What is the best way to vent an attic?
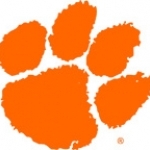
Good Evening To Everyone,
I have a 1970 Ranch that I am planning on re-roofing in the next few weeks. I want to add some more insulation and improve the ventilation in the attic as well. First off, will using the fiberglass batts be better or will the blow in cellulose be better? Second, will putting on a ridge vent and continuous soffit vent be better than using the soffit vent and gable vents with a exhaust fan placed at one gable vent be better? I am planning on shooting for a R value in the upper 40 range.
Replies
Where are you located? Would you consider a conditioned, unvented attic if you could gain better air quality, lower electric bills and less dusting required in the home?
Generally cellulose is better, but be sure it doesn't block eave vents.
Ridge + soffit vents is far superior to exhaust fan, and is maintenance-free. The soffit vent can be either continuous or a cut-in 8x16" vent about every 4 feet.
The best way to vent an attic is to reduce the need for venting!!! We supposedly vent attics to (1) REMOVE MOISTURE and (2) REMOVE HEAT TO LOWER AIR CONDITIONING COSTS AND INCREASE ROOF SHINGLE LIFE.
(1) If we airseal the attic/ceiling interface well, very little moist house air (and heat) will get into the attic to cause condensation/mould growth on the roof sheathing. So do this first before adding the retrofit blown cellulose on top of the existing insulation. Now the existing ventilation is probably more than enough. High 40's is a good R value to shoot for.
(2) A high level of attic insulation is better than attic ventilation at reducing air conditioning costs.
(2) Attic ventilation does very little to nothing at increasing shingle life. The biggest influences are: shingle quality, shingle colour and shingle orientation/direction (and the last we have no control over) If attic ventilation severely decreased shingle life, we would not be pushing all the foam sprayed unvented attic rafter cavities to make the attic a conditioned space. This technique allows no cooling of the roof during the hottest part of the day......period. They roof can cool to the exterior at night only. So if roof venting is needed for increased shingle life.......there are going to be a lot of prematurely failing roofs based on this "on the street" theory.
The best way to vent an attic is to reduce the need for venting!!! We supposedly vent attics to (1) REMOVE MOISTURE and (2) REMOVE HEAT TO LOWER AIR CONDITIONING COSTS AND INCREASE ROOF SHINGLE LIFE.
I don't know who "we" is but "you" suppose wrong. In your neck of the woods the primary reason to vent is to prevent ice damming.
DG/Builder
In my neck of the woods in jan/feb/mar, we get still sunny days of 0 to -3,4 celius (25-32 F) with no/little winds. Exposed parts of dark roofs warm enough to cause snow melting/running water until it gets to the cold snow covered eaves when ice dams still occur even with code venting installed. Some days you would have to have full ridge, soffit and gable end venting (a little impractical) to prevent the attic from getting over 32F and causing the melting leading to ice dams.
You can draw all the diagrams you want with arrows telling the air where to go, but in real life this will not always happen or happen with enough air volume so as to be effective to work as designed. Since it is virtually impossible to stop ice dams with code required passive venting, the best way to prevent damages from ice dams is to have proper eave protection installed on all slopes under 9 in 12. The code recognizes this here and requires the eave protection.
Read this recent publication from our national housing agency and you will see some of the misconceptions about venting floating around the streets and our building supply centers:
http://www.cmhc.ca/en/co/maho/gemare/gemare_001.cfm
Well, around here most winters (though not this last one) you can pretty well tell which homes have proper venting/insulation (they work together) and which ones don't.If you're not going to vent the attic you should go to a full "hot roof" strategy. Anything in-between is asking for trouble.
If Tyranny and Oppression come to this land, it will be in the guise of fighting a foreign enemy. --James Madison
I'm not sure where you are, but in Connecticut, I see "properly vented" vented roofs sporting spectacular ice dams on a regular basis. In most cases, air sealing and insulation are better solutions, with going to a full hot roof as you suggest often the best approach. Part of what I do for a living is home energy consultations. The things people think it's ok to do in attics continues to astound me.
Some roofs, in fact, are impossible to vent. How do you balance the soffit and ridge vents on a hip or a reverse gable? You can't. Andy
"Never try to teach a pig to sing. It wastes your time and annoys the pig." Robert A. Heinlein
"Get off your dead #### and on your dying feet." Mom
Yeah, I didn't mention air sealing, not wanting to get into gory details, but it's a "complete package" -- air sealing, insulation, ventillation.True, hip roofs are hard to "balance", but there are ridge vent products that can be used on the corners, so it's not impossible. And we don't have that many hip roofs around here anyway.Basically, I have nothing against a "hot roof" approach, but you have to pick one or the other -- a "cold" roof with poor ventillation is asking for all sorts of problems. And retrofitting a "hot" roof to an existing home is challenging at best.
If Tyranny and Oppression come to this land, it will be in the guise of fighting a foreign enemy. --James Madison
I've got to agree with Experienced. Roof venting is perhaps the single most poorly understood aspect of building, and our long-standing traditions are based on a marginal solution developed 60 years ago. We can do better.Andy
"Never try to teach a pig to sing. It wastes your time and annoys the pig." Robert A. Heinlein
"Get off your dead #### and on your dying feet." Mom
"I've got to agree with Experienced."
OK, then help me out here. How would you explain this statement of Experienced's? "If attic ventilation severely decreased shingle life, we would not be pushing all the foam sprayed unvented attic rafter cavities to make the attic a conditioned space. This technique allows no cooling of the roof during the hottest part of the day......period. They roof can cool to the exterior at night only. So if roof venting is needed for increased shingle life.......there are going to be a lot of prematurely failing roofs based on this 'on the street' theory."
I can't make heads or tails of it! Is anyone saying attic ventilation decreases shingle life? What does it mean that spraying unvented-attic rafter bays with foam insulation does not allow cooling of the roof during the hottest part of the day? Is he recommending foam in the rafter bays in all attics, or only unvented ones, or not at all?
- Confused in California"he...never charged nothing for his preaching, and it was worth it, too" - Mark Twain
He's saying, and I've spoken with researchers whose work bears this out, that attic ventilation has little to no effect on shingle life.
More to the point, shingle color has a far greater effect on shingle temperature than does ventilation. If heat were really the problem, manufacturers would only sell white shingles that don't get as warm as the black ones that seem so popular.Andy
"Never try to teach a pig to sing. It wastes your time and annoys the pig." Robert A. Heinlein
"Get off your dead #### and on your dying feet." Mom
I haven't done any studies, but I can think of at least one roof I tore off and replaced that had inadequate venting ( L-shaped house, one small gable vent at each extremity, no soffit venting) where the shingles near the vents were in pretty good shape, but their condition got progressively worse the higher up and the further they were from the gables.
That's one. How old was the roof? Were there other possible contibuting factors? The researcher I know has multiple roofs in service, with controls and known variables.
It's dangerous to draw general conclusions from small samples. For example, I've torn off cedar siding to expose deteriorated housewrap. Hmm, seems like the cedar did in fact contribute to the housewrap failure, or at least that was the conclusion my reading had pointed to. But still, what did I know? It's possible that housewrap stood exposed to the sun for 6 months before it was sided. There are lot's of unknowns in any tearoff.Andy
"Never try to teach a pig to sing. It wastes your time and annoys the pig." Robert A. Heinlein
"Get off your dead #### and on your dying feet." Mom
Let us all rejoice in the return of the vent wars. It's been a loooong time!;)
Welcome to the Taunton University of Knowledge FHB Campus at Breaktime. where ... Excellence is its own reward!
It has indeed. When asked your political affiliation, the proper answers are: Pro-vent and Con-vent.Andy
"Never try to teach a pig to sing. It wastes your time and annoys the pig." Robert A. Heinlein
"Get off your dead #### and on your dying feet." Mom
Thats a lot of extra money you are talking about I believe.
If I remember right the correct way to do it is wet spray the rafter bays and then you still have to fill with celulose in the joice cavities.
Now is the attic conditioned as well?
So if its 105 degrees out side in the shade what would that attic temp be in the sun with a black roof and a white one ?
tIM
I have as well seen premature checking and cracking of shingles with dark colors of unvented roofs in the soffit area while the ridge was in good shape and ridge vents were used.
Tim
Interesting, because with a ridge vent, the shingles closest to it should be the hottest on the roof. Think about it - If air moving up the rafter bays is cooling the roof above, that air is getting hotter as it rises. So, if the shingles nearest the ridge vent were in the best shape on the roof, then wouldn't that suggest that heat is good for shingles?Andy
"Never try to teach a pig to sing. It wastes your time and annoys the pig." Robert A. Heinlein
"Get off your dead #### and on your dying feet." Mom
If the soffit was vented I think you would be right . That way it would bring in a cooler supply of air from the bottom up. In the cases Ive seen where I could tell a difference the soffits were not vented but had two or more gable vents . From the description I was taught , the top section gets a cross breeze but no up draft.
From a mechanics view it takes air intake to produce an exaust.
Im more interrsted in the cost with my other questions involved about a conditioned attic space.
Tim
Conditioned attics cost more to do initially. Of course - there's more surface area to insulate, and foam costs more than other insulations (although it outperforms anything else on the market). Because foam actually provides its stated R-value, unlike fiberglass, there should be an energy savings there despite the greater exterior surface area. Factor in the losses that occur with air handlers and ducts in a vented attic( Which even if insulated to code at what, R-6? aren't insulated to ceiling and wall standards. Given that the highest Delta-T in a house is going to be between the attic ducts and the unconditioned attic air, this is just plain stupid, in my not so humble opinion) So, in fact, I'd expect both an energy and a comfort dividend with a hot roof that's not approachable with a conventional attic.Andy
"Never try to teach a pig to sing. It wastes your time and annoys the pig." Robert A. Heinlein
"Get off your dead #### and on your dying feet." Mom
What air handlers? What ducts?
If Tyranny and Oppression come to this land, it will be in the guise of fighting a foreign enemy. --James Madison
Im not trained in this subject. I had a state hvac inspector that could blow people away on the subject and taught at a votech school . Always made me feel stupid .
I think what hes talking about is the air temp outside the duct service. Which could include an air handler because lots of them are in the attic. Hes also including a hot roof which could be black [or dark color] or hes talking about the type .
He needs to get his fingers warmed up for me so I can fully understand it and hopefully take questions.
Its always been a subject of air temps around the duct pipes and plennum. There is little insulation compared around the pipe and such a small area inside the pipe that its hot inside. So we get a blast of air thats hot and still fights it as it runs because it will be warm at best for a minute or two. Then after 5 minutes of run time it shuts off and the cycle starts again.
Another topic has always been the temp of the attic compared to the amount of insulation separating the home area. Here he hasnt given the temps of a conditioned attic in either a white roof or a black one. Also the total costs to get one.
Now more in my area,
The problem I always have when we add new gadgets on a home is will the appraisor pay for them?[figgure of speech] They dictate the values and are lord of setting our prices off comparibles. The bankers use them to their own advantage to often set up their own team they use of AP that work only for them although the public pays them. They nearly always set values low if a bank calls them .
I asked the question in the truckers forum , What will it mean to owner operators when the fuel prices exceed 3.00 per gallon this year as forecast. BTW its already there and will climb higher. They have reports of 3.01 fuel now. They simply said they will charge more and they are not worried, but the public is the one who decides if the frieght moves and at that which frieght. Since transportation is a sizeable increase to some products it remains to be seen if we will pay the increase or do with out.
They of course dont have my studies to base their opinion. Across the Southern states where income is low it has remained low exceopt we have a bigger share of the market where as the unions are folding in the North East. We are picking up their work for half the price and are proud to get it . Outsourcing has been a big problem with the workforce and it depends on what work force someone is in which relates to customers. Although our construction figgures are just becomming soft there are still bunches of others going belly up. Our folks have been stangled by Heating costs this past winter and some have reported paying 5 times the normal amount . Gasoline as I mentioned has been another one to watch closely but its certain there isnt a lot of extra money. Of course I speaking about the Southern states only. Taxes have continued to climb for property taxes and bonds. Food costs citing beef prices are the highest they have ever been. Interrest has now began to rise after a surge in labor and material prices in housing . So whats left for them to give ? Not extra unless it can be financed. Which brings us back full circle.
Tim
My point is that in many parts of the country it's unusual at best to have any ductwork or air handlers in the attic.
If Tyranny and Oppression come to this land, it will be in the guise of fighting a foreign enemy. --James Madison
That could be. Here in the northeast, there aren't many new attics without ducts, and particularly on bigger homes, it's quite common to find air handlers there - often with hydronic coils.Andy
"Never try to teach a pig to sing. It wastes your time and annoys the pig." Robert A. Heinlein
"Get off your dead #### and on your dying feet." Mom
Tim, the answer to your question depends entirely on the house and the location. In areas without temperature extremes, it wouldn't matter a lot. In the north or the south, it does. Heat loss depends on the difference in temperature, delta-T, expressed in Kelvin. In the north, my attic might get below zero F, and the ducts might have 130 degree F. air in them. That's an extreme delta-T. The reverse happens in the summer with AC and 150 F. attics. Not to mention the typical lack of duct sealing that leaks to and from the attic. Conditioned attics solve these issues.
I am assuming fiberglass in the ceiling v. foam in the roof, btw.
Another issue is workmanship. I'm not saying that I've never seen fiberglass insulation installed correctly in an attic floor, but I could count the number of times that's been my experience on one hand. And even so, with one face exposed, the stuff loses half its r-value at a delta-T of 70F. or so.
Foam installers, in my experience, not only have a better product, they're aware of it's ramifications and do a better installation. Not always, but more often than the glass guys. And if you have an air handler in a vented attic, don't you think it would perform better in an insulated room there? Ever seen that done? You'd have to add that cost to the fg job for a fair comparison of fg and foam.
So, it's nearly impossible to compare apples to apples in most houses because of the typical differences not only in insulation, but in installation. I believe that the advantages of a hot roof and a conditioned attic frequently outweigh the disadvantage, which is only initial cost.
Go to http://www.buildingscience.com. Their Building America program did a study in Las Vegas that clearly demonstrated substantial energy savings from conditioned attics in that climate. They may have more data now. Also look on PATH's website.
But you've got the basics down right. Andy
"Never try to teach a pig to sing. It wastes your time and annoys the pig." Robert A. Heinlein
"Get off your dead #### and on your dying feet." Mom
Oh joy, I wanted to talk about unvented attics again, thankfully someone else has started the thread. I'm trying to become a foamed roof True Believer, but I can't shake these niggling doubts.Since I'm in a cold climate (NJ), buildingscience tells me that there needs to be drying to the interior as snow melts. But the only "Houses that work" spec for that scenario (Boston, no details BTW) requires foam insulation with 10 perms. Given permeability is determined by thickness of material as well as its perm rating, can you really get that with several inches of foam? Even EPS becomes vapor impermeable beyond 3". It seems to me that allowing some venting via baffles to dry the roof deck (from external moisture, not from interior moisture, which can be handled in other ways) would be useful insurance.Even in hot-humid climates, if you didn't put a VB over the roof deck like buildingscience says you should to prevent vapor pressure, then venting might at least dry out the roof deck faster than if you just relied on the foam absorbing and releasing the moisture.From what I've seen of roof leaks in my house, sometimes they come with water getting underneath the materials and into the sheathing and rotting it out, not a steady stream of water onto the attic floor. This form of "leak" will never show up on a foamed roof, but at least venting would dry out the roof deck a lot faster than if it is covered in foam. So maybe the roof deck might survive until the next tear-off.In all the talk of R-values of foam, I'm surprised no-one mentions thermal bridging through the rafters. That will surely reduce energy savings by anywhere up to 20%. Putting rigid foam over the rafters will obviously alleviate that, although again you won't see roof leaks. Just out of curiosity, has anyone actually seen a roof leak manifesting through open cell foam? I've heard it repeated as motivation for open cell many times, but I'm starting to get skeptical.And since I'm ranting here, let me complain about rafter baffles that provide a 1" air space, when buildingscience says it should be 2".I'm wearing asbestos, flame away.....
All interesting questions. I'd use Building Science's info for Boston in NJ. I think Boston is in the same agricultural zone as Sussex County, and that's considered a mixed climate. Living in that same zone myself, I can tell you that it's not a lot different than Warren County, where I grew up. If you're in Cape May, I might look to Baltimore as a model.
Otherwise, I'd research more. Look to PATH (Partnership for Advanced Technology in Housing) for more info.
If you want 2 in. vent channels, just make 'em out of rigid foam.Andy
"Never try to teach a pig to sing. It wastes your time and annoys the pig." Robert A. Heinlein
"Get off your dead #### and on your dying feet." Mom
I look at both Cold and Mixed-Humid climate for planning, since I expect big climate changes in the next 10-20 years. The Designs That Work page for BS, for both Cold and Mixed-Humid, both emphasize drying to the exterior, with an XPS vapor retarder under the insulated roof deck. With XPS on the inside, I wouldn't put XPS baffles on the outside over the vents, let alone the plastic provent baffles.
Given the lack of documentation, suggesting that this option has not been fully investigated, I'm increasingly nervous about following the Boston model. Also the Designs That Work have the feel of having been designed by a committee, which is good because they may reflect several viewpoints.
My current plan is:
Baffles constructed from 1x2s and 1/4" plywood (rafters are 2x6 @ 22oc, want to keep load down).
Fur out with 6" Marinoware studrite steel studs (smaller steel studs are just harder to install)
Fill the 9" space with open cell foam
1-1/2" XPS with 1x3 furring strips (Owens-Corning Wallmate)
My worry about closed cell foam: first that over time gaps will open up between the rigid foam and the sheathing and the air impermeability will be compromised; second, the double VB between SPF and XPS thermal break.
It is very very tempting to say, oh screw it, and just have open cell foam sprayed in the 2x6 rafter bays, as Icynene recommends.
Thanks for the PATH ref, I will look it up.
I'd just go with the Icynene, myself. If the AHJ allows it, that is, or if he's not looking. The Connecticut code allows hot roofs if they're insulated with closed cell foam. Lots of the local BIs look the other way and allow Icynene. Air sealing is the key, and open cell foam acheives that well enough while allowing some vapor transmission.
Andy
"Never try to teach a pig to sing. It wastes your time and annoys the pig." Robert A. Heinlein
"Get off your dead #### and on your dying feet." Mom
Thanks for taking the time to respond, I very much value your opinion.I've spoken to AHJ, as long as I've done my homework he is open to argument.Ray Moore suggests at least 8" open cell foam on roof deck. One time he made a remark that Icynene recommends 5-6" because that is as far as they are fire-rated, I didn't understand that. Do the math: 5" of icynene gives about R-18. Lose at least 20% to thermal bridging, brings it down to R-15 or less. Adding 1-1/2" XPS thermal break brings that back up to about R-22 optimistically. Still not great. Ideally for the roof deck I'd like something like R-38 (assuming in foam terms that is equivalent of R-50 in other insulation schemes). I can get there with 3-5/8" steel studs furring out, or do the baffles and fur out 6".
This thread is running through many of the reasons why the "hot roof" hasn't really caught on. There's simply too little experience with it long-term, and so issues like water leakage create big questionmarks. (Not to say that it's a bad idea, just one that is out of many folks' comfort zone.)The traditional "cold roof" has evolved over centuries, and recent changes regarding insulation and venting are relatively minor adaptations that are well-understood and don't leave a lot of questions unanswered.There is a general issue here, though, about "robustness". Some designs (like the "cold roof") are "inherently robust" -- they're pretty much guaranteed to work unless you do something fairly awful to screw them up. Other designs (like the "hot roof") lack this "robustness" -- they must be engineered and "tuned" to work correctly, and relatively minor things can foul them up.This is kind of like comparing a modern auto engine to, say, one in a 1955 Chevy. The 1955 engine was a design that really hadn't changed in 30-40 years. If you added up all the things that could possibly go wrong in one it probably didn't top 100 items, and there were only about 10 that were biggies. Adjustments (such as breaker point gap) could be off by a factor of two in many cases without seriously affecting performance. Look at the modern engine, however, and there are thousands of things (even if you don't count the transistors in the computer individually) that can cause a malfunction.This is not to say that the 1955 engine is better, or even more reliable, but the modern engine requires a much higher level of attention to design, construction, and maintenance details to work correctly. If you tried to produce a modern engine off a 1950s era assembly line you'd have an unmitigated disaster. The old 1955 engine was "inherently robust", but the modern engine ain't.
If Tyranny and Oppression come to this land, it will be in the guise of fighting a foreign enemy. --James Madison
Dan,
I agree with you but would add a couple of things to consider. A car engine is highly engineered, made of metal and manufactured in a completely controlled environment. Once the design is settled upon, thousands and thousands of identical engines are produced. The engines are expected to last about 15 years.
Compared to this, house construction is the wild west. Houses are made of wood in designs that change constantly. The manufacturing facility changes with each job because the house is anchored to the land and it's too big to ship in one piece. It is expected to last a 50 years and can easily last a century.
Construction is a decentralized industry and I think it's always going to be that way. This decentralization means that it's subject to conflicting forces and, thus, difficult to control. Here are some of the forces at work:
1.) The building system has to be "buildable". The people actually assembling the buildings have to understand the system and have the skills to execute it. It's fine for scientists and engineers to design more efficient buildings. The challenge is to get them built with the workforce and equipment available. The builders also have to have the motivation, which brings us to the next force.
2.) The building system has to be "saleable". The general contractor and all the sub-contractors have to be able to convince the homeowner to pay for the work. Installing an air-tight building envelope, bringing in conditioned air and so forth-- these things take time and money. Ultimately the client has to pay for it. But they seem to expect these things as a matter of course. If you look at the home and garden shows on television, the three things that are emphasized the most are how fast the building or addition can be assembled, how cheaply it can be done and how beautiful the finished surfaces are.
3.) A third force is how "verifiable and enforceable" the different measures of the building system are going to be. You can install a perfect vapor barrier and then the sheetrocker can put holes in it with sloppy screwing. (For that matter, the homeowner often comes in and puts nails and toggle bolts in exterior walls, which put holes in the building envelope.) After the fact, you can't see whether the vapor barrier has been perforated, whether the bricklayer has dropped mud in the cavity between the veneer and the frame or whether the frame carpenter has filled a header with insulation. In the automotive industry, it's pretty easy to institute quality controll systems; it's much harder in our industry. In fact, most of the motivation goes in the opposite direction: people who work fastest get the job and turn the greatest profit.
4.) A fourth, rarely mentioned, force is the "repairability" of the system. In the automotive industry, much thought is given to how a mechanic is going to disassemble an engine in the future. I don't think building scientists are giving future repairs and modifications enough consideration. I think a lot of the newer systems are going to be hard to fix.
5.) A fifth force is emotional. The homeowner, the contractor, the workers all want to see forward progress. It is as emotionally gratifying as driving on the highway with no traffic. Careful flashing, installing a rain screen, taping the vapor barrier, and all the other tedious details that improve the integrity of the building envelope not only cost money, they have an emotional cost. When the visible progress of the job slows or stops, there's an emotional let-down. It requires discipline to deal with these tedious details. Unfortunately, our "git-er-done" culture rarely rewards this discipline. In fact, it's often ridiculed.
6.) A sixth force is the rate of reward and punishment. The rewards of a nicely-appointed new home or addition are immediate: freshly-painted walls, new cabinets, new floors, etc. The punishments for sloppy details in the building envelope are invisible and the cost of them can be spread out for decades. Homeowners are usually oblivious to the details of the building envelope; at the same time, they can make the builder miserable over imperfections in the drywall.
I'm sure there are a lot of forces and considerations I've missed here.
Sorry I didn't respond earlier. My connection was down due to lightning damage at the tower that carries my wireless feed.
Icynene and Demilec for that matter used a test facility that was set up to test for fire rating when applied at a six inch thickness. They got a rating from that testing. Legally they can only refer to that thickness as it pertains to their fire rating. They can only recommend installation of their product in accordance with this accepted fire rating. That's the way it goes.
Of course, the product would be just as safe if applied at 10" but building officials cover themselves from liability by following prescribed methods that have testing to back them up. Commonsense has no place in the discussion.
Ray:
Don't know if you ever looked at my profile but I have three quotes there, one of which is from Will Rogers:
"Common sense ain't all that common, is it?"
I'll take R-15 from Iceynene over most fiberglass jobs, hands down. When you get an R-value from foam, it's honest. I discount fiberglass R-values by about half, because installed in a vented situation, that's the expected loss from internal convection when the temp reaches zero. The greater the Delta-T, the less effective fg is, and the more effective foam and cellulose are.
I think our perceptions of R-values are skewed because of that fact. Published R-values are established in an airtight box in a lab. Fiberglass performs well there, as do cellulose and foam. Put them in the real world, and fiberglass's ability to act as a path for air movement seriously degrades its performance.
Given that, and the discomfort we've all experienced in houses insulated "to code" with fg, our first reaction is to increase the R-value of whatever insulation we use. That's usually not the most cost-effective approach, as the point of diminishing returns is quickly reached. I'd rather see effective insulation used in the first place. A house that's got a true R-38 from foam or cellulose should be far more comfortable than one with a nominal R-38 from fg.
rAndy
"Never try to teach a pig to sing. It wastes your time and annoys the pig." Robert A. Heinlein
"Get off your dead #### and on your dying feet." Mom
Andy:
Why the big resistance to fiberglass batts and loosefill in the US?
I still claim to customers that batts are a good insulation product but care must be taken in installation. Batts, when properly installed in walls with a good sealed exterior air barrier/sheathing membrane (TYPAR and the like) perform very well in walls. I still do prefer a blown/sprayed cellulose in walls, if not too pricey but I have no problem with batts. In fact, probably over 95-98% of R2000 certified low energy homes in Canada have batts in the walls.
The only research I have seen on the deterioration of R value in attics was for low density, long fiber, "fluffer's delight" that was blown to about 1/2 required density. The top layers were so open due to the nature of the reduced density that convection currents formed in the upper few inches and reduced the R's. The effect got stronger as the temperature dropped. Not good!!! Fiberglass batts showed no similar loss due to the fixed factory density but we know they're a pain to install and never do really perform like other blown products due to truss gaps, etc. So no batts in the attic!!!
The thing is, you hardly ever see (in older homes, at least) fiberglass batts properly installed in an attic or similar situation. Usually just medium density unfaced bats layed loosely between the joists. This may satisfy the inspector and the unsuspecting purchaser that there's insulation, but is almost worthless in practice. High-density FG batts, carefully fitted between the joists and then covered at right angles with another layer of batts, should perform well, though.And in walls, fiberglass doesn't help reduce infiltration like blown cellulose will. This is doubly bad -- reduces the effectiveness of the FG and allows unwanted air exchange.Properly installed as a part of a system, with no gaps (which requires careful installation) and with a good housewrap, properly taped, FG batts can be effective. It's just far less forgiving than blown cellulose.
If Tyranny and Oppression come to this land, it will be in the guise of fighting a foreign enemy. --James Madison
The issue revolves around two factors, the first being the typical poor installation. I've rarely seen batts installed well. Insulators are typically the low bid contractor, and badly installed batts are what you get. It seems that cellulose and foam installers generally understand home performance better, so you get a better installation from these higher end contractors.
The other factor is that fiberglass's performance degrades as the Delta-T increases. When you need it most is when it performs the worst. I'd have to check my sources as I don't remember them, but I'm thinking that's from Oak Ridge National Labs.Andy
"Never try to teach a pig to sing. It wastes your time and annoys the pig." Robert A. Heinlein
"Get off your dead #### and on your dying feet." Mom
Totally out of my League on this one it looks like but I'm going to ask anyway. First what exactly is the difference hot roof vs. Cold roof? I'm guessing Hot roof the roof itself is insulated, cold roof the attic floor is insulated?Reason's I'm even daring to ask is I was going to try some form of insulation in the attic this year. Right now as Andy has said it is probably unfaced fiberglass loosely laid between rafters (ie useless). With the price oil is going we need something. Actually can't see what is there as there is a floor. I'm going to have to rip up in the attic to get at it. I can see insulation at the edges, but there is no ridge vent or soffit vents right now. Just two little windows at each end. Live just North of Boston. So far in 7 years in the house not one Ice dam (yes I know I'm jinxing myself). However I'm sure the heat is just pissing out the roof like nobody's business. No insulation in the walls of this place either (built 1935).Here's the plan so far, try to install some type of soffit vents to the inside attic. Use the foam channels (see don't even know what they're called) to get the air up into the attic past whatever insulation I put in. Install a solar fan on the attic roof to help vent it. Tear up the existing floor. Seal any perforations in the the attic floor/room ceilings with foam. Tricky part is the insulation and new floor. Pull up the existing floor in sections build a new floor on top of it with 2X6 running perpendicular to the existing 24 inches (perhaps less) on center. My guess is this will give me 14 inches of insulation (not sure what that works out to R value wise yet) Take out any existing insulation and blow in dense packed Cellulose into the new space. Re-cover with a new floor of some kind. This hopefully will still give me some storage space up there even loosing the 6+ inches (have no garage and this house is far from a McMansion (maybe 1500 sq. ft). Hopefully not too much new weight with the floor. Don't store anything massive up there.Any references or places to look things up would be great. Plan to start with building science.
Pull up the existing floor in sections build a new floor on top of it with 2X6 running perpendicular to the existing 24 inches (perhaps less) on center.
2x6 @ 24oc?
Get a structural engineer to evaluate it.
You may want to put new 2x6s in the center of the existing joist bays before laying anything on top of it.
> First what exactly is the difference hot roof vs. Cold roof? I'm
> guessing Hot roof the roof itself is insulated, cold roof the attic
> floor is insulated?That's the gist of it. You can, however, have a vaulted ceiling where there's insulation laying in the same plane as the roof, but with a ventillated air channel between insulation and roof. This is still a "cold" roof.
If Tyranny and Oppression come to this land, it will be in the guise of fighting a foreign enemy. --James Madison
Sorry to take so long to reply. I've been off the forums for a time.
Your plan sounds reasonable, but I'd skip the fan. It's not likely to do much good, and may increase air leakage into the attic. Andy
"Never try to teach a pig to sing. It wastes your time and annoys the pig." Robert A. Heinlein
"Get off your dead #### and on your dying feet." Mom
Thanks Andy,So I finally got a piece of the floor up there pulled up (pulled it up to see where the water leaking in around the chimney was going during the 10+ inches of rain we got last week (but that is another thread entirely)). It was a nightmare as the entire floor up there is tongue and groove so ripping it up in sections is going to be a lot harder than I first thought. There is actually a layer of felt/tar paper under it then 6 inches of very old fiberglass (this stuff is very thick and course nothing like todays). Not packed down from the looks of it at all. But not sure if it is any good or not. What do you think should I still rip it all out and fill it with compacted cellulose?Not sure I understand the part about skipping the fan, I thought I wanted the attic to be vented. If I put the soffit vents in won't the fan help move the hot air out of the attic?Another thought I had while up there was a combination hot roof/cold roof combination. The daughters (only 4 and 5.5 now) with the stairway up to the attic have no conceivable closet (they have a stairway to the attic :-) ) in their room so I'm thinking maybe a walk up at the top of the attic stairs, that however would mean insulating the roof itself instead. I guess if I do that I should do it for the whole roof? Decisions, decisions?
Unless you air seal the attic floor very well, and be certain that you've got adequate venting to replace the air the fan sucks out, an attic fan can worsen your energy use by pulling conditioned air from living space to the outside. I generally think they're a bad idea, as I generally think roof venting is highly over-rated.
The insulation you have is probably mineral wool, which works much the same as FG, but it's itchier. I'd still consider dense-pack cellulose on top of it. I wouldn't remove it. I'm a little concerned about the tar paper though. That can work like a vapor barrier, and it's on the cold side. You could very well get condensation there.
How's your basement or crawl? Damp? Bone dry?
Assuming a dry foundation, and the fact that you want to use the space in the attic as closets, I'd seriously consider insulating the roof deck with closed cell foam rather than messing about with the attic floor. It'll cost more up front, but long term it's probably a winner. Again, all of this depends on a dry foundation. Andy
"Never try to teach a pig to sing. It wastes your time and annoys the pig." Robert A. Heinlein
"Get off your dead #### and on your dying feet." Mom
Thanks again. Basement is bone dry (other than condensation, which has been completely taken care of with a dehumidifier the past few years). Curious as to what part that plays?If I go with the closed cell foam I'm only gong to get 6 inches as the house just wasn't built with joists the size they are today. Also what do I do about the thermal bridging of the joists themselves? Would you foam the 6 inches then put an inch of XPS over the joists before the sheetrock? We're not talking about a lot of extra room to play with up there.While I'm on the subject of insulation and roofs. I've complained about the retarded electrician we had (renovation we did a few years ago) plenty of times already on this forum but another mistake he (or we made) with our addition was when he installed the cans in the mudroom he put in non IC cans. The roof directly above the mudroom has soffit vents and a ridge vent so gets good flow but they obviously couldn't insulate over the cans (given the type he put in). Consequently the draft I get through them in the winter is outrageous. Is the only solution cutting them out of the ceiling and replacing them with a sealed can (insulation over the top) and replastering the ceiling?
6 inches of closed cell is pretty good, about an actual R30. One factor to consider is that fiberglass with a nominal, say, R38, doesn't usually perform anywhere near that number due to poor installation and to convective losses at very cold temperatures. So what we think of as normal is really overstated.
If you do closed cell foam, shave it off even with the rafters, and add an inch of rigid foam under it, you've dealt with the thermal bridging, and you've got a system that allthough it doesn't quite reach a nominal r38, will outperform most R38 jobs.
The basement moisture question comes into play because almost every house that has moisture in the attic also has a wet foundation. That's where the attic moisture comes from, drawn upward by the stack effect.
Yes, I think you're stuck re-doing the cans. The question isn't just air sealing the existing ones. That could be done. The trouble is that they rely on being drafty so as not to overheat. Air sealing them would be a fire hazard.Andy
"Never try to teach a pig to sing. It wastes your time and annoys the pig." Robert A. Heinlein
"Get off your dead #### and on your dying feet." Mom
Maybe I didn't read well enough but if he foams the rafters, then he won't need to replace the cans. That is part of the cost justification for the foam.
I thought the cans were in another part of the house? Maybe the rain got in my eyes and I didn't read right <G>Andy
"Never try to teach a pig to sing. It wastes your time and annoys the pig." Robert A. Heinlein
"Get off your dead #### and on your dying feet." Mom
No Andy was right the cans are in another part of the house. They are in the attached mudroom, completely independent of the regular roof where we're considering the sprayed foam in the rafters.Now I need to look at all this hot roof stuff and review all the pros and Cons of the sprayed foam (particularly which one) again.Tom
From EDU/May/1993 article: Fixing Fiberglass Convection Problems with Loose-Fill Cellulose
"Previous testing at ORNL showed that low density (0.5 lbs/cuft) loose-fill fiberglass suffers up to 50% loss of R-value at very cold attic temperatures (-18 F) due to convection within the insulation. However, laying fiberglass batts over the loose-fill effectively stopped the convection problem."
I'll summarize the other fixes:
-2" of blown cellulose prevented convection
-R8 higher density (0.7 lb/cuft) blown fiberglass did not stop convection.
- A researcher expected the 1.0 lb/cuft fiberglass (Owens Corning "Standard Blend") to resist convection since convection depends on the product's air permeability, which is strongly dependent on density. (but they had not tested it for that purpose yet)
Edited 5/12/2006 4:19 pm ET by experienced
My head just exploded...Justin Fink - FHB Editorial
I know the feeling -- Mine did that several years ago when I first started to understand this stuff. Keep reading, and remember that there is no violating the laws of physics.Andy
"Never try to teach a pig to sing. It wastes your time and annoys the pig." Robert A. Heinlein
"Get off your dead #### and on your dying feet." Mom
I understand that it's only one example. If it had been a badly worn roof, I wouldn't have even made a connection with venting. It would have just been an old roof. But I thought it was interesting that on the same roof with the same shingles, applied the same way with the same exposure, that the areas adjacent to the vents were in pretty good shape, whereas those that would have less access to cooler air (middle of the ridge) were deteriorated badly.
Shade could be a factor, too. My ridge runs east - west, and I have tall trees on the gable ends, and an open lawn to the south. So, the east end of the roof gets morning shade, the west end gets afternoon shade, and the middle gets sun almost all day.
Andy
"Never try to teach a pig to sing. It wastes your time and annoys the pig." Robert A. Heinlein
"Get off your dead #### and on your dying feet." Mom
On this particular lot, there weren't enough tall trees to provide any shade. It was several years ago, and I don't recall the orientation of the house in relation to the damaged areas of the shingles, but it was L-shaped, so several roof planes could have pretty dramatic exposure to the sun. There had been several articles on roof venting in FHB and JLC about that time, and I was struck by the deterioration being proportional to the distance from the gable vents.
That does suggest a relationship to venting, but it's only correlation, not proof. I'm still going with the findings of Bill Rose, who's been running controlled experiments for twenty years or so.
One of Bill's points is that if roof venting effectively cools roofs, it can't do so evenly. Here's the thought experiment, with soffit and ridge vents. Cool air is pulled in at the soffits, and as it rises, it cools the roof by picking up heat. Of course, as the air picks up heat on its upward journey, its temperature rises. Because the delta-T (difference in temperature) shrinks as the air rises, it can't cool the upper regions of the roof as well as the lower, and may in fact warm to the point where it's heating the upper roof. Now, I can't spot the flaw in that reasoning. And it begs the question of why, then, if venting actually cools roofs, don't they deteriorate more quickly at the top than at the bottom?Andy
"Never try to teach a pig to sing. It wastes your time and annoys the pig." Robert A. Heinlein
"Get off your dead #### and on your dying feet." Mom
Hi Andy:
Just sorting out training materials and found some copies of EDU/JLC articles on roof venting with comments from Bill Rose. Here goes with a few excerpts:
EDU/ January/1993:
The Mysterious Origins of The "1:300" Rule
"Surely these recommendations are based on careful testing of homes or simulated attics under various weather conditions. Not so, says Bill Rose, research architect at the Building Research Council of the U. of Illinois. After an extensive search for the roots of the "1:300" rule, Rose found that it was hastily derived from a single lab experiment on a flat roof 45 (now 58) years ago."
"Each of the panels had a 5/8" slot at each end. The roof to vent ratio, 1:300, appears to be merely an incidental detail," says Rose, "peculiar to the specific test setup."
JLC/August/1998: "On The House" Q&A section:
Q: "Is it necessary to provide ventilation under shingles installed over SIP roofs? I've heard that shingles installed directly over SIP's wil fail prematurely."
A: (excerpts)
"In fact, our measurements indicate that the top of the vented slot is at about the same temperature as an unvented cavity."
"We've also found that the top of a vented cathedral ceiling cavity is much hotter than an unvented full attic, all things being equal. In addition, our research shows that some ridge vents are so well designed to exclude snow that air barely moves through them.
So far I find little technical support for the claim that ventilation enhances shingle life. One argument- that higher temperatures cause faster diffusion of the compounds that keep shingles pliable - makes sense but the temperature differnce between vented and unvented is awfully tiny. Shingle colour and latitude make for a much greater temperature difference."
"Venting has been presented as the key to blissful service life of shingles. My opinion is that service life is first and formost a matter of shingle quality. If ventilation has one ill effect, it is that it gives shelter to manufacturers who are not investing in product improvement" -END-
I believe he's asserting that the nature of the roof insulation/ventillation has little to do with shingle life. I'm inclined to agree, so long as there are no secondary effects (eg, rot due to moisture buildup) that affect the sheathing.
If Tyranny and Oppression come to this land, it will be in the guise of fighting a foreign enemy. --James Madison
Huck:
I should read and edit my posts or.......stop posting late at night!!!!! Should have read:
"If no attic ventilation severely decreased shingle life......."
Sorry
XPD
Woodroe mentioned about building the best with the current knowledge we have........good idea but......most contractors don't seem to want keep up, retrain, buy code books,etc, etc etc.
A RANT!!!!!
The first written reference I have to sealing vapour barriers and avoiding making holes at all cost was in a free 1960 Building Digest from the Division of Building Research (DBR) of the National Research Council (NRC) of the Canada. The last two lines about VB's: "The most important general principle to be followed in both design and installation is to reduce to a minimum the number of openings in the barrier. Where such openings are necessary, special care should be taken to seal the barrier so as to approach complete continuity." The author of this digest (Gus Handegord) was/is a mentor to Joe Lstiburek!! For the rest of the digests go to:
http://irc.nrc-cnrc.gc.ca/pubs/cbd/index_e.html
For a little shocking reading, go to the formost energy newsletter in NA:
http://www.1800arkansas.com//energy/files/clearinghouse/Ordinary%20Paint%20as%20Replacement%20for%20Poly%20Vapor%20Retarder.pdf
In 1953 (hell,I was 3), a talk was given in the city nearest me (Halifax) by the head of DBR speaking of the merits of air leakage and movement on comfort, moisture, space conditioning, building deterioration ("Fundamental considerations in the design of exterior walls for buildings," 67th Annual General and Professional Meeting of The Engineering Institute of Canada (Halifax, Nova Scotia, 5/1/1953), pp. 25, May 01, 1953) We have these folks (building scientists) whose life it is is to research our failures. When they suggest something a bit out of line or different, we toss them and wonder when we fail again!!! So let's learn the building science and really know why we are making certain decisions.
It should be mandatory that licensed GC's and carpenters be required to retrain at least every 5 years. We have that up here in the wood heating industry through a private association called Wood Energy Technology Transfer (WETT). Insurance co's want all wood heating systems installed or inspected by WETT certified persons. To maintain your WETT status, dues is required every year ($75-$100) and a "New & Review" course must be taken at your own expense every 5 years. Works well.....not WETT certified.....work drops off severely.....and the gov. is not involved except to verbally support the system!!
We should not have made all the mistakes regarding tight buildings, moisture in attics, mould problems, rotting walls, etc, etc, that the first energy crunch brought on......it was pretty well all in books that no one wanted to read!!!
Re-train; learn; re-train; learn
END of RANT
I'm with you on this one. Insulate the snot out of it with cells and don't worry about the vents
Welcome to the Taunton University of Knowledge FHB Campus at Breaktime. where ... Excellence is its own reward!
OK, I can't resist. Southern Sawdust has a home built in 1970. It is going to be very difficult if not impossible to do a complete air seal job. He should vent his attic, eaves and a ridge vent.
As far as political affiliation, where would these neo-cons we hear about be on the scale?
I don't care what kind of insulation or venting you have in your attic. If your house has an attic and an eave you're going to develop an ice dam if conditions are right. Those conditions being alot of snow on the roof and long term snow cover an sub freezing temperatures, (Like we get in Minnesota.) The more poorly insulated and vented the attic, the more severe the problem. Snow melts in the sun (or from heat below) , runs to the shingles, down the roof to the eave edge where it freezes when it's exposed to colder air, causing the ice dam. I chose to say melts in the sun because it is a condition in which that ventilation has little bearing. Roof ventilation will make a difference here though, preventing ice dams in most years.
Finally, we do alot of "hot roofs" here too. Almost always spraying a couple of inches of urethane foam into rarter bays first to air seal the roof (and cause the roof's dew point to occur within the foam), followed by blown in insulation. (These would be roofs that have no attic space.)
All this is in a "cold climate" condition. As we are seeing now, vapor barriers are not always on the inside of the house. We know a whole lot more about vapor pressure and air movement. Building science and methods are (and always have been) changing. Anyone in remodeling can date a house within 10 years by looking at what is inside of a wall. Somethines I think we should all be saying what is true (I hope); that we're building the best product we can with our current understanding of building science (and codes which don't always agree).
Sorry, I didn't intend to run on so much.