I know you are expecting to see “hack work.” I hope you will be disappointed. Actually, I’ve had a chip on my shoulder from some of the negative comments regarding “Big Box Installers.” Here are a few photos of my latest Big Box installation (I hope the images are a pleasant suprise):
Discussion Forum
Discussion Forum
Up Next
Video Shorts
Featured Story
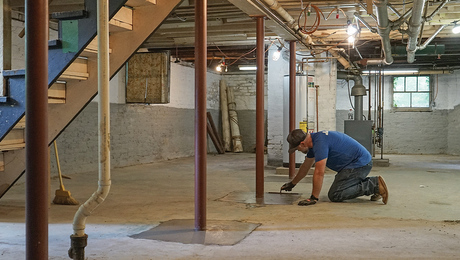
Upgrading the footings and columns that support a girder beam is an opportunity to level out the floor above.
Featured Video
SawStop's Portable Tablesaw is Bigger and Better Than BeforeHighlights
"I have learned so much thanks to the searchable articles on the FHB website. I can confidently say that I expect to be a life-long subscriber." - M.K.
Replies
Nice work, even nicer to have clients willing to pay for quality.
Let's not confuse the issue with facts!
Nice.
So how does one get to be a big box installer?
The heck, you say?
I do install work for two of the "Big Box" retailers. As these photos show, I am literally a "big box installer" (cabinet guy). This install was two huge, tall, end cabinets, 3 small base cabinets, two wall cabinets, a site-built TV nook w/ shelf and a 3-piece built-up crown.I am a sub for a company that handles installs for 20 big box stores in the Upper Midwest. I install for the No. 5 HD in the country. Though their reputation is less than perfect, I find it a good gig.
Nice installation, but if 99 percent of my clients saw that much sap wood and that great of a contrast in color, I'd be tearing it out. Course, I'd have known when I unboxed them and sent them back myself.
But the installation looks great.
I thought about replacing that one drawer front. Otherwise, most natural (unstained) cherry (and hickory) cabinets I see have considerable variation in color and most customers expect it (some even prefer it).I've been doing about two installs (mostly kitchens) a week and sending cabinets back really goofs up the schedule. I avoid this if possible (people get really cranky without a functioning kitchen). If the cabinets in the showroom have similar variation, that must be what they wanted. Usually it is what the customer wants/expects that arrives in the cardboard boxes.
Look at the color variation in the bricks they chose for the fireplace.
Dumb question from a former painter not familiar with the term; in the pics, which is the "sap" wood? The light or dark? Or neither?
Sap wood is the outter layer of wood on a tree. That is the layers where all of the water and nutrions flows (the sap). The inner layers to "dead wood" or heartwood and collect extractant that give it the color and also for woods like redwood and cedar it is the heartwood that is insect resistant.
thx -
sap wood = light color
and thx 2
i also do kitchen installations for a local lumber yard, and they buy cabinets from a large manufacturer
"our" store has a very professional capable design department and that makes all the difference and they keep me busy at least 50 hours a week
i have posted some pics in the last couple of days
big advantage to me? no estimating, no bill collecting, get paid for service calls etc etc
nice work by the way
caulking is not a piece of trim
Edited 6/25/2005 12:11 pm ET by steve
Were your recent photos of an "antiqued" or glazed, off-white kitchen? If so, that looked like some nice work.Edit to add: I found your photos again and they were the ones I was thinking of. Custom on-site laminating is rare around here. I only get to do that kind of work 2-3 times a year. Again, looks good.
Edited 6/25/2005 8:42 pm ET by basswood
That's what I thought
Welcome to the Taunton University of Knowledge FHB Campus at Breaktime. where ... Excellence is its own reward!
Looks great, but if I were you, I'd ask for a replacement for the bottom drawer; the sap wood detracts from the otherwise professional looking job.
Many manufacturers are willing to ship components for new installs; I have a set of cherry raised panel doors from a vanity set that arrived with small scratches in the finish. The lady asked if they could be replaced, and the manufacturer promptly shipped a new set. Need some doors? Have no idea what I'm gonna do with them, maybe build a vanity, lol.
I took your advice and I asked HD to replace the bottom drawer-front. They said they would, even though the customer didn't ask for it.We will suprise the homeowners and fix it even though they don't know it's broke.
And they will be pleased that you did. They will remember that, above all else.
I never met a tool I didn't like!
Install looks good.
The pictures just prove the flaws with "big box" stores. Those panels are a joke. The valance looks like it's made of 5-8 different pieces of wood. The crown moulding appears to be 3 different shades. The customer pays top dollar for junk, then assumes they are getting a good deal, because they see the same crap on TV shows.
Just to be clear the workmanship looks good.
IMO, the customer paid average $ for average quality cabinets (neither great, nor crap). I think the design was good (though flat screen technology will not require the deep cavern in the center of the unit). I'm glad you think I did a decent job installing them.
Nice job.
I would, however, replace the one piece of sapwood on the lower drawer in the middle of the built in.
I personally like variation in shading but this is just too much contrast.
But, JMHO. Otherwise I'd have this in my house in a skinny minute.
Chris
Basswood, not everyone knows what it's like to be handed a pile of finished materials that you have to make work the best you can. It's not like they give you a choice or anything extra to play with. Half the time you have to cut up refrigerator panels to make on site special applications. Handling the finished pieces is like trying to hold a greased pig, you have to be cautious of any mark and your cuts have to be accurate. Getting replacement parts can take weeks and there is no guarantee they will be better than what you have. Making a floor to ceiling installation, in an angled nook, that has to fit a masonry wall, takes a lot of skill and experience. Your workmanship is a compliment to the manufacturers product. The attention to detail that is evident in your work will be appreciated by the customer for many years. Flash photographs is a restricted area don't do anyones work justice. Once the piece has the owners belongings in place it will have a very different look. Thanks for the photos, it's nice to see a professional job.
Beat it to fit / Paint it to match
Thank you for the kind words. I can tell you have some experience with this sort of thing. Lucky for me the floor was close to level, the wall angles were good and the ceiling was only 1/2" out of level. There were a couple of issues getting the parts to work. I had to add fillers to the inside corners so the drawers and doors would not run into each other (due to the bay shape). The project came with angled fillers that were designed for use with cabinets with face frames overhanging the carcasses by 3/16", but these cabinets had flush sides (no overhang). It all worked out, just had to :>)
Who does the design and measuring for the jobs?
I have done a few kitchen jobs that were designed and sold by big box stores, but the install contract was through the customer. Few of them were ever straight forward. Most were a bigger PITA than they were worth. Since I wasn't contracted through the big boxes, I got no support, and a lot of grief when what they shipped didn't resemble what they designed for the customer.
That was twelve or fifteen years ago, and I stopped taking jobs like that. Getting caught in a three way "whose fault is it?" scenerio just wasn't worth it.
Ever have a customer wash thier dishes in the bathtub for two weeks, while thier custom top was being rebuilt? I had nightmares about that one.
BTW, nice work.
Dave
Customer does initial measurements.Designer designs (some are better than others).Then I'm paid $60 to check measurements and design on a site visit.Three or four weeks later the stuff shows up and I put it in. Most jobs have gone very well. Communication can be convoluted and lead to delays or mistakes. There is a PITA factor. The install company who hires me is a $70 million dollar a year business. They are hired to service 20 HD stores. So there are two large, often impersonal, mega businesses to deal with.I'm starting to tame the beasts though. They appreciate the work I do and have started changing some things to suit me. Responsiveness and flexibility may not be locally available at your Big Box. You'd probably have to take some of their jobs for several months to find out the local management climate.In this market, these jobs have been paying well (about $40-50/hr) with less overhead than my independent work. They supply the customer and product. They do the marketing and collect customer $. Also having a steady stream of their work, I can charge more for my independent work (higher bids and less concern about getting most of the jobs I bid). On the other hand I don't want to work for the Big Boxes exclusively. Trying to balance things.I'm glad you like the work.
I assume Keith C knows more about running a business that your parent company that's makes 70 million. How much is he grossing a year?Basswod is proud of his work, and he should be, seems like a hard working guy. I never saw where he said he designed the cabinet, picked out the wood or built the cabinet. No need to jump ugly how you could have done it better.Basswood, just always do things the best you can and you will be a success.Bear
Edited 6/22/2005 6:02 pm ET by Bear
The workmanship looks good. If you're fishin for critique though I'd have to lay it on the layout/design guy. When you're using kitchen base cabinets for a built-in next time eliminate the kick space and run a piece of matching base board. It'll give it a more professional look
Not like anyones gonna belly up to the entertainment center to wash dishes
Good Idea. Thanks.
Basswood - I'll join in the accolades. Looks good from here too. As far as the hollerin' about who does what, some people just want to hear themselves talk. I've seen "pros" who were independant that were hacks and the other way around too. My dad was a craftsman, probably the best I knew. For about ten years, he subbed basements - finishing them - from a big box. Studs were all 16" centers, everything was plumb, square, tight and true, etc. Miters (cut by hand) couldn't be open more than the thickness of a business card - and damn few were "open" anywhere near that much. Other crews used 24" centers, less nails, did garbage work. The bosses kept asking him to go back to their jobs and take care of the problems. (He finally said, No more.) He didn't want to be bothered during that time looking for work and doing the "business" nonsense. All depends who you are and where you are. Keep bangin' those nails.
Hammerlaw,Thanks for the good word. I've been asked to fix or finish about two kitchens a month. I've done most of them, but at a premium. Some of those can be like walking into a hornets nest. Sort of hard to turn a very unhappy customer into a happy one. With that kind of challenge, the money better be good.