Dang, I thought I posted this, maybe this designer site is too much for me, so… here it goes again….I really am stumped on this one. Architectect has designed a 1/2″ glass topped table supported by 6 stumpy cedar things. The cut offs from the cedar things are to be glued to the table top somehow, so they’re like sticking through it. The plan is to drill holes in the flattened, cut to length stumps, epoxy 3/8″ threaded rods in the holes, drill holes in the floor, stick the bolts through and crank ’em down and sit the glass top of them, then stick on the cut offs. I’ve done something similar, but not quite the same, and there’s the rub. I’ve got a laser, I think I’ll wrap tape around the wood at the cut line, sketch a line around the stump and cut all the way around with a Fein cut off saw. Some of the stumps are too thick for the Fein to cut all the way through, so I’d have to finish with a Japaneses pull saw. Ok, simple in theory,but…according to my little pea brain… I’m going to have make the bottoms of each stump a little concave for a nice tight fit to the floor. This might change the height of the stumps as they’re cranked down, which could affect the levelitude of the top. Or worse, make it rock… Then, I’ve got one, and only shot at cutting off the tops nice and smoothly, so I’m looking for any opinions, advice, health warnings, or whatever you got. Thanks, and I will post pics…
Discussion Forum
Discussion Forum
Up Next
Video Shorts
Featured Story
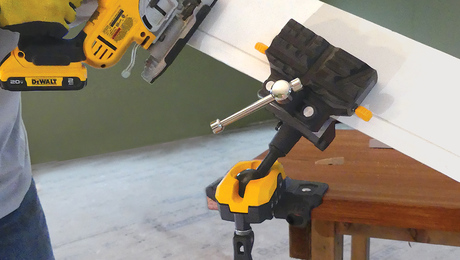
The IQ Vise has angled jaws, a simple locking mechanism, and solid holding power.
Featured Video
How to Install Cable Rail Around Wood-Post CornersHighlights
"I have learned so much thanks to the searchable articles on the FHB website. I can confidently say that I expect to be a life-long subscriber." - M.K.
Fine Homebuilding Magazine
- Home Group
- Antique Trader
- Arts & Crafts Homes
- Bank Note Reporter
- Cabin Life
- Cuisine at Home
- Fine Gardening
- Fine Woodworking
- Green Building Advisor
- Garden Gate
- Horticulture
- Keep Craft Alive
- Log Home Living
- Military Trader/Vehicles
- Numismatic News
- Numismaster
- Old Cars Weekly
- Old House Journal
- Period Homes
- Popular Woodworking
- Script
- ShopNotes
- Sports Collectors Digest
- Threads
- Timber Home Living
- Traditional Building
- Woodsmith
- World Coin News
- Writer's Digest
Replies
BB, you need the kind of laser Goldfinger had in one of those Bond movies. Just laser those stumps off at one pass. Keep an extinguisher handy though. Joe H
How 'bout this? First you bolt the stumps to the floor. You do whatever you have to do the stumps' bottoms to make them fit the floor. After they are nailed down, you cut the upper tips off. You can mark them all with the laser, but wrapping that level line around the irregular branches may be tough. Me, I'd rough-cut them, and then make flat table with holes in it for the branches to stick through, and use a router and jig to machine the tops of the branches to be in the same plane as that table. Now you have a nice flat plane to support the glass.
Jamie, I like that...it's one more damn template, but it might be the the right one,,, thanx
Following along with Jamie's idea, mount them first, then have a solid table that you can move to position next to each leg at the right height. Depending on the tools at hand--small chainsaw, handsaw--use the saw sideways with the tabletop as the sawing guide. If that's too rough a cut, you can mount a router to a scrap of ply secured to a table on wheels. Might be easier than a jig. Then roll the table (with router attached) to level the top.
Holly,
I posted my comments at the Crossing but can you tell me why your sketch looks obscene?
:)
Gabe
Crossing? The drawing's obscene because the architects trying to #### me...
BB.
First mount the stumps to the floor in the desired position.
Second set up your laser level to desired height.
Third remove batteries from laser and wire it direct to 440 volts. This should (crossed fingers) give the laser enough power to cut cleanly through the stumps. (the walls, your legs etc)
fourth place glass top
Voila!!
Let me know if this works......
Mr TDo not try this at home!
I am a trained professional!
there may be a slight sag in the glass if the supports are to far apart from the middle, maybe not to noticable, which means the outer branches need to be a hair longer, perhaps you could set the top down on some 2x2's standing up and see if it does sag.
no turn left unstoned
I would suggest that the top be secured with double threaded lags and epoxy. That would be more secure than just using epoxy, but would require drilling holes in the glass. Also this would reduce the chance of losing the tips from the top. Epoxy holds pretty good, but it will sometimes not hold to glass very well. The top will be tempered glass most likely, and cannot be drilled after tempering, but holes can be sandblasted through it with no problem.
So another thought is you can take the top, fit the tips and legs to it, then make the legs fit the floor, just like a regular table. You could probably cook up a quick jig that uses a router. I'd make the bottom of the legs flat then hollow them very slightly to fit the floor easier. The threaded rod is needed if you want the legs at an angle because you would not want any side thrust on the glass top.
This sound interesting. I hope you can make a little money on the job. Sounds like something you could lose your butt on if you arent careful.
Mark-
If I understand correctly, you suggest sandblasting holes after the tempering is done? Can't be done, it will disturb the tension in the glass and it will shatter, guaranteed. All hole drilling, edgework, etc. must be done prior to tempering.
By the way, sandblasting holes in glass gives pretty rough results, especially on 1/2".
Ken Hill
Thanks all, I'm still trying to distill a simple solution out of all these ideas. And, these are cypress knees not stumps. Musta been something in my water last night, like a little scotch...
Joe...man, I wish...
Cloud... I'm going to use that sometime, but I'm afraid cleaning up this lived in house/art gallery would take me longer than the job...
T...I wanna keep this client!...but I am gonna tell him what I could've done...
Red...at my age, youd'a thunk I woulda thought about sag...hmmmm
Mark...the bolts thru the floor are going to be epoxied into the bottom of the knees...the plan for the tops is some sticky stuff the architects wife uses? and it's an hourly gig, that's not typing you hear, it's my clock ticking...
Red... some may be 4" thick...not sure, but I think I could cut them with my 12" Makita slider, if I go that way...think I've got to start at the bottom 'cause I'm not sure if the oak flooring and subfloor are going to move when everything's cranked together...and it's a dining room table...going to be interesting passing the peas around those stiffies, as Gabe so aptly noted...
Next question, I've got some concerns about what's going to happen when these knees are inevitably kneed by raucous diners. Think one bolt will keep a knee stable?
Thanks, BB
Here's some similars but differents:
Ok, another wrinkle, is 45" x 78" with rounded ends gonna be big enough for eight burley diners? Even with the protrusions?
Here's the real knees:
Dining tables that size ordinarily can seat eight quite comfortably, with room in the middle for serving dishes. I dunno what impact you'll have from the cypress coming up through the middle of the table. Maybe you can just impale dinner on them.
What if you approached this backwards, e.g., cut the tops of the posts as best you can - how thick are they? Maybe a big honkin 15" chop saw would do it.
Anyway, mount the tops and bottoms to the glass with tops underneath the glass and then cut the bottoms to fit the floor instead of the other way around. That way you're assured of getting a tight fit to the glass and could deal with the legs one at a time if you had to to get them to sit flat on the floor.
Sound like an interesting project. A fellow builder of mine is doing a similar thing, except they're using stones instead of stumps and using it as a poolside table. Don't recall how they cut the stones, must have been a laser or some sort of water-saw.
Did you say what the function of this table is to be?
1 Fix the "legs" to the floor. 2 Cut the legs to within 1/4" of final height. 3 Make a dummy table of the right height with holes to clear the "legs" Place the dummy table over the "legs and run a router with a large base throught the holes and clean up the ends of the legs and they should all be nice and flat and on the same plane. I would stain the leg tops black or very dark and then epoxy the glass to them. 4 Clean up the top part of the legs and glue them on. I think this will work...............Pics if it does
Add cabinet door bumps to the base of the stumps before you bolt them down, should take care of any rocking.
Edited 6/23/2002 9:49:16 PM ET by NIGELUSA
Nigel, I think I'm becoming a sledder...here's the temporary situation, everything's put off 'til Monday...and, even if theses pics don't work, it's still put off a while...I'd still like some other takes...
Billy what format are these pictures?
ellifino?
Please repost in .jpg 'cause then we can all have a look!
Thanks billy
You don't know how I operate, do you? ;-)
Maybe these will work
BS: half inch glass is one tough hunk of stuff! I'll betcha it's not tempered. Probably just plate. You cannot cut through tempered glass by ANY means w/o shattering it. I have a glass worker friend who got a 1/2" table top from a dept store as a piece of reject scrap - it was not tempered. Epoxy is not good enough to hold w/o some other help. It will eventually separate from the glass. Know that from experience - been there, done that, wear that tee shirt. If you run bolts through glass, you want a sleeve to protect the glass from rubbing against the glass edge in the hole - will eventually stress the glass and possibly make it crack. The glass shop that prepares the top can bore the holes in the glass before it is tempered, if it is tempered. It will be easier to match everything else to the glass than the other way around. Granted, when you place the bolts in the floor it may well stress the glass - but take care of that w/ rubber/polymer bushings through the glass. If you have the bolts protrude through the glass far enough, you can thread the nubs onto the bolts to hold them down. Or, use silicone - it will stick to glass, and will also seal the joint between glass & cypress nubs. Those spots will be notorious dirt and filth collectors. Also, squeezing that glass too tightly w/ nuts & bolts will set up stresses in glass that may, over a period of yrs, cause cracking.
Good luck - sounds like the kind of glass jobs I used to get - looney and dang near impossible!
Don
I probably wasn't clear on this, but the top isn't going to be epoxied to anything, it will just be sitting on the cypress knees. After doing the mock up, I am sure that the weight of the top is enough to keep it in place. The bolts thru the floor will be epoxied into the bottom of the knees, if they ever all dry out, Adrian made a good call there 'cause one is reading over 19%...Emminent decay, Emminent deacy!!! another at 15%... The cut offs from the knees are to be stuck on the glass top for a continuity, flow thru ting, nothing structural...
Now I'm leaning towards getting a new and sharp and slightly bendable Japanese saw (my old one has some missing teeth), making a very flat plywood table with appropriate holes to fit over the already bolted in place knees, and with the ply as a guide, whacking them once and for all...any particular saw recommendations? These knees are already sandblasted (leaving me a nice unsandable texture, thank you very much), and stained ####rusty color), so, I'm worried about tearout...tape won't stick this wood...and I can only get 109V so I can't really crank the laser up...unless, perchance, someone has a spare sack of electric eels...put 'em in an email ettacment...
Maybe have only three of the legs actually supporting the table top and the others a little short.Save a little time on fitting and some of these legs are going to move off the table over time anyways. Noticable? Enough support? Dunno.
And that glue I used to stick my rear view mirror onto the windshield might hold you legs on the glass.