What size is your male connector…
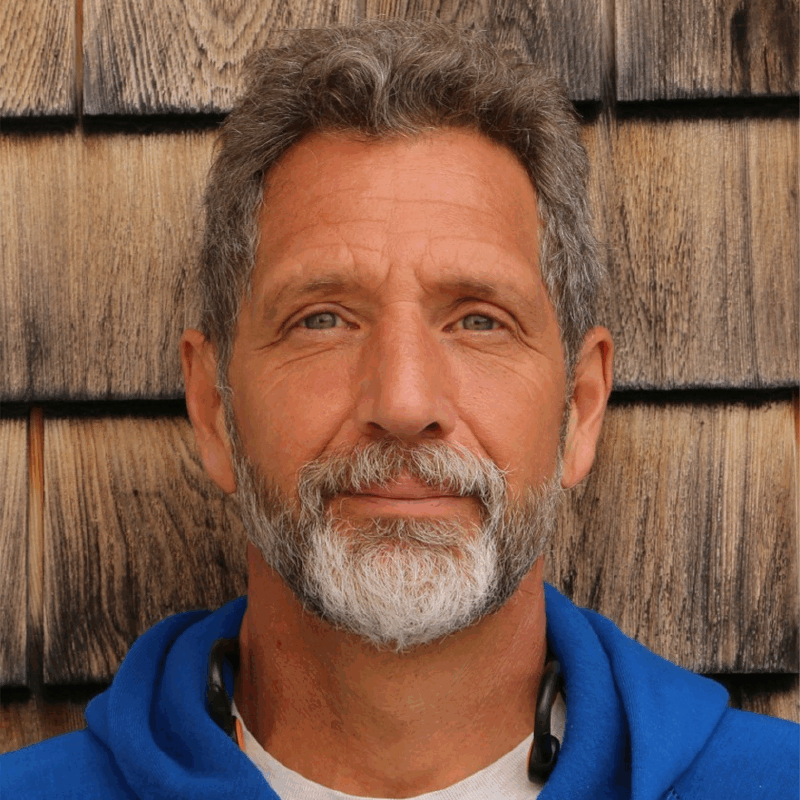
..on your framing nailers? Sorry, I just couldn’t resist. Do you use 1/4″ or 3/8″ fittings? Talking with a very old pneumatic tool repair guy a few days ago. He was a wealth of knowledge about tool care. He said that one thing that kills nailers is the fittings we use. The 1/4″ fittings or automotive fittings cause a restriction – we run our compressors at a slightly higher pressure and blow rings, bumpers, drivers and so forth. He says to only use 3/8″ fittings, shortest hose lengths and set an output no higher than 100 psi. I never gave a second thought to 100psi vs 120 psi but he pointed out that as a percentage – it’s a lot. Kind of like high blood pressure. What do you think? MG
Replies
I can understand the 100psi restriction because of the higher pressure wear and tear on the rings, bumpers and piston. I don't see what difference the length of hose should make, or the 1/4" to 3/8" should make. Once the chamber is filled with air, it's filled to the same capacity regardless of the length of hose or the milisecond faster or slower the air takes to get into the chamber.
That's what I said. His answer: If you have long hoses and/or 1/4" fittings and run your tools at 100 psi you will have plenty of pressure for intermittant nailing. However, if you are bump firing (sheathing or spiking a beam together) not enough air will flow fast enough into the 'plenum' of the nailer to recharge it up to full pressure for the next cycle. Figuring you can shoot off 3 - 6 nails per second, there's no way the air will refill. So what do you do? Turn up the regulator. Then you overstress the nailer's guts when you are intermittant firing. He says there's been testing on this that proves it out. Makes logical sense to me in any event. MG
I have a buddy that worked for a transport truck outfit and he gave me a whack of fittings that they used in their big shop. He said if I was ever working with him then I could run off his compressor. Now that you explain what your guy says I think it will be worth trying out his theory.
Have a good day
Cliffy
I don't see how the fitting is going to matter very much. Auto tools like grinders and impact wrenches use much more air than a nail gun and it doesn't restrict the air to those tools. I do think the air lines matter though. If it only 25 or 50 feet than a 1/4" air line is fine but anything more than that I go up to 3/8". Over the long distances, its not the psi, it the volume. It's similar to how plumbing and duct work are run. The beginning of the plumbing might be 1 1/4" but as you pass fixtures then you drop down in size. The water pressure is always the same but you need the volume (and that need is reduced as you go down the line.) AC and Heating ducts are the same, you'll the trunk run from the air handler at a large size and taper it down as you move down the house.
I run a large line from the compressor to a 1 to 4 split then run the regular air lines to each gun.
Mike, I think it's safe to agree that higher PSI will wear down all of the gun components faster than lower PSI.
The question then becomes, what is the best means for recovery? You're running a higher PSI that forces the air through faster, and he's advocating something different.
The problem I have with 3/8" fittings is their girth and weight. I'd rather blow the guns apart and have a lighter, more managable tool to wield. Of course, I am fortunate because I get all my guns repaired free forever, unless we blow it into smithereens by shattering it from a 50' drop or running it over with the skytrak.
We do experience slower recovery when we run a 100' lead (1/4") and hook a 1/4" 100 onto that too. But, it doesn't take up that much more time to simply control the rate of nailing or stapling. My feelings on the issue is that there is an optimum safe speed that the guys should use. I don't like to hear anyone doing the machine gun staple thing, because I've sent the guys off to see the doctor to get the fasteners out of their feet.
I'd advocate a holding tank, at the junction if air supply is an issue. From the junction, 1/4" hose would be sufficient. Weve done variations of this on occasion.
blue
Just because you can, doesn't mean you should!
Warning! Be cautious when taking any framing advice from me. There are some in here who think I'm a hackmeister...they might be right! Of course, they might be wrong too!
> I'd advocate a holding tank, at the junction if air supply is an issue.
A friend of mine made one out of an old propane tank, a 40 lb IIRC.
-- J.S.
Mike,
The old guy is right. My best buddy was the Bostich factory rep for northern New England in the late 60's early '70's. He was always whinning about the pallet manufacturers changing out the fittings and blowing out the seals. He used to repair guns at one place on a weekly basis because they refused to use 3/8 fittings. Since he made most of his money on commission, he had to put up with it since that one outfit bought nails, literally, by the rail car load.
However, like the pallet guys, I removed the 3/8 fittings from all the guns I bought from him and used 1/4. The big gun won't sink a 20d common with a 1/4 fitting though. Course I had, and still have, a lifetime supply of spare parts (along with an excellent repair man).
Holding tanks only work provided the restriction downstream (the 1/4" fitting) will allow a fast enough flow to do the job. Below are a couple pics illustrating.
In the picture below, unregulated shop air (100-130psi) flows through the red hose then through the blue washing machine solenoid and into the old thomas compressor tank via the orange hose when the pressure drops below 25psi in the tank. It fills the tank to only 40psi then shuts off the air flow.
View Image
When a collet, holding a 5/16 round x 12 foot long bar of stainless steel opens, a solenoid operated poppet valve with a huge flow capacity (hidden from view by the steel plate) is opened it allows air to rush out of the compressor tank, though the 1/2" black pipe, the 5/8 heater hose and into the bottoom of the 12' long 1 1/2" black pipe.
The pressure inside the big pipe shoots the stainless bar out through the collet to a stop.
I could hardly get the bar to move at all using 120 psi and a small valve, yet it moves so fast at 20-40psi that I cannot see it moving. The bar is really nothing but a giant nail. But the worst restriction in this instance is the 1/2" restriction of the black pipe sticking up out of the compressor tank.
View Image
Jim
Edited 3/5/2005 1:19 am ET by [email protected]
Thanks, you've convinced me to change to 3/8".
-- J.S.
I've heard that using the larger 3/8 fitting and hoses provides twice the air to the gun. Makes sense to me, I save the 1/4 fittings for the trim guns.
My old Bostitch coil nailer came with a 3/8 on it. Since that was the first gun I bought, I rigged up all my hoses and the compressor to it. And then most all the other guns and air toolers got the same connectors so I wouldn't have to futz around trying to match things. But my little trim guns have the 1/4; I keep a step-down connector or two around for using them. I just have to remember to bring it along.
Strangely I just got a used Blue Point impact wrench and it came with a 1/4 connector. I would have thought it would have required a 3/8 to move enough air. I'll swap the 1/4 for a 3/8 one of these days when things slow down. I used it yesterday afternoon briefly; it worked ok.
impacts will work fine with 1/4" fittings but you need a 3/8" hose feeding the gun. Every auto garage and body shop you go to will have 1/4" fittings but the 3/8" hose. The problem with air flow isn't the 1" of the 1/4" fitting it is the 50' or whatever of 1/4" hose. Put the psi at 90 to 100 and use a 3/8 hose and that impact will work as it should.
3/8" fitting are really only necessary in commerical applications for large air powered equipment. No nail gun or impact wrench, grinder, etc needs more than 1/4" fittings as long a the runs are under 50 ft and they use 3/8" air hose.
DDay,
Try pumbing air through a basketball filling needle, then unscrewing the needle and pumping air.
jim
Nailers just don't need that much air though. The 1/4" is fine as long as you have the volume behind it. The 3/8" hose provides the volume. An Ingersoll Rand or Snap On impact wrench uses at least twice the air per second than a framing nailer and every garage runs 3/8" air hoses and 1/4" fittings. The piping from the compressor throughout the building is probably 1 1/2" or 2" copper for the volume. You don't need the 3/8" fitting until you go up to something that devours air, something like a sandblaster.
Thanks DDay, I wondered about the automotive tools. Since I'm all set up with 3/8 hoses and fittings except on the little trim nailers, I'll stay with what I've got. The big pain was when I was getting started, it took 3 trips to the store to get all the right connectors to match. (Now it usually only takes me 2 trips.)
Dusty and Lefty and Forgetful