*
The cover photo of the January issue of FHB show concrete being placed into foundation wall forms. The article starting on page 64 talks about setting up foundation walls. I don’t see any re-bar dowels sticking out of the footers. There doesn’t appear to be any re-bar in the walls. Doesn’t Rhode Island require any reinforcing steel in foundation walls?
Out here in Utah, we are in a seismic zone 3. We have to put in bent leg dowels at 24″ oc out of the footers. Plus #4 bar at 24″ oc both horizontally and vertically thruought the wall.
The J-bolts have to hook under the top most horizontal bars which are doubled #5 bar. Anchor bolt spacing has to 32″ oc.
What building code prevails along the Eastern seaboard?
Any comments on how others do foundation walls are welcome.
Elwood, Layton, Utah
Discussion Forum
Discussion Forum
Up Next
Video Shorts
Featured Story
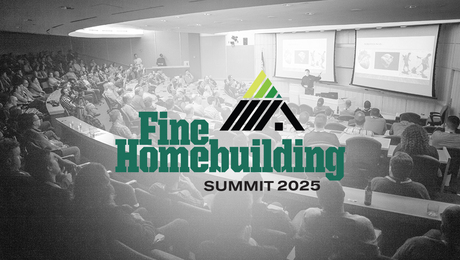
Join some of the most experienced and recognized building professionals for two days of presentations, panel discussions, networking, and more.
Featured Video
Video: Build a Fireplace, Brick by BrickHighlights
"I have learned so much thanks to the searchable articles on the FHB website. I can confidently say that I expect to be a life-long subscriber." - M.K.
Fine Homebuilding Magazine
- Home Group
- Antique Trader
- Arts & Crafts Homes
- Bank Note Reporter
- Cabin Life
- Cuisine at Home
- Fine Gardening
- Fine Woodworking
- Green Building Advisor
- Garden Gate
- Horticulture
- Keep Craft Alive
- Log Home Living
- Military Trader/Vehicles
- Numismatic News
- Numismaster
- Old Cars Weekly
- Old House Journal
- Period Homes
- Popular Woodworking
- Script
- ShopNotes
- Sports Collectors Digest
- Threads
- Timber Home Living
- Traditional Building
- Woodsmith
- World Coin News
- Writer's Digest
Replies
*
I noticed that as well !
But what does it mean?
*I think what it means is that there are different interpretations of code throughout the US. The issue before dealt with footers and the way they did them for the article was way different than what our building inspector wants to see. Our rebar must be tied and in place before concrete placement. The ICBO, BOCA etc. set down the guidelines that are supposed to be followed by all but different regions take it upon themselves to do what is best suited to their needs. We don't do much for earthquake and hurricane measures here in the Rockies but people in Florida don't go down 36" for their footers to prevent frost intrusion either. Publications like Fine Homebuilding I feel do the best they can to cover the basics of construction methods and issues but will always fall short of making everyone happy.
*The 1975 edition of the Ontario Building Code I have (I'm not a builder, but I see no reason why things should change) says plain unreinforced concrete 10" thick and a compressive strength of 2000 psi or more is acceptable for basement walls up to 7'6" below grade in residential construction. If 3000 psi concrete is used, 8" walls are good enough. Of course, local codes may vary.Full basements are common here because of the depth of frost penetration, even in thumbtacks and chewing gum subdivisions. Locally (SW Ontario), 3' is average in an average winter. 6' should cover just about the coldest winter. By that time, one might just as well clean the dirt out between the foundation walls, install a floor, and voila! A full basement.
*
It would be my hope that building inspectors from all over not wait for problems in the area before beginning consideration as to whether or not to consider changing something that may or may not happen in a given time period.
Frankly, I am tired of the bullshit.
Every time a disaster strikes, most are surprised. Why? Where is the surprise?
There should be no surprises in home construction.
There are other pressures on a basement wall that would cause one to , rightfully so, consider the re-bar with more value than the cost at that point.
It is my wish that a task force be created or found for purpose of bridging these types of issues. I think FEMA at http://www.fema.gov is a good place to start. They have plenty of useful information that is free of charge.
Hope this helps.
*Elwood,I had a small hand in authoring the Foundations article though Rick is the expert. Here in RI we follow CABO 1995 for 1 and 2 family. There are no rebar requirements unless soil conditions warrant a note from the building official. We certianly don't skimp on our foundations though it may seem so from your point of view. I've travelled throughout the US and it's amazing how differently things are done throughout the construction of a home. Just this weekend I hiked through the local forests and by several homes build on rubble stone foundations still standing after 260 years. Certainly rebar adds to the rigidity of a foundation but we generally pour 12" 2500# mix - which on good soils is overkill in it's own right. The foundations Rick likes to pour the most are set on 2'wide x1'thick footings (see previous issue of FHB). Those have rebar in them. There are no rebar verts connecting the foundation to the footing because we are generally concerned about lateral movement between footing and foundation. There is a keyway embossed in the footing to preform the duty. I do believe Rick wrote a page or two on rebar in footings and foundations but as is usually the case we write too much and our editors at FHB chop out the least important information (if you could consider rebar least impt.). One thing to consider that I've been wrestling with for a few years in an effort to be more resource efficient (as well as energy efficient) when building new homes is how much material do we really need to build into a home to be sure it will preform for a long long time. Rebar? code may require it in some regions and many builders will swear by it but i is it necessary?
*I am building a house in Stafford County, VA and the basement walls are 9' poured concrete. The locals follow CABO and they required rebar every 2' sticking out of the footers. But they required no rebar lengthwise in the footers ( 24" x 8" ). The poured walls varied between 6" and 10" depending on brick application. There is also rebar in the walls that was tied to the pieces sticking out of the footers, but I am unsure of the spacing. If the walls were only 8' tall, the foundation people were only going to put the verticals every 4'.Another detail that has changed this year, the sill plates must be drilled and placed over the twin ties instead of the old method of bending the ties out, around and over the sill plates. Now the foundation people need to get the ties very close to the center of the sill location. The crew I hired now just uses anchor bolts instead of the split tie.
*Please don't wish for the federal government to get involved in building regulation. Everytime the feds have done so its been a disaster! The building code system in this country is the envy of the world and works very well.
*Here in Boise, Idaho they (the code writers) removed the rebar requirement a few years ago for residential foundations. The arguement was that it was not necessary. From a purely strength point of view, that is true. Residential construction does not impose the kinds of loads that will cause normal strength concrete to fail. I read in one of the many books I collected as part of my house project, that if concrete fails in a residential environment, it is the result of improper placing or mixing of the concrete and not the lack of strength of the concrete itself. The fact that many builders in this area will pour one day and strip the forms the next in the middle of summer, would seem to support this observation, as foundation failures are pretty rare here. Concrete normally needs 28 days to reach full strength. To cure, it needs to stay moist. Stripping the forms off allows the moisture to evaporate which aborts the curing process. Based on the curing rate charts, you need to keep it wet for at least 3 days to get something like half of the expected strength. 24 hours gets only a small fraction of the total strength. Admittedly the interior part of the foundation stays moist and continues to cure even if the outside is dry but the early removal of the forms precludes obtaining the full strength of the concrete structure. Even if your house design doesn't require rebar in the concrete, for just a small increas in cost, you can greatly increase the crack resistance of a foundation. I choose to put it in just for that purpose and it made me feel a whole lot better about the job.Just my 2% of a dollar.
*
Down here in Baltimore we follow BOCA for the most part with some modifications as I am informed by our county inspector. We have a two bar requirement laid horizontaly, separated by 4" and placed at every 4' of vertical height of wall. Also there must be two bars set 4" down from the top of the wall regardless of heighth. In addition there has to be two bars across all cast openings for doors and windows. All of this can be totaly left out if the contractor uses Fiber Reinforced Concrete. There has been extensive use and testing of this product in Baltimore and it has proven to be equally as strong as a fully reinforced wall.
*
Mike,
Here in Calif. where unreinforced concrete or masonry is unheard of today, I have seen stone rubble foundations, too. What I have never seen, and you probably haven't either is all the foundations that collapsed 200, 100 or even 50 years ago. Just because something has worked in a few instances for 260 years does not mean that it will ALWAYS work, even for 1 year. We only see succcesses; the failures are long gone. Anecdotal evidence is not always reliable.
I have seen unreinforced concrete fail, and I have seen unreinforced concrete that has not yet failed, but I can't say that I have seen unreinforced concrete that will not fail. Neither can I say that I have seen reinforced concrete that will not fail, but I think it is far less likely.
*
One of my projects unfortunatly, was torn down this spring. A historic register listed mission-style hotel in Patterson, California. Built about 1907. A fire in a basement caused by a propane torch left standing on a workbench a foot or so from woodwork. An abandoned walled-off stairway, and lack of attic draft stops helped spread the fire slowly throughout the attic.
7'-2" high partial basement with 10" concrete unreinforced concrete walls 6' high. If I remember correctly, broken concrete cracked through the granite gravel aggregate, not around it, so the strength of the material was probably fairly good. Portions of the basement were already starting to crack and fail due to the expansive clay soil.
The city was considering converting it into a City Hall, but due to the loss of the roof, el Nino water damage, mold growth, handicapped access and required foundation repair, the costs were estimated by another architect to be higher than building from scratch and the building was demolished. They didn't have too much trouble demolishing the concrete.
While rusting rebar can cause blow-out of concrete eventually, lack of any reinforcement is very poor practice in my opinion.
*I'll have to forget writing my name as Gary Wheeler, AIA, as the program deletes the comma, and puts the AIA at the front of my name!
*
I think that the re- bar issue is missing a point. How about "side loads" from fill and big equiment back filling? How about five years down the road when the drain pipe is filled with ivy roots and all that water from a big rain sets againest that wall? I don't think that just following the code is a bail out for a contractor to over look site problems. Thats one of the resons that the code is so confusing to people. Here I work in three differant areas and all three are as differant as night and day. I long for the day when all codes are even in areas. (It's a given that costal area's and earthquake areas are differant) I see houses that are 5 years old with failing roof systems, septics that don't work, and rot in areas that shouldn't have this problem.(windows, doors ect...ect) I don't thing that missing the rebar is the point. It's that everthing is differant and by only my providing work and workmanship that adresses these problems on the long term can we stop being "coded to death" sorry to carry on but I as a builder am tired of having to make excuses about my follow builders
*Okay, Bill.Thanks for the laugh. It caused me to think of election time. There was this guy who prefaced his comments/questions to the candidates with..."imagine that you (the government) are the parent and we (the citizens) are the children"...And when Mike Dukakis was running, and had that trouble with the furlough program...they had these guys in prison-stripes holding signs that said..."murderers for Mike!"....But honestly, that James Lee Witt is doing an excellent job with FEMA!Really! Just go take a look at http://www.fema.gov.Hope this helps.
*
Worked for a concrete contractor in Oregon last year and we sprayed form release oil on the forms away from the footing before setting the forms. This was to prevent getting the oil on the footing and any verts protruding from the footing,
allowing better adhesion of the concrete to the footer and the rebar verts.
*
The cover photo of the January issue of FHB show concrete being placed into foundation wall forms. The article starting on page 64 talks about setting up foundation walls. I don't see any re-bar dowels sticking out of the footers. There doesn't appear to be any re-bar in the walls. Doesn't Rhode Island require any reinforcing steel in foundation walls?
Out here in Utah, we are in a seismic zone 3. We have to put in bent leg dowels at 24" oc out of the footers. Plus #4 bar at 24" oc both horizontally and vertically thruought the wall.
The J-bolts have to hook under the top most horizontal bars which are doubled #5 bar. Anchor bolt spacing has to 32" oc.
What building code prevails along the Eastern seaboard?
Any comments on how others do foundation walls are welcome.
Elwood, Layton, Utah