Deep Dive into Blower Door Testing
Learn testing tips and technical nuances of this essential home-energy diagnostic equipment from Collin Olson of The Energy Conservatory.
Over the last several years I have accumulated a range of questions about how blower doors and blower door testing work. So when another new query popped up in my head, a question about AeroBarrier and how it uses the blower door to both air seal and test for airtightness, I figured it was time to check in with an expert.
Collin Olson is Staff Physicist for The Energy Conservatory (TEC). He holds a PhD in Physics from the University of Wisconsin—Madison, where he initially specializing in high energy particle physics.
Collin starts our conversation by explaining why he is not an engineer, how he met Gary Nelson (the founder of TEC), and ended up working at TEC himself (it’s all about music).
“As an undergrad at St. Olaf, I full intended to study Engineering, but the latter meant a year away from St. Olaf. I had probably the time-equivalent of a music minor because of playing in the band, and just could not leave.”
Olson met Gary Nelson through music as well (Gary plays the trombone, Collin the euphonium). A colleague at one of Olson’s first jobs ran into Gary at a music event, and told Gary she had a PhD in Physics on staff who seemed way better suited to the work that Gary was doing at TEC. That was 1994 and Olson has been with TEC ever since.
With introductions out of the way, I started with basic questions about blower doors and proceeded from there. What you’ll find below is an edited version of our conversation, a paraphrasing of Collin’s responses, not a transcript. I did this for clarity and to present in writing the most useful information from a long interview as efficiently as possible. For the full interview, and more context, you can listen to the audio recording below.
How does a blower door work?
The fan motor and blades push air out of the building with the fan sensor located where the air is being pulled into the fan [more on this below]. Channel A reads the house pressure [with the reference outside], while Channel B measures the pressure at the fan sensor and just upstream of the sensor, converting this pressure difference to flow.
NOTE: The relationship between the pressure difference inside to outside the building and the air flow resulting from the pressure difference can be expressed by a power law equation:
Q = CΔPn
Q is the flow (cubic feet per minute), C is a constant, P is pressure, and n is the exponent of the power law equation.
The exponent can vary between 0.5 and 1.0, with essentially big holes in the building making an exponent of 0.5 the best fit (curved line) and very tiny holes making the exponent of 1 the best fit (a straight line). The cool thing about this power law equation is that it is just about the relationship between pressure and flow. Yes, other factors such as temperature and air density have impact, but they are easy to correct for and don’t fundamentally affect the pressure/flow relationship.
Why doesn’t “necking” down the fan with different rings create turbulence and mess with the key relationship between pressure and flow?
Think of the air just upstream of the fan sensor—where the air is being pulled in—as the water just above two rocks restricting flow in a stream. That water is smooth while the water downstream is turbulent. A similar situation takes place in the blower door and this is why the fan sensor is on the “calm” upstream side of the set up and why restricting the blower door with rings does not really disturb what happens at the sensor.
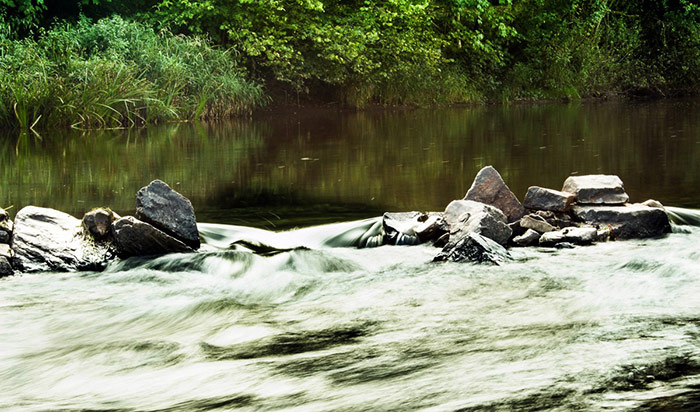
The other thing going on here is that the air is moving so fast, regardless of which ring is being used, that there is not really time for turbulence right where the air is being pulled past the sensor.
When performing a blower door test, is depressurizing the house inherently more accurate than pressurizing the house?
This is an interesting question with a couple of answers. First, since to pressurize you just spin the fan around, the sensor is still upstream in the “calm” spot. And the fan does not really care or know which way it faces.
However, during a depressurization test, the air upstream of the sensor is on the inside of the building and that air is always calm. During a pressurization test, the air upstream of the sensor is outside the building, where wind—either steady or gusting—can create “noise.”
Wind creates problems that can be overcome with an averaging baseline for depressurization but the wind can create an added problem during pressurization testing.
How do we know what exponent to use for any one building?
It turns out that for most buildings, the exponents are fairly clustered around .65, and if you are just doing a single-point test and using the cfm50 result, the impact is not really worth worrying over. However, if you extrapolate the ELA at 4 Pa from that single-point test with an assumed exponent—to better assess infiltration—then you could be introducing significant error.
To really compare how a building performs at 50 Pa of pressure difference to how it performs at 4 Pa pressure difference, a multi-point test can generate a curve and a better value for n, the exponent. But it is harder to get accurate pressure readings at low pressures and this also does not tell us anything about where the leaks are, an important part of understanding the air leakage a building experiences.
Shouldn’t we be using a different exponent for before and after deep energy retrofits and when doing AeroBarrier air sealing?
Look at it this way: you just changed the leakage factor in these buildings by a factor of 20 or so and that is like pulling an SUV off the road and replacing it with a plug-in Prius.
NOTE: To be fair to AeroBarrier, here is how their protocol works:
- Before and after the air sealing process, single point tests at 50 Pa are conducted.
- During the sealing process, the building is pressurized to 100 Pa, and the cfm50 is extrapolated.
AeroBarrier is working on incorporating multi-point testing into their protocol and software so that they will be generating a value for n instead of assuming 0.65. And AeroBarrier is interested in better understanding the drivers behind pressurization and depressurization differences to determine what role it should play in their protocol.
How different is using a duct blaster instead of a blower door fan for building air tightness testing?
The only thing that really changes is the shroud. We should be using a duct blaster for building air tightness more often. It works for homes in the 3 to 5 ACH50 range. And for multi-family unit testing you can literally leave the fan in the panel as you move it from floor to floor and unit to unit, assuming that the unit entry doors are the same size. In Europe, they call TEC’s duct blaster a mini-blower door.
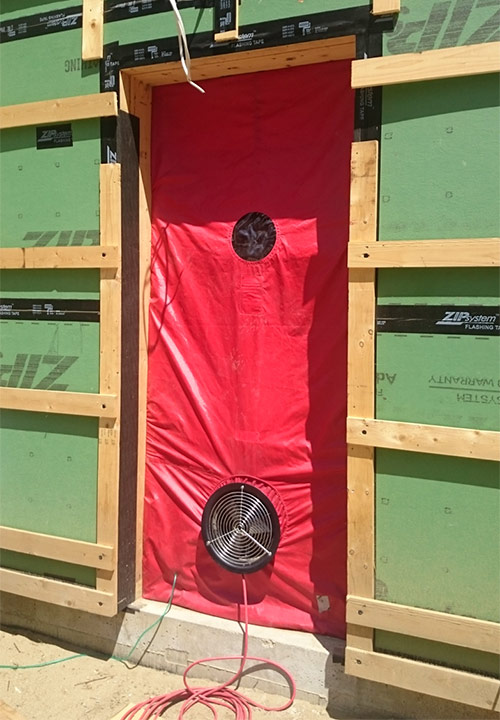
Is the Sonic LQ approach a viable option for measuring air leakage?
Fundamentally, if you want to know how much air flows through a building, you need to measure how much air flows through a building. Blower door testing is pretty much a DC phenomenon while sound is more of an AC phenomenon. Pascal’s principle states that when you create pressure in a closed vessel, that pressure makes it way all around the building at the speed of sound.
Sound waves drop off in intensity as the square root of the radius of their generation. This makes the AC phenomenon of sound a good complementary air leakage assessment tool for local or targeted air leakage but not well-suited for whole buildings.
Note: Airtightness testing for really big buildings is problematic: tough to schedule, very invasive to construction progress, often requiring sectioning, etc.
If Sonic LQ is not the answer, what is the answer for big buildings?
When we start to take our efficiency industry as important as the tile in the lobby, we will have in our schedules and in our plans accommodations for testing and people in our industry won’t have to work nights and weekends. It’s a matter of people recognizing the importance of air tightness testing and giving the issue the attention it is due.
The TEC DG1000 is a huge breakthrough, essentially combining a pressure gauge and a computer.
Yes. What’s new with the TEC DG1000?
One of the latest updates adds Bluetooth capability. This was a really difficult technical hurdle, even though we had the antenna already built into the gauge. Before, if you pulled up the TEC app on your phone to run the blower door remotely, it pretty much shut down the other capabilities of your phone. With Bluetooth, a point-to-point connection is made between the gauge and your phone, so you can still use say, google, on your phone.
Listen to the author’s complete interview with Collin Olson:
Originally published on GreenBuildingAdvisor.com. Peter Yost is GBA’s technical director. He is also the founder of a consulting company in Brattleboro, Vermont, called Building-Wright. He routinely consults on the design and construction of both new homes and retrofit projects. He has been building, researching, teaching, writing, and consulting on high-performance homes for more than twenty years, and he’s been recognized as NAHB Educator of the Year. Do you have a building science puzzle? Contact Pete here.