*
I had an opportunity to work on a friends 10 year old timber frame and came across a problem that I hope someone can help me with. His stress skin panels have deteriorated to dust,(the osb portion). There was no apparent water leak and I am assuming this was caused by condensation. The panels are covered with Typar and then red cedar clapboards. The side of the house that has the damage faces south west and is in the sun most of the day. Here on cape cod the winters do get a bit cold and I am wondering if this has anything to do with it. Can anyone lend a thought?
Discussion Forum
Discussion Forum
Up Next
Video Shorts
Featured Story
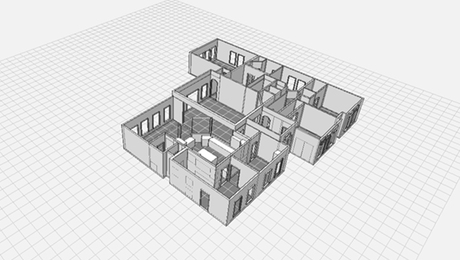
Hover's smartphone app offers an easier way to get precise 3D scans.
Featured Video
Builder’s Advocate: An Interview With ViewrailHighlights
"I have learned so much thanks to the searchable articles on the FHB website. I can confidently say that I expect to be a life-long subscriber." - M.K.
Fine Homebuilding Magazine
- Home Group
- Antique Trader
- Arts & Crafts Homes
- Bank Note Reporter
- Cabin Life
- Cuisine at Home
- Fine Gardening
- Fine Woodworking
- Green Building Advisor
- Garden Gate
- Horticulture
- Keep Craft Alive
- Log Home Living
- Military Trader/Vehicles
- Numismatic News
- Numismaster
- Old Cars Weekly
- Old House Journal
- Period Homes
- Popular Woodworking
- Script
- ShopNotes
- Sports Collectors Digest
- Threads
- Timber Home Living
- Traditional Building
- Woodsmith
- World Coin News
- Writer's Digest
Replies
*
I just read a report of damage in the hundreds of thousands of dollars in Alaska to SIPs houses in some internet thing. I don't have the site name (sorry) but I think it might have been a site linked to some discussion here in Breaktime. The article also might have been in a Journal of Light Construction update link. It had some good info that related to damage like what you mention. If I can find the site again, I'll forward it to you. Wish I could be of more help.
*Found it.www.jlc-update.com/archive/12_01/panel_roof.htmlIf that doesn't get you into the link just try the JLC site.
*"Here on cape cod the winters do get a bit cold "Hah! If you think Cape winters are cold, you haven't been around!There have been some concerns raised with cedar and Tyvek, maybe that's an issue? Plus, as mentioned, the incipient SIP concern.SW corner? I don't recall that's a high weather side on the Cape, but it has so many micro climates, who knows?Sometimes you can get exfiltration problems on the corner away from the weather side, but I think Nor'easters are really the exception there, not the norm.I'd check with a weatherization expert or an ASHI home inspector for specialized knowledge (although this week is the ASHI convention, so wait till we're home on Friday ... find a local ASHI inspector at http://www.ashi.com - semi-blatant advertising here! - I'm in NW Ohio myself, but used to live in Orleans)
*I wouldn't think that it'd be dust at this point if it were water intrusion. My understanding that heat actually did a better job at delaminating and breaking down the various OSB components (particularly to dust), than moisture. Any chance this could be the case? I don't pretend to be a building scientist, but I thought I'd throw this theory out.
*I read somewhere that fasteners sticking through OSB would gather frost and when warmed would drip into wall cavities. Possibly a daily occurrence during winter. Enough fasteners dripping a little bit over a period of time might take out a panel.Although these are SIP's, could this happen?
*I remember reading several articles detailing SIPs failure due to excessive heat build-up under roof shingles. The temperature given was 190F but there may be long-term , less temperature induced failure. Much like continual heat from say a wood stove will lower the combustion point of close wood to where even 250F will combust the wood.There are so many microclimates created on surfaces of a house, that failure could be caused by long-term effect, but within specs of the product's use. Remember that so much of our new building materials are tested via computer models and/or excellerated test chambers and do not reflect true environmental conditions over long term usage. walk gooddavid
*Mike .. what does "deteriorated to dust " mean... what is holding up the clapboards?...either the osb delaminated... in which case it would not be dust.. it would be chips and fibers..if it's dust it sounds like insect infestation..what's behind the non-existent osb?is the eps infested ?.. termites and carpenter ants love osb & eps... and they both love the piney woods of the cape...the cedar clapboards keep them warm and dry and snug while they go to the yummy layer... the osb... and the nesting layer.. the eps..... do tell...whatchagot ?
*Depends on who made the panels, There are a few who mix borax with the esp and the ant takes a bite and dies! Not too much chance for it to be ants. If it's a failure of the "glue" that holds your "chips" together I wonder if the owner has some recourse. Whichever I'd love more details since I'm in the middle of a timber frame right now! Hey don't you want me to get to sleep tonight?
*frenchy... the borate treated ones are marketed under "Performguard"...not much chance that these were treated like that.. i like ants...
*Believe it or not, the clapboards are nailed with 6d box nails into the 'once there' osb. The nails were just long enough to go into the foam core just a bit and that is what is holding things together for right now. I was called to the house when some of the boards blew off, which puzzled me as it was not that windy. Nor was the damage on the windward side of the house. I, (and I hate to use this word), assume as the wind came around the corner of the house created a slight vacuum and thus the boards came off. The osb has really turned to dust as if it had rotted and then dried out like in an old house. One of my options is to strip the clapboards off the house, remove as much of the dust as possible, and then screw 5/8 cdx plywood through the foam into the timbers, and then re-clapboard the area. But then I have the problem of the thickness of the new sheathing being thicker than the corner boards. And I still have not found the solutionto the original 'why' this happened.By the way; there was no evidence of ants, termites, or other insect iinfestation.So lets throw this out for an idea; is it possible that the curing of the foam produced a gas which interacted with the glue soaked obs?
*What can you tell about the brand. Some of those panels were made "under a shady tree by someone who knew how to make foam expand".... If that's the case who knows what. If there is a brand that's the first place I'd contact!
*No way I'd repair this place without getting an answer to what caused the problem that I believed. Just think about how quick ten years will roll around again, and now the sheathing YOU installed turns to dust. You have a reputation to protect, my brother. Don't let the opportunity for profits today entice you to risk your good name.
*Mike, Try the APA product support desk: 253-620-7400. Also, go to [email protected]
*If you don't know what caused it! You can't fix it! Crazy legs has a point, maybe run from this one.
*If you run from it then what's gonna happen? Are the owners supposed to say, "oh well, I guess we'll just give up....." Be a man, solve the problem. Explain to the owners that this is very difficult and that the time spent finding a solution must be paid for if they (the owners) don't want it to happen again. Reasonable people will understand and work with the contractor. Fools are another issue!
*The only problem with running from this one is that the owners are my best friends.....remember the old saying 'you can run but you can't hide?'
*It gets tough then. Do you have any pictures? Do you know who made the panels? Is it thick heavy "dust" or very fine, could it be carpenter ants? I get the feeling that you might have to replace the whole panel or build a wall over the foam left.
*In my opinion you shouldn't try to "patch" this, pull off the old "bad" Panels. Then replace them with new ones with a warrantee. The timbers should still be in good shape slap some new panels on put the new clapboards over the panels.
*There ya go.
*Mike,SW side you say? That's what gets the most exposrue to sun. Could it be that sun-driven moisture is the cause? Here's an exerpt from apost by Andy Engel over in the "Poly vapor barrier" thread in the Energy folder:"Brick veneer wall on the west side of a house. Housewrap on the sheathing, poly inside, air conditioned interior. Summer thunderstorm soaks the wall, sun comes back out. Moisture drive is warm to cold. Wet brick heats up, water in vapor form exits the back of the brick (or liquid water in the cavity between housewrap and brick vaporizes). Housewrap does its job and passes moisture vapor into wall assembly. The first condensing surface that the vapor is likely to encounter is the back of the poly. It condenses. Now, there's not enough heat in the wall for some time to change the phase of that water again, so it can't migrate back out as vapor either way. Mold grows. You could subsitute almost any type of siding for the brick. "In your case maybe the sun is driving moisture back into the osb. Also, maybe the tannins in the cedar have compromised the typar (has the siding been back-primed?), and it imight be acting like a rag, holding moisture as well. Eventually the osb dries out again if the weather stays dry long enough, then the cycle repeats over and over. You end up with the misnamed "dry rot" which is really wet-rot that has eventually dried out.I would get the homeowners to pay for a consultation with a building science professional. I see Joe Lstiburek is operating out of Westford, Mass. you can find his web site at http://www.buildingscience.com I have know connection with Joe and don't even know if he handles this kind of thing, but he would be a good one to at least ask where to go for help.Steve
*Getting the mfr of the panel involved will be key. Some panels (Insulspan, for one) are warranted for life against any kind of stuctural failure, and even if they're not under warranty I can't imagine a reputable panel co. not helping you out. Who did the timber frame? The same co. likely was involved in the panel sale/installation. Insulspan just came out with a recommendation for a vapor barrier over their panels. Tyvek is most often used- I prefer ASTM felt- esp. under cedar. I must say I've done about 60 timber/panel homes in tougher climes than the Island, and I've never seen anything like this.
*Well thanks Steve, you made my day. (and thanks to the rest of you that also helped out).I did some research on Steve's lead and found that (if I read correctly) that red cedar tannins will make the building paper absorb water. Thus the wetness will sit directly on the wood underneath. Now in the old days (LOL) before sips and osb, this wetness would not have been a big problem. But the osb is now getting wet, and with the sun beating on it, it's being driven even more into the osb. Thus we will have decay!Now I know what some of you are thinking, so you can read the reports for yourselves.www.buildingscience.com/resources/walls/siding_rainscreen_question.htmand also;www.buildingscience.com/resources/walls/problems_with_housewraps.htmSo feel free to tell me if I misunderstood this, but placing red cedar directly against building wrap, which is against an sip, is a no no?
*I believe the current consensus is either to have the rainscreen detail, or to have all six sides of the cedar completely sealed...not just the fronts. For my money, though, I'd guess I'd go with the rainscreen detail if possible...the firring would also help with siding attachment in providing a deeper nail penetration (instead of just into the OSB skins, into both the skins and firring).
*and for further protection, don't use tyvec /typar or whatever, just use building felt.those new fangled wraps will not only degrade when in contact with wood tannins, but also if they are exposed to surficants (soap), so when you power wash your walls (to paint) you'll be likely introducing soap to your house wrap and helping it to fail.builder's felt will not be bothered by these things.A rain screen detail is a good idea, in either case.
*Someone brought up in a previous thread that their inspector flat out refused to allow anything but Tyvek as a housewrap. No felt, no arguement.Is this going to be a problem when anyone else goes up against an inspector with that mind set?Does anyone have documentation as ammunition to take to these guys bosses?
*yeah.. the building code... which usually has provisions for appeal.. however... that is the same thing as fighting city hall, ain't it ?so , best bet.. bring it up in the plan review stage..before they dig in their heels
*Not terribly expensive to cover the tyvex and solve the problem..plus it makes the building inspector understand that you're not just trying to go the cheapest way (which they suspect of anything other than their approved stuff) Once you've established you willingness to do what's needed to get approval but intend to do it your way you now should have a more willing ear.
*
I had an opportunity to work on a friends 10 year old timber frame and came across a problem that I hope someone can help me with. His stress skin panels have deteriorated to dust,(the osb portion). There was no apparent water leak and I am assuming this was caused by condensation. The panels are covered with Typar and then red cedar clapboards. The side of the house that has the damage faces south west and is in the sun most of the day. Here on cape cod the winters do get a bit cold and I am wondering if this has anything to do with it. Can anyone lend a thought?