Earning a DOE Zero-Energy Ready Certification
Starting with stock plans, a builder prioritized his home's envelope details and made modifications to fit his family and their future.
Synopsis: Builder Brady Barkdull built this contemporary farmhouse using stock plans customized to increase the number of windows, create a more open living area, and meet a number of other needs. The home earned DOE Zero Energy Ready certification despite the lack of double-stud wall assembly because of the focus on quality windows, a high-performance space-heating and water-heating system, and air-sealing details. Unique features of the home include the 33 different truss profiles in the roof, which has multiple elevation changes, and the bonus conditioned space above the garage.
Our house sits on a 2-1/2-acre parcel in Victor, Idaho. It is 18 miles from Jackson, Wyoming, 30 miles from Teton National Park, and an hour-and-a-half drive from Yellowstone National Park. To the west are views of the Big Hole mountains, to the south we see Mt. Taylor and the Teton range. Suffice to say, it’s a beautiful and desirable location, which factored heavily into the design. We purchased the land in 2006 but it was 12 years before we started building. My family thinks of this as a legacy home, which meant, as a builder, I knew I had to get the big things right.
Although we had a tight budget, it was important to build beyond code-minimum requirements and demonstrate our values and ability to execute healthy, sustainable construction methods. My company, Wydaho Construction, has built seven DOE Zero Energy Ready and Energy Star-certified homes, so I was committed to getting those certifications for my house, but I had to be resourceful to keep costs down.
Customizing stock design plans
Teton Valley has a rich agricultural history that defines much of the region’s heritage and present-day character. For that reason, the farmhouse style made sense for our home. We love the simple and practical aspects of the traditional farmhouse but wanted it to have a contemporary feel.
We worked with a local a structural engineering firm, Design Intelligence, using basic plans we found online and customizing them to our liking. One of the changes we made was to the roof pitch, which was too steep. We also moved some interior walls to make for a more open living area; and we added more windows than the stock plan specified. It was great to be able to do some of the things I recommend to clients but also to have the freedom to do unconventional things like the windows I put in two of the bathrooms. They have an 8-ft. head height and a 6-ft. sill height to get nice natural light without forfeiting privacy. Another deviation from the original plans was moving the staircase connecting the house to the bonus space above the garage from inside to the exterior to create a separate entrance.
Perhaps the biggest change was one we made to accommodate our 14-year-old twin daughters. We had to configure the shape and size of their bedrooms to be identical, and we added a Jack-and-Jill bathroom between the rooms. They each have a sink, and there is a seated vanity area between. We installed a pocket door to separate the lavs from the shower, so the girls are able to share the bathroom with privacy. Plus, while one is showering and the other is at the vanity, the mirrors don’t fog. (This keeps the peace in our house.) The pocket door idea came to me because the bathroom is on the south end of the house; the generous window with 6-ft. sill height means when the pocket door is open, natural light reaches all the way into the bathroom mirrors.
Planning a home for views
To be parallel with the street and avoid too much heat gain on the south side, the house faces due west. There are views of the Big Hole Mountains to the west and south; on the other side you can see Mount Taylor and the Teton Range. One spot in the living room offers 270° mountain views.
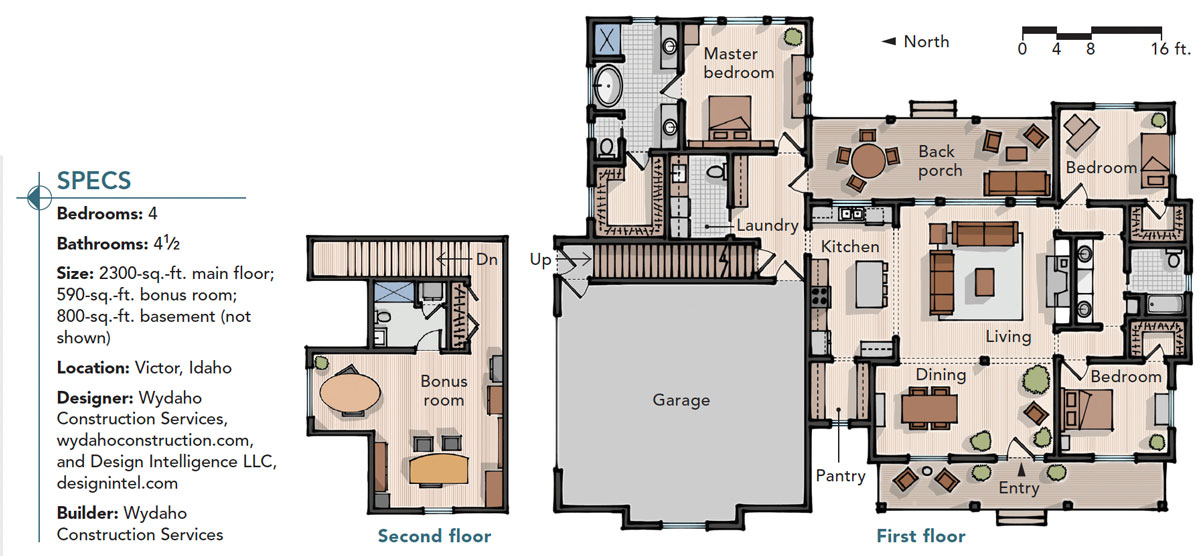
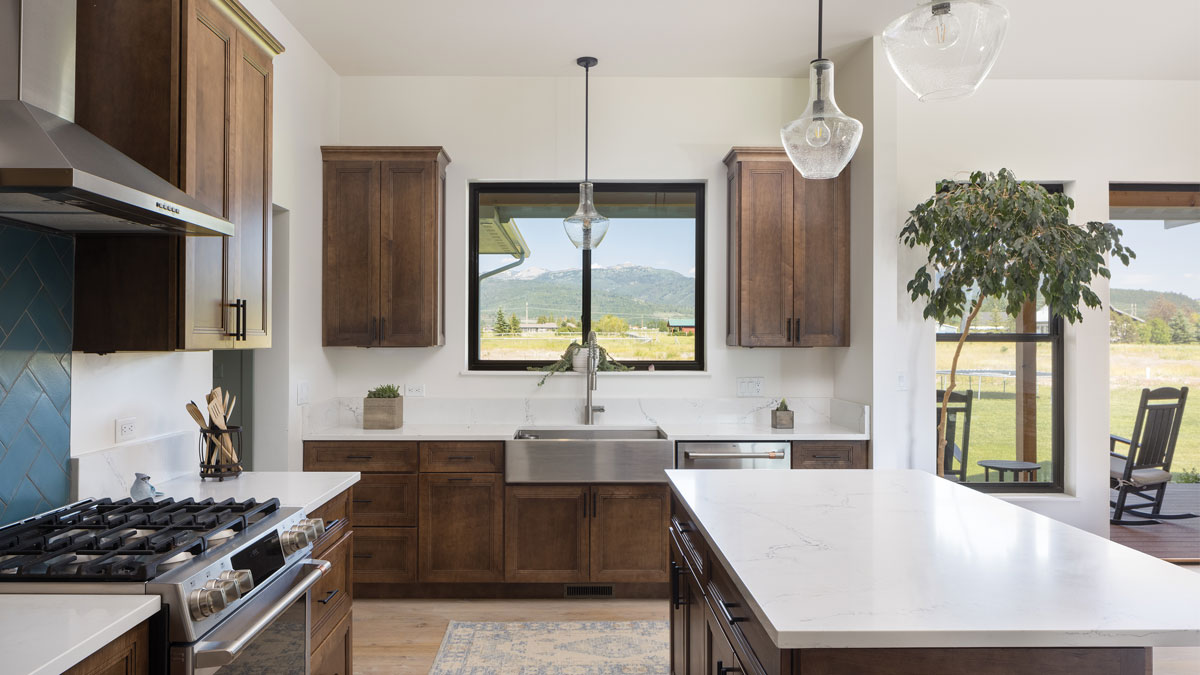
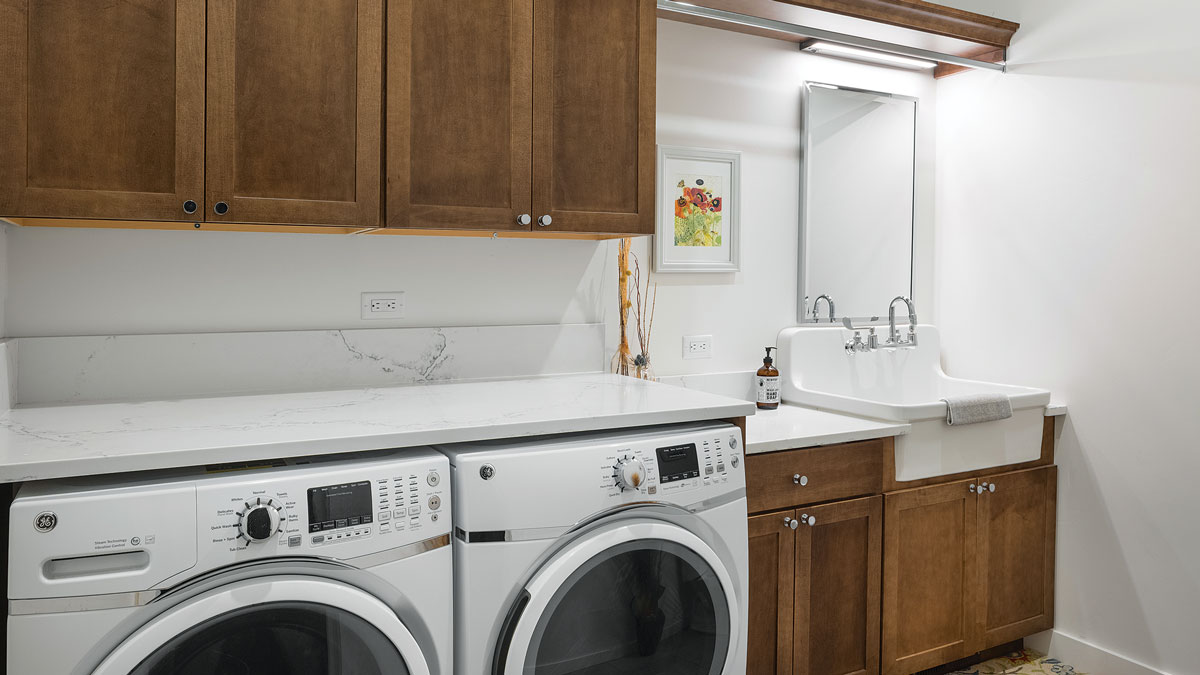
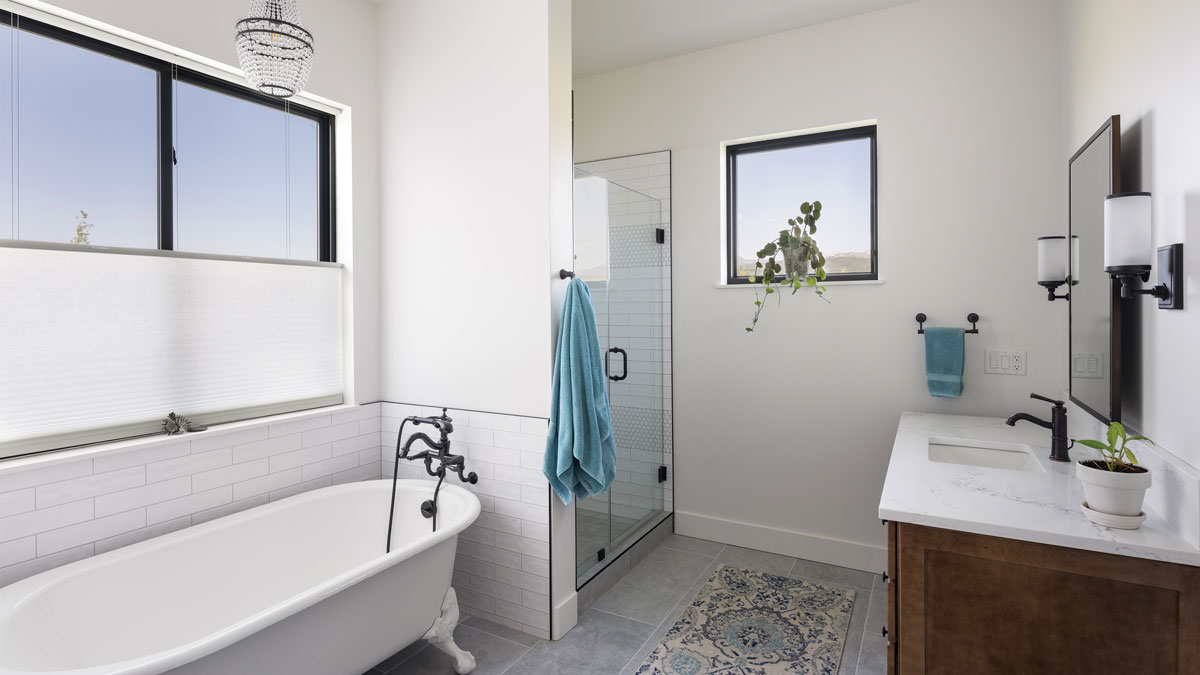

Adding below-grade space
We also decided to include a small basement. The footprint of the house is nearly 2400 sq. ft.—that would be too much basement, but we liked the idea of having private guest quarters for our parents and the annual family reunion we host. The house is L shaped, so we put the basement with full bathroom in the smaller portion. It measures 800 sq. ft and sits beneath the owner’s bedroom, mudroom, and laundry room.
Usually, in this area of the country, a full basement that is only partially finished is not cost effective. Code requires a crawlspace and digging down 42 in. to be below the frostline. We look at a fully finished basement as some of the most cost-effective space you can build; the footings are there, and you are already down 42 in. You just need to increase the height of the walls and add a slab—there’s no need for additional roofing and siding. In this case, the L shape worked well for a small, finished basement with a living area, bedroom, and full bathroom.
We used structurally rated closed-cell spray foam to insulate beneath the slab. The walls and rim joists were also insulated with spray foam for a continuous thermal control layer. It also serves as a vapor barrier, which is critical in high-radon country like Idaho. In fact, Teton County has some of the highest radon levels in the state, so mitigation was non-negotiable, but we did not want an active radon system because they typically require an electric fan running 24/7.
Custom covered-porch truss
There are 33 different truss profiles in the roof, which has multiple elevation changes. In one section of the house, running from the dining room at the front to the covered porch out back, the trusses take multiple turns. After extending horizontally from a header framing a window in a dormer and over the dining room, they drop vertically to land on an exposed beam separating the dining space from the great room. On the great-room side of the beam, the bottom chords create a vaulted ceiling, then continue horizontally beyond the exterior wall to shelter a deep covered porch.
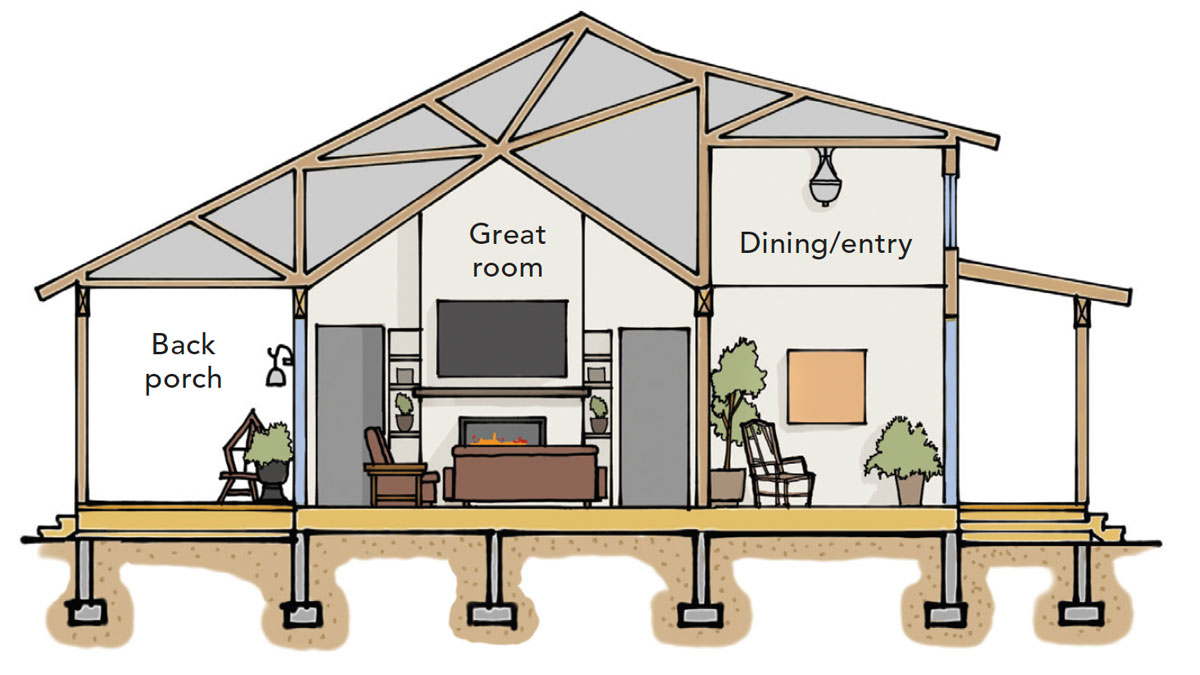
Where we saved, where we invested
We invested in areas that would have a payback and make an impact on energy efficiency and utility bills: the heating system, windows, insulation, and envelope detailing. We did upgrade to “Advanced Comfort” glass for the Pella Impervia windows, which vastly improved the U-values and satisfied certification requirements without the triple-pane price tag.
Double-stud walls filled with dense-packed cellulose are practically standard for our client homes, but my family couldn’t afford that assembly. Energy modeling helped determine that with proper detailing, quality windows, and a high-performance space heating and water heating system, meeting DOE Zero Energy Ready requirements was possible without double-stud walls. We used standard 2×4 walls with cellulose insulation and a Certainteed MemBrain vapor retarder. At .50ACH50, this is the tightest home we’ve ever built, and I attribute it to my wife’s meticulous help with the air-sealing. We spent hours and hours caulking ganged studs, headers, plates, penetrations, and panel edges, and we installed drywall gasket around door and window openings and at the bottom and top plates. Forgoing a double-stud wall assembly saved approximately $9500 in materials alone—not to mention the labor saved by not having to frame the double-stud assembly at all exterior walls.
Our ultimate goal is net-zero energy usage, so solar power is part of the plan—down the road. Idaho has some of the cheapest energy (hydroelectricity) in the country, so it is hard for some people to justify the cost of a solar array installation. We are committed to solar energy for many reasons, and we figure electricity rates are bound to go up. Plus, new products are coming onto the market all the time, so it makes more financial sense to add solar later. By the time we do, we will have a better system on our roof and the payback will be there.
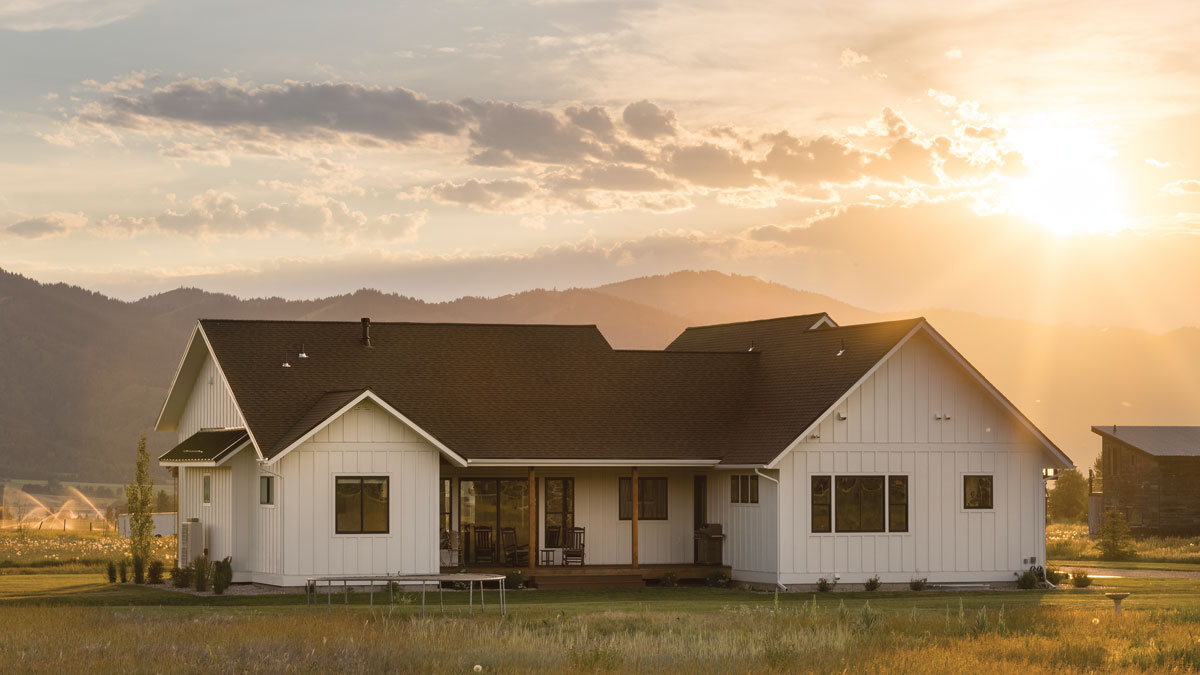
A flexible bonus space
The conditioned space above the garage has turned out to be an excellent investment. Pre-COVID, my company shared a co-working space in downtown Victor that also housed our attorney, our accountant, an architect, and a real estate agent. It was great for collaboration but less than ideal during a pandemic. We outfitted the bonus space with a conference table, and it has been the company office for over a year.
The future plan is to turn it into a studio apartment. We can rent it or use it to accommodate our parents or our kids while they get on their feet. Affordable housing is increasingly difficult to find in the valley, so we are glad to this option for them. With that in mind, we included all of the plumbing and electrical rough-ins for a full-size kitchen and bath. It was challenging to get drain lines up there, so we furred down the backside of the garage, which is adjacent to the house, so the drain can slope and get down into the crawlspace.
Attic space is continuous throughout the house to make for access easy and to aid good ventilation. The highest roof—on the bonus space and master bedroom—is a 10:12 slope. It was tall enough that it required a piggyback truss, which created a tricky insulation cavity. We had to figure out how to keep continuous insulation at that junction to allow air up to the highest point of the building; there was not enough room for cellulose, so we stapled cardboard baffles and used closed-cell spray foam from the baffle to the back of the dyrwall or face of the stud. This solution provides R-60 continuous insulation and an air channel. The rest of the ceiling is insulated with blown-in cellulose because it is less expensive and better for the environment.
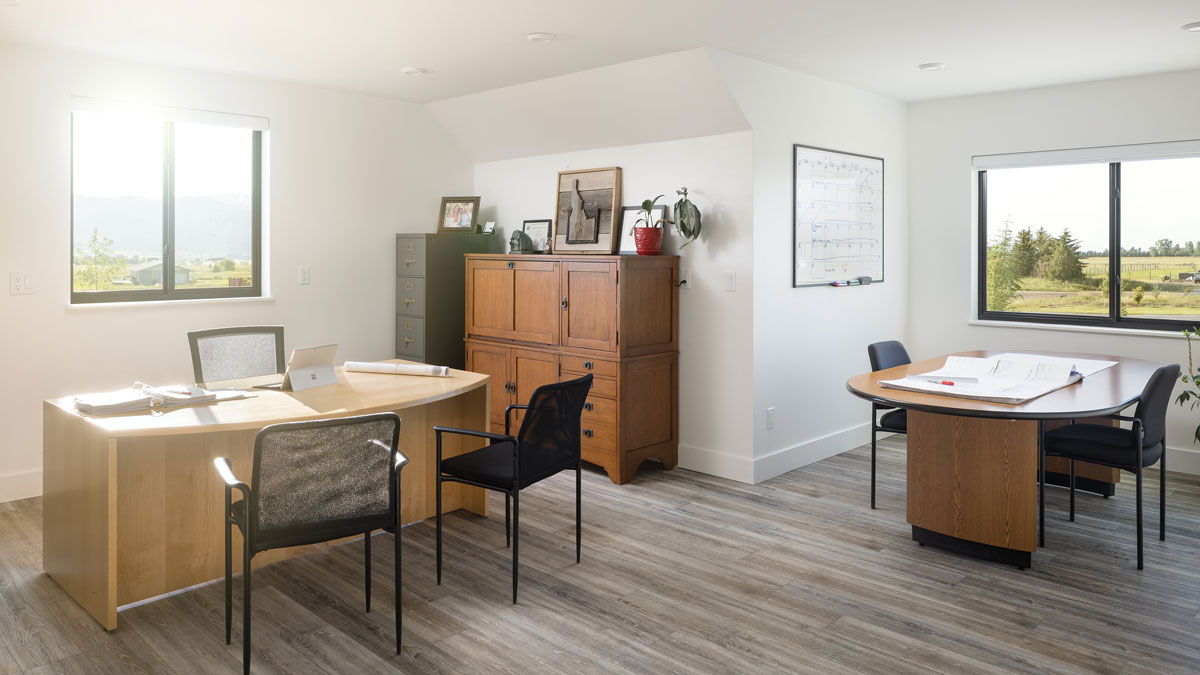
Where the trusses come together to form the bonus space, there was just a 2×4 cavity, which didn’t give us the wall insulation we needed. We solved that by running continuous Blue Board insulation on the backside of the walls in the vented attic space to eliminate all thermal bridging, and then furred them out to get 5-1/2-in. cavities for blown-in cellulose.
The water lines for the bonus space plumbing are in the garage ceiling, so we ran them snug to the bottom side of the subfloor of the conditioned space to keep them as warm as possible; that provides protection against an open garage door during freezing temperatures. We installed 11-in. floor joists, which means we could add 11 in. of cellulose between the garage ceiling and the water lines. That was a really important detail. We’ve had clients whose pipes froze and burst because someone left the garage door open for too long. We air-sealed between the garage and the bonus space, installed a vapor retarder, and put in a ceiling ventilation fan—an Energy Star requirement—to vent residual exhaust in the garage out the soffit.
The ductless minisplit was key because running duct up to that space would have been next to impossible; I was glad for the flexibility of a line set. The wall-mounted unit heats and cools the space, which is the house’s only second story; it has a west-facing window, so it gets hot.
An HVAC system designed for efficiency
The mechanical room is in the basement on the wall closest to the center core of the house, making for shorter runs and an efficient HVAC design. A Mitsubishi ducted minisplit system heats and cools the main floor; and in addition to the head in the bonus space, there are two ductless minisplits—one ceiling cassette and one wall-mounted head—for the basement. They share a single outdoor condensing unit. The ducted air handler includes a back-up heat strip, which is important in climate zone 6 because minisplits are not as effective below -9℉, and we see -20℉.
We maximized our water heating efficiency using a conventional water heater as a holding tank. It brings the temperature of the well water from 50℉ to 70℉ without using any electricity. The water from the tank feeds a heat-pump water heater.
To be eligible for DOE Net Zero Ready certification, a house must also be EnergyStar, Indoor Air Plus, and WaterSense certified. Continuous ventilation was a requirement. We installed a Fantech HRV for a constant exchange of stale air for fresh, tempered air. With a house this tight in this climate there will be a significant moisture and mold problem without a balanced ventilation system.
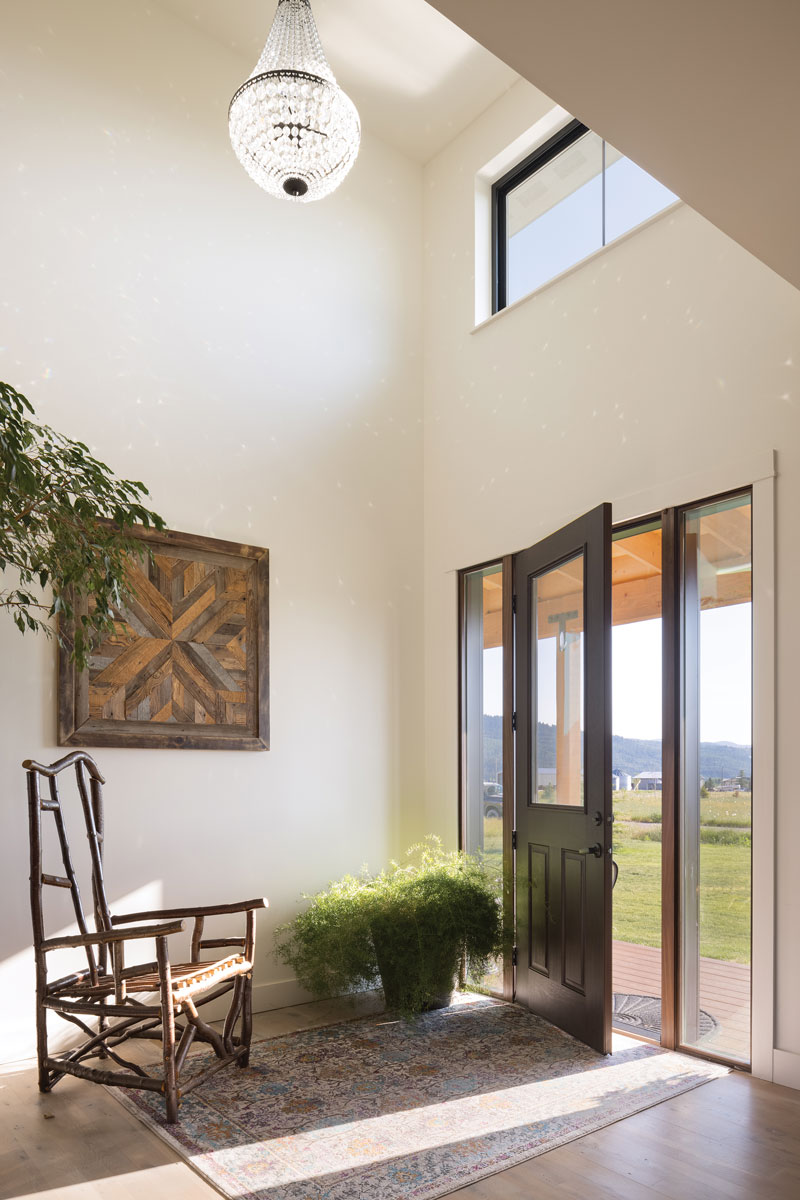
To ensure good indoor-air quality, we used low- or no-VOC paints and adhesives, Green Label Plus carpet, and CARB-compliant cabinetry. We also incorporated natural materials like white oak flooring and pine shelving, baseboard, and casement work.
The decisions we made and the work we did demonstrate a high level of care about the performance, craftsmanship, and longevity of our home. That degree of care is missing from today’s production building—the homes have no soul. Our home may be new, but it already has a lot of history.
Brady Barkdull is the owner of Wydaho Construction Services.
To read the entire article, please click the View PDF button below.
From Fine Homebuilding #302
RELATED LINKS
View Comments
Clean, simple layout.
Curious as to the original stock plan source.