Taping Fastener Heads and Seams: Third Coat
Apply this finish coat with a taping knife or, if you have a helper, a paint roller.
If you have been careful with the first and second coats, the third coat should be the easiest and require the least amount of joint compound. Because the third coat is usually the final coat, it is a good idea to do some light sanding before you begin—just knock off chunks of compound and tool marks. Use light pressure to sand every seam and along the inside corners. Use a pole sander with 100-grit or 120-grit sandpaper or a sanding screen. Be careful not to sand down to the tape. The aim is not to sand out every last defect but only to make it easier to get the finish coat of joint compound as smooth as possible. (It helps to think of this step as a light “brushing” rather than sanding.)
There are two ways to apply the finish coat to the seams: with a taping knife (the conventional method) or with a paint roller (the faster method—especially if you’re working with a helper).
Taping-knife application
Apply the compound over the entire seam using a wide taping knife (I prefer a 12-in.-wide knife), going slightly wider than the second coat. Next, remove most of the joint compound by pulling a 12-in. trowel firmly along the seam. Feather the edges one last time so that there are no thick or rough spots, and then take off any compound left on the center of the seam. The thin layer of compound left fills in all imperfections, scratches, dents, air bubbles, and so on. The compound dries out a little as it is worked, so you can thin it with water as necessary for easier application.
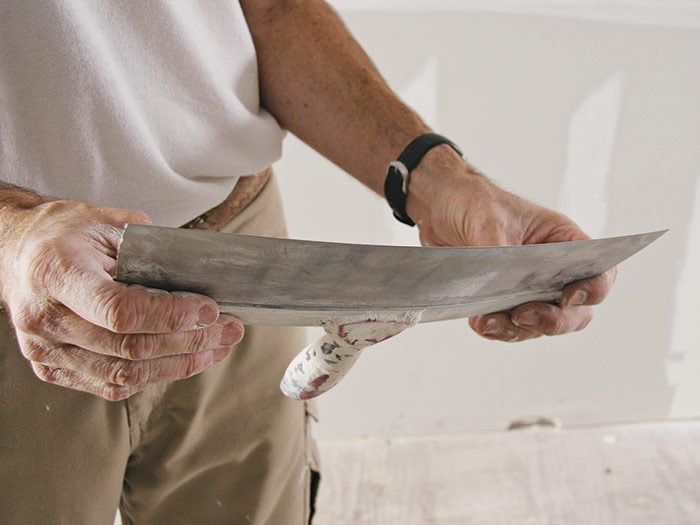
Paint-roller application
Thin the joint compound with a little water and then use a 3/8-in.-nap roller to apply it. Again, lay it on just a little wider than the second coat. Then smooth and remove the compound using a 12-in. trowel in the same manner described for the taping-knife application. I find that rolling works faster than applying the compound by knife, and if you attach a pole to the roller handle, it’s easy to reach high seams. (Working with a long-handled paint roller also places less stress on your wrists and arms than applying the compound with a knife or trowel.) One member of the crew can roll the compound on while another finishes the seam. This works especially well on ceilings.
General Guidelines for Applying the Third CoatI recommend using a topping or an all-purpose drying-type compound for all third-coat applications. These compounds can be thinned with water and are easy to apply and sand smooth. Taping and setting-type compounds dry out too quickly in such a thin coat, and they are harder to sand. Start the third coat by applying a thin layer of compound to the fasteners, and then move on to the seams and outside corners. Wherever taped areas intersect, smooth and blend them together, working both seams at the same time. Apply the finish coat to the inside corners after the intersecting joints are finished. When applying the third coat, keep the following points in mind:
|