Yesterday I got screwed again by Tapcons the “concrete” screw! I used the correct Tapcon drill bit in a correct hammer drill to drill the pilot hole. No problem there, then I blew the hole out with compressed air, then I vacuumed out the hole! I inserted the proper size tapcon screw, then proceeded to drive the screw in using a proper size #3 philips tip in a slow speed set drill and voila: the screw broke off midway into the hole, leaving the screw partial screwed in and leaving me completely screwed. I couldn’t back the broken off shank out so here I am. I hate Tapcon screws next time I’ll drill a larger hole and drive a wooden dowel into the concrete first then use a regular wood screw. These things suck!
Discussion Forum
Discussion Forum
Up Next
Video Shorts
Featured Story
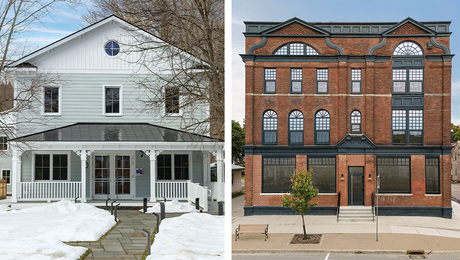
A high-performance single-family home builder shares tips from his early experience with two apartment buildings.
Featured Video
Builder’s Advocate: An Interview With ViewrailHighlights
"I have learned so much thanks to the searchable articles on the FHB website. I can confidently say that I expect to be a life-long subscriber." - M.K.
Fine Homebuilding Magazine
- Home Group
- Antique Trader
- Arts & Crafts Homes
- Bank Note Reporter
- Cabin Life
- Cuisine at Home
- Fine Gardening
- Fine Woodworking
- Green Building Advisor
- Garden Gate
- Horticulture
- Keep Craft Alive
- Log Home Living
- Military Trader/Vehicles
- Numismatic News
- Numismaster
- Old Cars Weekly
- Old House Journal
- Period Homes
- Popular Woodworking
- Script
- ShopNotes
- Sports Collectors Digest
- Threads
- Timber Home Living
- Traditional Building
- Woodsmith
- World Coin News
- Writer's Digest
Replies
I haven't used Tapcons much, but I read a tip here to make the hole quite a bit deeper than the screw to give the dust someplace to fall into. It makes sense because it doesn't seem like a vacuum would very easily remove dust from such a small hole.
But rather than dowels, if you decide to avoid Tapcons, I often use plastic anchors (solid wall anchors by Toggler). They work well.
-Don
Man, I'm glad that's never happened to me. :>)
I don't know what else to tell you. You took every single precaution I could imagine. Even vacuuming! Sometimes I've had problems putting in sleeve anchors or Tapcons if I tried to drill too fast. But it seems I would be remiss if I accused you of that.
What did you do? Just last week I had to put one at a slight angle next to one I had broken off, in a threshold no less. Luckily you couldn't tell. Most manufacturers require at least 2 Tapcons in a threshold for the hurricanes here.
We drive several hundred Tapcons on each basement we finish. We break maybe 1 per hundred.
As mentioned, the deeper hole helps...we never vacuum.
In this pic, there is a Tapcon every 2' in each furring strip (only look at one pic--they are all the same--didn't seem to be loading...so I kept clicking "upload."
Basswood, I use them the same way and have experienced very few snaps. Sometimes they strip out if I hit a dense patch, or a piece of rod.
Hillman fastener company makes a knock-off, that I see in every Lumber yard. They are the worst performing "Tapcon" like fastener. I would say that 30 out of every 100 strip out. Fastener Master makes an excellent " Tapcon " like product IMHO.
Change your bits often. If you start hitting hard spots, stick it in a tube of PC wax or what have you to reduce the drive friction. I also believe there is a benefit to drilling a slightly larger hole in the material you are fastening to the concrete. Just a theory, but, I believe the blue coating is more likely to get worn going through the material before it hits the concrete.
In addition to the other tips,
Stay away from the screw driver heads and go with the nut driver heads
Fighting Ignorance since 1967
It's taking way longer than we thought
good advice.
Don't use 2 nails. Instead, use a piece of bailing wire and a 16d nail (for a 3/16ths rotohammer bit, I think.) As fast as Tapcons, far cheaper, and hold much better. Learned this from the company that did my foundation replacement. I've had the same problems with Tapcons breaking...
explain to me what yur gonna do when the nail and / or bailing wire rusts out...
not a good move...
gravity won't do a damn thing for you against shear...Life is not a journey to the grave with the intention of arriving safely in a pretty and well preserved body, but rather to skid in broadside, thoroughly used up, totally worn out, and loudly proclaiming<!----><!----><!---->
WOW!!! What a Ride!<!----><!---->
Forget the primal scream, just ROAR!!!
Anyone ever use Con-serts? I've had pretty good luck with the hex-headed ones. They take a 5/32 bit. Like the others said, drill extra deep. They work well with an impact driver.
Mike
the square drive Tapcons from McFeeley's work well
Recently had an opportunity to try a bit of advice given thru BT or the mag somewhere in the past by somebody.
Involved tieing a base plate to a concrete floor.
Fella said instead of Tapcons he had drilled the hole and hammered in two nails side by side thru the plate and into the hole.
Don't try it unless you plan a permanent fixture because that sucker sure isn't going anywhere.
be immovable
'Nemo me impune lacesset'
No one will provoke me with impunity
Edited 3/28/2006 7:49 am ET by razzman
I remember the advice about the 2 nails in a hole, but don't recall the hole size that ws suggested.Anybody ???
Those prizes in Cracker Jacks are a joke. I once got a magnifying glass. It was so poorly made, ants were laughing at it.
dang boss, don't make me think, I'm no good at it.
let me see, normal size tapcon drillbit was probably for the 1/4" Tapcon and a framing sinker with a smaller penny run alongside seems what I did.
be but it's been so many years ago sometimes I'm still thinking funny
'Nemo me impune lacesset'No one will provoke me with impunity
I use 1/4" hole and three 16 penny, hold - start - and drive all three at once.Remodeling Contractor just on the other side of the Glass City
till it orodes away...
be slip sliding away Life is not a journey to the grave with the intention of arriving safely in a pretty and well preserved body, but rather to skid in broadside, thoroughly used up, totally worn out, and loudly proclaiming<!----><!----><!---->
WOW!!! What a Ride!<!----><!---->
Forget the primal scream, just ROAR!!!
We use a lot of tapcons for our copper downspout attaching straps, they HAVE to be strong else the crackheads steal the downspouts and sell for scrap...so, if by some stoke o' genius we are out of them, we snip a sliver of copper about a 1/16th wide and 3'' long. Fold in half and bend out two 1/4" 'ears' and then insert that onto the hole.
Like the feathers, in a feather and wedge for splitting stone, it can allow a deck screw to be used in Limestone or brick just dandy.
Be it works so good we hardly use tapcons anymore
Spheramid Enterprises Architectural Woodworks
" Iam not a poet, but your hat is singularily inadequate"
That might'a been me, Razz.We call 'em Texas Ties. Drill a 1/4" hole, drive two sinkers in together. Usually the board will break before the nails let go.The best politics is right action. -Mohandas K. Gandhi (1869-1948)
Right action
is cest bon
to all
that survive
with
or without
adornment.
Spheramid Enterprises Architectural Woodworks
" Iam not a poet, but your hat is singularily inadequate"
Beautiful. Thank you.The best politics is right action. -Mohandas K. Gandhi (1869-1948)
Interesting. I've used hundreds of them and never broken a one. Usually, though, I'm using McFeely's version of them. Also, I install them using an impact driver. I've broken some screw tips, but not a screw. Sorry for your bad luck.
Andy
"Never try to teach a pig to sing. It wastes your time and annoys the pig." Robert A. Heinlein
"Get off your dead #### and on your dying feet." Mom
They can be temperamental if you're not used to working with them. I stick with the nut driver heads, and try to avoid the 3/16" diameter. I try to use 1/4" for everything.
Speak the truth, or make your peace some other way.
HMMM...never had that problem.
I just drove a few of them this weekend...didn't even clean out the hole. I did drill about a 1/4" deeper.
I drove the screw in at high speed...I am thinking that maybe the slower speed is allowing the screw to build up more torsional resistance, hence your failure. Try it at a higher drive speed.
It sounds like you have the problem often which would rule out a bad lot or screw. It sounds like your technique of driving the screw at slow speeds is the culprit.
i've driven a lot of these, many 3 1/2". and the extra deep hole helps. also if you nick rebar, you're screwed, start another hole. if you back out the tapcon and it's shiny along the threads, then you're up against rebar.
Been there.
One thing that helps is to put wax on the threads. Requires less torque, so they are less likely to break.
I use toilet bowl wax.
I use a 18v Bosch hammer drill for that install, what I like to do is put it in low range to drive the screw but still in hammer mode. The effect is like a impact driver. Here is some info on sizing, if your using to long a screw it can be a problem.
Tapcon¯ Concrete Screw -
Screw Length:
We drive hundreds of Tapcons. 3/16" Tapcons snap very easily. We drive 1/4" with 14.4 V Boach battery impact drivers and rarely break them.
After using thousands of Tapcons I have never had your prob. Are you sure they are not a generic brand? As long as you use their instructions you should not have a prob.
I think the 'tapcons' available here are generic, and they suck. Doesn't matter how deep you drill, or what size, if the threads can engage then the screw will either break or strip out. I always use split anchors and think they work great... always go in, never bend, impossible to remove.
http://www.simpsonanchors.com/catalog/mechanical/split-drive/index.html
I agree. I don't know why anyone would use a tapcon. If you have a good concrete mix, you can forget about them going in.
The anchors you showed are terrific. Much cheaper, faster, and always work. They also hold much better than a tapcon. I keep a big selection in my truck at all times!
If they're generic they're not TAPCON -stear clear.
Thanks for that link. I hate Tapcons too, have broken about one in three, even drilling extra deep and carefully cleaning the hole. I put five in for a door threshold in my basement and broke one off, the concrete mix was set up for six months and originally specced at 4500 psi. This was even using the 1/4" anchors and an impact driver. Expansion anchors or plastic anchors are much better.
I have been using Phillips KwikTaps.http://www.phillipsii.com/kwiktap.htmThey have a modified phillips head and come with the bit. I really like them and the bit does not slip and I don't think that I have had one break since switching from Tapcons.Locally Lowes stocks both the Tapcons and the KwikTpas.
quit using the Tapcon drill bits...
prep the hole like you have...
drill the hole deeper than you need it....
use a bit matched to the material you are fastening to...
sink the Tapcon using the hammer mode and do it with gusto...
fergit slow speed..
Life is not a journey to the grave with the intention of arriving safely in a pretty and well preserved body, but rather to skid in broadside, thoroughly used up, totally worn out, and loudly proclaiming
WOW!!! What a Ride!
Forget the primal scream, just ROAR!!!
Edited 3/28/2006 12:46 pm by IMERC
IMERC- you need to squirt some graphite on yer tapcons.
be gaffing graph
'Nemo me impune lacesset'No one will provoke me with impunity
mail me yur tube of grap...... er ...... tooth paste... will ya....
Life is not a journey to the grave with the intention of arriving safely in a pretty and well preserved body, but rather to skid in broadside, thoroughly used up, totally worn out, and loudly proclaiming<!----><!----><!---->
WOW!!! What a Ride!<!----><!---->
Forget the primal scream, just ROAR!!!
sounds like a lot of operator problems here... and the screw takin' the heat...Life is not a journey to the grave with the intention of arriving safely in a pretty and well preserved body, but rather to skid in broadside, thoroughly used up, totally worn out, and loudly proclaiming<!----><!----><!---->
WOW!!! What a Ride!<!----><!---->
Forget the primal scream, just ROAR!!!
I see absolutely no reason to use Tapcons. They take too long to install, cost too much money, and their holding power can't compete with expansion style anchors. The only benefit is that they are removable. But when do you ever need to remove a concrete anchor?--Andy
<They take too long to install>I disagree, I use them because they are faster than"expansion anchors", think about it, YOu have to drillholes and be careful it doesn't move around while drillingnext hole or the previous hole won't line up. Then you've gotto move the piece your trying to attach and then insert anchors.
Tapcons, I drill. insert screw with out having to move the piecebeing anchored and go on to the next screw. And if I really don'twant it coming up I put some polyuretheane glue down andshe ain't never goin nowwhere nowhow.One other thing about tapcons(as someone else has pointed out)Is if you use to long of a tapcon, I don't care what you do youain't gonna get that sucker in. For a 2x I use a 2-3/4" tapconso that is 1-1/4" of penetration into concrete. And I alwaysuse hex heads.
Doesn't any one use cut nails?DCS Inc.
"Whaddya mean I hurt your feelings, I didn't know you had any feelings." Dave Mustaine
I did everything I could have to get this screw to go in right, I think it just had to do with the fact I was drillinfg into a 60 year old slab that probably had a lot of aggregate in it. I drilled the hole as deep as the drill bit would go. I will try to drive it in with the drill still in hammer mode thats a good idea. As far as removing them I never had any luck getting them back out. If you get them in and try and back them out they ususally snap..............
The posts that mentioned an impact driver are referring to a specific tool that does not work the same as a hammer drill. I do not think you will get good results trying to drive a screw using hammer mode.
I don't have an impact driver so I can't comment on how well it will drive Tapcons.
-Don
Bosch SDS Bulldog in Hammer mode....
drill hole....
slide driver sleeve over the bit...
run Tapcon at full power in hammer / drill mode...
remove driver sleeve...
repeat as many times as you want to park Tapcons...
Hole sized to match the size of the Tapcon and material you are putting the Tapcon into....
So what's the big deal....
Mountains and mole hills thing AGAIN....
git back to work...Life is not a journey to the grave with the intention of arriving safely in a pretty and well preserved body, but rather to skid in broadside, thoroughly used up, totally worn out, and loudly proclaiming<!----><!----><!---->
WOW!!! What a Ride!<!----><!---->
Forget the primal scream, just ROAR!!!
one inch of screw penetration is about all you need...
and I clean the holes with the bit and skip the rest of that stuff..
Life is not a journey to the grave with the intention of arriving safely in a pretty and well preserved body, but rather to skid in broadside, thoroughly used up, totally worn out, and loudly proclaiming
WOW!!! What a Ride!
Forget the primal scream, just ROAR!!!
i agree. Don't try to drive it all at once. I take my impact and go in a little then back it out and keep repeating this especially for the longer screws. I don't clean out the holes. Also, if you are attaching anything metal to the concrete and the holes are slightly offset, the shank will ride along the edge of the metal hole and generate heat and break. So if your bit drifts when you drill the concrete, enlarge the hole in the object you are fastening.
Ajust the torque on your drill or go part way and back off like you would if you were tapping threads into metal
Like the others have said, they're good if you use good technique. Any concrete anchor has to have a good hole. And I'm definatley in the hex head only camp.
The opening scene of the movie "Saving Private Ryan" is loosely based on games of dodgeball Chuck Norris played in second grade.
I used to curse the damn things all the time.
Then I started using my Bosch Bulldog for drilling the holes and always drilling deep and only using 1/4" tapcons with hex heads. No problems.
Then when I got my first impact driver I switched back to #3 phillips head - still no problems and also always pulls head flush or lower. Still always 1/4"
Just have Chuck punch them in for ya.
I have np with tapcons, put 100 in today, didn't break any.
I nevr use fake tapcons, only the real thing will do.I hope Chuck Norris never potato sacks me!!!!
bstcrpntr --- I hope to grow into this name.
I use a fast speed for inserting
use the bit that comes in the box
drill deeper than needed
just clean the hole with the bit
always use the fast speed for inserting screw
I also use a hex to tap hole for phillips screw
Use a rotary hammer to drill the holes & go extra deep. Use an impact driver to drive the Tapcons. Stay away from 3/16" Tapcons -- they should outlaw them except for very light duty, fresh concrete etc.
Billy
try hammering them in. works great unless you want to take them out.
I like 'em.
As others have said, overdrill the depth a bit. I avoid using phillips drive. Use hex drive.
I put in over 100 of them in the last few days and had no problems.
"Doubt is not a pleasant condition, but certainty is absurd." Voltaire