All About HVAC
Choosing heating, cooling, and ventilation systems can be complicated. Here's an overview of common options and things you need to consider to make smart selections.
Synopsis: Contributing writer Scott Gibson explains the basics of selecting HVAC systems by using the ACCA Manual J, Manual S, and Manual D software for calculating your heating and cooling loads, choosing right-sized equipment, and integrating ductwork as needed. Included in the article is a snapshot of heat-pump systems, three common cooling strategies, and ventilation options.
When it comes to heating and cooling equipment, which is more important: lower initial cost or lower operating costs? Should the equipment be all-electric, or is it OK in the era of climate change to buy appliances that burn fossil fuels? Is it safe to invest in new technology, or will that turn out to be an expensive mistake? There are many nuanced questions to answer when planning a new HVAC system or looking to upgrade existing components. Having a strong sense of your needs and the available products is a good place to start.
Energy and design consultants working with computer models can offer precise estimates of heating and cooling needs and the type of equipment—if not the manufacturer and model number—best suited to meet them. When the goal is to certify a new or renovated house under a rating program such as Passive House, that level of detail is a must. Energy consumption right down to the kilowatt-hour is a make-or-break question for certification.
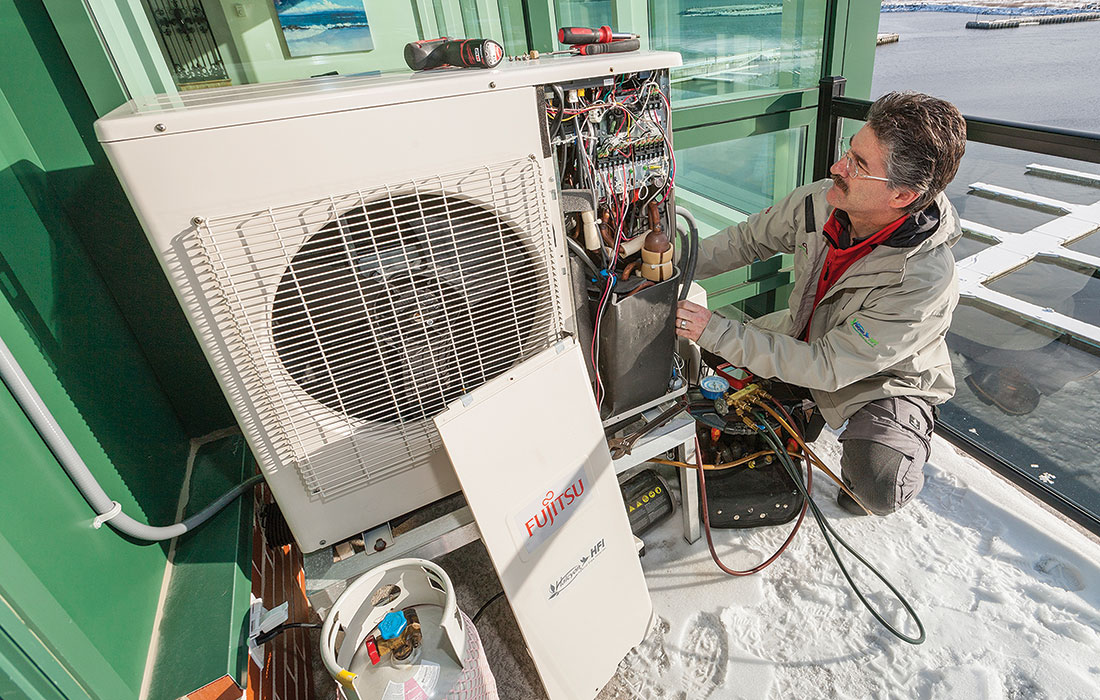
Whether or not a computer-armed consultant is in the cards, having a grasp of heating and cooling basics is a good idea for anyone building a new house or renovating an old one. Why bother? You won’t be spending money unnecessarily. You’ll at least know the right questions to ask the HVAC contractor. Plus, you’ll be investing in equipment that makes sense for your climate and house—not some hypothetical average.
With that in mind, consider the fundamentals of HVAC design. These are the standard industry planning tools developed by the Air Conditioning Contractors of America (ACCA): Manual J, Manual S, and Manual D. These ACCA manuals are software programs available from a number of companies and used primarily by HVAC professionals. All of them are important and the foundation for good design.
Start by calculating your needs
Manual J is the first step in planning a system. Its purpose is to calculate how much heat your house will lose on the coldest night of the year, and how much cooling you will need on the hottest day of the year. These are the heating and cooling loads, independent of what heating and cooling equipment a homeowner may choose. Loads are determined on a room-to-room basis so a contractor knows how much heating and cooling you’ll need to stay comfortable. Some of the most repeated advice from experts is that a Manual J calculation is essential to getting a heating and cooling system that works properly. Heating and cooling contractors develop their own rules of thumb over time. That’s understandable. If you’ve installed 500 systems and they all seem to work well enough, you’d probably be just as confident in recommending one. The issue is that little extra a contractor may want to add to the capacity of a furnace or air-conditioning unit simply to guarantee they never get a call in the middle of the night from a homeowner complaining the house is too hot or too cold.
Manual J is designed to take the guesswork out of the process and make sure the equipment that’s installed is well matched to the house and the locale. Here’s how it works: After the technician plugs in various bits of information—how much insulation is in the walls, for instance; the specs for the windows you’ll be using; and other variables—the program should produce a good estimate of heat loss or gain. The calculation will show how much heating and cooling you’ll need to remain comfortable under the hottest or coldest conditions that might be expected in that area. These values help steer the contractor toward appropriately sized heating and cooling equipment.
In theory, a Manual J calculation should be straightforward. But judging from anecdotal accounts, the opposite is true. Some heating contractors don’t know how to do a Manual J calculation. Contractors may want to rely on rules of thumb they have picked up over the years instead, resulting in equipment that is oversized and more expensive than it needs to be. Information entered into the software template may be inaccurate because various assumptions about the house’s construction are wrong, so the results are wrong, too. And the list goes on.
Look to reliable resources
In one of many articles on the topic at Green Building Advisor (GBA), Martin Holladay explains that the International Residential Code (IRC), the dominant model building code in the U.S., requires a Manual J calculation, or other “approved heating and cooling calculations methodologies.” Contractors are required to show local building officials that the calculations were completed. But code officials have been known to say that although they collect the data, they don’t actually know what it means. Asked whether HVAC contractors typically have a good grasp of ACCA planning tools, Michael Maines, a residential designer in Maine and a contributing editor at Fine Homebuilding, says no. “A few of the best ones do Manual Js in a thorough, honest way, but the vast majority just give their supply house the floor area and they input standard, leaky-home values, leading to grossly oversized systems. Most systems I’ve seen do not look like they were properly engineered.”
Because of these issues, Holladay believes that it’s a mistake to trust the calculations that your HVAC contractor makes. “The bottom line is that any load calculation supplied by an HVAC contractor should be looked at with suspicion,” he writes. He spoke with Allison Bailes III, an energy consultant in Atlanta, who adds: “Contractors are often engaged in a race to the bottom. There just isn’t any money in their budget for proper design.”
These are broad brushstrokes that portray all heating and cooling contractors unfavorably. Many contractors no doubt know very well what a Manual J calculation is. Still, warnings like this may prompt homeowners to ask themselves: If my HVAC contractor shouldn’t be doing this, what other options do I have?
There are several, depending on how much money you have to play with and your comfort level with detailed technical topics— your willingness to wade into the weeds and figure things out. Here are some possibilities:
1. Do your own calculations. Take a look at articles that Green Building Advisor has published online in the past, including “How to Perform a Heat-Loss Calculation,” and “Calculating Cooling Loads” by Martin Holladay.
2. Use a free online calculator. There are many to choose from, but the problem here is that you have no real assurance that the results will be accurate. One free program that Bailes recommends is Cool Calc Manual J Software.
3. Hire a professional. Bailes says a number of companies do third-party HVAC design—including his, Energy Vanguard. “An internet search on that term, ‘load calculation,’ or ‘Manual J’ should turn up several companies that can help,” he adds. “People can also go to forums like the Q&A at GBA or Building Performance Institute (BPI) and ask for recommendations.” It could take time to find someone who is both available and qualified, and it might cost more ultimately, but in the scheme of things it could be the best option.
Heat pumps are a high-performance favorite
Conventional ducted system
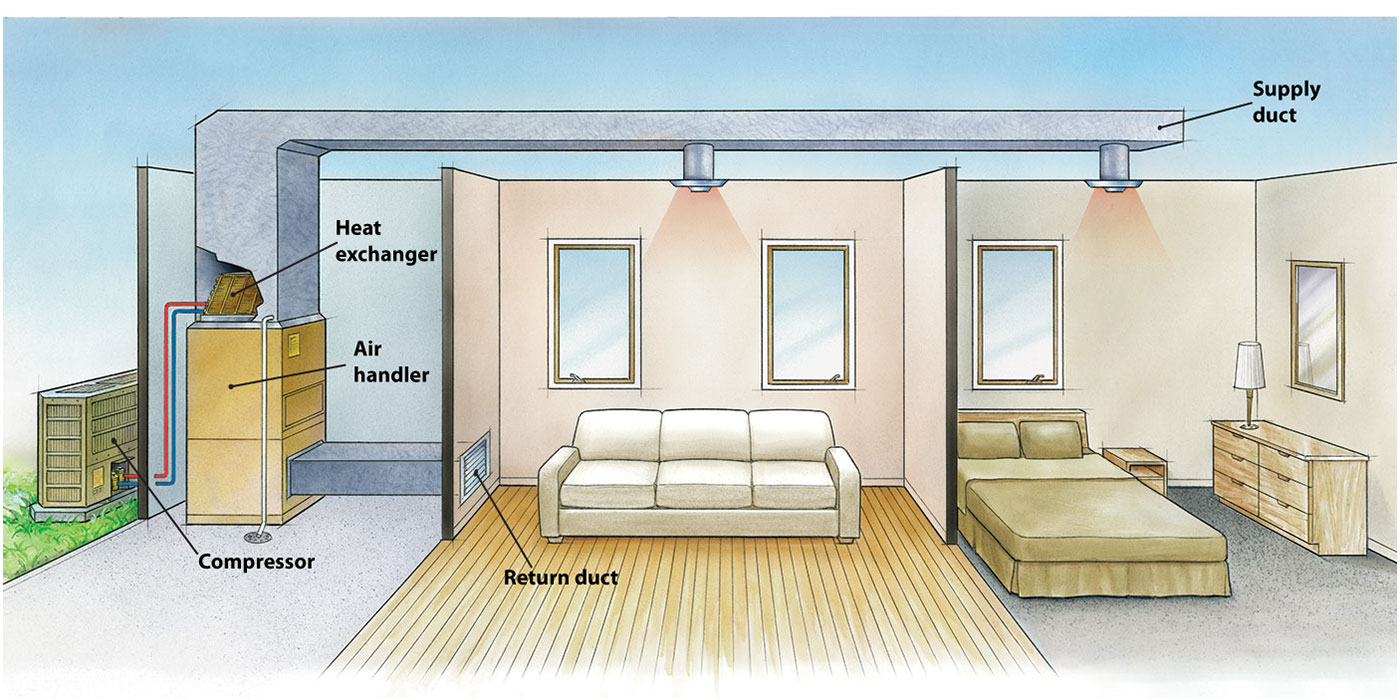
Ductless minisplit system
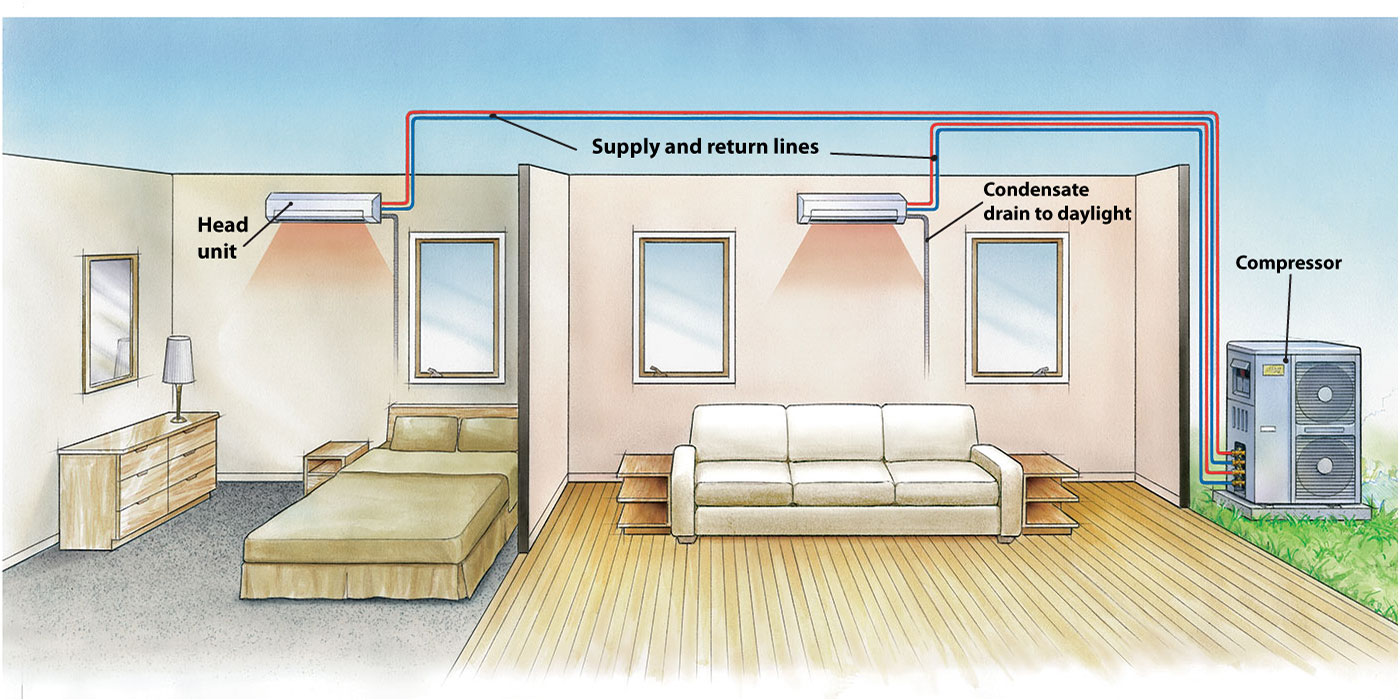
Next, choose your equipment
Once the heating and cooling loads are known, the next step in the process of designing a system is selecting the appliances. This is where the ACCA’s Manual S comes in. Both the IRC and the International Energy Conservation Code (IECC) require the use of Manual S to size equipment after load calculations are complete. Assuming your community has adopted the IRC, your contractor is required to use Manual S in this process (unless local officials have amended the code otherwise).
Equipment selection is key, no matter what type (or fuel) you choose. The capacity of the equipment—how many British thermal units (Btus) per hour the device will produce—should align with how much energy the house needs to stay comfortable. That concept seems like a no-brainer, but like many other HVAC issues, this also becomes complicated.
David Butler of Optimal Building Systems explains that there’s a difference between the nameplate capacity of a device (what the manufacturer says it will do) and what it will actually do once it’s installed. A number of variables can affect the performance of an air conditioner, Butler says, including indoor and outdoor temperatures and indoor humidity. If one of those variables changes, the air conditioner’s capacity to change sensible capacity (the temperature) and latent capacity (humidity) also change. That’s why the same air-conditioning system operates differently in the arid Southwest than it will in the hot, muggy Southeast, no matter what the nameplate capacity might be.
Manual S, not to the nameplate attached to the device. In Manual S, the procedure for choosing a furnace is simple, Butler says: The output should be between 100% and 140% of the design heat load. It gets more complicated for air-conditioning equipment because the contractor needs to know both the latent and sensible capacity of the equipment when it’s operating at design conditions, meaning the conditions specific to that location and not some hypothetical numbers that have nothing to do with where the house is.
Three ways to keep cool
Cooling strategies run the gamut—from a wholehouse fan in the attic that flushes out hot indoor air at night to a fully ducted mechanical system. In some parts of the country, AC is needed only a few days each year. In others, life is miserable without it. So, what are some of the options?
Whole-house cooling
Most central air-conditioning systems are split systems, which include a condensing unit that sits outside on a concrete pad, and an indoor coil connected to ducts that move cool air around the house. If you have a forced-air heating system, you already have the ducts for the air conditioning. Houses heated by some other means—a boiler, for example, or some other appliance that doesn’t need ducts—will have to be ducted separately for the AC, or you’ll have to choose a different type of air conditioning.
An air conditioner moves heat with the help of a refrigerant that alternates between a liquid and gaseous state. Inside the house, the refrigerant absorbs heat in a coil that cools indoor air. The refrigerant is then routed outside where the heat is ejected in an outside coil. This refrigeration cycle is the magic that pulls heat from inside the house and dumps it outside. The process involves the same mechanics as your refrigerator, which is just moving heat from inside an insulated box to your kitchen.
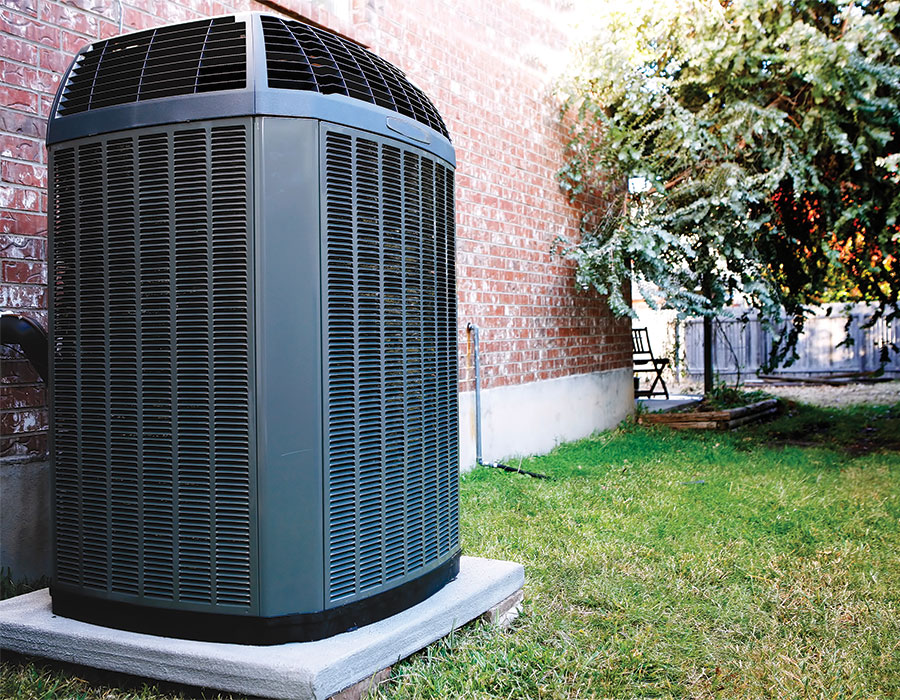
Air conditioners also dehumidify. Cold air holds less moisture than warm air. When the air handler inside blows warm (moist) indoor air over the evaporator coils, moisture in the air condenses on the coils. This water can be collected and sent down the drain and out of the house, so the air inside is drier and more comfortable. When the AC unit is too big, it cools down the air in the house very quickly and satisfies the thermostat before the system has had a chance to remove all the moisture. This is why experts suggest the best scenario is when the air conditioner runs for longer periods of time; if the AC is running more or less constantly on the hottest afternoon of the year, it’s been sized properly.
Space cooling
Window-mounted air conditioners are an excellent choice for people who don’t want a whole-house system and are content to cool just a room or two. They are less expensive to install and run than a central system, and for several reasons, they use less electricity for cooling. Smaller units will run on an 115v circuit. The downside is that they don’t cool the entire house, so there will still be pockets of uncomfortably warm and humid air. Also, they are noisy.
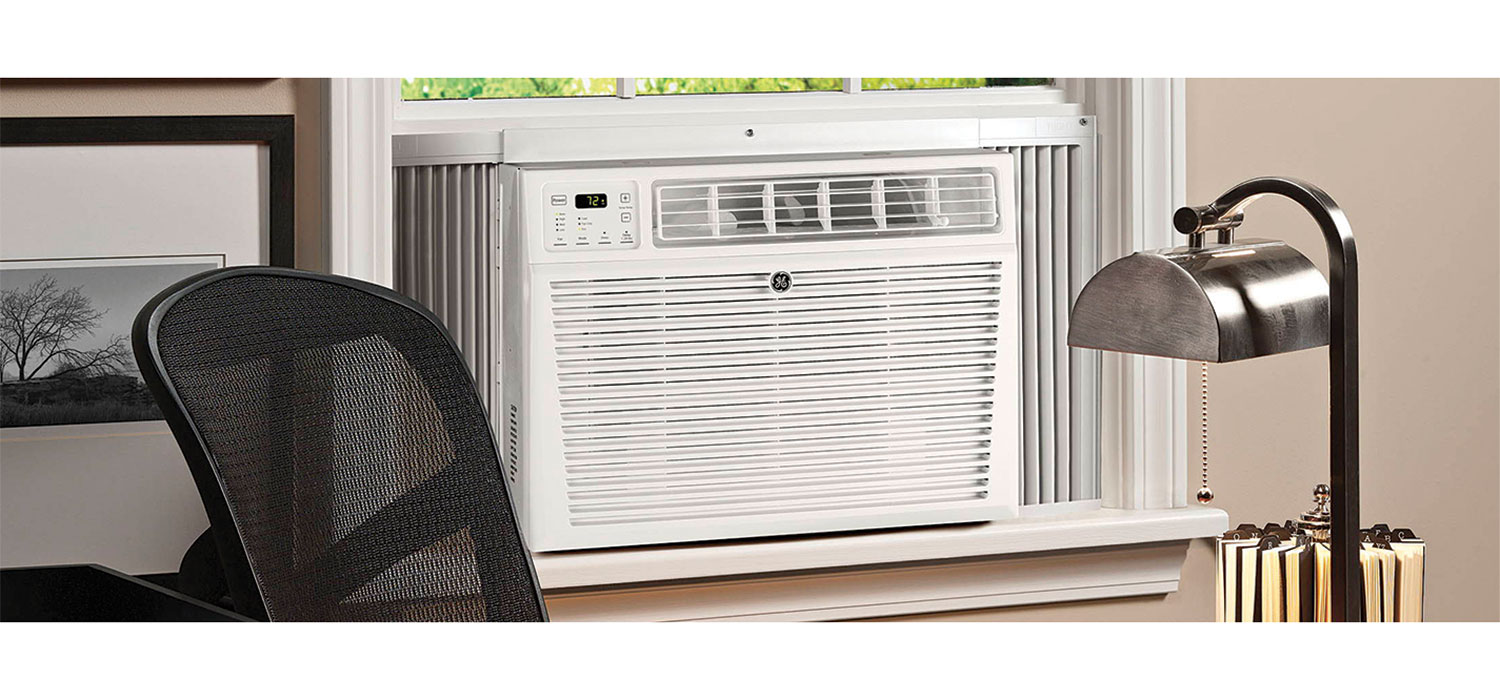
Cooling capacity (measured in Btu per hour) should be based on the room size, with some adjustment for factors such as solar gain, occupancy, or location in a kitchen. Energy Star’s recommended sizes start with a 5000-Btu unit for rooms of up to 150 sq. ft. and go up from there. Remember, bigger isn’t always better. AC units that are too big will bring down the temperature quickly and then power down even though the unit hasn’t run long enough to bring humidity levels down to a point where the room is comfortable. Longer run times will make for a more comfortable environment.
A dry-climate option
Most of us equate air conditioning with devices that use sealed refrigerant loops, but that’s not the only way of lowering indoor temperatures. One alternative is the evaporative cooler, also called a swamp cooler. These are often mounted on the roof and look like a louvered metal box, but window-mounted and portable units also are available. According to the Department of Energy, evaporative coolers can lower air temperature by as much as 40°F, although the air coming out of an evaporative cooler is typically not as cool as air blown from a window AC unit.
Inside the cooler is a thick pad moistened with water. Hot, dry air drawn through the pad by a fan evaporates water in the pad as it moves, lowering the temperature of the air. The fan pushes that cooler air into the house. Evaporative coolers are much simpler than a split mechanical system, so they cost less and are much less expensive to run because they use relatively little electricity. Some come with air filters that reduce airborne allergens, variable-speed fans, and remote controls.
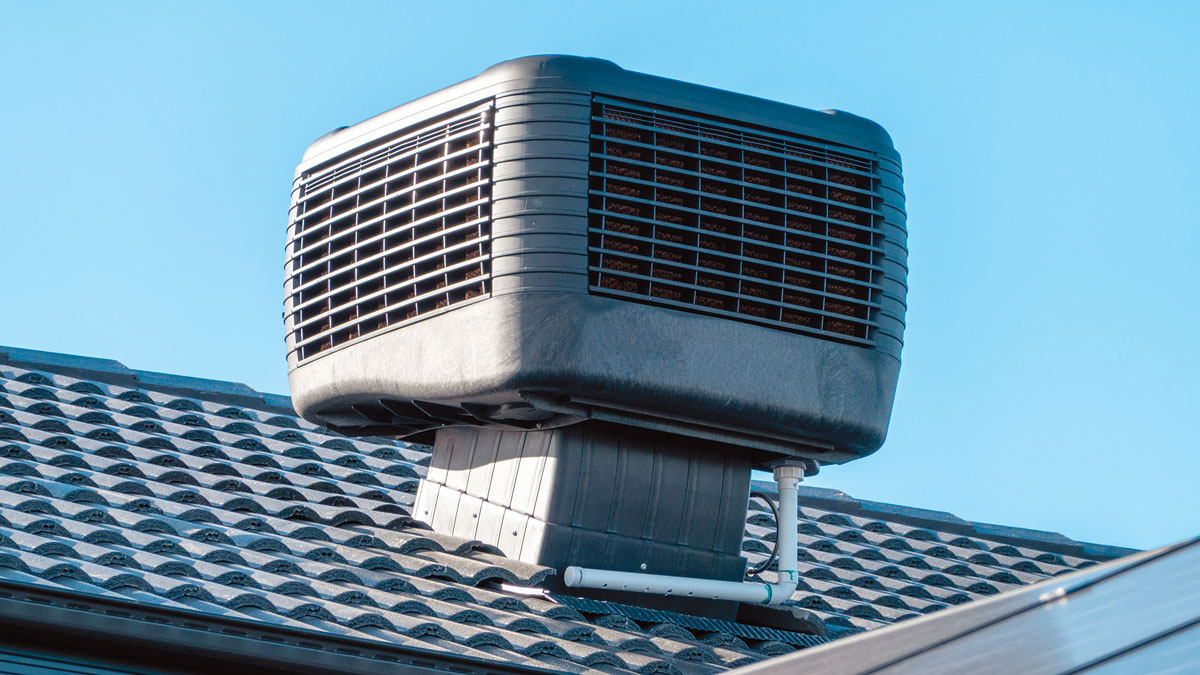
The fact that an evaporative cooler does not need a chemical refrigerant is a big environmental plus because refrigerants typically have high globalwarming potentials. But there is a catch: Evaporative coolers are best suited for dry climates. Where relative humidity is high, they are not as effective because when air is laden with moisture, evaporation slows down and with it the cooling effect.
For distribution, use Manual D
The “D” in Manual D is for ducts, the means by which a forced-air heating and cooling system moves conditioned air around the house. Not all houses have ducts. Instead, they may rely on hot water (hydronic heating systems, such as radiant-floor heating), radiation (such as a wood or pellet stove), or an air handler (with a ductless minisplit mounted on the wall or a direct-vent heater burning propane or kerosene). Even houses that don’t have forced-air furnaces, however, may need ducts for central air conditioning, whole-house ventilation, or dehumidification. That’s where Manual D comes in.
The physics of moving air around a house is more complex than it might seem. Unless you are interested in such topics as static pressure, effective duct length, and blower capacity, duct design will prove a difficult topic to understand. But there are general rules about ducts that should be helpful:
1. Ducts should not be located in an unconditioned attic or crawlspace. Ducts can be insulated, but a thin covering of insulation is no match for searing summertime temperatures or the deep cold of winter typical for an unconditioned attic. It doesn’t make sense to spend a lot of money to heat or cool air only to squander the energy before it can do its work. So, put ducts in places where they don’t get too hot or too cold—interior chases, conditioned attics, and conditioned crawlspaces.
2. Joist bays and stud bays don’t make good ducts.
3. Rigid ducts are less likely to restrict airflow. Insulated flex duct works, but it doesn’t work very well when an installer allows it to sag haphazardly. Flexible duct should be supported by straps, not wire, to avoid pinching off airflow.
4. Ducts should be sealed, ideally with mastic. Leaky ducts cause all sorts of problems, from wasted energy to pulling mold and other allergens into your distribution system. Duct tape isn’t suitable for sealing ducts at seams between sections because it will eventually dry out and begin to leak. Mastic is messy but effective. Another approach is to use a proprietary product called Aeroseal, a method of sealing ducts from the inside with an adhesive aerosol that plugs leaks as wide as 5⁄8 in., according to the manufacturer.
Build tight, ventilate right
Houses with low rates of air leakage are better able to maintain indoor temperature, humidity, and overall comfort. But as houses get tighter, the need for mechanical ventilation to maintain indoor-air quality goes up. As with all HVAC systems, there are choices.
Exhaust-only systems
Exhaust-only ventilation is relatively simple, often consisting of just one or more bathroom fans. The fans can be set to run continuously at a low volume, or they can be used as spot ventilation when someone is showering. A single-port fan (a self-contained, usually ceilingmounted unit) has a single inlet and an exhaust duct that sucks moist air out of the house. A multiport exhaust fan can handle larger bathrooms with toilet and shower enclosures, or even multiple rooms. These units include an inline fan and two or more inlets. Because the fans can be placed some distance from the inlet grilles, these systems are pretty quiet, and they are available in a variety of sizes.
Bathroom fans and range hoods have one thing in common: They depressurize the house relative to the outdoors, meaning that with the fan running, there’s a faint vacuum inside the building. The air that is pulled from the house must be replaced by air from the outside. Without any dedicated supply ducts, this replacement air will find its way through whatever cracks and voids there are in the building enclosure. In other words, you don’t really know where the air is going to come from, just that it will inevitably get in.
Supply-only ventilation
In a supply-only system, a fan brings fresh air into the house with exhaust air leaving the building through gaps in the building enclosure. The fan (or fans) can be installed in a mechanical room through an exterior wall with incoming air filtered or mixed with room air to lessen the temperature difference.
An existing air handler—what you’d have with a forced-air heating system or central AC—also can be used. Air from the outside is ducted into the return side of the furnace. To keep operating costs lower, the air handler can be run at a fraction of its usual speed as long as it provides enough fresh air to keep the house comfortable or meet the guidelines of ANSI/ASHRAE standard 62.2.
Supply-only systems pressurize the house. Some builders worry that this could cause problems during the winter by driving moisture into wall cavities. Energy expert Bruce Harley says not to worry about that. The upper part of a house already is under positive pressure in the winter from the stack effect, he says, and the relatively small airflow of the ventilation system won’t have much of an impact.
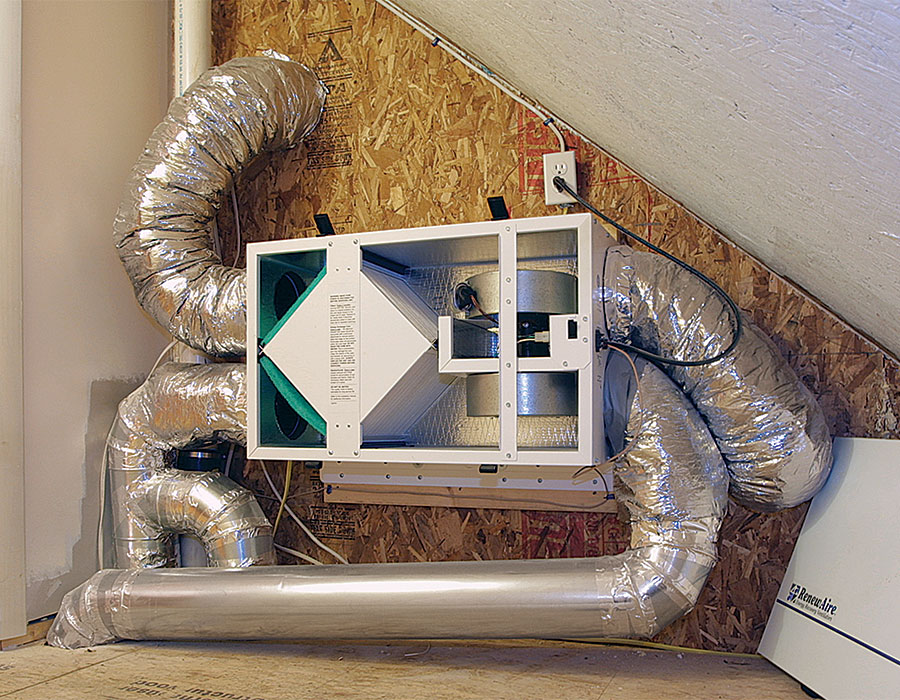
Balanced systems—the preferred method
Balanced ventilation systems match outgoing air with incoming air to eliminate pressure imbalances. One problem with whole-house ventilation systems is that in removing conditioned (heated or cooled) air from inside the house and replacing it with outdoor air, the ventilation system runs up an energy tab. The incoming air is fresh, but it also must be heated or cooled to keep the indoor temperature comfortable.
Balanced systems have a way of dealing with this problem. Outgoing air and incoming air go through a heat exchanger, so much of the energy that would be lost is transferred to the opposite air stream. In winter, indoor air transfers its heat to incoming fresh air; in summer, the opposite occurs. This type of system is called a heat-recovery ventilator (HRV). The two airstreams have no direct contact with each other. Heat transfer can be remarkably high—greater than 90% with the most efficient models on the market.
A second type of system is the energy-recovery ventilator (ERV), which in addition to capturing some of the heat in the air stream also transfers some of the moisture. This is helpful in certain climates. In a hot, humid environment, for example, outgoing indoor air in summer has been cooled and dehumidified by an air conditioner. An ERV is designed to transfer some of the moisture in the incoming fresh air to the stale indoor air that’s on its way out the door. With an ERV, there is some mixing of the two air streams. If you buy a top-of-the-line ERV system like the Zehnder ComfoAir, expect to pay $7000 or more, depending on the number of ducts and other features. From a cost-savings point of view, spending that kind of money makes more sense in very cold climates than it does in moderate ones.
Questions not covered in ACCA manuals
The ACCA manuals can guide HVAC decisions on a quantitative basis: How big a furnace do I need to stay warm in winter? What output do I need from an air- conditioning system to stay comfortable in July? But there’s other criteria that may have just as much relevance.
For example, if you’re replacing an existing gas furnace but planning to move in two years, do you buy a top-of-the-line condensing gas model with a great efficiency rating when it costs twice as much as a less efficient but more affordable alternative? Even an economy furnace should last a decade, so the new owners of the house will be the ones who are stuck with lower efficiency and higher energy bills. Spending a lot of money on a piece of equipment you’re about to leave behind may not make much sense when the simple payback on the purchase doesn’t equal its added cost.
First, the importance of cost vs. higher efficiency is a question that even homeowners planning to stick around will want, or need, to ask. Money saved up front with a less expensive appliance is always attractive. But higher efficiency that reaps bigger rewards over time may be a better longrange investment.
“It depends on what their priorities are,” Maines says of how he might advise clients on this question. “In most cases, I would say that higher efficiency is best, but if it comes at a huge premium, it may make financial sense to scale back on performance specs. An energy model should be helpful in making that decision.”
More pressing is the immediate need to lower carbon emissions in order to blunt climate change. Should homeowners limit their search to appliances that do not burn any fossil fuels because they may help reduce carbon emissions? Some municipalities around the country are already making that decision for home buyers by banning gas connections in new construction, and more restrictions are likely to follow.
For now, it’s both an ethical and practical question homeowners have to answer for themselves. If the source of electricity is renewable, an all-electric house is very appealing—as long as the grid stays up and running. But in some locales, power outages may be all too common, forcing homeowners to backstop their houses with both a gas-fueled generator and a fuel-powered auxiliary heater. “Whole-house batteries are getting close to being an effective alternative,” Maines adds, “but we aren’t quite there yet on the financial front.”
Avoiding fuel-burning heating equipment also may be the logical choice when the plan is to add solar capacity to the house. Excess production might be used to charge electric vehicles or offset the use of electricity by other appliances, such as a water heater or kitchen range. Decisions on heating and cooling equipment also can be guided by the interior design of the house. Ductless minisplits would do well in a well-insulated house with few interior partitions; not so well in an older house with a number of small rooms and lots of doors.
In short, one size does not fit all.
-Scott Gibson is a contributing writer at FHB and Green Building Advisor.
To read the entire article, please click the View PDF button below.
RELATED LINKS: