I am currently buildling and addition and we’re wanting to do a standing seam copper roof. Copper was not much more than tern metal and does not require the painting every 3-5yrs, and we did not want pre-painted metal. I know I need to use rosen paper under the copper, but have seen info showing 30lb felt going down first and then the rosen paper (from the Copper Developement Assoc.). Do I need the felt? Will it make for a better install? Looking for some feedback. Thanks!
Discussion Forum
Discussion Forum
Up Next
Video Shorts
Featured Story
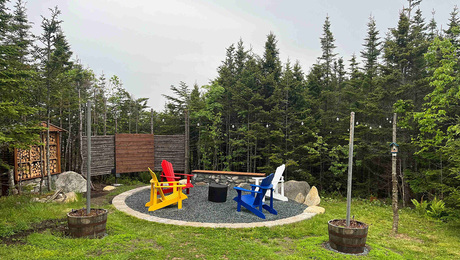
Listeners write in about fireplaces affecting family harmony and bionic suits, before asking questions about brick steps, ground-source heat pumps, and building a dome greenhouse in Maritime Canada.
Featured Video
SawStop's Portable Tablesaw is Bigger and Better Than BeforeHighlights
"I have learned so much thanks to the searchable articles on the FHB website. I can confidently say that I expect to be a life-long subscriber." - M.K.
Fine Homebuilding Magazine
- Home Group
- Antique Trader
- Arts & Crafts Homes
- Bank Note Reporter
- Cabin Life
- Cuisine at Home
- Fine Gardening
- Fine Woodworking
- Green Building Advisor
- Garden Gate
- Horticulture
- Keep Craft Alive
- Log Home Living
- Military Trader/Vehicles
- Numismatic News
- Numismaster
- Old Cars Weekly
- Old House Journal
- Period Homes
- Popular Woodworking
- Script
- ShopNotes
- Sports Collectors Digest
- Threads
- Timber Home Living
- Traditional Building
- Woodsmith
- World Coin News
- Writer's Digest
Replies
The felt is to dry-in the building until and through the roofing process in this case. It won't hurt to eliminate it if you don't mind the interior of the building getting wet. If you were using asphalt shingles, it also acts as a slip joint between the sheathing and the shingles which have different expansion rates. The rosin paper does this for the copper. It also keeps the copper from sticking to the felt if there is felt under the copper.
Feedback: Use the felt. At least 2 reasons - (1) standing seam copper is not really waterproof (like a flat seam roof) and (2) possibility of condensation on the underside of the copper.
T. Jeffery Clarke
jeff, this site S U C K S..
everytime i click on "Outdoor Stairs " i end up here... arrgghhhMike Smith
Rhode Island : Design / Build / Repair / Restore
and i do mean EVERY TIME..Mike Smith
Rhode Island : Design / Build / Repair / Restore
That's funny, Mike - every time I click on your name I end up HERE.T. Jeffery Clarke
Quidvis Recte Factum Quamvis Humile Praeclarum
go figger... squirrely , eh ?Mike Smith
Rhode Island : Design / Build / Repair / Restore
> standing seam copper is not really waterproof (like a flat seam roof)
Why would flat be more waterproof? What are the differences?
-- J.S.
john.. i've NEVER clicked on this thread... what a mess..Mike Smith
Rhode Island : Design / Build / Repair / Restore
The rosin paper is also to collect condensation if it occurs. Standing seam is normally not installed on pitches of less than 4/12, which is where you would switch to flat seam. Standing seam would be at least as watertight as any other roofing material (asphalt shingles, etc.) installed on a 4/12 or greater pitch.
When you switch to flat seam om a roof less than 4/12, do you solder the seams? Just curious.
Tom
All seams are soldered on a flat seam roof.
> All seams are soldered on a flat seam roof.
How do you do this without setting the underlying rosin paper and the attic on fire? Wouldn't it be easier to sweat standing seams without starting a fire?
-- J.S.
The point of flat seams (soldered) being more waterproof has come up in a typical situation where you have standing seam roofing terminating in an internal gutter. If the gutter backs up and the edge (overflow) elevation of the internal gutter is higher than the lowest standing seam termination (shouldn't, but CAN happen, especially with snow accumulation), the seam can leak into the roof construction.
Red rosin paper does not like moisture very much and generally speaking is used (unless I misspeak) to allow for effective movement between materials such as subfloor and finish floor, sheathing and metal roofing.T. Jeffery Clarke
Quidvis Recte Factum Quamvis Humile Praeclarum
You are correct about the rosin paper being a slip joint and about the situation with the outside edge of a gutter being higher than than the bottom termination of the standing seam. This is a design flaw akin to putting a screen door on a submarine. In regions where snow is an issue, or where there is potential for the gutters to become clogged, an apron on the back of the gutter should extend up under the standing seam. In this detail I solder a cleat at the bend at the top of the gutter and my standing seam pans connect to the cleat. Any moisture that might penetrate is then forced back into the gutter by the apron. I'll see if I can find a detail drawing I can post.
Oh, I also use ice and water membrane just as I would with asphalt shingles or any other type roof.
John,
I use a soldering copper, not a torch. There are two kinds- one is heated in an oven and then run along the seam and one has a propane hose hooked to it. The flame heats the end of the copper that's not touching the roof. I prefer the second type for several reasons I'll go into later if you're interested.
Grant --
I can see that the propane fired copper would give you a constant temperature, and therefore a more consistent solder joint. Also, it would use the gas more efficiently. Are there more reasons?
Still, if I were to try this myself, I'd definitely want my wife standing by in the attic with a garden hose at the ready. ;-)
-- J.S.
John,
I keep a fire extinguisher with me, but in nearly 20 years I have never discharged one. There is no open flame available to torch any combustibles. The heat spreads quickly in metals (especially in copper), so it's nearly impossible to heat the combustibles below the copper to combustion temperature.
About a year ago, a worker burnt down the oldest building at the University of KY soldering with an open flame. I undertstand your concern, but with the proper skill, knowledge, and equipment there are no safety concerns (other than to the solderer- I have set a hot copper on my leg, while I admired my work. What a dumbass).
One problem I have noted is if you want to know how to frame, trim, shingle, etc. there are excellent manuals and videos out there to teach you or wise you up to the fact that maybe you should hire a professional. I have numerous sheet metal books, but the only thing they cover in the soldering department is the equipment. Soldering is like riding a bicycle. Sudddenly, you can feel that you're doing it right. You have to be taught by someone. You can't read about it and do it right the first time. When I have an apprentice it takes about two years before I'm comfortable with them soldering out of my sight. Then, it's not the potential to start a fire, but to make sure they solder correctly.
BTW, the heat is very even and constant and I use maybe a tenth the amount of propane with the connected copper versus the oven system.
How much does your wife charge for attic standby? I spend a fair amount on refilling old fire extenguishers that have lost their charge.
Edited 4/12/2002 7:28:40 PM ET by grantlogan
Edited 4/12/2002 7:29:41 PM ET by grantlogan
Edited 4/12/2002 7:30:45 PM ET by grantlogan
Grant
I do a lot a this type of work and I agree with everything you've said. I use an acetylene heated copper for my work and I have several questions for you. Do you make your own killed spirits (flux) or what brand do you use? Do you stitch in your joints as a final pass to overlay them with solder, or is full, full enough? You say you attach a cleat to the top edge of your built in gutter. Is this pop riveted and soldered or merely a hemmed edge?
This discussion holds great interest to me.
Thanks for all feed back.
TerryTabula rase
Terry,
Good to talk to you. I've followed your posts since I started lurking here.
One of my competitors uses acetylene, and has tried to talk me into switching. I've resisted, since I can run my rig off of a 20 lb. propane tank or one of those small Coleman cylinders. I don't have to go to a welding supplier for refills.
I use Ruby Fluid for flux. I stitch (I call it "lace") anything other than horizontal joints. For horizontal joints (such as a flat seam roof) I use a big hatchet shaped copper with a goove cut into it. The groove rides on the bend of the flat lock and the flat surface on either side of the groove is in constant contact with the metal. I don't go back and lace in this situation. I just move slowly and let it sweat.
I solder the cleat (which is usually a 1 1/2" wide strip with a hem) to the back apron with 3/4" protruding into the gutter. The apron width varies by job, but it is held to the roof with nailed cleats locked into a top hem. The standing seam (or flat seam ) roof is then flat-locked to the soldered cleat. The gutter liner can expand laterally to the roof and vice-versa.
I once tried to bend the cleat into the gutter liner and realized I would have solder upside down where I couldn't see if I'd been successful or not and decided I was getting to fancy for my own good.
On the subject of flat seam: Do you pre-tin your pans?
AND: have you worked with Terne II?
Grant
Thanks for the info. I haven't pretinned my pans but I think I should. I just wonder how long you can get away with pre tinning until you have to solder. I worry about a corroded joint. Please give me your experience.
I have no experience with terne II, but I have a friend in Maine who might be able to help you.
Terry
Tabula rase
I don't pre-tin. I was gonna ask you the same question. I'm not interested in using terne II. I just wondered if anyone had had any luck with it. All I've heard are nightmare stories in this area.
GL
Do you have any pictures of your work? For my built in gutters I've always made the top apron as wide as I deem necessary for weather conditions. I also add a cleat to this apron at the top of the gutter, but I rivet my cleat to the apron and solder the rivets dry. I lock the bottom of my standing seam directly to this hemmed cleat. No soldering is necessary or prudent at this joint because the gutter apron continues above the weather line and solder won't allow for expansion. Just a different way to go.
Just a few more questions. Why do you lace your vertical joints and not your horizontals? What if you have a solder joint on a slope, do you lace this? What shape copper do you use for each application? You say that you won't trust an apprentice soldering until they have 2 years experience. Is this 2 years of soldering every day? Can you tell if a joint is full by the way it looks? How do you tell when you're soldering if a joint is full? Do you reflux a joint if you're making a second pass? Do you use sal amoniac to condition your coppers? Do you use a file to condition your coppers?
I greatly appreciate your input, Thanks
TerryTabula rase
Terry,
I just installed a new hard drive and don't have any pictures on the new one currently, but I'll post some soon. We're on the same page with the back apron of the gutter, I just don't like to make rivet holes in my gutter liner. I install my gutter liner in 3' lengths which makes more joints, but puts less expansion pressure on each joint versus 10' lengths. I also don't wind up with a bunch of 10' long wedge shaped strips of copper after each job.
I do lace all joints in gutter situations. On a flat seam roof it doesn't seam like the time spent to go back and lace is necessary. You can dwell on the horizintal long enough to get a good sweat without your solder running away.
We don't solder every day. Some take to it quicker than others. Others have come to me that had been taught by someone else and I didn't particulary agree with their soldering philosophy so I had to work with them to change it. Others have come in with fresh suggestions on how to do something. My methods change constantly due to input from others. I'm enjoying this discussion immensely. Anyway, 2 years would be an average (not a hard, fast rule) when I would leave a job site with someone soldering.
As I've said before, it's more of a feel thing to me. I've had helpers also express this. They think they're doing it right until they know they're doing it right. I've also had some that just never did get it. I've done joints myself that looked perfect, but when cut apart, were not sweated well. By the way that's normally how I get someone started: flatlock two scraps together in the shop on a rainy day, let 'em solder it and then cut thru their joint to see how they did.
I use a Primus-Sievert soldering rig with 18 oz. coppers. I shape them on a grinder for different applications. I haven't figured out how to link to other pages on this forum yet to send you to their page. I reflux for the second pass. I don't use sal amoniac anymore. With the torch I use, I seldom have to clean the copper. It does get pitted sometimes, in which case I reshape it on the grinder.
Grant
Our styles are incredibly similiar. I always reflux between passes. My copper rarely needs cleaning, but like your's it pits and needs reshaping on a grinder. I've seen your rig before and know it does excellent work. The one advantage mine has is, it's lighter in weight and less bulky. I really appreciate this when holding it in odd positions (as you know this is 99.999999% of the time). My arm still aches after a day of soldering, I'm getting ambisolderdextrous because of it.
I'm currently working on a roof with 19 dormers with window wells which intersect the roof line. It's a new house and I'm building flat locked solder seam pans. If you're interested I can get some pictures this week. Just to give you an idea of my work here's something I'm very proud of.Tabula rase
My thought on the rosin paper is you just need it under roof pans. A lot of people I know skip it all together, especially under standing seam.
Terry,
Is the exterior of the bay all copper? I can't tell from the photo. If it is, that's way beyond anything I've yet to do. I'd like to see more and I'll try to figure a way to post some of mine.
gl
Yes Grant it's all copper. Here's another:Tabula rase
Pretty darn impressive. I need to take some pictures using a lower resolution or whatever you call it. All my photos are over 1000k.
I look forward to seeing your work, and sharing more methods with you. Please email me when you have questions, pictures or just want to trade ideas. I hope my pictures don't put you off, I've been very fortunate in finding a discriminating client base and they constantly challenge me to new endeavors. It's fun recreating time honored architectural details. I, like you, am always learning new techniques. The more I learn the less I realize I know.
TerryTabula rase
No, I'm not put off at all, just impressed. I've been digging through pictures and it seems I forget to take photos after everything is complete. Everything I've got is in-progress shots. I'm going to try and post a copper shingle and box gutter shot. I think I'll spend some time this week and get some finished shots.
By the way, do you work alone or have a crew?
I got a boom lift and cut back from about 12 guys to me, one full time, and two part time. Our output hasn't dropped much, but headaches have.
gl
Crap - I still didn't do it right
I've been in business 20 years. Up till a year and a half ago I did all of the installation alone with part time, come and go laborers. At that time, I finally broke down and hired a full time employee. I've been incredibly demanding of my workers and when they quit I took a lot of the blame. Today I'm very pleased with my one worker and I realize it wasn't just my fault, I just hadn't found the right guy. I have now and it's a real pleasure to share my trade with him. As a matter of fact, I have enjoyed it so much that I hired 2 new guys 2 weeks ago. It's an interesting experiment. I just have to much work, and my original guy has shown me how much easier it is with the right help.
TerryTabula rase
Grant --
You need a program to work on your pictures and compress them. I use Adobe Photoshop, which lets me adjust color, contrast, and brightness, crop the picture, and apply a wide range of compression ratios. All the crawl space shots I posted in the gallery required a lot of tweaking.
-- J.S.
Yeah thanks, John. I just haven't had time to learn how to use some of my software yet.
gl
Thanks for the feedback. I spoke with another roofer that specializes in copper, but he uses only the soft type (100lbs rolls). He uses 30lb felt without rosin paper because the soft copper will not expand and contract like the "hard" copper. He likes soft copper because of this, and because it is quieter in windy conditions. He says alot of hard copper roofs will ripple due to the expansion.
The hard copper comes in 10' lengths, so that is the length of my pans. The lateral seam acts as expansion joints. Using this method, I can seam my hips and ridges rather than applying a ridge cap. If roll copper is used and pans are installed the entire height of the roof plane, then an applied ridge cap must be used to allow for expansion. If there is any expansion coeffiecient differance between hard and soft copper, I am not aware of it. Copper's copper.
The guy you talked to has a different method than mine. His is more of a commercial style. In my region, his method would not be allowed on an historical home. Doesn't mean either of us is wrong. It just depends on the appearance you desire. Personally, I don't like the look of a big clunky ridge cap. My system is more traditional. I dissagree with his reason for not using rosin paper, but not enough to get into an arguement about. I have never had a complaint of a copper roof being noisey in wind. On a commercial type roof with the applied ridge cap, wind might be able to get under the roof membrane or create a negative pressure underneath which could create sound. I have seen many of the pre-finished metal roofs loose a panel or two in high winds, but I suspect that was mostly due to the installers not being too far through the learning curve.
Copper has a high expansion coeffiecient - if you don't design expansion joints into your roof, you will have rippling, oil-canning, and or separation no matter which system is used.
Good Luck.
gl
Work hard, play hard, sleep hard, wear glasses if you need 'em.
Terry,
Here's one picture I found that shows some of my built-in gutter work. It's a little different situation than what we've been discussing-copper shingles rather than standing seam.
I'll post more as I find them. I'd like to see some of yours. Hope someone else finds this interesting since we've hijacked this thread.
gl
Edited 4/13/2002 7:42:39 AM ET by grantlogan
Sorry - my file is 1004kb-it won't attach. I'll try to find a smaller one.
Grant .
Do you think that rosin paper is needed under copper or will #15 or #30 felts work ok? I have some flashing sitting on the #30 felt . Would that be a problem ? I had neveer seen rosin under any flashing before . But read recently that copper should not sit on asphalt felts. Myth or fact? Don
I know this question was put to Grant but I'll give my .02$ worth and see if he agrees. I've never seen a problem as a result of setting typical copper flashings directly on felt paper. The application we're discussing is one where, with soldered joints, you want the copper to float between the soldered seams as opposed to sticking to the underlayment at mid span. My opinion is that there is no compatability issues between copper and felt paper.Tabula rase
> How much does your wife charge for attic standby?
Depends whose attic -- Eventually I want to go with copper on our house, but as the present roof doesn't leak, it's a low priority. I do scavange information on the subject when it comes my way. I also note any roof work safety info because this is 7 in 12 about 30 feet up.
Grant, you know how to do this, and there are no books on it. Bingo, there's a real opportunity. You could write the one and only book. How about checking with the Taunton guys to see if they'd be interested. Perhaps you could test the waters with an article in FHB.
-- J.S.
Edited 4/12/2002 8:31:06 PM ET by JOHN_SPRUNG
Yeah John,
I've considered writing that book for years. I've also been lurking around here for a while, and I realize that no matter how much I know about a subject, there's still another chapter I've got to read and a lot of my knowledge is regionally specific. I did call my wife in to look at your post (she used to encourage me) and didn't get much reaction. Maybe I'll do an outline. Thanks for the encouragement and good luck with your copper roof.
Hey, I do a project on the road every now and then. What part of the country are you in?
GL
Grant --
We're in Hollywood, CA, right across the street from where I work, Paramount Pictures. There's a whole bunch that's wrong with this house, and the roof isn't in that category, so I'll be very busy for the next couple years before roofing gets to the top of my list.
Fine copper work is the kind of knowledge that just gets lost if nobody ever bothers to write it down. Just like that damn Imhotep didn't write down how he got all those big blocks stacked up into pyramids.
-- J.S.
Howdy Grantlogan,
This topic and material is very interesting to me. I have a 140 year old home, Victorian, in something like the 'Cottage Style'. The roof currently on the house is asphalt, but the first roof put on was cedar shingle, with copper flashing throughout. {You can see this first roof from the attic.]
Point is that there are many bays with little roofs, and an octagonal screened in porch on this house. When I get to the point to re-roof, I would like to put a standing seam copper on these 'accent areas, while returning to cedar for the main roof area.
Can you recommend good, thorough reading on standing seam copper roof installation? To do this properly, does one have to have a sheet metal brake [sp?] and if so, can these be rented?
Thank you for your input!
Hey Pablo - go to the copper development association website http://www.copper.org/pub_list/homepage.htm and order
Copper In Architecture – Handbook View Image4115-1929
A comprehensive compilation of designs, details and specifications. Includes far more information than ever before assembled in one reference on the many, varied and cost-effective ways copper and its alloys are being applied in architecture and building construction.(100 pgs.) $85.
It's probably well worth the money for you. Lots of info that doesn't pertain to your project, but you'll probably find it interesting. Detail drawings for almost any application you can imagine.
Projects like this can be done with a rented portable brake, but not as well as with a stationary machine. The portable brake cannot make reverse bends as close together as the stationary machine, so the seams wind up being too tall or can only be rolled once. Also, those rental brakes are often out of tune.
Your best bet is to find someone like me (there's a lot of us out there) that will form your panels for you to install or maybe let you come in the shop and use our tools. I have had several interested homeowners trade free labor on another project for help on theirs. Also, hvac shops have basically the same machinery. Got any buddies in that line of work?
Also, If you decide to do it yourself, get a roll of terne metal to practice on before you cut into any copper. The bending is easy if the layout is good.
Check these sites out, too.
http://www.malcotools.com/
http://www.primus-sievert.com/
http://www.roperwhitney.com/index2.asp
http://www.nabocker.com/
Good Luck
gl
Work hard, play hard, sleep hard, wear glasses if you need 'em.
Grantlogan,
Thank you for your detailed input. The book is a reference I will hold onto, and likely invest in before I tackle the work myself.
You mention the idea of finding a copper roofer.......how are they listed in the [internet] yellow pages?
Thanks again!
/P
I have no advertising what so ever, nor does most of my competition. Your best bet is to go to the local roofing supplier and ask them or find a local project in progress and walk up and start asking questions.
Good Luck
gl
Work hard, play hard, sleep hard, wear glasses if you need 'em.