I’m thinking of rearranging my shop and am looking for opinions on shop lay out
Discussion Forum
Discussion Forum
Up Next
Video Shorts
Featured Story
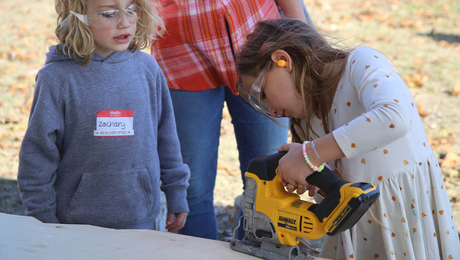
Listeners write in about continuing education, minisplit heat pumps, compact home shops, and building science.
Featured Video
Video: Build a Fireplace, Brick by BrickHighlights
"I have learned so much thanks to the searchable articles on the FHB website. I can confidently say that I expect to be a life-long subscriber." - M.K.
Replies
well the first thing i notice is everything is all dusty and the colors of the machines don't macth. so why don't i come over and help you clear all that stuff out of there so you can really get a clear view of what you want. i'll just haul that stuff to the scrap iron guys,i'm sure we can get a couple hundred for it.
shop layout is so tough you can get a layout in your head and just can't get better ideas until the first time you use it ,then it's like what was i thinking?
with a wood shop i like to think of how the wood process's thru the shop. lumber rack close to unloading door,next maybe a table saw,then to the planer,then to the chopsaw etc. finish area hopefully gets me by some doors to load out of.
not much help,but i will be waiting on your call to help clean out. larry
if a man speaks in the forest,and there's not a woman to hear him,is he still wrong?
While I apprecaite your willingnes to provide this kind service. I would hate to put you to that kind of effort.
I'm sure there's others here that wold help AOB...
I'm in...
Life is not a journey to the grave with the intention of arriving safely in a pretty and well preserved body, but rather to skid in broadside, thoroughly used up, totally worn out, and loudly proclaiming<!----><!----><!---->
WOW!!! What a Ride!Forget the primal scream, just ROAR!!!
go to grizzly.com and click on plan your own shop. It is so useful.
here's the link http://www.grizzly.com/workshopplanner.aspx
I too will help carry some stuff out
there's no need to reinvent the wrench
Edited 5/3/2008 11:06 pm ET by andyfew322
What is your objective for rearranging? To create more space for large assembly or storage? To allow for improved centralized dust collection? To improve workflow?
Said another way - what don't you like about the current configuration?
Easy to come up with all kinds of different layouts that don't really meet your needs.
As someone else mentioned, that Grizzly shop layout tool is really easy to use and will at least help you validate if your ideas will work before you start pushing everything around :-)
I'll try to come up with a sketch-up with the current lay out. As you can see by the pics things are a little tight. Storage is one of the bigger problems. I'm thinking pallet style racks may help.
I'm thinking you should've named this thread: "Look how much larger and cooler my shop is compared to your shop!"
or,
"Look at how many tools I have"
or,
"Look at how well lit my also well-equipped shop is..."
Show off... :)
Julian
that's funny right there....
Life is not a journey to the grave with the intention of arriving safely in a pretty and well preserved body, but rather to skid in broadside, thoroughly used up, totally worn out, and loudly proclaiming<!----><!----><!---->
WOW!!! What a Ride!Forget the primal scream, just ROAR!!!
While I understand your opinion, this is not a one man shop. I have 8 guys working here. From kitchen cabinet makers to construction workers to furniture makers. The current layout is a constant source of complaint. Each interest has a solution, but each is geared toward his particular interest. The lastest request is a slider tablesaw. I've spent too much time & effort to be off-hand.
Why so diverse a list of trades all sharing the same equipment/space? That alone seems to be a major problem . Any way to eliminate some of the trades or find more space for separation between them?
They can't get your Goat if you don't tell them where it is hidden.
You hit on a big part of the problem. When I found this space it was in a out of the way part of town. The landlord had built a nice big building then his business did well and he sold it and retired. it was really too big for what I needed but the price was good. I needed a couple of others to reduce the overhead. A few turned into several, which required more of everything. Things have gone from a heavy monthly payment to a positive monthly income. As I'm starting to contemplate retirement I would like to keep it. Everything kind of just grew based on where I could put the next tool somebody needed. The guys have made many comments about rearranging things. I've resisted because of the cost but am thinking maybe it time for a change.
I have set up many shops over the years, from my starter 12 x 20 detched garage to a 6500 SF CNC equiped shop. Weeke pointe-to-point, Holz-her beam saw and edgebander. We manufactured closet systems. Workflow and packaging was very important.For smaller shops I do it similar to Old Fred. Scaled floorplan then each tool was cut from card stock and labled. I use rubber cement or a removable glue stick so the layout can be rearranged or tweaked. I use different colored acetate for the for the footprint of the overall space each tool requires.I closed my nearly 30 year old business in 2004 and am working solo out of a 22' X 36' shop behind the house. Everything is on wheels except for my infeed and outfeed tables that are on levelors.Not to pry, but it sounds like you rent "shop time" or "space" to other tradesmen. If so, do you have to have any extra insurance. or do rquire your "tenants" to carry insurance? I would be leary of letting others make set-ups and tooling changes unless I knew them and their work habits.I had 8 employees in a 4400 SF shop for a while and each was assigned to one primary tool, but were crossed trained with all tools.BTW, I have been following and enjoying your "Door Jamb" thread. Are the doors milled in your shop? If so do you make them by hand?Chuck Slive, work, build, ...better with wood
"Not to pry, but it sounds like you rent "shop time" or "space" to other tradesmen"That is pretty much what it has turned into. About a year ago I firmed up the idea and turned it into an LLC which is owned by the corp. Everyone is required to carry their own insurance and sign a waiver as well. My lawyer says I'm covered, I hope so.Yes, I prep all the stock for the door jambs in the shop but do the fitting in the field. One of the nice things now about having the renters is I can be more selective about the jobs I do. For a long time I took every job I could get just to keep making the payments.
Sounds as if you have physically transitioned from being personal shop owner into being a "property" manager for a variety of businesses with out having made the accompanying mental shift of being in that position. What you have going sounds like a small business all in itself. A nice one too I might add.
Maybe time to think about the needs or requests the renters are making as client requests and see about meeting them through some expansion of space/equipment.
Possible to switch from rent to lease on the renters part to help finance the long term costs of the upgrade in services you are providing?
Or look at who's needs have really been paying the majority of the bills and focus on that trades needs as a priority. Just thought's as I don't have much of a head for business.
They can't get your Goat if you don't tell them where it is hidden.
"Sounds as if you have physically transitioned from being personal shop owner into being a "property" manager for a variety of businesses with out having made the accompanying mental shift of being in that position"That is what I'm struggling with now. It has been a hard mental shift for me. I've always been "the boss", the guy who bought the tools and made payroll every week. Now I'm more like a hotel manager and need to get with the program.
I've laid out several school shops and have found the easiest method for me was to draw a scale floor plan and then cut out a scale size paper shape for every single item that would be in the shop space. Then I got some sticky-backed magnetic tape and stuck each scaled item on a piece of the tape.
I taped the floor plan to a piece of sheet metal. I could then put all the magnetic scaled pieces on the floor plan and move them at will without them getting easily disturbed or lost.
When I found a plan I liked I could just set it upside down on a photo copier and record it, then try another plan.
Takes a bit of time to make the scale pieces, but once they are made the rest is easy, and you'll have a planning tool you can tool use for ever. I even made scale people (top view) and found it gave a better idea of needed space.
I made one large-scale layout for a new shop and displayed it where others could move the magnetic pieces around and add ideas. With eight employees, this might work for you.
By having every item sitting on the paper you'll have a visual inventory and will have a chance to evaluate each one's value.
Not a very futuristic method, but it's worked very well for me. (got me an "A" in an industrial layout course too) Sort of like having a chess game sitting out where you can walk by now and then and move a piece and think about it.
Good luck!
oldfred
oldfred,Talked to some of the guys today about making a scaled drawing with cut-outs so everyone can look at it and move things around, then vote on lay-out. Seems positive so far.
Nice setup! I hope you've got more to do there than rearrange the furniture. ;D
--------------------------------------------------------
Cheap Tools at MyToolbox.netSee some of my work at AWorkOfWood.com
Edited 5/6/2008 10:29 pm by Ted W.
Good luck!I agree with Lou C. on the need for a central dust system. Looked like you have a bunch of individual collectors taking up space.
Mathewson, How about a more piped in dust collection system? Oneida makes a nice cyclone. Thats if the budget warrants it. My question is: Is your table for the radial armsaw long enough for you? I'm thinking of redoing mine. You may have alot of machines clustered in the middle of the room. It may work for you. Good luck on the new move.
Lou C
Funny thing is I had a large central dust collector and was going to have the dust drop into a dumpster outside but the landlord wouldn't allow a hole in the wall. To set it up inside would have made things even tighter. Got rid of it only last month. Maybe I'll look at a smaller one.I got the radial arm saw for doing bookcases but it hasn't been used in a long time. In fact it is one of the things voted on to go. The table was long enough for what it was used for.
Give the landlord a deposit to cover the cost to repair the hole if you should leave. A dust collector outside would be a huge improvement.
I would also get some tall heavy duty shelves/racks to utilize that high ceiling and forklift.
BTW what is the dimension of the shop?
I'm meeting with the owner tomorrow, but he has said "no holes" on more than one occasion. Good point on the racking, I have them on the front walls & the guys would like more to go in their work stations.Thanks,
Keith
For my shop, the jointer is parallel to and right beside the planer, each faciing in the opposite direction. The table saw is nearby.
I believe it's easiest to have those machines out in the middle of the room, but only if you have underground electrical wiring. Your pictures show wires across the floor and that would seem to be a significant obstacle and liability when handling large pieces.
Conversely, the shaper, drill press and radial arm saw/mitre saw can all be pushed up against a wall.
And the single biggest improvement for you, it would appear, is a system of overhead ducts tied to a single dust collector, preferably away from the other machines.