Discussion Forum
Discussion Forum
Up Next
Video Shorts
Featured Story
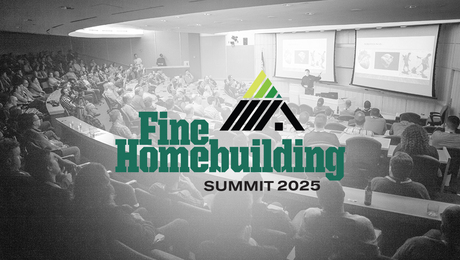
Join some of the most experienced and recognized building professionals for two days of presentations, panel discussions, networking, and more.
Highlights
"I have learned so much thanks to the searchable articles on the FHB website. I can confidently say that I expect to be a life-long subscriber." - M.K.
Fine Homebuilding Magazine
- Home Group
- Antique Trader
- Arts & Crafts Homes
- Bank Note Reporter
- Cabin Life
- Cuisine at Home
- Fine Gardening
- Fine Woodworking
- Green Building Advisor
- Garden Gate
- Horticulture
- Keep Craft Alive
- Log Home Living
- Military Trader/Vehicles
- Numismatic News
- Numismaster
- Old Cars Weekly
- Old House Journal
- Period Homes
- Popular Woodworking
- Script
- ShopNotes
- Sports Collectors Digest
- Threads
- Timber Home Living
- Traditional Building
- Woodsmith
- World Coin News
- Writer's Digest
Replies
“[Deleted]”
Create an floating subfloor - 2 layers of 1/2" or 3/4" plywood, layered perpendicular to each other and joints staggered. Layers are screwed to each other, and are not mechanically fastened to the slab.
Then install the solid or engineered flooring as normal.
Frankie
Is the original 1940s hardwood floor installed on a wood framing over the ground and not on a concrete slab? Is the original part of the house on piers? Is the original pier and beam construction? If it is I suggest your new part should be like the original. When you mix the different foundation styles movement is unpredictable and much more difficult to correct. I have seen this happen in Houston, TX and the owner couldn't find anyone that would fix it again due to unpredictable movement. What was eventually done is the original pier and beam section from 1910 was raised two feet and the new section's outside longitudinal beam that became the inside longitudinal beam, was bolted to the original outside beam of the 1910 pier and beam foundation. Then the old and new would move together and were at the same elevation. The original piers were also increased in size to match the new piers. Termite flashing was added. Original beams were cypress so there was no rot and no insect damage. Unfortunately cypress beams are in short supply and have been since the 1960s.
In the old days there were two methods of putting hardwood on concrete. One used hot asphalt when installing parquet and treated sleepers over hot asphalt to seal the concrete. Today you would put the concrete over a thick membrane that is placed on packed crushed gravel to eliminate capillary water. Some would add hardboard insulation under the concrete. The concrete would get a lot of rebar to keep it together if it cracked and some would use epoxy coated rebar to prevent steel corrosion in the event of concrete cracking especially if you were near to the coast and salt water. Some would put a thick membrane on the concrete with a floating subfloor and hardwood on top. Where the old and new come together you could attach an oak threshold to one side and allow it to float on the other side, where the gap is only about 1/4 of an inch between the old and the new.
In the first quarter of the 20th century, when hardwood floors were installed in homes a 1/4 inch gap was left between the floor planks and the wall framing to allow for floor expansion, even though it was nailed through the tongue with cut nails to the 1 inch thick diagonal subfloor. I cannot imagine you would get much expansion but that was the procedure. Base boards were typically 3/4 inch thick and nailed to the wall with the bottom 1/4 round nailed to the bottom edge of the base board. It was never nailed to the hardwood floor boards, the floor and baseboard were always separate and able to move separately. Yup, redundant; trying not to leave out any details.
If you can visit The Build Show online there was a visit they made to this place in Texas that has been recycling and purchasing heart of pine and old growth wood to repurpose. They may have wood that closely matches your old growth pine flooring, or maybe you would like to exchange your old flooring for oak that is more abundant than the pine. I do not remember the name of the company but they also do or make fire treated wood siding. It was covered on one of the Build Show episodes in late 2021 or early 2022.