Built to Outlast: An Interview with Jon Frost
The Minneapolis cabinetmaker and designer talks about his work
The principal of Frost Cabinets Inc. and a cabinetmaker for 25 years, Jon Frost begins every project the old-fashioned way by “spending a lot of time planning.” During the process, he asks and answers many questions before putting blade to wood. In an interview with FineHomebuilding.com, Jon tips his hat to the past St. Paul architects and cabinetmakers who have influenced his work and describes what he considers the ideal challenge from a client.
What is your approach to cabinetmaking?
JF: We try to build things that are going to last. I like to think the stuff we build will outlast its owners (even the eternal baby boomers). When we build traditional cabinets, we like to use mortised butt hinges. They’re a good investment, well worth the money and effort. We use plywood rather than melamine since melamine spoils (a shelf with a short shelf life, so to speak). And we use just enough joinery, where it will be really effective. We won’t use joinery for decorative purposes or the implication of quality—unless, of course, the joinery detailing is part of the design and the owners know where their money is going. With modern designs, we lay up our own veneer, which gives us a great deal of control over the quality and appearance of our work.
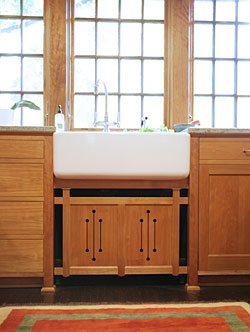
What do you do first?
JF: I’ll build a model to help keep the scale in check. Inevitably, it brings about and answers the early important questions: Are the legs too fat? Is a 30-in. desk height OK? Is the island too huge? It also helps if we’re incorporating a mechanical element we haven’t done before and need to be especially precise.
Selecting the right lumber or veneer is often times less than automatic and needs to done early. Next, I case the job site and look for mechanical details that might affect how we put something together. We ask ourselves: Is the building plumb and level? Are there any potential problems with access? We also try to get our hands on appliances or plumbing fixtures that need special fitting.
Finally, I resolve any discrepancies between the plan and the building, and I try to get a read on the general contractor. Is he on time and in control, or are the subs working on a first-come-first-served basis?
Who or what are your design influences? Who inspires you?
JF: My design influences are always changing. At times, I have been interested in and have made things influenced by Emile-Jacques Ruhlmann, Thomas Chippendale, Augustus Pugin, Frank Lloyd Wright, Greene and Greene, Gustav Stickley, etc. I like anything from the coast of California. I have been looking at buildings and furniture lately that use boards and planks in patterns.
I’m inspired by the artwork of George Morrison and the furniture of Roy McMakin and Piet Hein Eek, and I’m always looking for opportunities to try things out. I’ve always been influenced by St. Paul architects Clarence Johnston and Cass Gilbert, along with the St. Paul cabinetmakers William Youngbauer and Sons, who built dozens of houses in turn-of-the-century St. Paul that are absolutely dazzling.
Do you have any signature design elements, things that really identify a piece as one only you could have made?
JF: We don’t have any signature design elements, and it’s my hope that our work simply looks and feels right with the building. Maybe I just don’t have any original ideas, but I try to let the house and the owner drive the styling. A good example of this is shown in the photos; the turned post on the homeowners’ porch became the inspiration for the turned legs on their kitchen island.
I do, however, like to think that we have some signature construction methods that are evident, like the use of mortised butts on traditional cabinets. And, especially when we make contemporary pieces, we never let production machinery drive our methods. The more edgebanders and line borers you use, the more efficient, but it ends up looking like it could have come from anywhere.
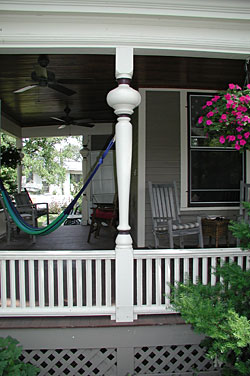
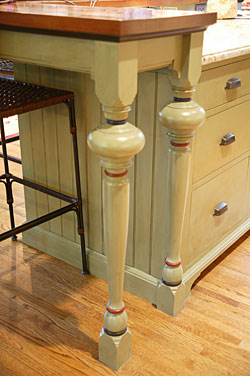
What do your customers seek you out for?
JF: I like to think that we’re like a kitchen in four-star restaurant that will make you anything you want and provide old-school, no-flash service all the while.
What tricks do you use for customization? How do you keep your designs diverse?
JF: We have appliances delivered to our shop and bench-fit them. We get things to really align well this way.
If the owner has something to store or use in the cabinets—special spice bottles or an old mixer, for example—we get the items in the shop and fit them carefully. I like to make simple wooden roll-outs and dividers for the insides of the cabinets, and I avoid the gimmicky gadgetry organizers.
Another tip for customization: I think it’s cool, if not a little tedious, to build the electrical receptacles into the underside of the upper cabinets so that the backsplash is left clean. We also use the wall depth, or thicken the walls, to disguise the actual depth of a fridge or oven cabinet.
And we also integrate the trim and cabinetry. That integration can take many forms: Maybe the baseboard is the same height as the toe space. Maybe the base continues across some of the cabinets. Maybe there is a trim band around the room that continues across thecabinets. Maybe a cabinet fits in a hole in the wall and is cased like the windows.
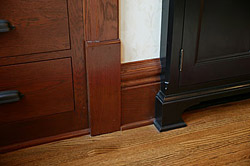
If you had to pick a first love, would it be designing or building the cabinets?
JF: I like them equally well. Anyone who builds things develops a sense for design, and anyone who designs things should do some building. What I really love and am always working toward is a balance of designing, building, and installing. One of things I like best is to get lost in my work, and that’s easiest to do in the shop.
Do you have a favorite project?
JF: My favorite projects allow me to apply whatever my current design interests happen to be. Another favorite: When an client approaches me and says, “Here’s my TV and my bowling trophies. Make me something cool.”
Related Article: To learn more about Jon’s work, read Signature Details for Kitchen Cabinets in the August/September 2007 issue of Fine Homebuilding.
Photos by Charles Bickford, except where noted