A Practical Look at Deep-Energy Retrofits
Cutting a home’s energy use by 50% to 90% is a worthy goal, but the extreme costs keep it out of reach for many. We take a look at the most cost-effective alternatives.
Synopsis: Reducing energy consumption is a goal for many homeowners. However, the cost of retrofitting a house to make it as energy efficient as possible can seem to be insurmountable. Contributing editor Martin Holladay takes a look at the most cost-effective methods of reducing a house’s energy use by 50% to 90%. Energy retrofits can be done in phases and in different locations in a house. The roof, for instance, can become better insulated with a lower-cost project like sealing air leaks. Basements, walls, windows, and HVAC equipment all also can be air-sealed to help reduce energy consumption. The author considers both deep-energy and practical approaches for retrofits in each of these locations, and also looks at performance and cost comparisons for each. This article includes two case studies of deep-energy retrofits.
If you pay any attention to building science, you have probably seen the term “deep-energy retrofit” — a phrase being thrown around with the colloquiality of “sustainability” and “green.” Like the word “green,” the term “deep-energy retrofit” is poorly defined and somewhat ambiguous. In most cases, though, “deep-energy retrofit” is used to describe remodeling projects designed to reduce a house’s energy use by 50% to 90%.
Energy retrofits of all levelsPaul Eldrenkamp is a Massachusetts remodeler who has performed several deep-energy retrofits. When his clients balk at the high cost of a full retrofit, he sometimes advises them to work in phases. Although it is common to perform energy improvements over time as finances permit, it’s also important to take advantage of upgrade opportunities even if they seem to fall out of sequence. For example, if you have to install new siding or roofing and you do so without installing thick rigid foam underneath, you may regret your shortsighted decision in time. Here’s a general overview of the work to be done, the order in which it should be completed, and the practical alternatives to going deep. Phase
Roof insulationDeep-energy retrofit Many deep-energy retrofits call for insulating a roof to R-60, which can most easily be done by adding 4 in. of rigid polyisocyanurate foam on top of the roof deck and then filling each rafter bay with loose fill or batt insulation. Exterior foam sheathing has the added benefit of reducing thermal bridging through the rafters. ![]() Practical approach It’s much less expensive to install cellulose on an attic floor than to install rigid foam and new roofing. Address air leakage before dragging a cellulose hose into the attic. Seal all ceiling leaks under the existing insulation (for example, at electrical and plumbing penetrations, at utility chases, and at the gaps between partition drywall and partition top plates). It’s also important to be sure that there are no air leaks at the perimeter of the attic, where the ceiling air barrier meets the wall air barrier. Performance comparison While there is no upper limit on the R-value that can be achieved when installing foam on top of the roof sheathing, the maximum R-value of attic-floor insulation depends on the available height at the perimeter of the attic. Achieving R-60 requires about 16 in. of cellulose. Cost comparison Attics with easy access are easier and cheaper to retrofit than cluttered attics with lots of penetrations that need to be sealed. From a material standpoint, the practical approach is almost always more economical. For any given R-value, polyisocyanurate costs from three to five times as much as cellulose insulation. Needless to say, adding rigid foam on top of the roof sheathing includes significant expenses for roof demolition, new roof sheathing, and new roofing—costing between $3 and $5.80 per sq. ft. |
Remodelers have been performing deep-energy retrofits — originally called “superinsulation retrofits” — since the 1980s. Most deep-energy retrofit projects are predominantly focused on reducing heating and cooling loads, not on the upgrade of appliances, lighting, or finish materials.
While a deep-energy retrofit yields a home that is more comfortable and healthful to live in, the cost of such renovation work can be astronomical, making this type of retrofit work impossible for many people in this country. Those of us who can’t afford a deep-energy retrofit can still study the deep-energy approach, using it to shed light on more practical and cost-effective measures to make any home tighter and more efficient.
How deep?
No standard-setting agency has established a legal definition of a deep-energy retrofit, but the term generally refers to retrofit measures that reduce a home’s energy use by 50% to 90% below that of a code-minimum house — or, according to a more lenient definition, below preretrofit levels. Probably fewer than 100 homes in north America have completed deep-energy retrofits that conform to the strictest definition of the term.
A house that has undergone a deep-energy retrofit typically ends up with R-20 basement walls, R-40 above-grade walls, R-60 roofs, and U-0.20 windows. A typical airtightness goal, determined by a blower-door test, is 1.2 AcH (air changes per hour) at 50 pascals.
Retrofit results
Cost: $140K
Annual savings: $2300
Location: Arlington, Mass.
Size: 3000 sq. ft. (duplex)
Renovation cost: $47 per sq. ft.; $140,000 total
While planning a deep-energy retrofit of his 3000-sq.-ft. two-story duplex in Arlington, Mass., owner Alex Cheimets got a lucky break: He was eligible to participate in a pilot superinsulation program sponsored by the Massachusetts Department of Energy Resources and his local utility.
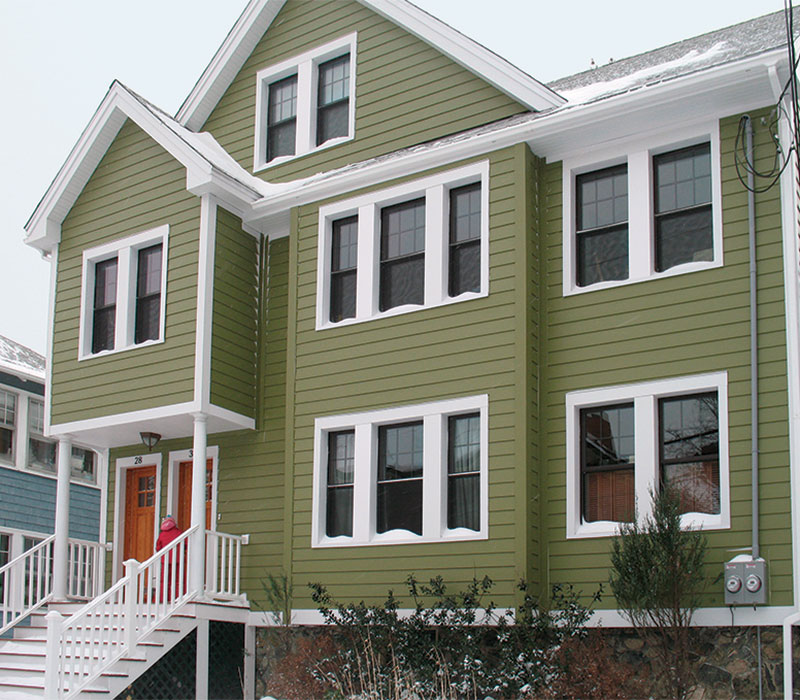
Construction
Basement: Ceiling sprayed with open-cell spray polyurethane foam (adds thickness and R-value)
Walls: 2×4 construction filled with cellulose; 4 in. of foil-faced polyisocyanurate foam outside of sheathing for a total of R-39
Roof: 6 in. of polyisocyanurate insulation installed above the existing roof sheathing, topped with a layer of plywood; 8 in. of open-cell spray polyurethane foam (Icynene) installed between the existing rafters for a total of R-59
Windows: Double-pane (U- 0.33) windows by Pella
Mechanicals
Heating: Oil-fired steam boiler in each unit
Water: Main boiler in unit 1; on-demand gas water heater in unit 2
Ventilation: Heat-recovery ventilators (one for each apartment)
Results
Energy reduction: 65% (heating fuel)
Annual savings: $2300 per year
Payback period: 61 years. If the cost of the roofing and siding are subtracted, payback is reduced to a little over 35 years.
A deep-energy retrofit doesn’t make sense in all climates, and not every home is a good candidate for the work. Cold-climate homes have higher energy bills than homes in a hot climate, so a cold-climate home is a better candidate than a home in a hot climate or a home that already has low energy bills. A house with a simple rectangular shape and a simple gable roof is easier and less expensive to retrofit than a house with complicated exterior elevations, bay windows, dormers, or a roof full of hips and valleys. Most of the deep-energy retrofits include the installation of a new layer of exterior insulation. Intricate architectural details add to the difficulty of such retrofit work, driving up costs. Homes with simple exterior trim and uncomplicated cornice details are much easier to work on than Victorian homes with gingerbread trim. Because many deep-energy retrofits require existing roofing and siding to be replaced, the best candidates for deep-energy retrofit work are houses that are in need of new roofing and siding.
The payback
Homeowners who undertake deep-energy retrofits are usually motivated by environmental or energy-security concerns rather than a desire to save money on their energy bills. These jobs are so expensive—in the range of $50,000 to $150,000 per house— that a homeowner would have to wait decades before the investment could be recouped. “In a retrofit situation, it can cost a lot of money to save a small amount of energy,” says energy the best options. consultant Michael Blasnik. “Going from r-19 to r-40 walls or r-30 to r-60 ceilings doesn’t save a whole lot of Btu—and the cost of that work is potentially tremendous.”
Retrofit results
Cost: $148K
Annual savings: $2490
Location: Somerville, Mass.
Size: 2966 sq. ft. (duplex)
Renovation cost: $50 per sq. ft.; $148,300 total
Alarmed by the implications of the global climatechange crisis, Cador Price-Jones embarked on a major retrofit of his Massachusetts duplex.
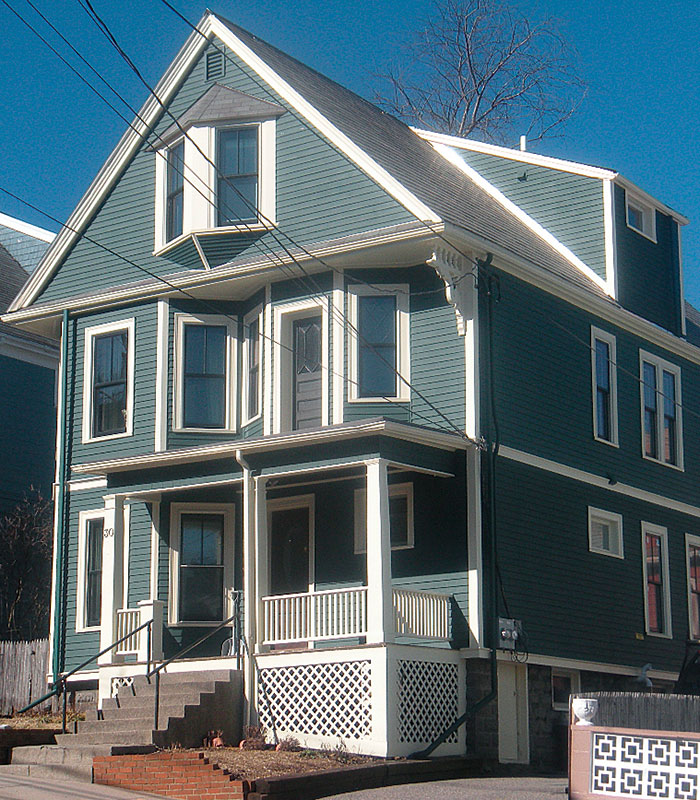
Construction
Basement: 3 in. of closed-cell spray foam (R-18) applied between the studs of a 2×4 wall built against an 8-in. block foundation
Walls: Existing 2×4 walls filled with dense-pack cellulose; new 2×2 frame installed on exterior and filled with 4 in. of closed-cell spray foam for a total of R-37
Roof: Attic floor air-sealed and filled with 17 in. of loose-fill cellulose for an R-value of 60; 2 in. of spray foam air-seal the eaves
Windows: Main house windows are double-glazed, low-e, argonfilled units by Jeld-Wen; basement windows are double-glazed hopper units by Harvey Industries
Mechanicals
Heating: Modulating condensing gas boiler, 22,700- to 75,200-Btu rated output, 95% AFUE
Water: 60-gal. Superstor indirect hot-water tank
Ventilation: Heat-recovery ventilators (one for each apartment)
Photovoltaic: 5.25kw package system by Nexamp
Results
Energy reduction: From $5650 per year to $3160 per year
Annual savings: $2490
Payback period: 60 years
There’s no easy way to calculate the payback period for many deep-energy retrofits, in part because a major overhaul of a building’s shell inevitably includes many measures (for example, adding new siding or roofing) that aren’t energyrelated. Although these elements don’t make a significant contribution to a home’s energy performance, they may greatly enhance the home’s aesthetics and value.
Those of us without a Midas budget will need to settle on a less ambitious approach to energy savings than a full-blown deep-energy retrofit, and that’s OK. Less expensive and less invasive retrofit measures, typically referred to in the industry as weatherization, have payback periods of 15 years or less.
– Martin Holladay is a contributing editor.
For more photos and details, click the View PDF button below: