-
I would like to pour a cement floor suspended above a crawl space. The pour will be app. 8x9x4inches deep. Radiant heat tubes are being considered. What kind of design should be used in the structural layout of re-bar, mesh , supporting joists&etc. Can the underlying supports be removed after the cement has properly cured.
Discussion Forum
Discussion Forum
Up Next
Video Shorts
Featured Story
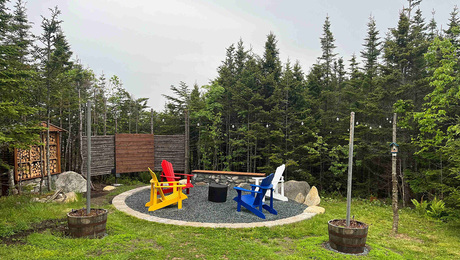
Listeners write in about fireplaces affecting family harmony and bionic suits, before asking questions about brick steps, ground-source heat pumps, and building a dome greenhouse in Maritime Canada.
Featured Video
Video: Build a Fireplace, Brick by BrickHighlights
"I have learned so much thanks to the searchable articles on the FHB website. I can confidently say that I expect to be a life-long subscriber." - M.K.
Fine Homebuilding Magazine
- Home Group
- Antique Trader
- Arts & Crafts Homes
- Bank Note Reporter
- Cabin Life
- Cuisine at Home
- Fine Gardening
- Fine Woodworking
- Green Building Advisor
- Garden Gate
- Horticulture
- Keep Craft Alive
- Log Home Living
- Military Trader/Vehicles
- Numismatic News
- Numismaster
- Old Cars Weekly
- Old House Journal
- Period Homes
- Popular Woodworking
- Script
- ShopNotes
- Sports Collectors Digest
- Threads
- Timber Home Living
- Traditional Building
- Woodsmith
- World Coin News
- Writer's Digest
Replies
You don't say what the support conditions are. Is it supported around the perimeter? Are you attempting to pour over an existing subfloor?
As an alternative if the subfloor is in place it might be easier to lay down an inch of rigid foam lay down radiant heat and pour 2" of gyp-crete on top of that.
True suspended slabs should be engineered by knowledgeable design people. There is a lot of engineering for that .
I would agree to get engineering. We pour lots of suspended conc. in the islands and all are perimeter supported with conc. beams, or on conc. walls. Typically we use #4 rebar on 8in centers (the upper steel could be 10 inch centers, we call this rebar "temperature steel")
Also around the perimeter is top steel, #4 bars 12 in. oc. This steel should end up approx. 1 inch below the surface. If the span goes beyond 16 feet we use #5 steel for the support steel and go to 6 inch centers.
Yes you can remove the forms after two weeks of curing.
Some of the ICF systems have forms for suspended floors. And if you are withing the range of their products they have it all engineered for you.
And with radiant heat you need the insulation.
.
A-holes. Hey every group has to have one. And I have been elected to be the one. I should make that my tagline.
Yoro -Not exactly sure what you mean by "suspended". To me suspended means to hang, but I doubt that you are asking about floors tht are hung from above. I will assume that you are talking about a concrete floor that is supported from walls and spans a space below the floor. Two commercial systems for concrete floors that can span up to 30' or more are:
LiteDeck - http://www.litedeck.com/
InsulDeck - http://www.insul-deck.orgThese systems use polystyrene forms that stay in place as insulation once the concrete floor as cured. I had a floor designed to span 20' and I believe the total thickness of the polystyrene, the concrete floor, and the concrete support beams that were cast in the Litedeck forms were about 11". Shorter spans would require forms with less overall thickness.If you don't need or want the insulation of the above systems, there are precast hollow core and solid concrete panels of less thickness than the above systems that span various distances. I was thinking about using hollow precast beams for the floor of my garage, but probably will not go that route.
Edited 2/26/2008 8:44 pm ET by CaseyR
CaseyR thanks for the tip on the insul-deck web site. The pictures there made it come together in this old finns (of Finland) head. I appreciate all of the response that the members gave me; thank-you men...and women if anyone was in that catagory.yours yoro
Edited 3/7/2008 11:39 am ET by yoro
If you don't need or want the insulation of the above systems, there are precast hollow core and solid concrete panels of less thickness than the above systems that span various distances. I was thinking about using hollow precast beams for the floor of my garage, but probably will not go that route.
Will you please share any links you have for products of this kind.
I've just begun considering building an attached two car garage with a driveway which would connect from an elevated road to the third story of the home. I'm wondering which method and products would be the most cost effective.
happened to catch this awhile back, might be someone you could talk to in the list of suppliers. ""To handle the job, DiMarco selected three precast concrete manufacturers: Empire Precast of Rochester; Lakeland Concrete Products of Lima, N.Y.; and Jefferson Concrete Corp. of Watertown, N.Y. Jim Boyce, president of Empire, says his company was involved in phase one and was called upon by DiMarco to consult on the second half of the project."" http://www.precast.org/publications/solutions/2007_summer/collegiate.htm
They can't get your Goat if you don't tell them where it is hidden.
Thanks DT,
Lots of possible methods, including pouring sections on top of another slab nearby, like a tilt slab operation, and then moving them into place.
I like that idea the best so far. I'm just not yet knowledgeable about the engineering requirements and weight for a twenty foot span.
Considering the cost of fill for such a project, I'm happy to consider any other options.
I don't either. What little I know about them came from being a super on a 2 jobs that used pre-stressed planks. All engineering was done by the manufacturer. Ours were trucked in and craned into place. Also the floor load requirements were for a winery so the loads were high as opposed to a residence.
They can't get your Goat if you don't tell them where it is hidden.
Interesting engineering, such large voids running through them.
I've never seen anything like that before. Thanks for the photos.
I helped on a project once where we used something called-
Q-decking
You laid steel beams out across the span every five feet ( can't remember actual interval) and set these steel pan between them.
Very fast and simple.
Something to think about. beats the heck out of building
and removing forms.
Also no crane.
Edited 3/7/2008 6:05 pm ET by Henley