Workshop from Shipping Containers
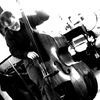
I am considering building a freestanding workshop is stages, starting with two steel shipping containers on a concrete slab, adding roof trusses, and enclosing the top & sides with structural insulated panels. Any comments?
Replies
Build a pole barn over them. If you have to move you load up the boxes and leave the cheap roof. Also If you have a sudden need for a roof you can back the containers out a bit to free up cover space. I have a friend with a conex box shop. He moves them with a come along using the eyes he poured into the flab that extends about 25' out both the front and back. These also made great parking and material storage spots to keep everything out of the mud.
He made over 50 book cases for a contract and moved the container about 20' out of place so he had extra covered storage. When the job was done he pulled it back for the superior insulation and protection.
Thank you very much. Your comments provided valuable insight and ideas I had not considered!
jazz- you going to have enough head room in there?
Half of good livin' is staying out of bad situations.
Rez makes a good point. I wouldn't want to have a workshop with less than a 10' ceiling - 12' would be better, if money were no object. (Which it always is)
How about building a small building to start, then adding on as you have the funds? I thinkDid you ever wonder if the person in the puddle is real, and you're just a reflection of him?
My concept is to (1) place two shipping containers parallel to one another (16- to 24-feet apart) on a reinforced concrete slab, then (2) place (steel?) roof trusses on top of them to form a roof with ample headroom, then (3) cover the roof with structural insulated panels and roofing to keep out the weather, then (4) surround the whole shebang with SIP walls to form a secure & weatherproof workshop.
The plan is to use the shipping containers to store (a) tools and (b) building materials until the entire shop is constructed (weathered-in and secure).
The "commissary" at the Boy Scout camp I attended as a child was similarly constructed, and is still in use some four decades later.
Thanks for your time and comments!
All I can say is it's a good thing you don't live around here. You'd get about 2 days of use before the inspectors had you tearing it down.
That...is a good idea. Slick. Hope you can post pics when the time comes. Ain't it grand not being a city slicker. Roar! Half of good livin' is staying out of bad situations.
Near my in laws place, there is a contractor with a shop made out of 4, 50 ft boxcars; two on each side, with a roof over the top. He's got 4 10x50ft rooms, with a big open space (roofed over) in the middle for his dozers. Seems to work for him, so I don't know why shipping containers wouldn't work, too.
No interntion to hijack the discussion here, but a little while ago I received an email about negative comments and the way I talk to customers.
My "negative" comments are directed at building codes, not the idea here. I'm having a go around with the local assessor and building inspector right now. Long story, but I can't believe that I'm the only one that would have codes as an issue with ideas like this. Workable and practical have nothing to do with what you can and can't do in a lot of areas. The first problem would be that there is no way you could get a power drop to a non-foundationed structure on residentially zoned property. There is no way you would get a permit to run a sub panel off of existing power to the sturctureshop described here. Geeesh, this is only the beginning.
Nope, if anything, my comment was envious of the idea and the ability to pull it off, surely not slamming.
Don
Understood you from the get-go. No misunderstandings here and no need of explanations.
Knowledge is power, but only if applied in a timely fashion.
Thanks, I appreciate that. I have to say thought that after rereading what I wrote I can see how it could be interpreted to go either way.
Don
I think that given a certain amount of modification there, if your area is like this one, shouldn't be any insurmountable problems, code wise, getting power into the boxes. There may be requirements that a second exit be added, I think the opposite end would be the logical spot, but if classified as a portable structure there are certainly legal ways to get power into these units and use them as a workshop. I have installed power systems in quite a few skid mounted sheds and outbuildings. The second door seems reasonable, but entirely up to the AHJ, considering the normal 40' length and the possibility of a fire blocking the only way out.
Given the ceiling height and wall materials I would use EMT and surface mount boxes, florescent lighting, and, if called for a 30 or 60 amp pigtail if the AHJ objects to a hardwired connection. This I would sub, by way of an underground feed, off any convenient panel capable of supporting the load.
Don't want to get into a wizzing match over this, but yes, you can get a temporary permit, usually 18 months for a portable sturcture as long as you pull the permits for a permanent structure at the same time. On residential property, most will first build a garage or other permanent structure because it is just a lot less hassle. Can't even put a mobile home on a plot if you don't put in a foundation, remove the axiles, and mount the home to the foundation permanently.
I'm arguing over a building on some property of mine right now. Zoning was changed while the property was in foreclosure, and because of necessary filings that need to be made prior to a rezoning grace period expiring, I lost my grandfather clause. The building is on a slab with no footer. Put one in, or take the building down. Further mud in the eye is the building is not homstead eligible as a commercial building, but I can't use it for anything. So--I have to pay full commercial millage on 26% of my property with no tax benefitsadvantages. And not being zoned commercial, I can't use it commercially. Their way of telling me to hurry up and take it down. Can't fight city hall.
Don
Edited 12/11/2002 6:07:49 AM ET by Don C.
Just got to talk to the code wizards where ever you live.
My last house. I wanted to build a small workshop (12x16). To build it I would need to get a waiver from everyone of the people who lived in a 4 block radius of my house, and attend a planning & zoning commision meeting and present my plan for consideration. But, if it was a portable vs. a permanent structure I didn't need a permit at all.
Wanting to build it that year, not 3-4 months down the road, which would have then meant waiting for winter to pass, I built it as 2 halves bolted together in the middle. Half sets on an existing concrete slab, the other half on deck post concrete blocks. Ran underground power to it off my main panel. No permits or inspections needed or called for.
Turned out nice, but I sure wouldn't want to be the one to move it.
Now I live in another town. Portable structures are handled similar, but I have no idea what the rules on a permanent structure would be.
Round here, Florida, the call is that the building itself, if it is portable need not be inspected. They, the AHJ, wanted it anchored so it doesn't blow away and knock down someone else's house but this was accomplished by using screw anchors.
The container shop I referred to was looked at and the conclusion was that given its weight it need not be anchored. The man did install angle iron plates that, when the box is pulled into position, line up with anchors sunk into the slab but these are accessible and easy to remove. When a hurricane comes near he bolts it all down just to make sure.
The inspector was called in to check the electrical installation. The system, a small mobile home panel subed off the house panel, a pigtail feeding another sub inside the box to serve three circuits, easily passed.
Sounds like this guy built a pretty slick little system.
I like how he used the shipping containers.
The electrical sounds pretty similar to mine. I just shot 60 amps out to the shed to a sub-panel. Never got the welder I wanted, so it only ran lights and power tools.
I never tied mine down, but hurricanes aren't much of an issue in the Rocky Mountains. There was a tornado once, 20 or so years ago that took a shed roof off about 5 miles from here, but not much of an issue. We did get some 70mph gusts last spring that peeled 1/2 the shingles off a small storage shed I built, but it's not a common thing.
If you don't have covenants to deal with, it sounds like a great way to go. There's a big storage rental unit a couple miles from me that used a ton of them. Every other spot in the unit is a 2 shipping containers end to end. They framed in a garage door and dividing wall in the middle of the building and roofed over the whole thing. Pretty slick, using the shipping containers for a storage unit, and as the side walls for the other units.
Gotta run
Bill
The city recently passed a law here within city limits although it's country. Cannot build a pole barn type garage structure unless you have a house already there. So you have to build the house first and leave all the materials exposed to weather.
I'd like to express my feelings for city government but this is a family forum. Half of good livin' is staying out of bad situations.
I don't understand why you're bothering with the shipping containers. If you're going to do roof trusses, SIP panels, and a slab, you're most of the way toward a "real" outbuilding. Do you have the containers already? If not, they're pricy. I'm guessing it more economical to just do a pole barn or something similar.
It's really hard to find local shipping containers because they are only sourced locally or otherwise. I was able to find a shop locally but at http://shippingcontainersale.org/ you should be able to find a local source.