A Sustainable Farmhouse with Roots in Tradition
A Vermont architect uses the state’s energy-efficiency guidelines to craft a new zero-energy home steeped in traditional character.
Doug and Joan called my firm in late January 2014 to explain that they had purchased property with a beautiful view and a 1950s ranch that was in terrible condition. A young professional couple who enjoys outdoor activities, they planned to remove the existing house and build a new family home. They had several goals that influenced our design work as well as the construction process. At the top of the list was a traditional exterior—a Federal-style farmhouse that would fit comfortably into its country-road setting. They also sought a compact footprint and energy-efficient performance, and they knew they wanted as few petroleum products as possible used in the construction and functioning of the house. They wanted a house that would be straightforward to maintain, with an open plan for the main living space.
It seems to me that for the last several years, high-performance homes have been developing an identifiable style that leans toward the clean lines and minimal details of modern architecture. With this project, we were able to redefine what’s possible when it comes to the appearance of a superefficient home. Specifically, we showed that a home built with today’s best practices that meets perhaps the most important level of energy performance—net-zero energy consumption—can have authentic, period-appropriate character.
The site that Doug and Joan bought could not have been a better place for a sustainable, energy-efficient house. Not only is it environmentally and economically advantageous to build on an already developed site, but the excavator even found someone to repurpose the existing house as a hunting camp. With beautiful views to the south and east and the road to the north, we were able to set the house along an east–west axis so the south-facing roof would receive maximum solar collection but the photovoltaic panels would be hidden from almost every public view. In this way, the street-facing elevation is all traditional Vermont farmhouse. Fortunately, many of the hallmarks of traditional architecture complement sustainable and energy-efficient design. The simple shapes lend themselves to effective air-sealing and insulation details.
As long as a project’s efficiency goals and the necessary details are included from the beginning, they will survive the processes of design, budgeting, and construction. In other words, sustainability and efficiency cannot be add-ons or upgrades; they must be integrated from the start. And of course, modern building materials make both style and efficiency much easier to achieve. For example, double-hung windows are the tradition in Vermont, but triple-glazed double-hung units are still somewhat scarce and expensive. We installed triple-pane casement units from Kohltech— which in general perform better than double- hung windows anyway—with a meeting rail that simulates the look of double- hung windows.
We also employed a broad definition of the term sustainable. The locally harvested lumber, trim, and wood-flooring materials; the Vermont slate tile; and the granite counters were selected not only for their character and connection to the site, but to support the local economy as well. We also considered the energy used in the construction and functioning of the house, the comfort and health of the occupants, the house’s resilience to storms, and the need to create a durable home.
Traditional in detail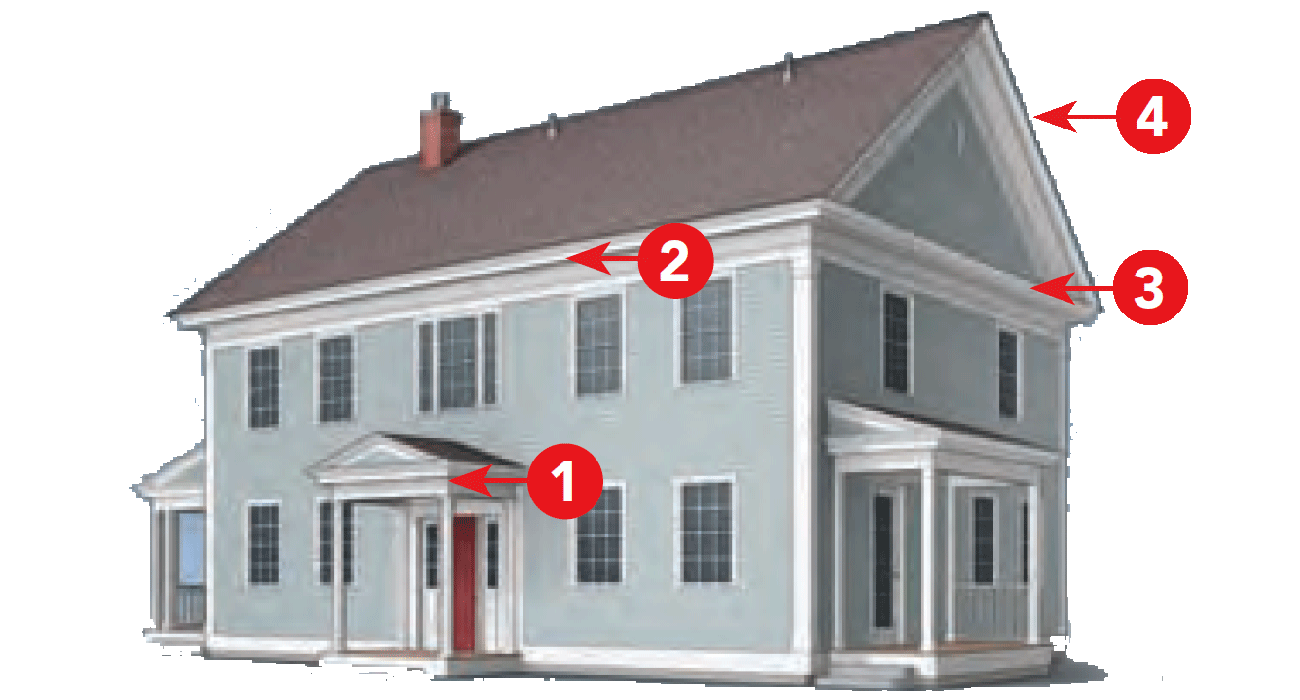
The Federal-style trim around the rooflines is a hallmark of the Vermont farmhouse vernacular. Executed with a combination of common building materials and stock moldings from Brosco, these details are more attainable than ever.
![]() |
![]() |
![]() |
![]() |
Help from the state
We are fortunate in Vermont to have a state-mandated organization that helps designers, builders, and homeowners achieve sustainable energy solutions. Efficiency Vermont has done extensive research to learn which sustainable design strategies and systems work best in our climate. Its High Performance Homes program sets minimum insulation and maximum air-leakage levels, as well as requirements for a number of other key components.
The Efficiency Vermont staff reviewed our schematic design and specifications and confirmed that we were on track to achieve net zero. They also provided advice throughout the process on systems and construction details. Projects that meet the High Performance Home designation are entitled to rebates. In our estimation, however, the rebates are not large enough to be a great factor when making decisions.
To heat and cool the house, we used two highly efficient electric air-source minisplit heat pumps from Mitsubishi that are rated to operate in temperatures as low as -13°F. In a radical shift from normal approaches to heating and cooling, there is no heat in the bedrooms and bathrooms. With high levels of insulation and triple-glazed windows, the interior surfaces stay warm enough to keep the radiant surface temperatures comfortable. Even on the coldest winter nights, the two small electric-resistance heaters that we installed to supplement the minisplit heat pumps rarely come on. In the end, the house is powered entirely by electricity, with a heat-pump water heater, electrical appliances, and all-LED lighting.
Through Efficiency Vermont, we found Build Equinox, the company that developed the CERV—Conditioning Energy Recovery Ventilator. This refinement of the ERV provides fresh air from outside, circulates air within the house to maintain even temperature and humidity levels, monitors indoor air for key pollutants, and even has a small heater to temper the incoming fresh air.
In search of the view
The house’s open living space is not the only break from tradition. The look of double-hung windows is implied with a faux meeting rail in these large casement windows. The deep window wells are the result of 3 in. of insulation on the outside of the walls. Still, the light fixtures and the Shaker-style cabinetry, wood flooring, and simple baseboard and casings add historic character.
Bedrooms: 3
Bathrooms: 3
Size: 2,240 sq. ft.
Completed: 2014 Location: Connecticut River Valley of Vermont
Builder: K.D. Johnston, Inc.
Architect: R. Andrew Garthwaite, AIA, hgarchitects.com
Energy consultant: Brent Mellen, Building Energy, buildingenergyvt.com
The entries, stair, mudroom, and sitting room are located on the north side of the house to buffer the living spaces from the road. The kitchen, dining, and living area runs along the south side of the house, and the sitting porch faces east across the valley. All of these spaces have views that span from the adjacent field to distant mountains. Upstairs is an efficient arrangement of a master suite, two additional bedrooms, and a shared bath with a study to boot.
![]() |
![]() |
Energy to spare
Although Karl Johnston had not yet built a net-zero-energy home, his reputation as a careful and thoughtful builder led us to choose him for this project. The owners also engaged Brent Mellen of Building Energy, a local insulation and energy efficiency consulting company.
Achieving the air-barrier continuity over the transitions in materials and construction types was one of our significant challenges, and Brent was a big help in identifying practical strategies. For example, the underslab vapor barrier was lapped onto and taped to the foundation wall. Then at the top of the wall, a piece of poly sheeting was taped to the inside of the foundation, lapped over the top of the foundation, and taped to the plywood sheathing after the walls had been built. Thus, complete air-barrier continuity was achieved from below the slab to the top of the wall, with the second-floor ceiling providing the final link.
The weakest part of our air-sealing system is the woodstove. The owners loved the woodstove at their previous house, and it was important to them to include one. We were able to provide sealed combustion air to the firebox and decent air-sealing of the flue. In the end, the new house is so comfortable even in the depths of winter that Doug and Joan use the woodstove infrequently.
There were three blower-door tests. The first—a preinsulation test—was the most critical. We met our goal of less than 1 ACH50 at this early stage, and the two subsequent tests confirmed that we maintained our target as construction progressed.
In many ways, this house has functioned better than we all expected. It is warm, quiet, comfortable, and easy to operate. When the 9kw solar array was installed on the southfacing roof, the electric production resulted in an annual net surplus. Doug and Joan have been able to assign the excess power to family members living nearby. One lesson we learned is that during our cold winter’s climate, it is best to turn the heat-pump water heater to standard electric-resistance heating; otherwise, it cools the basement.
Doug and Joan moved into the house in mid-November, just in time for the harshest winter we’ve had in many years. Shortly after they moved in, a severe overnight windstorm swept through the valley. Winds in excess of 60 mph blew shingles off the garage roof, but the house was so quiet that Doug and Joan didn’t even realize that there had been a storm until the next morning. Every time the temperature hit a new low, I would email them to see how the house was doing. Every time, they replied that the house was warm and working as they had hoped. And with all the south-facing windows, sunny days are particularly pleasant, they said.
—R. Andrew Garthwaite, AIA, is principal at Haynes & Garthwaite Architects in Norwich, Vt.
Photos by GBH Photography (gbhphotography.com).
Drawings: Christopher Mills.
Floor-plan drawings: Martha Garstang Hill.
For more photos and details, click the View PDF button below:
From Fine Homebuilding #267