*
did one on a roof deck, used doubled lup 3/4 pt plywood with a product called ice dam on top ( supposed to be self sealing when punctured with nails or screws) the stuff is reverse wound and sticky, you have to peel off the top layer of plastic to make it stick to whatever you put on top, then put down 3/4 mortor board with screws ( the coated kind recomended) 6″ on center square pattern, oh and for good measure the ply was t&g and we sealed all of the joints with sillicone. solid as a rock, will not leak ( if you slope the floor and overlap the ice dam properly, and flash it correctly at all corners ( i like copper but thats just me))this deck is the roof for a bedroom and is exposed to the nastiest san francisco weather. it will not leak or break down. overbuilding is the only way to go. after all the house it is attached to is about 100 years old and i figure i will be dead and gone by the time anything goes amiss with my work. do your self a favor, over build and sleep good at night. just when you think you have gone too far go that extra yard… you too can sleep like a baby.
Discussion Forum
Discussion Forum
Up Next
Video Shorts
Featured Story
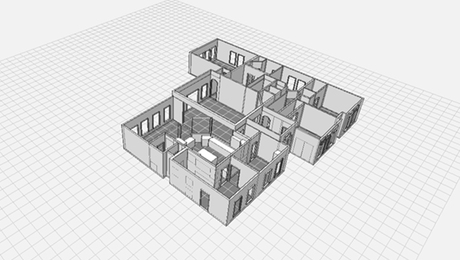
Hover's smartphone app offers an easier way to get precise 3D scans.
Featured Video
How to Install Exterior Window TrimHighlights
"I have learned so much thanks to the searchable articles on the FHB website. I can confidently say that I expect to be a life-long subscriber." - M.K.
Fine Homebuilding Magazine
- Home Group
- Antique Trader
- Arts & Crafts Homes
- Bank Note Reporter
- Cabin Life
- Cuisine at Home
- Fine Gardening
- Fine Woodworking
- Green Building Advisor
- Garden Gate
- Horticulture
- Keep Craft Alive
- Log Home Living
- Military Trader/Vehicles
- Numismatic News
- Numismaster
- Old Cars Weekly
- Old House Journal
- Period Homes
- Popular Woodworking
- Script
- ShopNotes
- Sports Collectors Digest
- Threads
- Timber Home Living
- Traditional Building
- Woodsmith
- World Coin News
- Writer's Digest
Replies
*
I will be making a screen porch/sunroof addition to a house which ideally includes a masonry or tiled floor. I'm pushing for a quarry tile floor but I'm at a quandary as to the most cost effective way of building a nice stable substrate for the tiled deck. The entire deck will be under roof and only take whatever weather penetrates the screens. The deck will finish at about 3 feet above grade and the owner does not want to enclose the area beneath the deck, which ruled out my plan to make a block foundation wall and backfill and cast a slab. some dimensions; 14' X 39' with attachment to house running the long dim. I thought to frame the floor system stout, like PT'd 2x10's 12" o.c. with a doubled 2x10 midspan support beam and doubled 2X10 band, each supported on masonry piers every 10 feet. Subsequently double layers of 3/4" ply glue and screwed plus tile backer bedded in thinset and screwed down. Certainly, straightforward and labor intensive.
Any better ideas to achieve an ideal tile subfloor? Would a Mudset be easier and cheaper? I,m all ears.
*I don't think it matters (sounds stout to me), but someone might want to know, so to save time:Are the PT'd 2.10's 12" o.c. running the 14 feet or the 39 feet?Rich Beckman
*Sounds like overkill ... I deliberately overdid it with a small porch: 2x6's (ripped to 5") 12" o.c., 5' span, 3/4" pt T&G plywood, and construction adhesive to hold slate tiles. The adhesive was the stone supplier's suggestion, worked fine.It -sounds- like you have just a 7' span? Deflection is everything, of course -- someone here will have a L/? figure, I bet -- but I don't see why the floor need even be as stiff as a tiled bathroom floor. Even if you want it that strong, there must be cheaper and faster ways -- maybe a lightweight concrete floor?
*I have limited experience with tile, but I've done several slate floors with just doubled glued and screwed ply 5/8 X2 over existing floor framing (I added the 2nd layer). . .no backer board, no exceptional sub structure framing except maybe some added solid blocking. No problems, except with wonky slate.With 2X10 12"o.c. you don't need the support beam. . . a #2 Spruce with 40lb/sq' live load will span 16'-5" AND support a ceiling!!! You could back off to 2X8 @ 12"o.c. and use the beam and still be comfortably overbuilt.Be sure to build in a slope for drainage. 45degrees should do it! :} -pm
*Overkill is what I seek but not to the extreme, and I think I have some room to downsize to 2x8's. I thought of maybe casting a slab of 3" concrete on onelayer of 3/4 ply seperated by a layer of 30 lb felt. Cost would be cheaper material wise and labor wise as well. but would this be okay when framing will be exposed to temperature fluctuations w/expansion/contraction=movement? A structural engineer acquaintance was kind of negative about the idea saying he only would spec. a steel structure to support the slab for stability in the face of temp. variations. I'm also including some kind of translucent roof on the porch. Anyone seen affordable translucent roofing material that looks and installs better that the corrugated stuff commonly available. I priced some nice looking commercial stuff w/ standing seam details and it looks nice but at around $12/ft2 a bit too much. ideas? Anyone ever cast slabs on wood framed floors esp. in unconditioned environments.
*yeah the slope for the floor sounds good..45 degrees oughta keep it nice and dry.nd.
*Noel,I can't imagine tiling on top of a wooden substrate in an exterior application, concrete board & thinset or not. The first bit of water that seeps in somewhere, and it will, will be the beginning of the process. I see nothing but future problems. If the floor will be tile, I would go with a concrete floor somehow. I've never put a concrete floor on top of wood framing, but I'm sure it's been done. I'm sure someone else can let you know how much support you need.Red dog
*Noel,I have used Suntuff polycarbonate. It is unbreakable, UV resistant, and very clear. Foam or wood closures are available. The dreaded Home Despot carries it here. I could not find a website.KK
*did one on a roof deck, used doubled lup 3/4 pt plywood with a product called ice dam on top ( supposed to be self sealing when punctured with nails or screws) the stuff is reverse wound and sticky, you have to peel off the top layer of plastic to make it stick to whatever you put on top, then put down 3/4 mortor board with screws ( the coated kind recomended) 6" on center square pattern, oh and for good measure the ply was t&g and we sealed all of the joints with sillicone. solid as a rock, will not leak ( if you slope the floor and overlap the ice dam properly, and flash it correctly at all corners ( i like copper but thats just me))this deck is the roof for a bedroom and is exposed to the nastiest san francisco weather. it will not leak or break down. overbuilding is the only way to go. after all the house it is attached to is about 100 years old and i figure i will be dead and gone by the time anything goes amiss with my work. do your self a favor, over build and sleep good at night. just when you think you have gone too far go that extra yard... you too can sleep like a baby.
*The framing sounds great to me. I'd forgo the double 3/4" ply, and go with a single 1 and 1/8" T&G exterior glue. That stuff is perfect for tile. Doubling up on layers just compounds any lips or uneven-ness.I'd float a fairly standard 1" substrate of deck mud with some 2x2" 16 guage wire in the middle over an isolation/curing membrane of 15-30 lb felt. Thinset the tile over that.My only worry is expansion. Wood and tile expand and contract at different rates, and for that matter, so will the deck mud and the tile, but at least its closer. The deck mud is denser than gypcrete or concrete, so there is less likeley a chance for cracks.Lets hope this job is in a temperate climate.