*
Back when I worked commercial construction in college, we did quite a few tilt up jobs, and some with pre-cast “double t’s”. the tilt up panels were poured on the interior finished slab floor (with a release liberally sprayed on the surface first!), and the tilt up panels were well reinforced. Each also had two “pull holes” installed, which consisted of a metal tube surrounded by a web of cables, the length of which depended on the slab. These were placed in the form with the cables splayed out in the centerline of the panel, which gave a lot of adhesion to the interior of the panel before the lift. The bottom and sides of the panels had weld plates installed flush with the surface, as did the foundation. When the panels were set in place, they were simply welded, backfilled and the 2 or three feet remaining between the interior floor slab and wall then poured. Adjacent panels were sealed with foam backer rod and caulking. This same contractor eventually developed a panel material which included a high concentration of gypsum to lighten it up some. These were tall (30 feet plus) panels, about 8 inches thick, and were heavy, heavy, heavy. –Ken
Discussion Forum
Discussion Forum
Up Next
Video Shorts
Featured Story
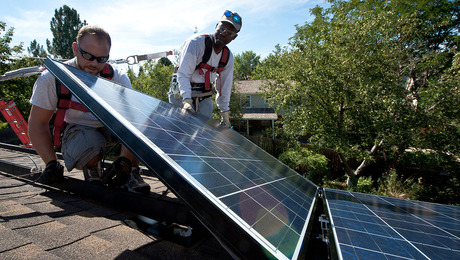
Does drilling new screws into the roof rafters compromise the strength of the roof?
Featured Video
Video: Build a Fireplace, Brick by BrickHighlights
"I have learned so much thanks to the searchable articles on the FHB website. I can confidently say that I expect to be a life-long subscriber." - M.K.
Replies
*
Have done a search of the archives for topics on Tilt up and there dosen't seem to be much.
Now I know it probably falls into the same category as working with steel but it is a big field and I think we could all learn something. How about it? Any experienced contractors out there? Tell us the pitfalls, advantages,costs etc.
In anticipation....
Mark
*Mark, most of the tilt up work that I've seen or done is with big commerical work. Most of the problems with this is having the room on the jobsite to layout the walls and pour. Last one a did was a problem due to steel delivary. I had enought room to layout three tilts and kept getting held up waiting for steel.For people who are not up to speed on tilt up construction, you first pour the footers with a keyway. Then you build all forms on the ground flat. After building all forms and placing all steel you pour concrete. You then wait about three days(this depends on concrete mix and weather) Then using a crane you pick up and place the walls. I know that this is a simple explainion of the procedure and that I have "glossed over" many of other points related to this.Ok Mark as far as pitfalls most of the problems are as follows.1. Space to work. This includes areas for forms and steel.2 A good steel company that can meet deadlines for steel delevary(rebar).3 Crane for just this work. This means have a crane schedule and sticking to it.4 Form removal. Crews have to us care in removing forms and clean up of formsAdvanages1 control over finishes. On must commerical work the concrete recives a texured finish and this allows you to have a better control over insert form finishes.2 Once the form work is done a few times and the crews have the learning curve down you can speed up as most of this is the same old thing.3 Less forms needed for job. By reusing the forms over and over again you have less forms on job for the same amount of concrete placed4 Greater amount of detail can be cast flat. This includes window details, interior drain flashing,and "fancey details"As far as costs go I think precast can get you where you need to go with less money and time.
*Mark, one thing to add to Bill's excellent summary: IF you plan to use the building slab for the tilt-up work area, be sure the slab is strong enough for the equipment you will be using. It may be that the slab must be heavier than normally required simply to accomodate the tilt-up activity. (This is from an article I read, not from personal experience).Do things tilt from the opposite direction down there?Regards, Steve
*Steve have used she-bolts that were installed in slab to add strong backs and stiff backs for the lift. Still no fun in patching concrete from the boom lift or hanging scaffold.
*Thanks for the input guys. Any words on how panels are attached to each other? Anyone know of any web sites with more information? Steve.. tilt is the same as our bath water... it would have to be different... maybe I can get a govt. grant to do a study on this subject??If the footers are poured first and then keyed for the panels, how does the floor fit into this set up.. do you leave it short of the footers and fill in later?Kind regards Mark
*Back when I worked commercial construction in college, we did quite a few tilt up jobs, and some with pre-cast "double t's". the tilt up panels were poured on the interior finished slab floor (with a release liberally sprayed on the surface first!), and the tilt up panels were well reinforced. Each also had two "pull holes" installed, which consisted of a metal tube surrounded by a web of cables, the length of which depended on the slab. These were placed in the form with the cables splayed out in the centerline of the panel, which gave a lot of adhesion to the interior of the panel before the lift. The bottom and sides of the panels had weld plates installed flush with the surface, as did the foundation. When the panels were set in place, they were simply welded, backfilled and the 2 or three feet remaining between the interior floor slab and wall then poured. Adjacent panels were sealed with foam backer rod and caulking. This same contractor eventually developed a panel material which included a high concentration of gypsum to lighten it up some. These were tall (30 feet plus) panels, about 8 inches thick, and were heavy, heavy, heavy. --Ken