being a general contractor, I am considering framing a house on my own for an extremely patient client. Any thoughts, comments or horror stories out there?
Discussion Forum
Discussion Forum
Up Next
Video Shorts
Featured Story
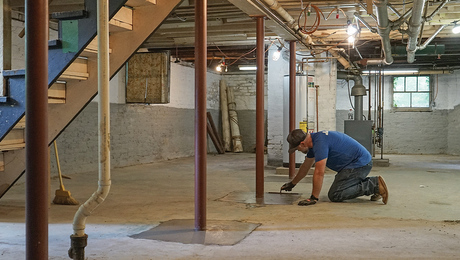
Upgrading the footings and columns that support a girder beam is an opportunity to level out the floor above.
Highlights
"I have learned so much thanks to the searchable articles on the FHB website. I can confidently say that I expect to be a life-long subscriber." - M.K.
Replies
Go up and read the thread, What am I doing wrong?
Actually, I sell to a lot of framers and am amazed at what they get away with, so the answer is yes you can do it yourself if you have the know how and equipment. without a forklift, nailgun and compressor generator (or power on site) forget it.
I framed one house totally solo...which just happened to be my own house.
Lots of work. Lots and lots of work.
One day for beam, temp beam support, and mudsills.
It took me six days per "floor"...three days for a platform (each floor about 1600 sqft), and three days to do the exterior and interior walls for that platform. Another three days for the second floor platform, and three more for the second floor walls.
Sho' nuff, another three days for the attic platform. A day to frame and raise the gable end walls...which was the first time I thought what a sight it'd be to see one of those gable walls tumble to the ground below. I raised all of the walls as bare studs except for the attic gable walls. I sheathed those before raising them.
I forget how long it took to frame the roof...I think a day to set staging and get started on the ridge beam, then another couple of days for the rafters. But it must have taken me a couple of more days to sheath the roof, as I had to manhandle all the ply sheathing up on the roof. No boom truck back then.
Six days to shingle...membrane, drip edge, felt, and about 22 square of shingles. Again, no boom truck, just a sore shoulder to stage the bundles on the roof.
Joists were TJIs. Walls were 2 by 6, 9'8" on first floor, 8' on second. All three decks were 3/4" T&G subfloor. Roof and walls were half-inch ply.
Think ahead on how you can section long walls (for raising) while still offsetting the breaks in the sole and top plates.
I busted my arse. Thankfully figuratively and not literally.
Did I mention it was lots of work?<g>
Tools? I had a 12" CMS, a sidewinder, and a framing hammer. No air, no wall jacks, no forklifts. I ran the electrics off of a gas generator. I used pumpjacks for staging.
Lots of work.
Your customer may be patient...but Mother Nature may not be. Repeated soakings may wear everyone's patience, especially when the ply delamnates, the OSB swells, and the framing turns black.
Also, your local inspector (if there is one) may only allow portions of the framing (usually sheet goods) to get rained on only so many times. Then he could order you to R&R it. Ouch.
Lots of work...but do-able.
With all the other little tidbit jobs thrown in...backfilling the foundation, building construction stairs, getting materials, installing Bilco basement stairs, etc, etc...it took me about six or seven weeks from nekked foundation to getting a framed shell with the walls sheathed with ply and the roof capped with laminated architectural-type shingles.
Worst part of the job? Roofing. It was so hot...cloudless skies, temp in the mid-90s with 90%+ humidity...with so much heat radiating off the dark shingles...that at the end of every day, I swore that when I looked in a mirror my eyes would be shriveled up like raisins.
Oy.
No horror stories. Just lots of work. Plan material deliveries so that if you are going to work slowly you don't have too much material sitting on site for too long, just in case of theft. I had a platform delivery (joists, rim stock, ply), then two days later had the walls delivered (studs and sheathing). The material didn't back up, and it kept me on a timeline.
Edit: Wanted to add: Brace your framing often, and brace it well. Don't skimp on bracing. And one more thing...framing solo is lots of work.<g>
Edited 6/29/2002 12:14:27 AM ET by Mongo
View Image
I GC'd and framed my own house. I used to be a framing contractor, so still had all the stuff...three guys is a good ,and IMO minimum, crew size (and I did have two guys with me: one carpenter and one helper), and there's always some friends dropping by, that you can put to work. I know I got a much better job by being there all the time, rather than subbing it out and fixing stuff every evening...
Good luck, BB
Bucksnort.....that's my plan on the house I'm now at engineering with
Mongo....what a story!!! And ooohhhh so true.
Framing is a young man's job. Yes, it is great to have good tools and a forklift, but a healthy dose of youthful testosterone is, I think, equally important.
Real question....I'l like to lap the exterior sheathing over the platform joints for strength. I've thought of several ways to do this, but I'm afraid the framing sub will give me a hard time about it, as the only way I can think to do it is from the outside once the studs are up....not real easy. So do others think this extra step is useful and if so, how would you go about it?
BruceM
"Real question....I'l like to lap the exterior sheathing over the platform joints for strength. I've thought of several
ways to do this, but I'm afraid the framing sub will give me a hard time about it, as the only way I can think to do
it is from the outside once the studs are up....not real easy. So do others think this extra step is useful and if so,
how would you go about it?"
first I am not a pro, just a DIYer that has done some framing. This is how I would do it.
I would frame the wall on the deck, then install a hinge onto the bottom plate of the wall and the deck with the metal banding that comes with the lumber when delivered making sure that the bottom plate is located the correct distance from the edge of the deck (usually I have a chalk line there from doing the plating), sqaure the wall, sheath and then raise the wall. the hinge will prevent the wall from sliding off the deck. I am sure there is a faster/better way, lets hear what the pros have to say.
If the sheathing is not to overlap the rim/band joists then I would just nail on some 2x4's to prevent the wall from sliding off.
line the bottom edge of the bottom plate up with the chalkline, toenail from the top of the bottom plate into the floor w/16s every four feet or so. I've never had a wall slide out doing this. I've never done it with a wall taller than 9 or 10 feet, though. If you're going to go that far, why don't you go a little farther and install the windows, trim, siding, while it's still flat? they go right up with wall jacks, and if you're prepared (trim prepainted, etc.), it's pretty efficient. FHB has an article on it - don't recall the number.
Thanks for the responses 27Sean and AlanRobertson.
Sounds like a plan, but let me recap.
1. Frame up the first floor, but put the first layer of sheathing on sideways, thus the sheathing will rise 4 feet on the first wall
2. On the second floor platform, layout the bottom plate, mark the inside edge on the subfloor, and nail a 'hinge' to keep it from sliding off when the wall is raised.
3. Tip the bottom plate up on edge and put the wall studs together and square it.
4. Nail on the sheathing...allowing enough to stick over the bottom plate that will match up with the edge of the sheathing already on the wall below
5. Raise the wall, nail in bottom plate, brace and go down from below and cut/install nailers at the sheathing joint, then nail it into the first floor wall studs.
Think it'll work?
BruceM
I wuz 52 when I framed my last house, I'm not bragging, but you can learn to work smarter, and I could do it again. Actually I'm planning to do a spec, so, I will do it again...and sheathing 'round here usually laps the band, don't see why that should be a problem...
Good lick, BB