What Happens if Your Framing Gets Rained On?
Here's why learning to use a moisture meter is important.
Rain during framing is hard to avoid, so how do you know when a house is dry enough to move ahead with construction?
Q: What happens to the typical American house that’s built in a 4-6 month cycle?
A: The moisture in the framing lumber dries after a few months of heating/cooling and the house settles. This is indeed normal but it doesn’t need to be so pronounced.
First, let’s talk about the property of wood called Hygroscopy. Hygroscopy is the ability of a substance to attract and hold water molecules from the surrounding environment. This is achieved through either absorption or adsorption with the absorbing or adsorbing material becoming physically ‘changed’ somewhat, by an increase in volume, stickiness, or other physical characteristic of the material, as water molecules become ‘suspended’ between the material’s molecules in the process. (Source Wikipedia.org)
Most of the lumber used in my homes is kiln dried (KD), meaning it should arrive to the job site at a moisture content of 12-14%. Non-KD lumber or pressure-treated lumber generally has 15-19% moisture content. That 19% is a critical number as it’s a general consensus among the building-science experts that above 19% moisture content is the point where mold spores are activated and the rot processes start (assuming it stays above 19% for an extended period). Wood can absorb water up to 28-30% moisture content and is saturated at that point.
So, what happens if you close up framing that is still “wet”?
You may see:
- Sheetrock cracks, nail pops, cracks in the sheetrock above windows/doors
- Floor squeaks, Stair squeaks
- In the worst case scenario, plumbing stacks can move, which could lead to Roof leaks
Now that you have a brief lesson on Wood Moisture Content let’s talk about what to look for in regards to Moisture Content for a home under construction. First, you as a Builder NEED to own a moisture meter. I like pin-based meters like the Extech model I currently use. Next, we want to ensure there is ZERO lumber in the house with a MC above 19%. This is a hard rule, if you are getting readings on your Moisture Meter above 19% then cancel your sheetrock hang crew till it’s all below that 19% threshold.
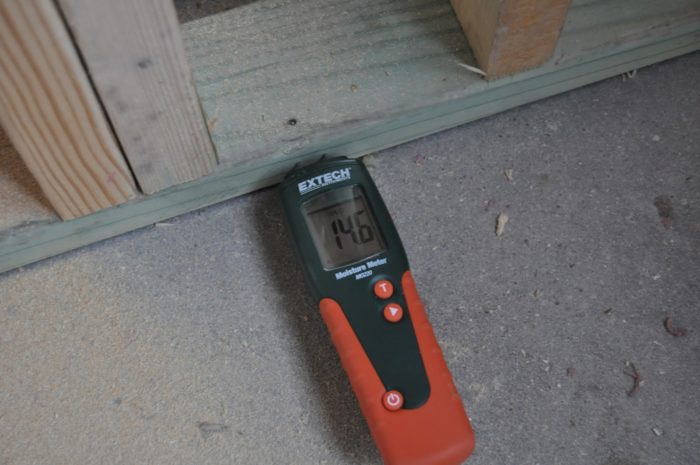
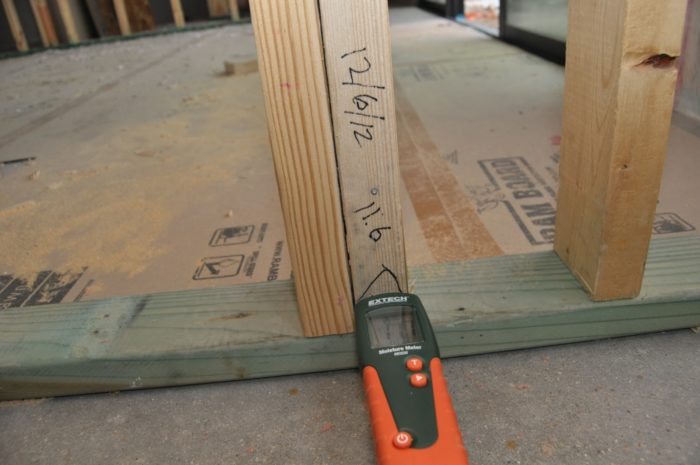
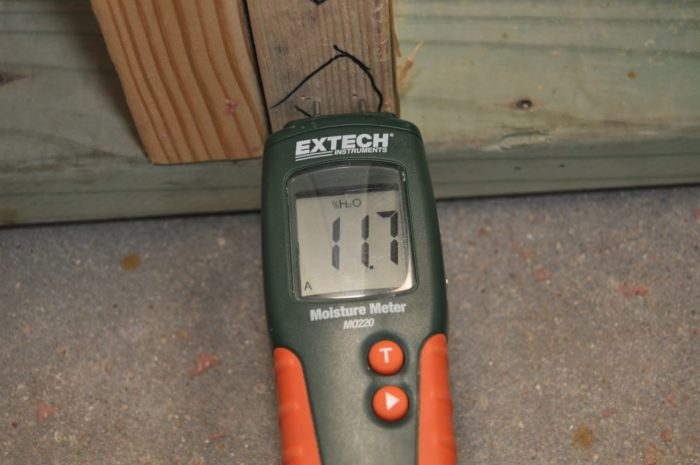
This testing is critical to really knowing what moisture content your wood is reading prior to hanging rock. As I said before you must get all readings less than 19%, but MY standard is all readings below 13-15% for my KD lumber and less than 17% for any green Pressure treated lumber. Once your home is completed and the heat/cooling equipment runs for a year it’s typical to see those studs reach equilibrium MC around 10-12%. That’s why I really want to see MC %’s below 15%. A small degree of drying is expected but when you get more than 5% MC loss the shrinkage of that lumber will show greater flaws in your finishes.
I’ll show you how to dry a wet house in a future post!
Best,
Matt Risinger
Risinger Homes in Austin TX
Risinger Homes is a custom builder and whole-house remodeling contractor that specializes in architect-driven and fine-craftsmanship work. We utilize an in-house carpentry staff and the latest building science research to build dramatically more efficient, healthy and durable homes.
Be sure to check out my video blog on YouTube.
Fine Homebuilding Recommended Products
Fine Homebuilding receives a commission for items purchased through links on this site, including Amazon Associates and other affiliate advertising programs.
Leather Tool Rig
Bosch Wall Scanner (GMS 120)
QuikDrive PRO300s
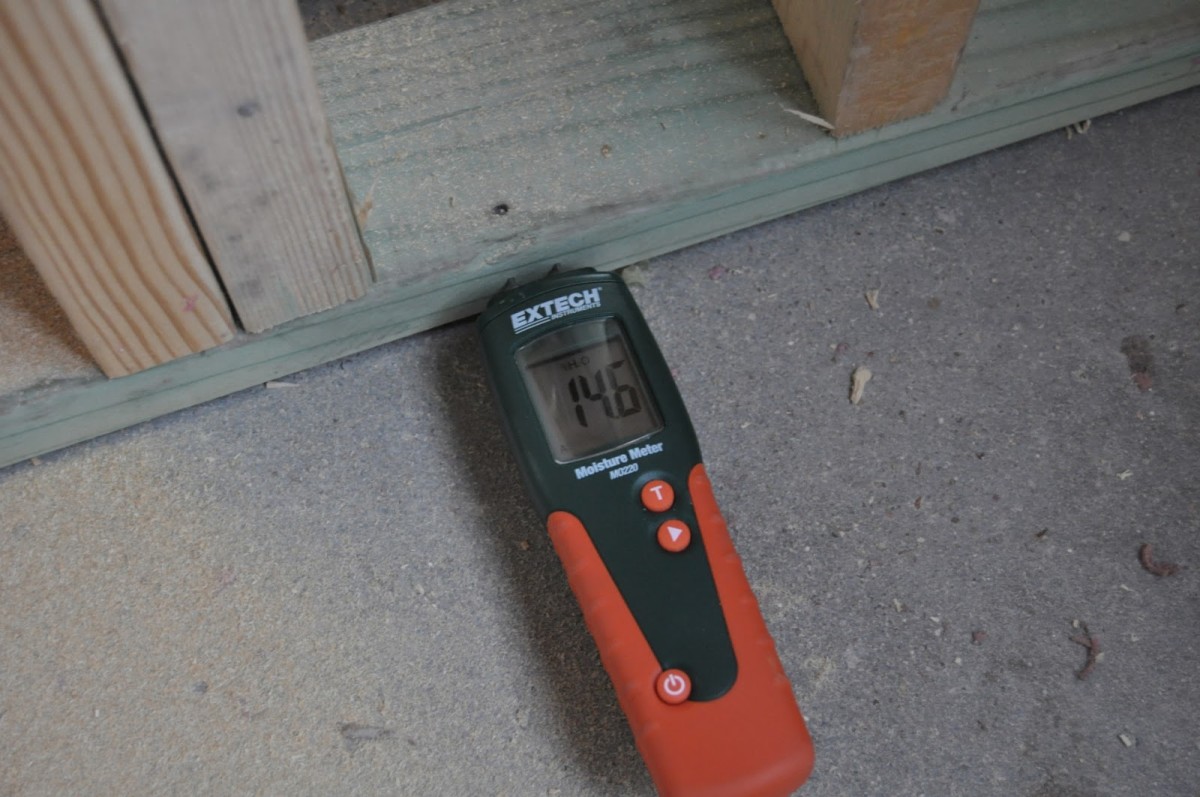
View Comments
Folks, you should check out Matt's video blogs on YouTube. He has provided a link at the end of his article. I just viewed one on captured (let-in) treads and risers. Matt is well spoken--not so easy to do when you're live on camera--and the video has tons of good information. Good job, Matt!
@Olitch: Thanks for the complements and the plug for my video blog! I grew up as a fan of This Old House and my video blog is my way to pretend to host TOH. I've been blessed with some great Clients & Architects who have provided interesting work and it's fun to share. Best, Matt
I totally agree with moisture problems with framing material. Most lumber yards in the NE where we build don't have covered storage so framing lumber absorbs large amounts from rain at the yard even before getting rained on during construction. This is compounded by winter conditions leading to not only wet lumber but also lumber with moisture frozen in it. This does not dry out if temps don't rise and before the structure can be heated. A dilemma since to hold the heat in a structure during winter construction you need the insulation. A real catch 22.
Due to added moisture issues with delivered material and it even being delivered with mold already evident on some loads we have begun to spray all structures with mold inhibitors prior to insulating and sheet rocking. We sell this as a value added benefit to our clients who are concerned about mold. We have found Aftershock from Fiberlock Technologies works well at killing any residual mold and prevents future growth.
You frame with KD? Must be in some rich, dry state like Texas or CA. In Oregon you drive a nail and water splashes out of the wood.
What rules apply to MDF or OSB which is commonly used in the Northwest?
Jumping ahead to Matt's next chapter, don't even THINK of using a non-vented propane heater to dry a house –– 100,000 BTU of propane creates about a gallon of water! It keeps you warm, but not dry.
I remember a house I inspected several years ago that the homeowner claimed was built with saturated wood. The house was drywalled and finished in the winter, so most likely the water was frozen and trapped in the wood. It had all of the signs except mold. The studs shrank so much after the homeowners moved in that in addition to lots of drywall cracking and nail pops, all of the electrical boxes extended proud of the drywall face by as much as an 1/8th of an inch (hence the cover plates all floated off the wall face).
@BGodfrey: I actually built houses in Portland, OR for three years and learned a TON about this subject while living there. This technique of checking for moisture with a meter and drying prior to SR is VITALLY important for your climate. I saw a ton of rot in 1-2 year old homes from houses that were framed wet and moved right to sheetrock. It's not easy for a house to dry when the studs are wet and Sheetrock is on one side of the wall and a pin punched weather barrier is on the other. Add to that MDF that's painted with Oil based paints and everything is caulked tight. Disaster can ensue.
@rgunth: Same rules go for OSB, except saturated OSB has a hard time drying. Once it "poofs" out it's time to replace it. Same for wet MDF. This is one reason I like sheathing my houses with a base course of PT Plywood 2" around the bottom course of sheathing then going up from there with OSB (or plywood if the budget can take it). The plywood is much more forgiving with moisture.
@eastcliffe: Great examples of issues that come from wet houses. In general we're not talking about structural failures but cosmetic issues that can be avoided. On the other hand, if you have saturated lumber with Moisture contents above 19-20% rot can happen. It takes a LONG time for a 2x4 buried in an exterior wall to dry from a saturated state and rot can happen even in a new house.
I've seen roofers put a new roof on a brand new house where it has rained and is still raining. I keep thinking that would trap the moisture under the shingles and do no good either.
A carpenter once told me in all seriousness that wood gets wet and I should live with it. He also said how they bring up huge old logs from a lake bottom and make houses with them. Yeah, but not until they're cut and dried out!
I have shingled wet roof sheathing many times and it seems total nonsense to think the sheathing won't soon dry out; air still circulates above and below felt paper and shingles and therefore won't evaporation still occur ? I have been involved in framing hundreds of structures and have seen firsthand substantial joist shrinkage after a heating season but in my experience all cases of rot and deterioation that I've seen have been the result of poor moisture prevention detailing. Years ago I attended a seminar called the Hundred Year House and the one fact I remember was that 90% plus of all home problems are moisture related in one way or another and it seems very true to me.
@user-214653: Yes, many roofs get put on wet and with a traditional vented attic they will dry to the bottom and be perfectly fine. What I'm mainly talking about here is framing that will be buried on both sides by other construction materials. Remember that our houses have less and less solid wood that can absorb water and release it. OSB and other "was wood" products don't take a wetting very well. They either have so much glue that they don't absorb water, or if they do absorb it, they blow up. Houses from the 1940's and earlier had solid framing lumber, solid 1x sheathing, solid 1x decking, etc. I've heard Joe Lstiburek say that a typical pre-1950's house could absorb 50+ gallons of water and that a new house today can soak up less than 10 gallons. I'm digressing, but the main point of this post is that framing that will be buried needs to dry to lower moisture % so future problems in finishes can be avoided. Thanks for the comments everyone. Best, Matt
See the follow up post to this about drying wet framing here:
https://www.finehomebuilding.com/item/27129/drying-wet-framing-lumber
Thanks, Matt
Framing, in construction known as light-frame construction, is a building technique based around vertical structural members, usually called studs, which provide a stable frame to which interior and exterior wall coverings are attached, and covered by a roof made of horizontal ceiling joists and sloping rafters.
http://www.riverviewhomes.ca/
Guys, you might be interested in checking out fine luxury homes by Brejnik Fine Homes (www.brejnik.ca). They build fine luxury houses. Brejnik team consists of qualified and trusted: Architects, Interior Designers, Appraisers / Lenders, Trades & Suppliers, Geo-technical engineers, Structural Engineers, Arborists, Landscape Architects, Pool & Water Feature Specialists.
Doing some more research into this problem I came across these plastic bottom plate packers that keep the framing from being in direct contact with the floor. Only available in New Zealand at this stage it seems - wonder if anyone has tried anything similar in the USA?
http://www.hiandri.com/