foot of insulation?
Jon Blakemore
that refers to the wall area, I pay a little over 3 dollars a sq. foot for a six inch thick panel so a 4 foot by 8 foot panel (32 sq.ft) will cost about $96 bucks
In a house that is 40 feet by 50 feet with 8 foot walls or a total of 1440 sq.ft.(of wall) the cost would be $4320.00 @$3.00 sq.ft.
Hi Jon,
What does $4/ft² mean? Floor area of house, wall area, board foot of insulation?
We just met with our local Icynene installer. He said he usually gives a rough estimate of $3 to $4 per sq ft. of floor area, or $1.15 - $1.25 per sq ft. for walls and $1.45 - $1.75 per sq ft. for cathedral ceilings. We are waiting for the final figure on ours.
kestrel
I'm not familiar enough with foam to know if they have a standard thickness. If not, then what is your speced thickness? For $1.25/ft² would you get 1.5" and R11 or 3.5" and R25?
Jon Blakemore
Icynene is 3.5/inch. Polyurethane is 7.14, or aged, 6.5.
Cloud,
What I meant to ask was what thickness will the foam be for the given price. I've always heard it sold by the board foot, but the prices that are floating around on this thread have no absolute quantity ascribed to them.
Jon Blakemore
The applicators I know quote by either the board foot or the pound. Under either scenario, you get the thickness you want. The ones who go by board foot are good enough that they can lay it on with sufficient precision to know 1" v 3 or 4".
jim, are you saying that spf/puf (are they the same thing?) has almost double the insulating value as icynene? and lower permeability? and might even be cheaper? any idea who does spf/puf around here? thanks.
m
>are you saying that spf/puf (are they the same thing?) has almost double the insulating value as icynene?
Yes. I don't know if there are accepted initials for the polyurethane foam. I've seen all kinds of things.
>and might even be cheaper?
Haven't priced the icynene, though I've never thought it to be costlier than spf/puf/whatever.
>any idea who does spf/puf around here?
Allied Insulation on Lyman Street.
mercy buckets!
m
i was told on icynen it would vary from 1.5-3.5 because they can't completly control the expansion rate. i'd sure feel more comfortable with a little better control.larry
Hi Jon,
I'm not familiar enough with foam to know if they have a standard thickness. If not, then what is your speced thickness? For $1.25/ft² would you get 1.5" and R11 or 3.5" and R25?
We speced 3.5" in the walls and 6" in the roof. We haven't received his final quote yet. He said he would try to improve on the price, since we will get the site ready to spray - that's cover all windows, floors, and everything else we don't want coated. We are also making the channels for the roof vent out of 1/2" styrofoam, and will have them taped to seal.
kestrel
My guy charges by the board foot, and it is 60 cents.
The urethane foam he and his competitors use isn't much different from that used by the insulated steel door industry to pack out the cavities of all those exterior steel doors you see. When I did the purchasing for Therma-Tru, we were paying about 80 cents a pound for 2 pound density foam components, and I'll bet the price is about that today.
At 2 pcf, each board foot slice taken from a 12-inch cube of solidified foam will weigh 2/12 of a pound, or 0.1666 pounds, and the cost of the foam would be 0.1666x0.80, or 13 cents.
Let's say these little spray foam insulation guys (by little I mean in comparison to Therma-Tru using a tanker truckload per day) get the foam for $2.40, instead of $0.80. Their cost is then 39 cents per board foot, and my guy sells that board foot, installed, for 60 cents.
He's not getting rich, but he's doing OK.
I estimate my cost by taking off all my wall cavity area, and figuring a 3-inch fill. Ceilings, roofs, and floors exposed to the outside are treated the same, but with different fill thicknesses. Load them all into a spreadsheet, use the 60 cents factor, and there you have it.
Costs have been rising badly lately, both be/c of the oil used, and be/c there are changes to the allowed blowing agents.
Well, this is a timely discussion. After many months of consrtuction (don't ask), we are at the insulation phase. I'm looking at either icynene or corbond. (It's been some time since I did my original research (and even got a bid - mostly for the bank numbers) so I'm going back through it now. Something has come up from the three installers that I have talked to so far. I've been told that there is no need for venting of any kind in either cathedral or truss roofs. In fact one guy said, "If you vent it, I won't do the job. And you'll have to clear this with the County" (Island, outside of Seattle). I understand that the foam makes a complete seal of the entire perimeter. It does make sense that the foam completly seals the inside from the out and therefore no moisture reaches the plywood. In fact one guy said that venting would only introduce outside mosture. I have radiant floor heat and two air-handlers so I don't see inside moisture being a problem. One installer said that this nonventing is not a problem in the many other states where use of foam is considered more the norm. I will talk to the County as soon as I get a few more ducks in a row. This was not an issue at the time that I submitted my plans. What's the story?
For wherever your ceiling finish (drywall, wood, plaster) is right on your rafters (i.e., cathedral ceiling), then your foamer is right. Spray it right to the underside of the roof decking, and don't think about venting.
For flat ceilings with "attic" space above, my foamer does faced roll insulation above the truss chords or ceiling joists, then sprays foam against that. Eaves are vented in these instances, so the cold attic can breathe.
Bob, You reminded me that one of the three foamers that I talked to did say that it was only vaulted ceilings that he did unvented. I have read in an icynene pamphlet of a homeowner saying his attic is now approximately the same temperature as the house since he sprayed against the roof. Why not define the outer perimeter as the sheathing wall/roof and include the attic space in with the house - thereby leaving it unvented also? Funny you should mention roll insulation, one foamer said he nerver touches the stuff.
My foamer does the flat ceilings the way I described because it is less expensive than going way up against the roof. Let's say you have a 28 foot truss or rafter span roof with an 8/12 pitch. Run the numbers and see if you want to pay the difference between spraying 4 inches of foam against R21 faced batts, or 7 inches of foam up and back down those 8 pitch rafters.
Volume and outside surface have something to do with heating costs, too. Why heat the attic if it is not living space?
That is a very good point - not to mention very good number logic. If the foamer I select is the one with an aversion to FG, I will have to A: convince him that this is the way I want it done (I've seen this movie many times) and B: put the batts down myself. Of course he might have some valid counterpoints and if so, I will run them by the forum. Thanks, Jeff.
I call him "my foamer," but "he" is an insulation contractor.
Foam is one of the things in his toolbelt. But fiberglass batt insulation certainly has its place and use, especially in this case.
In the midwest, many of the large insulation contractors use sprayed urethane, going into all the exterior wall cavities with a thin coating, which when foamed out, puts about a 3/8" veneer of foam against the sheathing and up a little onto each stud, plate, header, or sill. FG batts are then placed into cavities, with the flange of the paper facings stapled to the studs. Not much foam usage, but enough to enjoy the benefits from a total seal-up of the building envelope against air infiltration.
I wouldn't think well of an insulation contractor who won't consider hybrid methods. Insist that your guy run your numbers both ways, and let you make your choice, with him including labor and materials for placing the ceiling batt backup. Tell him he needs to be able to offer his customers real value, not just foam. Ask him if it were his house, how would he spend his money?
Bob:
I looked into using this combo/hybrid approach in my Northern Illinois home. I found a formula that gave the temp of the point of first condensation with varying R values and outside temps. In every case where less than 2 or 2 1/2" of closed cell foam were used, the dew point ended up inside your wall. On paper, it didn't work.
Look at http://www.buildingscience.com
For hot areas where the HVAC is often in the attic they recommends insulating the bottom of the roof system and thus putting the HVAC equipment in conditioned space.
Let me clarify something for you, I hope you don't have your shingles on yet, if you do they won't last as long as they should.. the problem is the back side will get wet and tend to stay wet with foam right up against the roof decking..
To solve that issue I used cedar breather under my cedar shakes and that provides the needed air gap to ensure long lived roof.
I don't know if you could use the same thing under asphault shingles or if you need to build a cold roof.
With sips the shingles are against the paper, plywood and foam. Is this also a problem w/ moisture? I am in AZ No Moisture
In your case NO! Plenty of time between rain fall for the shingles to dry out..
Where it is a problem is here where we get months where there isn't a drying out period..
It's doubly worse when those rainy periods immediately proceed winter. The freeze thaw cycle becomes viscous when it's rain, freeze, thaw, freeze, thaw, all winter long with no time to dry out..
This is the heart of the issue: standard vented construction versus foam with no venting. The information I have so far is that the use of foam prevents any air migration from the interior to the exterior (in fact one installer said they aren't even using R-value in many places in Canada where foam is more common because there is 100% resistance). The foam combined with my HVAC should keep the underside of the plywood dry. If the composition roof has been installed properly then there should be little to no moisture penetration from that direction. There is no condensation under felt because there is no moisture to condense. But I continue to look for holes in this current perception.
The Building Science site (suggested by Mr. Hartman) has some great diagrams with some comprehensive info - relating to standard construction. But there is little on the foam/venting question. There is one segment where they talk about sealing a roof deck completely from below. 100% foam is one of the methods suggested. It's almost like the use of foam is the complete antithesis to all that we know, i.e. from, roofs must be vented to move moist air (primarily from the living side) out to, stop airflow completely using foam to create an impenetrable barrier, with HVAC and a good roof on opposing sides to minimize condensation.
there are only two problems with your theory.
The first is that the 2x's are a vapor conductor!. That is, vapor in absence of any other path will migrate thru wood, thus the 2x's used in traditional stick building provide the moisture path. Wood does eventually become water logged, (that's why we can pull logs up from the bottom of lakes and rivers)
And second that does not address the issue of moisture that is trapped under shingles.
As I understand the problem without regular drying out of shingles rot can and does form in the area directly under shingles. Thus your plywood decking could rot. There are several solutions to that issue, the use of cedar breather under wod shakes. The use of skip sheathing over the plywood deacking and finally the use of a built up roof over the plywood decking.
Well, now I have to come out with more of my story. This is a steel house, red frame with lgs partition interior/exterior walls and roof members. I can see this conduction occurring and it has been a prime consideration throughout this project. This would indicate the need to spray foam the underside of the roof as opposed to the ceiling as suggested in an earlier post (5 1/2" foam will cover the metal chord. Now my 12" "C-studs" are another thing and I can see transmission there due to condensation. I guess the question is, how much? Again, interior moisture reduced by HVAC.
I cannot buy the moisture under the shingle angle - unless the roof has been installed improperly. Yes, there will be some - water is everywhere. But enough to do damage? How much water would get past a properly shingled and papered roof? There's always a stopping point in the goal of building the perfect house. I have done several tear-offs of some average (old) roofs and found only dry plywood underneath - some of the valleys were a different story.
But again this begs my original question. Not the one of dealing with exterior moisture but the one of no venting on the interior side of an impermeable (foam) barrier.
Your location affects the shingle issue much more than the issue of hot or cold roof..
In the right climate there never will be an issue of rot under shingles.. In damp or wet climates it can and is a major issue. I see homes with 30 year shingles torn off in less than 7 years and much of the roof decking replaced.. Outside appearance wouldn't suggest such a radicle measure was required, yet as soon as the shingles are off there the rotted plywood sags! In those extreme cases I suspect that water vapor from the inside was the prime problem but not always! Water can and does wick uphill and get under even properly installed shingles..
I was recently in the attic of a home where after a heavy week of rain the plywood was damp in most places. New home with very careful construction.. 30 # felt underlayment Ice and water in the valleys and eves, 35 year shingles, proper exposure. No leaks were visable but that didn't prevent dampness from affecting things..
My job got quoted with Icynene spray foam at $ 1.50 a sq ft. is that a good price? I have never dealt with the spray on foam before. What's the difference between Icynene and the other spray ons? I know they warned me about wiring getting pushed out of the wall if not fastened well. Any other things to look out for? Thanks
AFAIK $4/sf icynene is for wall area (at least that's what I assume I was told, $2/sf for SPF was definitely wall area, 2.5" depth). The icynene quote is for spraying into the closed cavity behind the walls, not an option with SPF because of foam expansion, and even so it's a bit of an art. If I could get icynene at $1.50/sf wall area it would be price competitive with cells.
SPF is vapor impermeable so it provides its own vapor barrier, that's the big win for me, where I can apply it. Switching the VB between inside and outside every year is just a pain :-)
>SPF is vapor impermeable so it provides its own vapor barrier
That's not entirely true. Follow this link-- http://www.itsa.info/VaporArticle7.shtml --and click the link at the bottom of that page to the SPFA research paper on vapor transmission through foam. It's written by the Spray Polyurethane Foam Alliance, so the credentials are there.
"Spray applied polyurethane foam, silicone and acrylic coatings all have measurable water vapor diffusion rates."
regarding diffusion, lets not get carried away.
SPF has a really, really low air flow rate.
Icynene and Cellulose have a rather low air flow rate.
Fiberglass has a high air flow rate.
Is a vapor barrier needed with cells or icynene? Not in my experience with the products (and not in the product literature that I have seen). Their tendency is to slow down the air flow enough to not need one, has been my understanding.
With FG, sure, you MUST have a barrier, but of the other choices you should not.
Norm
>regarding diffusion, lets not get carried away.
Don't know what getting carried away would mean in this context. The material is permeable. It has a perm rating in typical application usage. Don't know that anything else has been asserted.
One of the contractors I work with regularly is a roofing and exterior coating specialist who sprays polyurethane foam all the time as his business..both flat roofs and domes. He's done restorations where he's been able to squeeze water out of foam like it was a sponge. It is permeable in some circumstances. Vapor happens. Gotta account for it appropriately. Not saying that stick built with puf need another vapor barrier. Not saying anything other than it is not impermeable.
As long as we are not reading a white paper by Joe Lstiburek in 10 years about all the problems caused by SPF installation...
Re foam and flames (and the importance of a thermal barrier):
http://www.monolithic.com/plan_design/fire_hazard/index.html
http://www.monolithic.com/plan_design/fire_barrier/
While we're on the topic, there was something in the UK recently about the effects of flame-retardant chemicals on kids brain development. Wondered if any of these chemicals were used in cells.
http://www.guardian.co.uk/print/0,3858,4937157-103690,00.html
Is there a story on outgassing for icynene?
The operative phrase for insulation appears to be, Let's be careful out there.
For poly- icynene, I've been told there is outgassing for the first 30 days, after that there are no measureable amounts being given off.
Those daring young men in their flying machines!
I spoke to one icynene contractor a while back, spoke to another one this week. Contractor #1 says he can pour foam between the walls (from inside usually, get a plasterer to patch the holes later). Contractor #2 says it's too hard to do, he takes off a foot of siding and sheath on each side of the house (presumably on each floor) and sprays in.
Any comments on whichever approach you approve of? The second is actually more expensive because of the labor, but at least they can see where the foam is going. But ouch I can feel that blade going into the house.
If spraying icynene like this is plausible, how about for spf/puf?
I've looked through the archives, some of the concerns there are about electrical wiring (not just overheating but wiring being pulled out by the expanding foam).
That's a great link. I was under the impression that Spray foam was essentially non-permeable. So much for that!
I found it stunning that 1/2" plywood has a perm rating of 0.35 whereas polyurethange insulation (1") is 2-3. I wonder about asphault shingles...other asphault products are quite low, so I would assume shingles with a tar paper base are quite low.
I have been debating whether to put an air channel in my cathedral ceiling before I sprayed it. 4" of polyurethane foam will have a perm rating of about 0.5 or so, which isn't a lot different than plywood and asphault shingles, so it seems to me the airspace isn't required. I actually think local codes require the airspace, but I like to joust a little bit with the building department.
MERC.
The other thing I learned recently is that, while puf is a closed-cell foam, that's a bit of a misnomer. No foam has cells that form perfectly all the time. Even a closed-cell foam will have 5%-15% open cells. No kidding!
That said, I love the stuff, spec it in all my designs (that's the only real way to do the insulated thin shells). We're looking hard at the issue of vapor diffusion and the use of appropriate coatings, etc. But I stick to its application in thin-shell concrete and don't know what's most appropriate in frame or sips construction.
We used the polyurethane foam (corbond) from the basement up to the roof. You will have a draft free comfortable environment. The attic space on a hot or cold day is the same temperature as the rest of the house. If you go this route you will need some type of heat recovery ventilation system. The insulation was expensive, but money well spent.
It's too late but why didn't you build with SIPs? Would have been cheaper and faster...
Tom: we used SPF in our house. Before I bought, I had an SPF & Icynene guy bring me samples of the product & went to see their work. Took samples & put a propane torch to them. Neither would support combustion! Yes, they would burn, but only as long as I put heat into them. My conclusion - if that stuff burned, I'd lose my house anyway! Chose SPF for a bunch of reasons. Been very happy w/ it. Done on the hottest day in July. Blower-inner darned near died from dehydration in his bunny suit. Next day he came back to finish job. Same exterior conditions, but 20 degrees cooler inside than day before. Last winter our attic was as toasty as the second floor & and w/ no drafts. HVAC bills are really neat. Minimal use of heat or air.
Don